Гидроизоляция фундамента мастикой своими руками: технология нанесения, виды мастик
Виды мастик
В состав гидроизоляционной мастики входят:
- Битумные вяжущие — основа, которая обеспечивает гидроизоляционные свойства.
- Минеральные добавки и наполнители — для улучшения эксплуатационных характеристик материала и увеличения прочности покрытия.
- Растворитель.
Иногда в состав добавляют модификаторы (стирол-бутадиен-стирол), гербициды и антисептики.
Так как основные свойства гидроизоляции зависят от вяжущих, битумные мастики для фундаментов и крыш чаще всего классифицируют именно по типу вяжущего.
Строительный битум. Разогретый до 300 °C битум наносится на поверхность для гидроизоляции. Способ трудозатратный, слой гидроизоляции ненадежный, подвержен разрушительному воздействию окружающей среды, его требуется постоянно обновлять, поэтому строительный битум вытесняется более современными кровельными и гидроизоляционными мастиками.
Битумные мастики. Состоят из битума, наполнителя и пластификатора, разогревать их перед нанесением не требуется.
Битумно-полимерные. Включают, помимо битума и армирующих наполнителей, полимерные добавки. Полимерные модификаторы увеличивают температурный диапазон эксплуатации, делают покрытие более эластичным и долговечным. Наносятся в холодном виде.
Битумно-эмульсионные мастики. Мелкодисперсная смесь в водной среде битума, минеральных наполнителей и технологических добавок. Как правило, используется в качестве праймера. Предварительный разогрев не требуется.
Мастики бывают однокомпонентные и двухкомпонентные. Первые полностью готовы к нанесению (иногда в них нужно добавить растворитель, чтобы довести до нужной консистенции). Двухкомпонентные смешиваются непосредственно перед нанесением.
Для глубоких (>5 м) фундаментов битумные мастики в качестве основной гидроизоляции не применяют. В таком случае целесообразно использовать рулонные материалы.
Толщина гидроизоляции и межслойные интервалы
Чтобы не допустить разрыва гидроизоляции, необходимо рассчитать количество слоев мастики. Толщина и количество слоев зависят от глубины заложения фундамента:
- до 3 м — 2 мм (после высыхания), в 2 слоя;
- от 3 до 5 м — 2–4 мм (после высыхания), в 2–4 слоя.
Чтобы убедиться в том, что слой равномерный и достаточной толщины, его следует замерять дважды: до высыхания (например, при помощи диска или гребенки) и после полного высыхания (толщиномером). Обычно мастика после высыхания усаживается на 30–70%, в зависимости от доли летучих компонентов в составе. На этот параметр обязательно нужно обращать внимание, так как в противном случае сильно усевший слой изоляции может в дальнейшем порваться.
На квадратный метр гидроизоляции фундамента битумной мастикой на горизонтальной поверхности расходуется 2–4 кг состава. На вертикальной — до 1 кг. Точная норма расхода конкретного вида мастики указывается производителем на этикетке.
Каждый последующий слой можно наносить исключительно после полного высыхания предыдущего. Если не соблюдать это технологическое требование, гидроизоляция начнет расслаиваться. Скорость высыхания гидроизоляционной мастики зависит от ее вида и обычно указывается на упаковке. В среднем на высыхание одного слоя требуется около суток. На время высыхания влияет также температура воздуха, влажность, материал основания и т. д.
Порядок обработки поверхности мастикой холодным методом
Надежность гидроизоляционного слоя напрямую зависит от двух факторов: качества продукции и соблюдения технологии гидроизоляционных работ. При нарушении технологии поверхность со временем может начать трескаться, отслаиваться, пропускать грунтовые воды.
Подготовка поверхности
Перед началом работ проводится подготовка основания: поверхность нужно выровнять, устранить пыль, загрязнения, старую гидроизоляцию, если она вздувается, отслаивается от основания. Для нанесения состава поверхность должна быть тщательно просушена.
Нанесение праймера
При выборе праймера нужно ориентироваться на вид используемой обмазочной гидроизоляции, так как не все праймеры и мастики сочетаются между собой. Праймер улучшает адгезию между основанием и слоем изоляции, уменьшает расход мастики. Наносится на предварительно подготовленную поверхность коротковорсовым валиком. При обработке сложных элементов можно использовать кисть. Праймер наносится одним равномерным слоем и оставляется до полного высыхания.
Нанесение битумной мастики
Материал наносят вручную или распылителем. Вручную мастика наносится при помощи шпателя, фальцевой кисти с короткой жесткой щетиной или коротковорсового валика. При механизированном способе обмазочная гидроизоляция наносится методом безвоздушного распыления под давлением 150 бар. Мастику следует наносить со стороны попадания воды равномерным слоем, сверху вниз. Дождаться полного высыхания слоя, нанести следующий слой таким же образом.
Армирование гидроизоляции
Гидроизоляцию фундамента новой постройки нужно армировать, чтобы избежать повреждения гидроизоляционного слоя при усадке строения. Для надежной защиты от негативного воздействия влаги с особой тщательностью нужно армировать желоба, стыки, углы, выступы, места примыканий и другие сложные элементы конструкции. Армирование проводится с помощью стеклоткани или стеклохолста, которые укладывают на первый слой мастичной гидроизоляции до ее высыхания. Стеклоткань (стеклохолст) пропитывается мастикой. После высыхания наносится следующий слой.
Перед применением мастику следует выдержать в течение суток при температуре 15–30 °C. При необходимости добавить растворитель, тщательно перемешать. Двухкомпонентные мастики смешивают не ранее чем за полчаса до нанесения. Смешивание производится миксером со спиралевидной насадкой не менее 5 мин на низких оборотах.
Продукция ИКОПАЛ
ICOPAL выпускает линейку гидроизоляционных мастик различного назначения.
Гидроизоляционная мастика ИКОПАЛ на основе битума и органических растворителей, пластификаторов и минерального наполнителя используется для гидроизоляции фундаментов и других заглубленных конструкций, внутренних помещений, защищает от коррозии металлические элементы. Полностью готова для использования. Ее можно наносить при температуре от –5 до +45 °C. Обеспечивает надежный гидроизоляционный слой при низком расходе.
СБС ИКОПАЛ на основе СБС-модифицированного битума, органического растворителя и пластификаторов применяется для гидроизоляции фундаментов, внутренних помещений, кровли, защиты от коррозии металлических конструкций. Состав можно наносить при температуре от –20 до +45 °C. Полностью готова для использования.
Водоэмульсионная мастика ИКОПАЛ. Битумно-латексный состав на водной основе с поверхностно-активными добавками и минеральными наполнителями. Применяется при температуре от +5 до +45 °C, можно наносить на влажное основание. Используется для обработки заглубленных сооружений, металлических конструкций, внутренних помещений, кровли. Может применяться для грунтовки поверхностей под обмазочную гидроизоляцию и рулонные материалы. Готова для нанесения.
Кровельная мастика ИКОПАЛ на основе нефтяных битумов, органических растворителей, с добавлением пластификаторов и минерального наполнителя. Применяется для гидроизоляции кровли, наносится при температуре от –5 до +45 °C. Теплостойкая, долговечная. Готова для использования.
Что такое битумная мастика: свойства, виды и сферы применения
Наверх Перепланировки- Каталог домов
- Квартира
- Спальня
- Кухня
- Столовая
- Гостиная
- Ванная комната, санузел
- Прихожая
- Детская
- Мансарда
- Маленькие комнаты
- Рабочее место
- Гардеробная
- Библиотека
- Декорирование
- Мебель
- Аксессуары
- Загородный дом
- Ландшафт
- Системы хранения
- Коридор
- Уборка
- Фундамент
- Кровля
- Стены
- Окна
- Двери и перегородки
- Потолок
- Балконы и лоджии
- Внутренние конструкции
- Пол
- Водоснабжение и канализация
- Отопление
Битумные мастики, которые можно применять зимой
Бывает так складываются обстоятельства, что выполнение гидроизоляционных работ приходится проводить в зимнее время, когда температура воздуха опускается ниже 0 градусов. В таких условиях возникает вопрос:
— какой выбрать наиболее оптимальный вариант гидроизоляционного материала и как с ним работать. В данной статье речь пойдет о битумных ( битумно-полимерных) мастиках, которые мы можем использовать в зимнее время.
Следует отметить, что все битумно-полимерные, битумно-каучуковые, битумно-латексные и др. мастики на водной основе мы исключаем, так как температура их применения должна быть не ниже, чем +5С.
То есть мастика должна быть на органическом растворителе ( уайт-спирит, сольвент или машинное масло) или же можно использовать горячие мастики ( которые нужно разогревать до температуры +150С-+180С).
