схема крепления кровли с помощью саморезов
Из большого количества известных кровельных материалов металлочерепица выделяется своей долговечностью, практичностью и привлекательным внешним видом. Покрытие крыши металлочерепицей существенно изменяет облик постройки, придает дому солидный и нарядный вид.
Производится из стали (реже — из алюминия или меди) толщиной около полмиллиметра, отчего вес кровли ощутимо снижается — по сравнению с шифером — в 2 раза. Материал имеет двойную степень антикоррозийного покрытия — оцинковка и полимерный слой, надежно сохраняющий металл в течение большого количества времени.
Попутно с покрытием изготавливаются все необходимые доборные элементы — коньки крыши, карнизные и оконные уголки, ендовы, водостоки и т.д. Выпускается несколько цветовых вариантов, размеры и рисунок профиля у разных производителей отличаются друг от друга, что создает возможность выбора наиболее привлекательного варианта.
В этой статье вы узнаете, как правильно прикручивать металлочерепицу и как крепить металлочерепицу на крыше частного дома.
Содержание статьи
Что такое обрешетка и ее установка
Для правильного монтажа металлочерепицы необходимо соорудить обрешетку, представляющую собой деревянную подложку в виде решетки или сплошного слоя. Обрешетка выполняет несколько функций:
- Обеспечивает крепеж металлочерепицы
- Образует необходимый вентиляционный зазор, исключающий намокание подкровельных материалов от конденсата.
- Создает ровную плоскость, компенсируя возможные неровности стропильной системы, что способствует нормальной установке листов и обеспечивает максимальный срок службы.
ВАЖНО!
Обрешетка устанавливается поверх слоя гидроизоляции, крепится к стропилам рядами, соответствующими шагу волны металлочерепицы. Крепится оцинкованными гвоздями, исключающими их коррозию.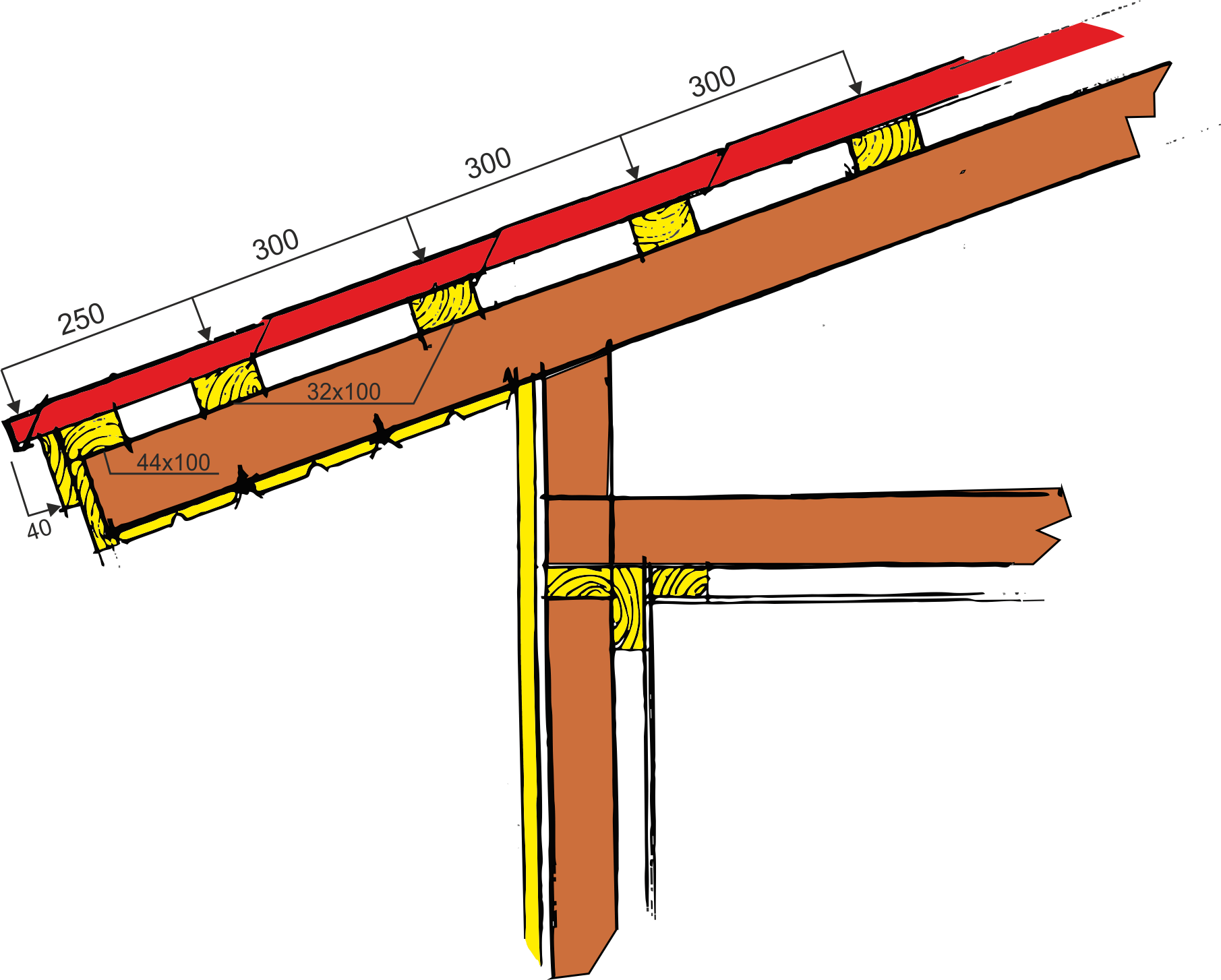
Два способа стыковки листов
Крепление металлочерепицы саморезами начинается с подготовки кровельных листов. Листы металлочерепицы стыкуются
Разница в том, что в первом случае каждый последующий лист подсовывается по предыдущий, а во втором — накладывается на него сверху. Выбор того или иного способа диктуется удобством работы, типом крыши или другими соображениями и никакого влияния на результат не имеет.