Далее нужно смотреть на показатель морозостойкости. В технических характеристиках по каждой мастике есть такой параметр, как гибкость на брусе. У различных битумно-каучуковых, битумно-полимерных и битумно-масляных мастик он может быть от -5С до -50С. То есть чем больше цифра, тем мастика более морозостойкая и соответственно лучше подходит для работы в холодную погоду. Помимо температуры воздуха нужно еще учитывать и влажность поверхности (на которую будет наносится эта мастика). Помните, что мастики на растворителе нельзя наносить на влажную и мокрую поверхность, поэтому перед гидроизоляцией, основание на которое будет наносится мастика должно быть сухим, а если оно влажное, то его просушивают ( например при помощи пропановых горелок). Кстати нельзя забывать о том, что перед гидроизоляцией нужно обязательно проводить грунтование поверхности с помощью битумного праймера. Это не только обеспечит лучшую адгезию ( прилипание) битумно-полимерной мастики к поверхности, но и обеспечит краткосрочную гидрофобизацию основания. То есть, если вы обработали фундамент битумным праймером, то в течение 2-3 недель бетон не будет впитывать влагу и поверхность будет относительно сухой и пригодной для нанесения мастики.
Еще очень важным фактором является удобство мастики в работе. Хочется, чтобы открыл ведро и сразу можно было мастику наносить с помощью кисти или валика. К сожалению при холодной температуре битумная смесь застывает, снижается ее текучесть. Всвязи с этим появляется неудобство в работе с ней. Можно ли устранить эти неудобства? Можно значительно снизить, если знать определенные правила.
- Изначально нужно выбрать мастику в которой меньше сухого остатка и больше растворителя. Например мастику у которой сухой остаток составляет 60% легче наносить, чем ту, у которой сухой остаток 80%.
- Перед выполнением работ, мастику примерно сутки выдерживают в теплом помещении, а затем сразу наносят на поверхность.
- Если же теплого помещения рядом с объектом нет, то мастику разогревают, ставя ведро на огонь или же с помощью пропановой грелки. При таком способе ее разогрева ведра должны быть обязательно металлические. Пластиковые ведра категорически не подходят. Да и еще. При разогреве на огне, мастика должна быть обязательно однородной. Если вы используете битумно-резиновую мастику с мелкой порезанной крошкой из шин, то при сильном нагревании эти крошки будут плавится и слипаться в большие куски резины, которые плавают на поверхности мастики. После этого работать с мастикой будет крайне неудобно и она потеряет множество своих свойств.
- Для того, чтобы мастика была менее густой и вязкой и ее можно было лучше наносить, в мастику можно добавлять растворитель (уайт-спирит, сольвент, бензин). Для начала в ведро заливаете 0,5 л растворителя и начинаете ее мешать. Если полученная консистенция вас устраивает, то этого достаточно, если же мастика еще трудно наносится, то растворитель добавляем еще. Допускается добавлять расторителя до 8% от массы мастики. То есть, если ведро 20 кг, то максимально количество растворителя будет 1,6 кг (или 2 литра) на это ведро. При таком соотношении мастика не теряет своих свойств . Если добавить много растворителя, то мастика превратится в битумную грунтовку (праймер).
Из тех битумных мастик, которые есть у нас в продаже можно выделить следующий список по удобству применения зимой в порядке убывания:
- Битумно-полимерная мастика БИТЕП.
- Битумно-масляная мастика МБ-50.
- Битумно-полимерная высокоэластичная мастика Полиэласт
- Битумно-каучуковая мастика «Универсальная»
- Горячая битумно-полимерная мастика
Успехов вам в работе и хороших материалов.
как наносить и сколько сохнет
Не важно, насколько мощная в доме система кондиционирования, если стены дома постоянно страдают от проникающей через фундамент влаги и покрываются плесенью. Ее споры постоянно присутствуют в воздухе и, попадая в легкие человека, могут стать причиной аллергических или легочных заболеваний. Не допустить разрушительных процессов поможет соблюдение всех требований технологии гидроизоляции фундамента и пола. Если гидроизоляция выполняется без привлечения профессиональных строителей, лучше обратить внимание на средства гидроизоляции, не требующие специфических навыков и инструментов. Привычный всем рубероид сегодня настойчиво оттесняют битумные обмазочные смеси. Битумная мастика для гидроизоляции фундамента используется все чаще по причине легкости нанесения и скорости обработки.
Застывая, битумная мастика создает надежное покрытие, которое становится преградой влаге, проникающей из верхних слоев земли. Оберегая дом от сырости, гидроизоляция способствует целостности конструкции строения и сохранению тепла в доме. Самой эффективной считается влагозащита, выполненная на этапе строительства дома (до возведения стен), но после заливки фундамента.
Виды гидроизоляции фундамента
Вид обработки фундамента зависит от задачи, которую требуется решить:
- горизонтальная изоляция создает отсекающий эффект. Влага, проникая в фундамент, не может преодолеть гидроизолирующий барьер, и стены остаются сухими;
-
вертикальная влагоизоляция защищает наружные вертикальные стороны фундамента, не позволяя влаге проникнуть внутрь бетонной конструкции. В сочетании с горизонтальным способной изоляции фундамента и основания подвала создается полноценная защита всего здания.
Какими бывают обмазочные средства
Эффективную гидроизоляцию способны обеспечить не только битумные мастики, но и другие обмазочные средства. При производстве таких жидких мастик могут применяться различные вещества:
- битум – черное вещество, получаемое путем нефтепереработки. Обладает резким запахом и недостаточной пластичностью. Поэтому для производства готовых к применению средств используют специальные компоненты, повышающие текучесть средства;
- каучук – выполняет задачу повышения водоотталкивающих свойств мастики и обеспечивает готовому покрытию гибкость и прочность. Защитный слой обладает высокой устойчивостью к разрывам и качеством сцепления с поверхностью. Сочетание битума и каучука повышает прочность покрытия и облегчает создание гидроизоляции.
- полимеры – способствуют улучшению сцепления с поверхностью и улучшают износоустойчивость готового покрытия. Прочность жидких мастик при добавлении полимерных компонентов увеличивается в два раза.
Особенности применения битумной мастики для гидроизоляции фундамента
Для обмазочного метода гидроизоляции очень удобны и выгодны так называемые холодные мастики, которыми можно пользоваться сразу же после покупки. Они имеют вязкую текстуру и удобно распределяются по поверхности обычным шпателем. Жидкое состояние горячих мастик достигается добавлением специальных растворителей, стабилизаторов и других дополнительных компонентов.
Горячие мастики отличаются более высокой прочностью, но использовать их не так удобно. В строительных магазинах они представлены в виде брикетов. Перед обмазкой фундамента брикет мастики необходимо расплавить и быстро нанести на обрабатываемую поверхность, пока масса не застыла. Битум – легко воспламеняемое вещество. Поэтому нагревать массу следует очень аккуратно в защитных перчатках, не допуская попадания мастики в открытый огонь. Выполнить своими руками весь комплекс мероприятий по гидроизоляции горячей мастикой проблематично. Создание равномерного защитного слоя требует определенных навыков у мастера, поэтому при создании влагозащитного барьера для фундамента холодная битумная мастика применяется гораздо чаще.
Соблюдение всех этапов технологии гидроизоляции фундамента битумной мастикой в процессе возведения дома очень важно. Это избавит домовладельца от необходимости периодического проведения ремонта отсыревших участков стен и отделки. Гидроизоляционные работы выполняют в сухую теплую погоду, так как эластичность и текучесть битумных мастик снижается при охлаждении.
Подготовка фундамента
Данный процесс проводится по следующему алгоритму:
- На момент начала гидроизоляционных работ фундамент должен быть сухим и чистым. Перед тем, как наносить битумную мастику на фундамент, следует внимательно его осмотреть. Если замечены щели и неровности, их лучше убрать специальными строительными штукатурками. Технологический процесс заливки фундамента предполагает применение опалубки. Часто после ее удаления остаются острые края на углах основания. Для того чтобы при выполнении гидроизоляции острые зазубрины не повредили свежий слой защиты, края немного округляют и зачищают поверхность.
- С фундамента сметают пыль, мусор и остатки бетона после зачистки. Еще раз проверяют сухость бетонной стяжки. Это важно. Даже небольшое увлажнение может привести к отслоению защитной пленки и образованию пустот.
- Очищенную поверхность обрабатывают грунтовкой, которая усилит сцепление мастики с бетоном. Лучше выбрать грунтовку и битумную мастику одного производителя, это обеспечит их идеальную сочетаемость и предотвратить расслоение.
Обработка мастикой поверхности
Начинать нанесение битумной мастики на фундамент следует с нижней его части, если выполняется вертикальная гидроизоляция. В этом случае при повышении уровня грунтовых вод внешнее давление на основание обеспечит хорошее прилегание влагозащитной пленки к поверхности и риск ее отрыва от поверхности будет минимальным.