Чаще всего при работе применяются оба способа, где как удобнее.
При стыковке листов между рядами нельзя располагать их в шахматном порядке, каждый лист должен располагаться строго над нижним. Исключением может быть единичное включение фрагмента листа при заполнении, например, уклона шатровой крыши или подобных участков.
как крепить металлочерепицу на крыше саморезами: фото
Все листы, помимо крепления к обрешетке, обязательно крепятся между собой короткими саморезами по линии стыка для обеспечения герметичного соединения и исключения проникновения ветра под лист, отчего его может сорвать.
Как крепить металлочерепицу по линии карниза?
Чаще всего линия карниза перекрывается листом металлочерепицы примерно на 5 см. Такой свес позволяет воде скатываться прямо в водосточный желоб, исключая возможность контакта с деревянными деталями стропильной системы.
При этом, в некоторых случаях приходится располагать край листа выше карнизной доски, что бывает вызвано сложными условиями монтажа, наличии ступенек или иных нарушениях геометрии карниза. При таком креплении вода сходит с карнизного уголка, что несколько хуже, чем первый способ, но вполне приемлемо.
Крепление покрытия по линии каркаса
Водосточный желоб и карнизный уголок устанавливаются перед монтажом листов, чтобы обеспечить правильный сток воды.
Крепление металлочерепицы к обрешетке саморезами
Как правильно крепить металлочерепицу саморезами к обрешетке? При установке листов надо учитывать особенности материала.
Дело в том, что полимерное покрытие довольно легко разрушается при сгибании или продавливании, отчего защита листа существенно ослабляется.
Один оцинковочный слой надолго защитить металл не сможет, начнется коррозия и лист выйдет из строя. Поэтому важно правильно настроить силу прижима листа к обрешетке. Крепление металлочерепицы к обрешетке производят по следующей схеме:
- Чтобы рассчитать примерное количество саморезов, можно воспользоваться следующим правилом: на 1 квадратный метр кровли понадобится 9-10 саморезов.
- Если в процессе укладки было повреждено лакокрасочное покрытие металлочерепицы, то место скола следует тщательно закрасить антикоррозийной краской того же цвета
- Если саморез недостаточно глубоко завинтить, не получится плотного прилегания резиновой прокладки к листу, отчего возникнет щель, в которую проникнет вода.
Слишком сильное завинчивание продавит материал, покрытие отслоится и лист начнет ржаветь. Выходом из этой ситуации может стать использование шуруповерта с заданным усилием завинчивания, или постоянный контроль за глубиной погружения самореза.
ОБРАТИТЕ ВНИМАНИЕ!
Саморезы должны быть специальными, предназначенными для таких работ. Они имеют оцинкованное покрытие, уплотняющую прокладку из специальной резины. Обычная не подойдет!
Монтаж металлочерепицы вокруг труб или иных препятствий
Схема крепления металлочерепицы довольно проста, но случаются моменты, о которых стоит поговорить отдельно. Все выступающие элементы кровли должны быть обложены по периметру дополнительным рядом обрешетки, отступающим от них на 20 см. Это необходимо для установки уголка, перекрывающего стык.
В зависимости от расположения того или иного элемента может потребоваться изготовление специально обрезанного листа, соответствующего размерам оставшегося пространства или доходящего до следующего листа, расположенного штатным образом.
Правильный обход трубы металлочерепицей
Производители выпускают детали, соответствующие всем элементам крыши — внутренние и наружные уголки, коньки, ендовы, желоба и пр. Практически все они имеют единое требование к установке — наличие дополнительной планки в обрешетке, к которой они, собственно, будут крепиться.
ОСТОРОЖНО!
Следует помнить о необходимости предварительной гидроизоляции всех стыков от внешних протечек, такие места наиболее подвержены этой опасности. Конек крыши крепится поверх листов, для его крепления также требуется установка дополнительной доски вдоль верхнего конькового среза крыши.
Расположение саморезов определяется размером элемента, или по правилу — не менее 3 шт на погонный метр. Требования по усилию завинчивания такие же, как и к листам — контроль и недопустимость продавливания.
Распространенные ошибки крепления
- Наиболее частой ошибкой является неправильное соединение листов между собой, образующее щели или зазоры, в которые врывается ветер.
Частое воздействие порывов ветра при довольно большой площади листа рано или поздно оторвет его от обрешетки. Кроме того, часто встречается неправильно обрезанный край листа, накрытый уголком таким образом, что вода беспрепятственно подтекает под него.
- Все места, в которых может скапливаться или проникать вода, требуют особенного внимания и местной дополнительной гидроизоляции.
- При монтаже металлочерепицы могут возникнуть различные ситуации, требующие нестандартного решения. Надо учитывать, что в любом случае должны соблюдаться общие требования — отсутствие щелей, возможности проникновения воды, части листов должны располагаться по направлению стока воды.
- К часто встречающимся ошибкам можно отнести отсутствие контррейки при установке обрешетки, отчего исключается возможность циркуляции воздуха.
- Не рекомендуется использование рубероида или подобных материалов с использованием битума, так как в летнее время он плавится, провисает и издает удушливый запах.
- Ни в коем случае не надо использовать саморезы без уплотняющей шайбы с прокладкой.
Советы опытных мастеров
- Листы металлочерепицы довольно тонкие. Ходить по ним можно только в мягкой обуви, наступая на нижние точки волны в местах расположения планок обрешетки.
- Нельзя допускать проворачивания самореза при завинчивании, от этого сила сцепления с древесиной снижается во много раз.
- Монтаж скатной крыши можно начинать справа или слева
- Саморезы должны закручиваться строго перпендикулярно плоскости листа, иначе возникнет продавленный участок со стороны наклона.
- Обычно к приобретаемой металлочерепице прилагается подробная инструкция по монтажу. Ее рекомендуется внимательно изучить, так как все виды материала имеют свои особенности, их необходимо знать и учитывать при монтаже.
крепление металлочерепицы саморезами: схема и советы
Полезное видео
А теперь предлагаем вам посмотреть видео по самостоятельному креплению черепицы к обрешетке:
Заключение
Крепление металлочерепицы — процесс не столько сложный, сколько требующий внимания и определенных знаний. Прежде, чем начинать работы, надо детально уяснить себе все аспекты вопроса, подготовить материалы и инструменты. Теперь вы знаете, как закрепить металлочерепицу на крыше и сможете использовать полученные знания при монтаже крыши.
Самостоятельное крепление металлочерепицы будет успешным только тогда, когда человек ясно представляет себе все этапы работы и понимает очередность и правила установки всех элементов. Тогда срок службы кровли будет максимальным и не потребует ремонтов или переделок.
Вконтакте
Google+
Одноклассники
Как класть металлочерепицу на крышу: инструкция + разбор ошибок
Укладка кровли на крышу и монтаж водосливной системы – завершающий этап строительства коробки дома, зависящий от погодных условий. Все дальнейшие работы по обустройству внутренних помещений можно выполнять в любое время года и при любой погоде, что намного упрощает и ускоряет процесс строительства. Кровельные работы выполняются на большой высоте, это создает дополнительные трудности и требует безусловного соблюдения правил техники безопасности.
Как класть металлочерепицу на крышу
Перекрытие крыши выполняется в самых сложных условиях, требуется максимальная внимательность и осторожность. Кровля – один из самых ответственных элементов любого здания или сооружения. Вот почему класть металлочерепицу на крышу должны опытные строители не только теоретически знающие все тонкости производства работ, но и имеющие солидный практический опыт.
Укладку металлочерепицы проводят опытные кровельщики
Дело в том, что жизнь намного сложнее любой книги, ни одна из них не может предусмотреть все возникающие во время кровельных работ ситуации. В этой статье будут даны практические советы и рассмотрена подробная пошаговая инструкция, полученные знания помогут самостоятельно принимать правильные решения для решения различных проблем.
Содержание статьи
Перечень инструментов для укладки металлочерепицы
Работать на высоте опасно, крайне нежелательно отвлекаться на неисправные инструменты. Пред началом работ нужно проверить их техническое состояние, заменить режущие элементы и т. д. Профессионалы настоятельно советуют купить специальный пояс плотника. Он имеет множество различных карманов и приспособлений для фиксации ручного инструмента и метизов, они всегда под руками, не отвлекается внимание на поиски, не теряется напрасно время.