Мастику равномерно наносят сначала по вертикальной поверхности, движениями снизу-вверх, затем на горизонтальную поверхность. Это удобно делать валиком или шпателем. На полностью отвердевшую мастику наносят второй слой, но направления мазков должно быть перпендикулярными первой обработке. Такой способ обмазки фундамента битумной мастикой позволит получить ровную одинаковую по толщине пленку. В зависимости от глубины грунтовых вод делают от двух до пяти таких слоев. Повышенного внимания требуют участки, где возникли трещины. Эти места лучше армировать специальным материалом из стекловолокна.
Если используется горячая битумная мастика, ее помещают в металлическую емкость и расплавляют до жидкого состояния. Наносить обмазку нужно быстро, так как она хорошо схватывается на поверхности. Битумные мастики горячего типа применяются чаще для горизонтальной обработки, так как с их помощью легче и быстрее создать толстый равномерный слой. Для усиления водооталкивающего эффекта часто на слой жидкой битумной мастики укладывают листы рулонной гидроизоляции.
Несмотря на прочность битумного слоя, без дополнительного укрепления в нем могут образоваться трещины во время усадки грунта под зданием. Вероятность возрастает, если проводится обработка только застывшего фундамента. В местах трещин влага будет беспрепятственно просачиваться вверх по стенам. Для того чтобы слой гидроизоляции при незначительных деформациях оставался целостным, его армируют стеклохолстом. Отрезок армирующего полотна прикладывают и, прокатывая валиком, впечатывают в незастывший слой первой мастики. Второй слой гидроизоляции делают без изменений. Засыпку грунта и отделочные работы вертикалей фундамента начинают лишь после полного высыхания защитного покрытия.
Преимущества и недостатки битумных мастик
Гидроизоляционная битумная мастика для фундамента имеет как недостатки, так и преимущества. Ее эффективность проверена годами. При этом легкость применения делает возможной обработку даже без услуг профессиональных строителей. Обработка фундамента битумной мастикой не требует масштабных финансовых вложений и доступна для любого семейного бюджета.
Как любое бюджетное средство, битумная мастика не лишена недостатков. Самый значительный из них – это возможное образование трещин и вздутий за счет того, что в чистом виде битум не обладает эластичностью. Недостаток устраняется либо армированием, либо использованием жидкой мастики на основе битума с полимерными добавками. Кроме того, неэстетичный вид покрытия требует обязательной отделки или покраски. Но существенным этот недостаток назвать нельзя, так как для любого дома отделка фундамента является частью общего дизайна.
Как правильно наносить мастику при герметизации швов.Стройполимер
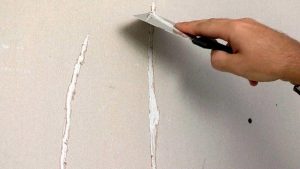
Стыки, трещины, швы ухудшают теплоизоляционные свойства здания. Через них в помещение проникают холод и влага, скапливается конденсат – источник сырости и плесени. Подобные дефекты заделывают на этапе строительства, а затем – планово или внепланово, в ходе ремонтных работ. Как правильно наносить герметизирующую мастику, чтобы добиться максимального результата?
Любая мастика наносится на очищенную сухую поверхность
Принципы герметизации стыков
Герметизация бывает первичной – до момента эксплуатации дома – и вторичной (в рамках ремонта). В зависимости от этого отличается и технология. При первичной обработке стыков в швы закладывают уплотнитель или обрабатывают специальными материалами, устойчивыми к осадкам и перепадам температур. При вторичной – иногда достаточно заменить поврежденный наружный слой мастики или обновить его, предварительно расширив, зачистив и углубив.
Для герметизации швов и стыков снаружи здания нужна эластичная мастика, которая не разгерметизируется из-за усадки дома, температурного расширения материалов или механических нагрузок. Для ремонта кровельного покрытия предназначена битумная разновидность. Принцип их нанесения схож, но имеет отличия.
Никогда раньше не работали с мастикой? Начните со швов, расположенных не на виду
Какие бывают мастики
Мастика – это вязко-пластичная масса на основе органических веществ с добавлением специальных наполнителей. В ее составе могут присутствовать каучук, природные и синтетические смолы, пластификаторы. Широко применяются битумные мастики – в основном для ремонта кровельных материалов. Востребованы на рынке и полимерные мастики, например полиуретановая «УРЕМАСТ». Они отличаются хорошей адгезией и эластичностью.
Срок годности любой мастики – не более 15 лет. Однако эксперты рекомендуют обрабатывать швы и стыки повторно не позднее, чем через 7 лет после возведения здания, пока они еще не потеряли эксплуатационных свойств.
Как правильно наносить нетвердеющую мастику НГМУ
В крупнопанельном домостроении, а также при ремонте больших стыков в месте примыкания оконных/дверных конструкций применяется нетвердеющая герметизирующая мастика. Она представляет собой густую вязкую массу на основе каучуков искусственного происхождения, пластификаторов и наполнителей. Поставляется в брикетах диаметром 30–50 мм длиной до 150 см, завернутых в полиэтиленовую пленку.
В частном строительстве эту мастику используют для уплотнения мест примыкания дверных и оконных блоков к стенам. Работать с ней несложно, но также есть некоторые технологические нюансы:
- Для нанесения мастики НГМУ необходим электрический герметизатор.
- Работать можно с мастикой, которую выдержали предварительно в течение суток в помещении с температурой воздуха около 20 °С (температура материала непосредственно перед монтажом должна быть +15…+20 °С).
- Поверхность стыка очищают от пыли, мусора, бетонных крошек, а на улице в зимнее время – от наледи и снега. Использование праймера ГСР увеличит качество сцепления мастики с поверхностью и расширит диапазон температур применения, особенно в холодное время года.
- Внутренние поверхности стыка должны быть сухими, так как, соприкасаясь с влагой, мастика теряет эксплуатационные свойства.
- После нанесения мастику покрывают специальным окрасочным составом, который защитит поверхность шва от испарения и миграции пластификатора. С этой же целью можно использовать ленты Липлент, например Липлент С. После этого поверхность необходимо оштукатурить.
- Декорировать шов можно с помощью полимерцементного раствора.
Нетвердеющая мастика НГМУ предназначена для герметизации швов шириной до 30 мм с потенциалом деформации до 15 %
Как правильно наносить битумную мастику
Битумная мастика – это смола вязкой консистенции на основе битума. Материал прочный и эластичный, выдерживает динамичные нагрузки, а поскольку не имеет в составе пор, прекрасно отталкивает влагу. Для заполнения швов, для ремонта рулонных покрытий, дефектов мягкой и жесткой кровли используется «холодная» битумная мастика, сразу готовая к применению без разогрева.
Шаг 1. Очистите поверхность.
Шаг 2. Просушите.
Шаг 3. Используйте для нанесения кисть, валик или штукатурную станцию.
Шаг 4. Дождитесь, пока основание высохнет.
Шаг 5. Нанесите второй слой мастики
Шаг 6. Крупные дефекты закройте заплатками из рулонного материала, пропитанного битумом
Фронт работ готов? Трещины на фасаде дома или стыки на крыше давно нуждаются в ремонте? Запасайтесь соответствующей мастикой, готовьте инструмент – и приступайте!
Как наносить полиуретановую мастику «УРЕМАСТ»
Полиуретановые мастики предназначены для заделки наружных стыков во время строительства и ремонта. Однокомпонентные – сразу же готовы к применению. Двухкомпонентные – требуют перемешивания. Рассмотрим этапы работы с двухкомпонентной мастикой «УРЕМАСТ». Освоив их, вы с легкостью сможете работать с любым однокомпонентным составом. Для работы понадобится такой нехитрый набор инструментов.
Готовим раствор
Шаг 1. Двухкомпонентная мастика включает основную пасту и отвердитель. Переложите их в общую емкость.
Шаг 2. Планируете использовать часть мастики? Возьмите ингредиенты в нужной пропорции.
Шаг 3. Перемешайте на низких оборотах в течение 15 минут от центра к краям и обратно.
Шаг 4. Должен получиться раствор с однородной консистенцией.
Готовим поверхность
Шаг 1. Очистите основание от пыли, грязи, жира и наледи.
Шаг 2. Расшейте трещины, удалите из них старую краску и герметик.
Шаг 3. Очистите от грязи и пыли смежные участки.
Шаг 4. Просушите устье стыка.
Наносим полиуретановую мастику в стыки
Шаг 1. Наносите раствор шпателем вдоль трещины слоем не более 5 мм толщиной.
Шаг 2. Разровняйте мастику расшивкой.
Шаг 3. После затвердения покрасьте мастику фасадной краской в нужный цвет.