Технология покрытия требует подготовить следующие инструменты:
- измерительные. Надо иметь маркер, угольник, длинную ровную рейку или правило, рулетку. Желательно, чтобы рулетка имела тряпичную ленту, металлическая может повреждать верхний декоративный слой черепицы. Следует знать, что, кроме декоративного, покраска выполняет и защитную антикоррозионную функцию, ее повреждения намного уменьшают сроки эксплуатации кровли;
Измерительные инструменты
» data-font=»» data-listid=»1″ aria-setsize=»-1″ data-aria-posinset=»1″ data-aria-level=»1″>инструменты для резки и изгиба металлических листов. Требуется подготовить электрические высечные ножницы или насадку на дрель для резки металла, электрический лобзик, клещи «Гофра», ручные ножницы, просечные ножницы, ручную ножовку по металлу. Мы привели перечень инструментов для профессионального кровельщика, если строительство не ваша основная работа, то этот список можно существенно сократить и оставить только самые необходимые и доступные по цене; - молоток, монтажный нож, шуруповерт с насадкой 8×45 мм. С помощью этих инструментов закручиваются саморезы.
Инструменты для закручивания саморезов
Инструменты для резки и изгиба металлических листов
Важно. Настоятельно рекомендуется одновременно с покупкой металлочерепицы приобрести баллончик с такой же краской.
Она необходима для закрашивания мест среза, царапин поверхности листов и иных незначительных механических повреждений кровли.
Цены на металлочерепицу
Металлочерцепица
Подготовительные мероприятия
Для того чтобы во время выполнения работ не возникали непредвиденные ситуации, не тормозился процесс и не понижалось качество кровли, все свои действия нужно продумать и разбить на несколько этапов.
Первый этап – доставка материалов
Надо замерить размеры скатов крыши, подсчитать количество и длину ендов и коньков, нарисовать схему водоотвода. На основании этих данных сотрудники магазина при помощи специальной программы рассчитают оптимальное количество каждого элемента, метизов и подсчитают сумму. Необязательно сразу заказывать материал, можно проделать такие подсчеты в нескольких торговых предприятиях и на основании имеющейся информации выбрать для себя самый подходящий вариант. Сразу следует договориться о доставке кровли, длина кузова автомобиля должна быть не меньше длины листов металлической черепицы.
Длина машины должна соответствовать длине заказа
Грузоподъёмность машины должна соответствовать отгружаемым заказам
Практический совет. Если такой автомобиль дорого обходится или его сложно найти, то можно к короткому кузову прибить длинные доски. На небольшие дистанции кровлю можно перевозить и на таких приспособленных автомобилях.
Сразу выбрать площадку для складирования материалов, выровнять ее поверхность, при необходимости сделать временный навес.
Второй этап – изготовление приспособлений
Надо иметь минимум три приспособления, они существенно ускоряют процесс монтажа металлической черепицы и повышают безопасность труда.
Наименование приспособления | Назначение и краткое описание |
---|---|
Переносная лестница с упорами | Используется во время монтажа карнизных планок и водосливной системы. В верхней части имеет две специальные ноги, которые упираются о стену дома.![]() |
Леса | Они не только намного облегчают монтажные работы, но и делают их безопасными. На двухэтажных домах леса должны обязательно устанавливаться и иметь специальные поручни для упора. Могут быть самодельными или заводскими, есть большое количество вариантов изготовления лесов, конкретный следует выбирать учетом индивидуальных условий. |
Трап для передвижения по кровле | Внешне похож на деревянную лестницу, в верхней части сделаны специальные зацепы для фиксации к коньку крыши. Позволяет перемещаться по смонтированной кровле и не повреждать ее. Намного облегчает процесс вкручивания саморезов, обхода дымоходов, герметизации примыканий. Это приспособления считается обязательным согласно требованиям техники безопасности. |
Направляющие для подачи металлической черепицы | Самое простое приспособление.![]() |
Работать нужно в обуви с мягкой и нескользящей подошвой, одежда должна быть свободной, не мешать движениям, без свисающих деталей.
Для работы нужно правильно выбирать одежду и обувь
Третий этап – проверка размеров стропильной системы
Еще не поздно устранить проблемы стропильной системы. Вначале следует убедиться, что скаты двускатной крыши прямоугольные. Делается это просто, надо измерить две диагонали, если они одинаковы – все в норме. Если есть разница, то нужно устранять брак. Треугольные скаты должны иметь форму равнобедренных треугольников, проверьте расположение вершины, ее проекция должна располагаться точно посредине.
Проверка геометрии скатов
Одновременно нужно сделать замеры расстояния между рейками обрешетки. Эти параметры зависят от вида металлической черепицы.
Схема шага обрешетки
Первая от карниза доска обрешетки
Расстояние между центрами досок должно быть равным шагу волны металлочерепицы
Шаг обрешетки для металлочерепицы макси
Рекомендуемый шаг обрешетки для металлочерепицы монтерей и супермонтарей
Деревянные элементы стропильной системы рекомендуется обработать антисептиками.
Четвертый этап – кровельные работы
Приступать к ним следует только тщательной подготовки. Надо поинтересоваться прогнозом погоды и выбрать солнечные дни. Особенно это важно, если планируется делать теплую крышу. Минеральная вата быстро намокает и очень долго сохнет. Если неприятность случилась с уже уложенным между стропилами утеплителем, то его придется вынимать. Это не только долго, но и может стать причиной механических повреждений утеплителя.
Кровельными работами, особенно утеплением, стоит заниматься в погожий день
Калькулятор. Толщина утепления ската кровли
Перейти к расчётамУкладку металлочерепицы нужно делать с учетом конструкции крыши, обязательно выполнять все рекомендации производителей и требования строительных норм и правил.
Пятый этап – монтаж водосливной системы
Некоторые элементы водосливной системы следует устанавливать до начала кровельных работ. Конкретный перечень зависит от конструктивных особенностей системы и выбранной технологии монтажа кровли.
После окончания работ обязательно нужно проверить ее работоспособность. Для этого надо выливать на крышу по ведру воды с каждой стороны дома и проверять, какой объем вылился из сливной трубы.
Проверка работоспособности водосточной системы
Должно быть не менее 9,5 литра. Если ее меньше, то это указывает на две проблемы:
- неправильное расстояние между желобом и краем кровли, вода со ската льется мимо желоба. Очень неприятная ситуация, придется полностью переделывать крюки фиксации и изменять положение элемента системы;
Край желоба должен быть на 25-30 мм ниже края металлочерепицы
- держатели расположены не на одной линии, желоб не прямолинейный, а волнистый. В некоторых местах вода не уходит, а застаивается. Этот недостаток не критичен, но и его желательно устранить.
Дело в том, что в этих местах будет накапливаться грязь, потом появятся растения, пропускная возможность системы намного уменьшится.
Крепление водосточного желоба
Обрешётка под металлочерепицу: шаг, монтаж, устройство
Обрешетка под металлочерепицу монтируется с целью придания прочности всей конструкции кровли, а также обеспечения естественной вентиляции под кровельным покрытием. Она является несущим каркасом на который укладываются листы металлочерепицы. Правильно выполненный расчет расстояния между досками и их сечение непосредственно влияют не только на процесс монтажа, но и последующую эксплуатацию всей кровли. Обрешетка для металлочерепицы должна обеспечивать надежное удержание металлических листов во время сильных порывов ветра.Пример обустройства каркаса
Шаг обрешетки под металлочерепицу должен строго соответствовать расстоянию между волнами в зависимости от типа этой продукции.Саморезы, которыми листы металлочерепицы крепятся к элементам обрешетки, по технологии должны фиксировать металл в наиболее жестком месте волны.При монтаже важно, чтобы нижняя часть волны совпадала с расположением горизонтального бруска обрешетки. Именно поэтому точное вычисление расстояния между досками каркаса влияет на качество обустройства кровельного покрытия. Например, при монтаже наиболее популярного типа металлочерепицы Монтеррей, правильно придерживаться шага между центрами обрешетки, размер которого составляет 350 мм. Исключением является укладка второго от нижней части ската бруска, где расстояние должно составлять 300 мм. При монтаже не менее популярного вида металлочерепицы Каскад основной шаг будет составлять 300 мм, но расстояние между первым и вторым рядом обрешетки составит 250мм. А размеры отступа между вторым и третьим рядом обрешетки для кровельной конструкции Каскад – 350 мм. Это обусловлено особенностью фактуры металлочерепицы и размерами волны (высота волны металлочерепицы Каскад составляет 45 мм, а Монтеррей – 39мм).Этим местом является его, так называемое дно, которое расположено практически у основания следующей волны.
Необходимый набор инструментов
Перед тем как сделать обрешетку под металлочерепицу, мастера должны позаботиться о наличии необходимого для этого типа работ арсенала инструментов. К ним можно отнести нижеперечисленные:- Строительный степлер.
- Ножовка по дереву, циркулярная пила или бензопила.
- Молоток или аккумуляторный шуруповерт (при использовании в качестве основ для обрешетки досок, в том случае если их толщина это позволяет, то можно соединения фиксировать саморезами).
- Уровень.
- Строительный маркер и рулетка.
Расстояние между горизонтально укладываемыми досками можно измерять при помощи мерного бруска, длина которого соответствует расстоянию между ближайшими сторонами горизонтально располагаемых брусьев.
Необходимые строительные материалы и «расходники»
Монтаж обрешетки под металлочерепицу должен осуществляться на заранее размещенный слой гидроизоляции и, при необходимости, на конструкцию контробрешетки. Для работ по монтажу несущего каркаса потребуются нижеперечисленные строительные материалы:- Доска сечением 25 (32) мм на 100 мм, или бруски, размеры сторон которых составляют 50 на 50 мм;
- Гвозди, длина которых зависит от толщины используемых досок или брусков. Лучше использовать оцинкованные или медные гвозди, срок службы которых значительно больше.