Шаг 4. Удалите отвержденную мастику с инструмента ацетоном или бензином.
Внимание!
- Не работайте, если на улице менее +5 °С или выше +35 °С
- Берегите мастику от прямого попадания капель дождя и снега.
- Очищайте инструмент сразу после работы, пока мастика не затвердела.
Битумная гидроизоляция пола в ванной
Битумная гидроизоляция – необходимое условие для предохранения пола от протечек и повышенной влажности. При монтаже и ремонте пола важно позаботиться об ёё устройстве в местах, где наиболее часто возникают проблемы с воздействием воды. Среди множества используемых для защиты поверхностей от влаги материалов битумная гидроизоляция пола наиболее востребована.
Из чего делают битумную (обмазочную) гидроизоляцию
Битумная гидроизоляция считается самой надёжной. Это обусловлено использованием жидких компонентов, которые проникают во все микротрещины, сколы, незначительные повреждения основания. Особенно важным это свойство является для ванных комнат и кухонь. Для создания такой защиты используют разные изделия:
- битумно-латексные смеси;
- жидкую резину, каучук;
- рулонные материалы.
Битумно-латексную смесь продают в строительных магазинах готовой к применению. Её называют мастикой. В её состав входят вяжущие вещества и полимерные наполнители. Средство склонно к растяжению и восстановлению, не содержит вредных компонентов, токсичных примесей. Мастики превосходно справляются с перепадами температуры и агрессивными воздействиями окружающей среды. Материал широко применяют для защиты от влаги пола в ванных.
Жидкая резина, каучук – состав, который легко наносится на поверхность, а при застывании блокирует проникновение воды. В качестве рулонных материалов используют рубероид. Его полотна скрепляют жидкими составами.
Битумная гидроизоляция пола – лучший и наиболее доступный для выполнения своими руками вариант устройства защиты от влаги. Технология её создания называется обмазочной. Её применяют в небольших по площади помещениях. Таких, как ванная.
Как делать битумную гидроизоляцию на бетонный пол
Битумную изоляцию пола в ванной можно наносить на бетонную и деревянную поверхность. Технология немногим отличается.
Подготовительный этап
В многоквартирных домах гидроизоляцию наносят непосредственно на бетонное перекрытие. Для этого выполняют следующие мероприятия:
- снимают старый материал до самой плиты;
- тщательно удаляют грязь, цементную пыль;
- исследуют поверхность и заделывают раствором крупные трещины, сколы;
Внимание! На влажную поверхность гидроизоляцию не наносят. Если плита мокрая, её нужно высушить.
- наносят слой грунтовки. Используют специальный состав, после высыхания которого образуется тонкая влагоудерживающая плёнка. Она служит дополнительным средством для гидроизоляции пола в ванной;
- по периметру помещения в углах, на стыках стен и пола приклеивают специальную ленту шириной 20 см. Она станет дополнительной защитой труднодоступных мест.
Если подготовительные работы проведены правильно, то с нанесением мастики в ванной проблем не будет.
Основные работы
Битумные мастики – пластичный материал. По консистенции он напоминает разогретый детский пластилин. Если синтетическая смесь слишком густая, её разводят по рекомендации производителя.
Изоляцию пола битумной мастикой выполняют широкой кистью. Готовую смесь наносят по поверхности основания тонким слоем. Обязательно захватывают не менее 20 см прилегающей к полу стены. Тщательно замазывают стыки. В местах выхода канализации и водопровода ставят резиновые уплотнители. Их надевают на сами трубы. Сверху наносят мастику, захватывая 10 см трубы.
Гидроизоляция из битумной мастики должна хорошо затвердеть. О сроке этого процесса можно прочитать в инструкции производителя. обычно это около суток. В это время нельзя допускать попадания пыли на заизолированную поверхность. Двери в ванную плотно закрывают. Можно открыть вентиляцию.
При использовании рубероида его полотна расстилают по поверхности внахлёст. Края должны заходить на стены. Места соединения полос и края смазывают битумной мастикой или жидкой резиной. Данная технология ускоряет процесс нанесения гидроизоляции.
Чтобы рубероид хорошо лёг вокруг труб, по углам и в других труднодоступных местах, его размягчают. Для этого используют паяльную лампу или строительный фен. Нагретый материал хорошо «сплавляется» с битумной мастикой и гидроизоляционная прослойка становится надёжной защитой от влаги в ванной.
После застывания битумные мастики превращаются в тёрдую водонепроницаемую поверхность. На неё наливают бетонную стяжку и стелют кафельную плитку.
Как сделать битумную гидроизоляцию на деревянный пол
Битумная мастика для гидроизоляции пола в ванной хороша тем, что наносится тонким слоем, но при затвердении становится твёрдым, надёжным и долговечным материалом для защиты от влаги. Она идеально подходит для бетонных перекрытий. На деревянное основание её тоже наносят. Но здесь есть свои нюансы.
Доски покрывают двухкомпонентным составом, в который входит жидкий каучук (резина) и активатор, необходимый для затвердения. При неплотном прилегании досок жидкое средство может стечь вниз. Защита теряет свои качества. Чтобы мастичная гидроизоляция, хорошо держалась и была эффективной, особенно тщательно готовят основание.
- С чернового настила удаляют грязь и пыль.
- Поперёк досок кладут лаги из толстых реек с шагом в 30-40 см.
- Поверх стелют пароизоляционное полотно.
- Далее кладут плиты пенополистирола, который играет роль утеплителя. Благодаря ему образуется твёрдая устойчивая поверхность.
- Стыки между теплоизоляционным материалом и лагами заполняют герметизирующим составом.
Внимание! Для утепления деревянных полов лучше использовать материалы из натуральных волокон, например, минеральную вату. Тогда поверх них кладут влагостойкую фанеру.
На подготовленное таким образом основание наносят жидкую резину (каучук) смешанную с активатором. Операцию проводят быстро, так как состав мгновенно схватывается. Для работы используют валик. Им проводят по стенам, захватывая по 20 см. Особенно тщательно промазывают углы и стыки.
Этот состав сохнет быстрее обычной битумной мастики, поэтому результат можно оценить в тот же день. Гидроизоляционный слой должен иметь гладкую, однородную поверхность. Для повышения качества влагозащиты состав наносят дважды.
Внимание! При полном соблюдении технологии можно не только создать отличную гидроизоляцию деревянного пола в ванной, но и укрепить доски, не дать им двигаться, рассыхаться. Это актуально для последующего покрытия пола кафельной плиткой.
Клей, с помощью которого крепят керамические напольные покрытия, плохо адгезируется с каучуком. Рекомендуется постелить армирующую сетку и залить тонким слоем бетонную стяжку, чтобы к ней крепить кафель.
Данный «слоёный пирог» утяжеляет конструкцию. Перед началом проведения работ проверяют, насколько прочно держатся черновые доски. При необходимости их укрепляют снизу дополнительными лагами.
Сооружённая таким образом гидроизоляция подходит не только для деревянных полов. Её делают на бетонном основании. Она является надёжной защитой от влаги в ванной, помывочной бани, бассейне. Главное — следовать инструкции производителя и дать материалу основательно высохнуть. Спешка при выполнении таких работ приводит к плачевному результату.
Просмотрено: 1 385
Оценка эксплуатационных характеристик асфальтобетонного покрытия из модифицированной каменной крошкой из каменной мастики в Малайзии
Для предотвращения повреждений дорожного покрытия существуют различные решения, такие как принятие новых смесей или использование асфальтовых добавок. Основная цель этого исследования состояла в том, чтобы изучить влияние добавления резиновой крошки шин в качестве добавки на эксплуатационные свойства смеси SMA. В этом исследовании изучались существенные аспекты модифицированных асфальтовых смесей, чтобы лучше понять влияние модификаторов CRM на объемные, механические свойства и свойства жесткости смеси SMA.В этом исследовании использовался первичный битум со степенью пенетрации 80/100, модифицированный резиновой крошкой (CRM) на пяти различных уровнях модификации, а именно 6%, 12%, 16% и 20%, соответственно, от веса битума. Было обнаружено, что подходящее количество добавленного CRM составляет 12% по массе битума. Этот процент обеспечивает максимальный уровень стабильности. Модуль упругости (Mr) модифицированных образцов SMA, включающих различные процентные содержания CRM, был явно выше по сравнению с немодифицированными образцами.
1. Введение
Битум считается термопластичным вязкоупругим клеем и используется для дорожных и автомобильных покрытий, прежде всего из-за его хорошей цементирующей способности и водонепроницаемости [1]. Сложность химического состава битумных продуктов обусловлена, прежде всего, сложной композицией сырой нефти, из которой получают битумные продукты. Из-за присущих обычному битуму недостатков, которые привели к высоким затратам на техническое обслуживание систем шоссе, возникла необходимость в модификации битума.Модификация / усиление битумного вяжущего возможна на разных этапах его использования, либо между производством вяжущего и процессами смешивания, либо перед производством дорожной смеси [2].