Пошаговая инструкция
После того как необходимые инструменты и материалы подготовлены, подробная схема монтажа несущего каркаса составлена, а рабочая поверхность очищена от постороннего мусора, следует переходить к установке первой доски.- Установка первой доски обрешетки. Крепить бруски или доски обрешетки кровли необходимо начинать с нижней стороны ската. Для этого необходимо разместить в горизонтальном порядке доску каркаса и прикрепить ее к вертикальной контробрешетке или стропилам крыши при помощи гвоздей и молотка. Каждое место соединения элементов обрешетки с поверхностью крыши или контробрешеткой необходимо укреплять как минимум двумя гвоздями. Расстояние между брусьями обрешетки следует выдерживать в соответствии с техническими характеристиками выбранного вида металлочерепицы.
- Монтаж второго ряда обрешетки. Необходимо помнить, что расстояние между первым и вторым рядом будет отличаться от последующих, на это следует обратить особое внимание, осуществляя расчет.
- Установка последующих рядов. Далее обрешетка под металлочерепицу монтируется со стандартным расстоянием в зависимости от типа металлочерепицы. Используется мерный брусок, толщина которого соответствует размерам досок обрешетки, для того чтобы быстро и комфортно фиксировать последующие ряды.
- На внутренних углах кровли, где планируется своими руками оборудовать ендову, доски основания обрезаются под углом для обеспечения плотного стыка. Также ендову кровли, дымоход или мансардные окна можно оборудовать по периметру сплошной доской.
- Последний ряд обрешетки в области верхнего конька правильно сделать большей ширины. Для этого может использоваться либо более широкая доска, либо при креплении стандартных брусков соединить их вместе, а при необходимости добавить еще несколько рядов для формирования однородной поверхности. Сплошная обрешетка делается для предотвращения прогиба края листа металлочерепицы.
- На последнем этапе осуществляется обрезка краев каркаса, уравнивая тем самым их длину до миллиметра.
Особенности монтажа и дальнейшей эксплуатации кровли
Поскольку устройство обрешетки под металлочерепицу предусматривает высотные работы, то при их выполнении своими руками необходимо позаботиться об индивидуальной безопасности. Следует правильно пользоваться индивидуальной страховкой, подошва используемой обуви не должна скользить. Учитывая тот факт, что используемая древесина после монтажа в большинстве случаев еще содержит определенное количество влаги, по истечении первого года эксплуатации крыши необходимо подтянуть каждый саморез своими руками. Из-за усыхания древесины ее размеры незначительно уменьшаются, соединение кровли ослабевает и существует риск попадания воды на поверхность обрешетки по резьбе кровельного самореза, которыми фиксируются листы металлочерепицы к обрешетке. Расчет необходимого количества составляющих и монтаж обрешетки своими руками является ответственным этапом при оборудовании крыши кровельным покрытием. Любая инструкция по укладке различного вида металлочерепицы, акцентирует внимание именно на качественном и правильном монтаже основания. При этом расчет количества материала для покрытия крыши, размеры элементов обрешетки и всех расстояний должен быть максимально точным, а требования к последовательности работ неукоснительно соблюдены. Например, при монтаже металлочерепицы типа «Каскад» в основном используются бруски с сечением 32 мм на 100 мм. При таких характеристиках элементов основания в среднем для обустройства 1 квадратного метра обрешетки потребуется 3 погонных метра досок. Своими руками такой объем работы выполнить вполне реально, однако, следует учитывать сложность геометрии крыши, размеры скатов и общую площадь. Смотрите видео по теме:Кровля из металлочерепицы: покрытие, расчет, устройство, монтаж
Главная » Крыша » Как сделать крышу из металлочерепицы
Выбор кровельного материала — непростая задача. Надо чтобы крыша была надежной, красивой, долговечной, да еще, желательно, — недорогой. Всем этим запросам отвечает кровля из металлочерепицы. К плюсам ее надо добавить, не самый сложный монтаж, с которым может справиться своими руками даже человек без опыта кровельных работ.
Кровля из металлочерепицы — красива, надежна, долговечна и недорога
Содержание статьи
Виды металлочерепицы
Металлочерепица формуется из листового металла толщиной 0,35-0,7 мм, на который наносят защитные и декоративные составы. Получается многослойный пирог. Основа этого строительного материала — чаще всего стальная, но есть варианты из меди и алюминия. Так как алюминий и медь намного дороже стали, то и изделия из них имеют высокую цену. По этой причине медная или алюминиевая металлочерепицы практически не встречается, но при желании ее могут доставить под заказ.
Есть в продаже как металлочерепица импортного производства, так и отечественного. Европейский вариант идет строго из стали 0,5 мм толщины — это прописано в стандарте. В нашем ГОСТе допускается от 0,45 до 0,5 мм.
Состав металлочерепицы
Кроме разных материалов основы, наносится разное защитное покрытие. В первую очередь есть два типа защиты стали от окисления — цинковое и алюмоцинковое. Второй вариант появился не так давно, но именно он дает более качественную защиту, хоть и стоит такая обработка немного дороже.
Больше разных составов есть для финишного покрытия, то, которое наряду с защитой от атмосферных воздействий придает материалу тот или другой цвет.
Типы защитно-декоративных внешних покрытий
Внешнее покрытие металлочерепицы выполняет одновременно две функции. Оно защищает металл основы от коррозии, и придает материалу привлекательный вид. Есть следующие типы этого покрытия:
- Самая распространенная кровля из металлочерепицы имеет глянцевое полиэстеровое (PE) напыление — около 70% от общего количества крыш, покрыты этим видом материала. Все потому, что имеет он среднюю цену и неплохие характеристики. Толщина слоя 25-30 мкм, срок службы 5-10 лет. Это покрытие стойкое к ультрафиолету и коррозии, но легко повреждается механически — царапины появляются даже при сходе большого количества снега. Потому полиэстеровую металлочерепицу не рекомендуют использовать в регионах с обильными снегопадами. В других областях для предотвращения массового схода снега желательно установить систему снегозадержания. Если будете крыть крышу таким материалом, надо быть осторожным при монтаже.
Крыша из металлочерепицы с покрытием из полиэcтера (PE)
- Матовый полиэстер (MPE) получают при добавлении тефлона. В результате пленка получается более прочной — срок службы 10-15 лет, может использоваться и в снежных регионах. Наносится этот состав толщиной не менее 35 мкм. Недостаток черепицы покрытием из матового полиэстера — меньшая гамма цветов (около 20 оттенков по сравнению с 40 глянцевого).
Матовый полиэстер не дает бликов и служит дольше
- Пластизол (PVC) — состав на основе ПВХ. Имеет красивую структурную поверхность, наносится слоем в 200 мкм, благодаря чему покрытие получается устойчивым к повреждениям. Недостаток -невысокая стойкость к ультрафиолету, что значительно сужает диапазон использования. К тому же в некоторых странах из-за наличия в составе поливинилхлорида данное покрытие запрещено.
Покрытие из пластизола имеет интересную структуру
- Пурал ̵
стоимость работ, технология и расчеты. Монтаж металлочерепицы своими руками :: SYL.ru
Задумались, как сделать внешний вид своего дома более красивым? Тогда следует подготовить себя к работе с кровлей. На сегодняшний день особой популярностью стал пользоваться вопрос о том, как произвести монтаж металлочерепицы. Именно об этом и пойдет речь в данном обзоре.
Правильная укладка металлической черепицы
Как правильно постелить выбранный вами материал? Застройщики нередко задают себе такой вопрос после приобретения современной, практичной и долговечной металлочерепицы. Следует более подробно рассмотреть, что собой представляет монтаж кровли. Кроме этого, в данной статье будет рассказано о том, что такое кровельный «пирог», какими материалами и инструментами потребуется обзавестись, а также о многом другом, что пригодится вам в вашей деятельности.
Основные понятия, характерные для кровли
Что скрывает под собой такой термин, как кровельный «пирог»? Перед тем как начать монтаж металлочерепицы, потребуется разобраться в некоторых понятиях. Данный термин появился во многом благодаря большому количеству слоев, на которые возлагаются самые разные функции. Такая конструкция в случае правильного подбора всех необходимых материалов способна обеспечить не только надежность, но и высокую долговечность всей кровли в целом.
Следует руководствоваться нормативами и правилами
Вне зависимости от того, кто будет производить монтаж металлочерепицы, необходимо осознать, что крыша представляет собой очень сложную конструкцию. Поэтому и сооружать ее требуется при строгом учете всех необходимых рекомендаций от производителей металлочерепицы. Также не стоит забывать про нормативы и правила, характерные для строительной сферы.
Надо все делать грамотно и основательно
Всегда необходимо держать под контролем такой сложный процесс, как монтаж металлочерепицы. Если что-то будет упущено из виду, тогда и последствия могут оказаться достаточно серьезными. Да и проявиться они могут, допустим, только через несколько месяцев. К примеру, если изоляционный материал будет уложен не совсем качественно, то будет появляться конденсат. Ухудшится и такая характеристика, как теплоизоляция. Древесина начнет гнить. Все это приводит к значительному уменьшению долговечности всей кровли в целом. Стоит понимать, что монтаж кровли из металлочерепицы должен происходить при полном соблюдении всех основных правил. Тогда и крыша будет радовать владельцев своим прекрасным внешним видом долгий период времени.
Основные этапы проектирования крыши
Создание кровли из металлочерепицы должно происходить в определённой последовательности.
- Создание стропильной системы.
- Проектирование контрреек.
- Укладка гидроизоляционной пленки.
- Создание вертикальной обрешетки посредством использования брусьев.
- Установка начального бруска для горизонтальной обрешетки.
- Установка всех оставшихся брусков для горизонтальной обрешетки.
- Проектирование дополнительной обрешетки.
- Установка ветровой доски.
- Монтаж кронштейна для желоба.
- Установка планки для карниза.
- Укладка металлочерепицы.