Каменно-мастичный асфальт (SMA) — смесь горячего асфальта, разработанная в Германии в середине 1960-х годов [3] для обеспечения максимального сопротивления колейности, вызванной шипованными шинами на европейских дорогах. В знак признания его превосходных характеристик в 1984 году в Германии был установлен национальный стандарт. Поскольку SMA распространилась по всей Европе, Северной Америке и Азиатско-Тихоокеанскому региону, несколько отдельных стран Европы теперь имеют национальный стандарт для каменно-мастичного асфальта, а CEN, Европейский орган по стандартизации находится в процессе разработки европейского стандарта на продукцию.Сегодня SMA широко используется во многих странах мира в качестве покрытия или покрытия для сопротивления наведенной нагрузке, и его популярность растет среди дорожных властей и асфальтовой промышленности.
Повышенный спрос на шоссейные дороги может снизить их прочностные характеристики и сделать дороги более подверженными постоянным повреждениям и поломкам. Как правило, на эксплуатационные свойства дорожного покрытия влияют свойства битумного вяжущего; Известно, что обычный битум имеет ограниченный диапазон реологических свойств и долговечности, которых недостаточно, чтобы противостоять повреждениям дорожного покрытия.Поэтому исследователи и инженеры битума ищут различные типы модификаторов битума с превосходными реологическими свойствами, которые напрямую влияют на характеристики асфальтового покрытия. Во всем мире существует множество добавок, используемых в качестве армирующего материала в битумных смесях, таких как стирол-бутадиен-стирол (SBS), синтетический каучук-стирол-бутадиен (SBR), натуральный каучук, волокна и модификатор резиновой крошки (CRM). Использование коммерческих полимеров, таких как SBS и SBR, в строительстве дорог и тротуаров увеличит стоимость строительства, поскольку они являются очень дорогими материалами.Однако использование альтернативных материалов, таких как модификатор резиновой крошки (CRM), определенно будет экологически выгодным и не только может улучшить свойства битумного вяжущего и его долговечность, но также потенциально может быть экономически эффективным [4] .
Резиновая крошка или отработанная резина покрышек представляет собой смесь синтетического каучука, натурального каучука, технического углерода, антиоксидантов, наполнителей и масел типа наполнителей, которые растворимы в классе для горячего дорожного покрытия. Прорезиненный асфальт получают путем включения резиновой крошки из измельченных шин в асфальтовое связующее при определенных условиях времени и температуры с использованием любого метода сухого процесса, который добавляет гранулированный или модификатор резиновой крошки (CRM) из утильных шин в качестве замены процентного содержания заполнителя. в асфальтобетонной смеси, а не как часть асфальтобетонного вяжущего или в мокрых процессах (метод модификации асфальтового вяжущего с помощью CRM из утильных шин перед добавлением вяжущего для образования асфальтобетонной смеси).Существует два довольно разных метода использования резины для шин в битумных связующих: во-первых, растворение резиновой крошки в битуме в качестве модификатора связующего, во-вторых, путем замены части мелких заполнителей измельченной резиной, которая не полностью реагирует с битумом [5]. В 1840-х годах самые ранние эксперименты включали включение натурального каучука в асфальтовое связующее для повышения его технических характеристик. Процесс модификации асфальта с использованием натурального и синтетического каучука был введен еще в 1843 году [6].В 1923 г. модификации натурального и синтетического каучука в битумах были дополнительно усовершенствованы [7, 8]. По словам Йилдрима [8], разработка резинобитумных материалов, используемых в качестве герметиков, заплат и мембран, началась в конце 1930-х годов. Первая попытка модифицировать битумные вяжущие путем добавления каучука была сделана в 1898 году Гаудмбергом, который запатентовал процесс производства резинового битума. Затем Франция получила признание за установку первой дороги с прорезиненным битумным покрытием [9].Применение модифицированного каучуком асфальта началось на Аляске в 1979 году. Сообщалось о укладке семи прорезиненных покрытий общей протяженностью 4 км дороги с использованием сухого процесса Plus Ride в период с 1979 по 1981 год. Были описаны характеристики этих разделов в отношении перемешивания, уплотнения, долговечности, усталости, устойчивости и текучести, а также сцепления шин с дорогой и сопротивления скольжению. Прорезиненный битум мокрым способом был впервые применен на Аляске в 1988 году [10]. Lundy et al. (1993) [11] представили три тематических исследования с использованием резиновой крошки как для мокрого, так и для сухого процесса на Mt.Проект Сент-Хеленс, Орегон-Дот и Портленд, Орегон. Результаты показали, что даже после десяти лет эксплуатации изделия из резиновой крошки обладают отличной стойкостью к термическому растрескиванию. Несмотря на то, что асфальтобетонные смеси могут быть успешно изготовлены, необходимо поддерживать контроль качества для обеспечения хороших характеристик.
Ассоциация по производству резиновых покрытий обнаружила, что использование резины для шин в смеси с открытым слоем связующего может снизить шум шины примерно на 50%. Кроме того, при нанесении распылением частицы резины разных размеров лучше поглощают звук [12].Более того, еще одним преимуществом использования асфальтовой резины является увеличение срока службы дорожного покрытия. Однако были даны рекомендации по оценке экономической эффективности асфальтовой резины [5].
В Малайзии использование резиновой крошки в качестве добавки при строительстве дорожных покрытий предположительно началось в 1940-х годах, но не было никаких официальных записей о такой практике. О первом зарегистрированном испытании с использованием технологии прорезиненного битума было сообщено в 1988 году, и был использован процесс влажного смешивания с добавлением резиновых добавок в виде латекса в битумное связующее [13].В 1993 году в Негери-Сембилане было проведено еще одно испытание прорезиненных материалов на дороге с использованием использованных перчаток и натурального латекса [14]. Кроме того, Малайзия производит около 10 миллионов утильных шин в год, и, к сожалению, они утилизируются экологически вредным способом. Чтобы свести к минимуму повреждение дорожного покрытия, такое как сопротивление колейности и усталостному растрескиванию, асфальт необходимо модифицировать выбранным полимером, таким как модификатор резиновой крошки (CRM), и это определенно будет экологически полезным, а также улучшит свойства битума, долговечность и снижает стоимость реабилитации [15–19].
Постановка проблемы и цель исследования : первичный битум со степенью проникновения 80/100 широко используется в Малайзии, и, кроме того, он подвергается высокой транспортной нагрузке и жарким погодным условиям. Погодные условия в Малайзии приводят к колебаниям температуры от 55 ° C на поверхности до 25 ° C на земляном полотне в жаркие дни. Из-за увеличения плотности обслуживающего движения, нагрузки на ось и низких эксплуатационных расходов дорожные конструкции пришли в негодность и поэтому быстрее выходят из строя.Основная цель этого исследования состояла в том, чтобы изучить влияние добавления резиновой крошки шин в качестве добавки на эксплуатационные свойства смеси SMA. В этом исследовании изучались существенные аспекты модифицированных асфальтобетонных смесей, чтобы лучше понять влияние модификаторов CRM на объемное, механическое сопротивление, а также сопротивление свойствам жесткости смеси SMA.
2. Материалы и методы
Экспериментальная программа в этом исследовании направлена на изучение влияния CRM на реологические характеристики прорезиненного битума и механические свойства смесей прорезиненного SMA.
2.1. Материалы
Использовался битум со степенью пенетрации 80/100 и средней температурой размягчения 47 ° C. Таблицы 1 и 2 иллюстрируют некоторые физические свойства и химический состав битума соответственно. В данном исследовании градации резиновой крошки нет. 40 (0,45 мм). Плотность резиновой крошки составляет около 1,15 (г / см³). Модификатор резиновой крошки (CRM), полученный путем механического измельчения при температуре окружающей среды, был получен от Rubberplas Sdn. Bhd. (Поставщик из Малайзии).Химические компоненты CRM показаны в таблице 3.
|
|
|
Гранитный щебень с заполнителями SMA 14 был доставлен из карьера Каджанг (около Куала-Лумпур, столица Малайзии) использовался на протяжении всего исследования. Совокупная градация принятого агрегата соответствует стандарту JKR Malaysia [20], как показано в таблице 4.
|
2.2. Подготовка образцов и метод испытаний
Метод расчета Маршалла был использован для модифицированных и немодифицированных асфальтобетонных смесей. Для включения каучука в битумную смесь был проведен сухой процесс. В сухом процессе добавка (CRM) смешивается с заполнителем перед добавлением связующего в смесь. Содержание связующего, использованное в этом исследовании, составляет 5%, 5,5%, 6%, 6,5% и 7% от массы всей смеси. Модификатор резиновой крошки добавляют в смесь в различных концентрациях 6%, 12%, 16% и 20% веса связующего.В данном исследовании использовался 5% наполнитель. Для приготовления смесей SMA 1100 г смешанного заполнителя помещали в печь при 160 ° C на 2 часа. Битум также нагревали до 120 ° C перед смешиванием с частицами заполнителя. В качестве метода сухого процесса модификатор резиновой крошки добавляли непосредственно в смесь. Температура перемешивания поддерживалась постоянной на уровне от 160 до 165 ° C. Смесь переносили в пресс-форму Маршалла. Термометр из нержавеющей стали помещали в центр формы, и смесь была готова к уплотнению при температуре 160 ± 5 ° C.Все образцы были подвергнуты 50 ударам уплотнения с помощью молотка Маршалла с каждой стороны образца при температуре 145 ° C. Лабораторные испытания, использованные для исследования и оценки эксплуатационных свойств битумной смеси SMA, модифицированной образцами CRM, представляли собой Стандартный метод испытаний на сопротивление пластическому течению битумных материалов с использованием аппарата Маршалла [21] и Стандартный метод испытаний для испытания битумных смесей на прочность при косвенном растяжении [ 22].
3. Результаты и обсуждение
3.1. Результаты теста Маршалла
3.1.1. Стабильность по Маршаллу
Результаты, полученные для различного содержания CRM для каждого содержания связующего, показаны в таблице 5 и проиллюстрированы на рисунках 1 и 2.
|
Устойчивость по Маршаллу относится к максимальному сопротивлению нагрузке, возрастающему во время процедуры испытания при 60 ° C при нагрузке скорость 50,8 мм / мин до разрушения уплотненного образца. Стабильность по Маршаллу определяется «как измерение восприимчивости битумной смеси к деформации, обеспечивающей защиту от частых и тяжелых транспортных нагрузок.”
На рисунках 1 и 2 показано значение стабильности по Маршаллу в зависимости от содержания CRM для различного содержания связующего. На диаграммах показаны значения стабильности для разного содержания связующего, изменяющегося вместе с содержанием CRM. После добавления CRM значение стабильности повысилось до максимального уровня, который составлял примерно 12% от используемого CRM, но затем оно начало снижаться. По сравнению с контрольной смесью (смесь с 0% CRM) значения стабильности по Маршаллу в целом были выше. Тем не менее, дальнейшее введение битума в смесь привело к снижению значения стабильности, поскольку применение избыточного битума снижает точку контакта грубого заполнителя внутри смеси.Единственной смесью с более низким значением стабильности была смесь с 20% CRM. Стабильность повышается за счет добавления вяжущих CRM к асфальтовой смеси из каменной смеси, поскольку между материалами в смеси развивается лучшая адгезия [9, 23].
3.1.2. Marshall Flow
Flow можно понимать как измерение постоянной деформации, которая имеет место в тесте Маршалла при отказе. Было указано, что параметр потока, полученный в результате испытания Маршалла, довольно неудачен, поскольку более высокое значение потока не обязательно означает более высокую тенденцию к течению или деформации под нагрузкой [23].Результаты, полученные для различного содержания CRM для каждого содержания связующего, показаны в таблице 6 и проиллюстрированы на рисунках 3 и 4.
|
На рисунке 3 показано значение потока по Маршаллу в зависимости от содержания связующего для каждого содержания CRM.Результаты показали, что значение текучести увеличивается с увеличением содержания битума в смеси; то есть значение текучести SMA имеет тенденцию к увеличению с более высоким содержанием связующего. Это связано с процентным содержанием дополнительного битума, который позволяет заполнителям плавать в смеси, что приводит к увеличению потока.
В случае взаимосвязи между потоком Маршалла и содержанием CRM (рисунок 4) значение потока SMA с CRM выше по сравнению с SMA без CRM. Как показано на Рисунке 4, присутствие CRM в смеси увеличивает ее расход.Кроме того, это показывает, что увеличение содержания CRM в смеси SMA не обязательно увеличивает значения расхода. Добавление большего количества содержимого CRM увеличило поток до оптимального уровня и с дальнейшим добавлением CRM в смесь; было замечено очевидное снижение. Более высокие значения расхода могут быть связаны с увеличением воздушных пустот (требуется большее уплотнение) за счет использования большего количества CRM в смеси, что приводит к более гибкой смеси [9, 23].
3.1.3. Плотность уплотненной смеси (CDM)
Полученные результаты показали, что содержание связующего влияет на характеристики уплотнения смесей SMA, таким образом оказывая значительное влияние на плотность смеси.Таблица 7 и рисунки 5 и 6 показали, что при любом конкретном содержании связующего плотность уплотненной смеси постепенно увеличивается по мере увеличения содержания битума в смеси. Это связано с тем, что битум заполняет пустоты частиц заполнителя.
|
Результаты показали более низкую плотность смесей с включением резиновой крошки. Оценка результатов, касающихся влияния содержания битума в CDM (рис. 5), показала, что значение CDM увеличивается с увеличением содержания битума в смеси SMA. Основная причина этого — заполнение битумом пустот частиц заполнителя.Однако после заполнения пустот чрезмерное процентное содержание битума могло привести к значительному увеличению плотности смеси.
Рисунок 6 показывает, что при любом содержании связующего плотность уменьшалась по мере увеличения резиновой крошки в смесях SMA. Увеличение содержания CRM подразумевает увеличение количества битума, абсорбированного CRM, вызывая большее количество пустот с частицами заполнителя, следовательно, снижение плотности смеси. Объяснение различной плотности смесей связано с влиянием вязкости на совместимость смесей.Увеличение вязкости может быть результатом количества асфальтенов в битуме, которое улучшает вязкую текучесть модифицированного образца битума во время процесса взаимодействия. Более высокая вязкость полученного связующего обеспечивает лучшее сопротивление при уплотнении смеси, что приводит к более низкой плотности модифицированной смеси. Это согласуется с предыдущим выводом Мареза [23], который показал, что для идеальной смеси для дорожного покрытия требуется хорошая корреляция между вязкостью вяжущего и усилием уплотнения.
3.1.4. Пустоты в смеси (VIM)
Прочность битумного покрытия зависит от пустот в смеси (VIM) или пористости. Как правило, чем ниже пористость, тем менее проницаема смесь, и наоборот. Слишком много пустот в смеси (высокая пористость) обеспечит проходы через смесь для проникновения вредного воздуха и воды. Слишком низкая пористость может привести к промывке, когда излишки битума выдавятся из смеси на поверхность. Влияние содержания CRM для различного содержания связующего на пористость исходной смеси и смеси SMA показано в Таблице 8 и на Рисунках 7 и 8.
|
Цифры 7 и 8 показывают, что при любом используемом связующем увеличивается CRM за содержанием в смеси следует увеличение VIM, что связано с точкой контакта между агрегатами, которая ниже, когда содержание CRM увеличивается.Большое количество частиц резиновой крошки абсорбирует связующее, которое требуется для инкапсуляции заполнителя и последующего заполнения пустот между заполнителями. Высокая пористость битумной смеси означает, что имеется много пустот, обеспечивающих проходы для проникновения вредного воздуха и воды через смесь. С другой стороны, при низкой пористости происходит промывание водой, в результате чего битум выдавливается из смеси на поверхность [23]. Однако результаты на Рисунке 7, касающиеся влияния битума, показывают, что любое увеличение содержания битума в смеси приводит к снижению значения VIM, что происходит из-за чрезмерного заполнения битумом воздушного кармана между агрегатами [24] .Поэтому очень важно производить смесь с достаточно низким содержанием пустот, чтобы она была непроницаемой и, следовательно, прочной, но с достаточным количеством пустот, чтобы предотвратить деформацию битума.
3.2. Результаты испытаний на непрямое растяжение (модуль жесткости)
Для определения модуля жесткости был проведен модуль упругости образцов в соответствии с [22] при 25 ° C. В образцах асфальта в результате избыточной деформации возникли трещины относительно прочности на разрыв, которые в основном представляли собой микротрещины.Эти трещины были перпендикулярны направлению максимального растягивающего напряжения; объединение этих микротрещин за счет увеличения деформации приводит к образованию макротрещин. Эти трещины вместе с исследованиями привели к образованию в образце зоны разрушения. Длина этой зоны разрушения может рассматриваться как параметр материала и может быть истолкована как результат энергии разрушения материала. Температура и процентное содержание битума — два основных параметра, которые существенно влияют на характеристики асфальта.
В таблице 9 и на рисунках 9 и 10 показано изменение модуля жесткости (Mr) в зависимости от содержания битума для асфальтовых смесей, армированных различным содержанием CRM, и неармированной асфальтовой смеси (содержащей 0% CRM). Как показано на рисунках 9 и 10, существует заметная разница между усиленными и неармированными образцами в модуле жесткости (Mr). Повышенный битум оказывает значительное влияние на модуль жесткости образцов с различным содержанием CRM из-за того, что оптимальный процент битума ниже в неармированных образцах.В образцах армированного асфальта с CRM содержание резиновой крошки абсорбирует часть битума, что приводит к увеличению оптимального процента связующего. По мере увеличения содержания резиновой крошки всасывается больше битума, что, в свою очередь, увеличивает оптимальное содержание связующего в смеси. Видно, что модуль жесткости армированных образцов асфальта выше, чем у неармированных образцов.
|
предлагают более высокую жесткость
что, помимо большей жесткости, они более устойчивы к деформации.Однако следует проявлять осторожность со смесями очень высокой жесткости из-за их более низкой способности к деформации при растяжении до разрушения; то есть такие смеси с большей вероятностью разрушатся из-за растрескивания, особенно при укладке на фундамент, который не может обеспечить адекватную поддержку [23].
4. Заключение и рекомендации для будущих исследований
На основании проведенного исследования можно сделать следующие выводы: (1) Стабильность повышается за счет добавления вяжущих CRM в асфальтобетонную смесь по мере развития лучшей адгезии.По сравнению с контрольной смесью (смесь с 0% CRM), значения стабильности по Маршаллу в целом были выше. (2) Независимо от количества включенного CRM, добавление CRM в смесь увеличивает VIM смеси при уменьшении ее плотности. . (3) Модуль жесткости образцов SMA с различным содержанием CRM значительно выше по сравнению с неармированными образцами. (4) Подходящее количество добавленного CRM составляет 12% по массе битума. Этот процент обеспечивает максимальный уровень стабильности и VIM.(5) Объемные и Маршалловые свойства смеси CRM-SMA демонстрируют приемлемые тенденции и могут удовлетворять стандартным требованиям. (6) Для дальнейших исследований рекомендуется использование различных типов заполнителей, градации заполнителей, различных методов смешивания и различных методов уплотнения.
.Колейность и усталостные свойства бетонных смесей из каменно-мастичного асфальтобетона с добавлением целлюлозного волокна
В этой статье исследуются динамический отклик, сопротивление колейности и усталостное поведение трех бетонных смесей из каменно-мастичного асфальта (SMA), выбранных на основе номинального максимального размера заполнителя (NMAS) : 25 мм, 19 мм и 12,5 мм с использованием целлюлозного волокна, добавленного в количестве 0,3% от общего веса заполнителя. Были изготовлены гираторные образцы суперпаве, которые подверглись испытаниям на динамический модуль () и текучесть (число и время текучести) с использованием тестера характеристик асфальтовой смеси.Результаты испытаний были использованы для построения зависимых от напряжения основных кривых для каждой смеси, показывающих, что смесь с NMAS 25 мм относительно жестче, чем другие испытанные смеси; эта смесь также демонстрирует отличную стойкость против колейности. Кроме того, определяется параметр усталости, который получается из динамического отклика и фазового угла, и результаты показывают, что смесь NMAS толщиной 12,5 мм имеет относительно лучшее сопротивление усталости, чем другие выбранные смеси. Кроме того, для прогнозирования накопленных деформаций в зависимости от циклов нагружения использовались спецификации модели нелинейной регрессии.Кроме того, разработана модель числа потоков, которая предсказывает колейность смесей, и результаты показывают, что прогнозируемые и наблюдаемые модели выходы смеси 25 мм SMA оказываются очень близкими. Результаты этого исследования помогают понять характеристики и поведение асфальтобетонных смесей из каменно-мастичного мастики с добавлением целлюлозного волокна при различных смоделированных температурах и уровнях напряжений, которые могут использоваться в областях, где часто наблюдается преждевременное разрушение гибких покрытий. Протокол испытаний, использованный в этом исследовании, также поможет в оценке характеристик покрытия с использованием Механико-эмпирического Руководства по проектированию покрытия.
1. Введение
Колейность и усталость на гибких покрытиях — два распространенных нарушения, которые проявляются на национальных автомагистралях по всему миру. С этими проблемами связаны различные факторы, включая перегрузку, высокие температуры и эмпирический подход к проектированию, используемый для проектирования конструкций. С этой целью SMA считается эффективным решением в районах с интенсивным движением транспорта из-за большего размера заполнителя одного размера, который можно использовать с увеличенным битумом, что позволяет контролировать склонность к образованию колей.Устойчивость к усталостному растрескиванию и растрескиванию при отражении повышается за счет более высокого содержания связующего в смесях SMA. В различных частях мира использование SMA очень распространено для районов с интенсивным движением. Причиной такого использования может быть конструкция смесей SMA, в которых нагрузку на колесо выдерживает каркас из крупного заполнителя, который способствует сопротивлению колейности, и богатое связующее, которое закрывает пустоты и, следовательно, делает его более жестким. Таким образом, преобладает контакт между камнями в крупном заполнителе, в то время как мелкий и средний размеры заполнителей помогают захватить более крупные частицы, когда смесь разнесена.
Текстура SMA обычно обеспечивает хорошее качество езды, лучшее сопротивление скольжению при относительно низком уровне шума. Крупнозернистый заполнитель обеспечивает долговечность, что способствует огромной устойчивости к остаточной деформации, а более высокое содержание битума герметизирует пустоты и делает его чрезвычайно эластичным. Ингибитор дренажа необходим для предотвращения вытекания битума на протяжении всего срока службы конструкции дорожного покрытия. Для улучшения механических свойств SMA можно использовать модифицированный битум вместе с подходящими добавками; а в некоторых ситуациях это может снизить или даже исключить потребность в других ингибиторах дренажа.
В недавнем прошлом наблюдалось значительное улучшение конструкции конструкции дорожного покрытия, где фундаментальным механистическим свойствам уделялось большое внимание. Были разработаны различные новые смеси для дорожных покрытий, а также система классификации и анализа смеси, основанная на характеристиках, более известная как Superior Performing Asphalt Pavements (Superpave) Программой стратегических исследований автомобильных дорог (SHRP). Такие разработки значительно снизили зависимость промышленности от традиционных эмпирических методов расчета смеси, предлагаемых Маршаллом и Хвимом во всем мире.Дальнейшее обсуждение будет продолжено в следующих разделах.
2. Обзор литературы
Bonaquist et al. [1] рекомендовал три типа испытаний производительности в отчете 513 Национальной совместной программы исследований автомобильных дорог (NCHRP): испытания на динамический модуль (), число потока (FN) и время потока (FT) для процедуры расчета смеси суперположенных для прогнозирования характеристик разработаны асфальтовые смеси. Испытание уже использовалось для прогнозирования характеристик асфальтобетонных смесей на месте, а также для использования испытаний на текучесть (т.е., FN и FT) был очень ограничен. Позже выяснилось, что сам по себе тест не может точно предсказать поведение смеси при более высоких температурах; больше внимания теперь уделяется двум другим тестам производительности, то есть тестам FN и FT [2]. Чтобы пролить больше света, ниже представлен подробный обзор литературы.
Judycki [3] определил влияние низкотемпературного физического упрочнения на жесткость и предел прочности при растяжении обычного асфальтобетона и SMA. и непрямые испытания на прочность при растяжении были проведены на смесях после изотермического хранения при температуре -20 ° C, в различные интервалы времени до 16 дней.В этом исследовании сделан вывод о том, что после хранения прочность заметно увеличилась. Muniandy et al. [4] оценили усталостное поведение смесей модифицированного и немодифицированного асфальтового вяжущего SMA с использованием недавно разработанной техники меандра трещин. Результаты, полученные при испытании на анализ трещин, сравнивались с использованием графиков деформации, полученных при косвенном испытании на усталость при растяжении, и были сделаны выводы о том, что усталостные характеристики можно определить с использованием метода появления трещин. Искендер [5] определил стойкость к колейности базальта и комбинации базальт-известнякового заполнителя для SMA с помощью теста отслеживания колес Laboratoire Central des Ponts et Chaussées (LCPC).В этом исследовании сделан вывод о том, что сопротивление колейности снижалось при добавлении известняка в SMA в качестве мелкодисперсного материала / наполнителя. Исследование иллюстрирует влияние добавления отработанного полиэтилентерефталата (ПЭТ) на жесткость и усталостные свойства смесей SMA. Это исследование пришло к выводу, что жесткость смесей увеличивается при добавлении меньшего количества ПЭТ, а смеси, армированные ПЭТ, демонстрируют более высокую усталостную долговечность по сравнению с контролируемыми смесями (без ПЭТ) [6]. Ахмадиния и др. [7] использовали отходы пластиковых бутылок в качестве добавки к смесям SMA, и 6% по весу битума были найдены оптимальным количеством ПЭТ.В этом исследовании сделан вывод о том, что введение ПЭТ в смеси SMA значительно улучшает инженерные и механические свойства. Бенуд и Амери [8] использовали заполнитель стального шлака в SMA, и результаты показывают, что использование стального шлака в качестве заменителя крупного заполнителя улучшило стабильность по Маршаллу, модуль упругости, предел прочности на разрыв, устойчивость к повреждениям от влаги и устойчивость к остаточной деформации.
Sengul et al. [9] провели подход с использованием коэффициента Маршалла (MQ), повторное испытание на ползучесть (RCT), непрямое испытание на прочность на разрыв (ITST) и испытания на отслеживание колес SMA, модифицированного полимером SBS, и LCPC.Результаты показывают, что добавление SBS повышает сопротивление пластической деформации и снижает колейность по сравнению с обычными смесями. В другом исследовании в SMA добавляли известь, чтобы снизить способность к отгонке и чувствительность к влаге. Методология поверхности отклика использовалась для определения влияния содержания и сортировки извести на потенциал удаления SMA с использованием индекса коэффициента прочности на разрыв (TSR), и было обнаружено, что содержание извести 1% и самый мелкий заполнитель дало оптимальное значение TSR 91.8% ± 0,8% [10]. Cao et al. [11] оценивали SMA (базальт, B-SMA, известняк, L-SMA и BL-SMA), и результаты показывают, что B-SMA показала лучшую устойчивость к колейности, чем другие испытанные смеси. Пазетто и Бальдо [12] провели сравнительный анализ SMA со стальным шлаком электродуговых печей. Исследование было изложено в предварительном исследовании химических, выщелачивающих, физических и механических свойств стального шлака и привело к выводу, что стальной шлак удовлетворяет всем требованиям технических стандартов дорожного сектора и показывает более высокие механические характеристики, чем другие смеси.Многочисленные исследования показали использование различных добавок в SMA помимо целлюлозного волокна [4–6, 9, 11, 13–15]. Различные исследования продемонстрировали оценку и развитие мастер кривых [14, 16–28].
Дизайн смеси SMA состоит из выбора материала, определения оптимальной градации заполнителя, выбора добавки и ее количества, а также оптимального содержания связующего. Кроме того, смеси SMA должны обеспечивать стабильность и устойчивость к колейности, достигаемую за счет контакта агрегатов и блокировки; Долговечность смесей SMA достигается за счет соответствующей конструкции смеси, включая воздушные пустоты, пустоты в минеральном заполнителе, толщину асфальтовой пленки и количество наполнителя.
Асфальтобетонный материал ведет себя как вязкоупругий материал, и его жесткость зависит от температуры. Более высокая жесткость / модуль при низких температурах (зимой) приводит к усталостному растрескиванию, а более низкая жесткость / модуль при высоких температурах (летом) приводит к колейности. Прочность асфальтового материала значительно снижается с повышением температуры, как в Пакистане. Следовательно, необходимо охарактеризовать смеси с добавкой, используя полный протокол испытаний с простыми характеристиками (, FN и FT) для различных нагрузок и условий окружающей среды Пакистана.В этом исследовании оцениваются характеристики смесей SMA, содержащих целлюлозное волокно, с помощью трех тестов производительности, то есть FN и FT. Результаты, полученные в результате этих испытаний, были далее использованы для построения основных кривых и оценки усталостного растрескивания путем определения параметра усталости.
3. Цель и масштаб
Целью данного исследования является изучение характеристик различных смесей SMA с добавлением целлюлозных волокон путем изменения NMAS. В данном исследовании используются следующие показатели эффективности: FN и FT.Полученные результаты используются для определения модулей жесткости и оценки сопротивления усталостному растрескиванию на основе значений фазового угла. В этом исследовании также описывается колейность смесей с использованием статистических моделей, в которых используются две разные нелинейные формулы для выражения количества циклов до разрушения как функции осевой деформации. Три различных градации номинального максимального размера заполнителя (NMAS) 25 мм, 19 мм и 12,5 мм выбраны из диапазонов градаций, разработанных Национальным центром асфальтовых технологий (NCAT).Было добавлено 0,3% целлюлозного волокна от общего веса заполнителя смесей SMA и использовалось асфальтовое связующее со степенью проницаемости 60/70. Обратите внимание, что на начальном этапе тестирования были протестированы различные процентные содержания целлюлозного волокна, и было обнаружено, что 0,3% является оптимальным количеством, которое удовлетворяет критериям дизайна смеси Маршалла.
4. Методология
В следующих разделах объясняется методология, принятая в этом исследовании и проиллюстрированная на Рисунке 1.
4.1. Выбор материалов
Это исследование включает испытание трех смесей SMA, дифференцированных NMAS, которые практикуются во всем мире. Три различных градации на основе NMAS: 25 мм, 19 мм и 12,5 мм выбраны из диапазонов градаций, разработанных Национальным центром асфальтовых покрытий (NCAT) в отчете Национальной совместной программы исследований автомобильных дорог (NCHRP) [29], и градационных диаграмм. для смесей SMA представлены на рисунке 2. Целлюлозные волокна прессованных гранул длиной 2-3 мм использовались в качестве добавки к смесям SMA для улучшения пленочного покрытия на агрегате, стабильности смеси и лучшего сцепления скелета агрегата.Оптимальное содержание битума и объемный анализ смеси представлены в таблице 1.
|
Конструкция смесей SMA в первую очередь зависит от объемных свойств, таких как воздушные пустоты, пустоты в минеральном заполнителе, пустоты в крупном заполнителе и содержание связующего.Браун и Хэддок [30] представили op
.Технология поверхностей и покрытий — Журнал
Surface and Coatings Technology — международный архивный журнал, в котором публикуются научные статьи о значительных разработках в области проектирования поверхностей и интерфейсов с целью изменения и улучшения свойств поверхности материалов для защиты в сложных условиях контакта или агрессивных средах, или для …
ПодробнееSurface and Coatings Technology — это международный архивный журнал, в котором публикуются научные статьи о значительных разработках в области проектирования поверхностей и интерфейсов с целью изменения и улучшения свойств поверхности материалов для защиты в сложных условиях контакта или агрессивных сред, а также для повышения функциональных характеристик.Вклады варьируются от оригинальных научных статей, посвященных фундаментальным и прикладным аспектам исследований или непосредственного применения металлических, неорганических, органических и композитных покрытий, до специальных обзоров современных технологий в конкретных областях. Ожидается, что статьи, представленные в этот журнал, будут соответствовать следующим аспектам процессов и свойств / производительности:
- A. Процессы: методы физического и химического осаждения из паровой фазы, термическое и плазменное напыление, модификация поверхности с помощью методов направленной энергии, таких как такие как ионные, электронные и лазерные лучи, термохимическая обработка, влажные химические и электрохимические процессы, такие как гальваника, золь-гель покрытие, анодирование, плазменное электролитическое окисление и т. д., но без покраски.
- B. Свойства / рабочие характеристики: характеристики трения, износостойкость (например, истирание, эрозия, истирание и т. Д.), Стойкость к коррозии и окислению, тепловая защита, сопротивление диффузии, гидрофильность / гидрофобность, а также свойства, относящиеся к поведению интеллектуальных материалов и улучшенные многофункциональные характеристики для экологических, энергетических и медицинских приложений, но исключая аспекты устройства.
Статьи должны выходить за рамки формата технических рецептов и получать существенное новое понимание и понимание, основанное на подробных характеристиках покрытий и процессов.Экспериментальные документы должны содержать полную информацию о параметрах процесса и соответствующие характеристики микроструктуры. Кроме того, документы, включающие данные испытаний, должны содержать полную информацию об испытательном оборудовании и параметрах. Такие документы должны сообщать о взаимосвязи синтеза-характеристики-свойства-характеристики.
Рукописи должны быть написаны на хорошем английском языке и содержать сбалансированный и актуальный список литературы, отформатированный в соответствии с руководством для авторов.
Примечание для авторов:
Для рассмотрения для публикации, сопроводительное письмо к вашей статье должно четко объяснять новизну и оригинальность вашего исследования и его научный вклад помимо ранее опубликованных статей.В противном случае ваша заявка не будет рассматриваться для публикации и не будет отправлена на рецензирование.
Преимущества для авторов
Мы также предоставляем множество преимуществ для авторов, такие как бесплатные PDF-файлы, либеральная политика в отношении авторских прав, специальные скидки на публикации Elsevier и многое другое. Щелкните здесь, чтобы получить дополнительную информацию о наших услугах для авторов.
Информацию о подаче статей см. В нашем Руководстве для авторов. Если вам потребуется дополнительная информация или помощь, посетите наш Центр поддержки
Hide full Aims & Scope .