- Проектирование конька кровли.
- Создание уплотнителя для конька.
- Монтаж слухового окна.
- Укладка теплоизоляции.
- Укладка пароизоляции.
- Обшивка мансарды.
Какие инструменты понадобятся?
Для того чтобы монтаж кровли из металлочерепицы прошел качественно, потребуется запастись некоторыми основными инструментами. Среди них можно выделить перечисленные ниже.
- Ножницы, с помощью которых будет разрезаться метал.
- Ножовка по металлу, имеющая мелкие зубья.
- Просечные ножницы для работы с металлическими изделиями.
- Насадка на дрель, позволяющая работать с металлом.
- Ножницы электрические, высечные.
- Дисковая пила.
- Болгарка и абразивный круг для нее.
Также потребуется шуруповерт, молоток не слишком большого размера, рейка для прочерчивания ровных линий, маркер. После того как все работы по обрезке листа будут закончены, потребуется с особой тщательностью избавиться от опилок металлического характера. В противном случае они, поржавев со временем, нарушат структуру полимерного покрытия.
Что требуется знать?
Производя монтаж крыши из металлочерепицы своими руками, следует помнить, что нельзя резать листы посредством использования абразивных кругов. В противном случае при температурных перепадах будет разрушаться не только полимерный слой, но и покрытие из цинка. В результате ничего хорошего не получится. При бурном процессе ржавления на крыше начнут появляться соответствующие, не слишком приятные для глаза, потеки.
Как произвести расчет шага стропил?
Когда будет формироваться кровля из металлочерепицы своими руками, монтаж и расчеты будут играть очень важную роль. Следует понимать, что шаг тех стропил, на которых будет крепиться материал, должен находиться в диапазоне от 550 до 900 мм. Знайте, что если уже были закуплены плиты для теплоизоляции, то и шаг стропил требуется выбирать, руководствуясь их размерами. Ведь в дальнейшем утеплитель надо будет монтировать между стропилами кровли. Брус, сечение которого составляет 150х50 мм, является оптимальным вариантом для создания стропил. После их установки потребуется сделать все необходимее замеры будущих скатов. Допустимы не слишком большие отклонения — до 10 мм. Скрыть их впоследствии можно будет с помощью доборных элементов.
Какая длина должна быть у листов?
Технология монтажа металлочерепицы подразумевает, что скат должен обладать уклоном более 14 градусов. Для того чтобы определить длину листов, следует руководствоваться длиной ската. Измерять её нужно, начиная с конька и до карниза. При этом следует учесть карнизный свес, длина которого не должна быть меньше 40 мм. В том случае, если скат превышает 6 метров, и материал надо будет разбивать как минимум на два куска. Укладка их впоследствии должна производиться вперехлест, с напуском 150 мм. Длинные листы образуют наименьшее количество стыков, однако и укладывать их намного труднее.
Утеплитель также требуется защитить
Для того чтобы предотвратить промерзание крыши в холодные периоды времени, необходимо выбирать утеплитель должной толщины. Кроме того, схема монтажа металлочерепицы подразумевает использование обязательной защиты утеплителя, которая крепится со стороны МЧ за счет использования гидроизоляционной пленки. Пленочная пароизоляция будет защищать утеплитель со стороны комнат. Чтобы влага в подкровельном пространстве не скапливалась, необходимо проектировать естественную вентиляцию. Чтобы сделать ее, надо оставить немного свободного пространства между МЧ и гидроизоляционной пленкой с помощью обрешетки. Потребуется также оставить щели на карнизных свесах. В резиновом уплотнителе, который крепится на коньке, следует освободить специальное отверстие.
Монтаж металлочерепицы своими руками — пошаговая инструкция по монтированию кровли, с фото и видео
Необходимость надёжного и качественного перекрытия сооружений различного назначения является аксиомой. Застройщики все чаще предпочитают металлочерепицу, в замену классическому шиферу и оцинкованной жести. С виду сложная укладка материала, доверяемая специалистам, может быть успешно выполнена самостоятельно с подсобниками из числа родственников и хороших знакомых. Желание, азарт, наличие необходимых инструментов должны базироваться на определённых теоретических знаниях для получения, ожидаемого от работы результата. Теоретические моменты и полезные советы представлены в этом материале.
Преимущества и недостатки покрытия
В пользу выбора металлочерепицы можно привести такие качества кровельного материала:
- экологичность – в составе отсутствуют вредные вещества и составы;
- небольшой вес – 3,6-5,2 кг/м2;
- отличная прочность, достигаемая наличием конструктивных рёбер жёсткости, придаёт правильно установленному листу металлочерепицы с толщиной 0,5 мм способность устоять при нагрузке более 200 кг/м2;
- монтаж и ремонт кровли не отличается сложностью;
- пожарная безопасность;
- эстетичный классический вид с широкими возможностями выбора материала различной толщины, профиля, защитного покрытия и цвета;
- минимальное линейное расширение под действием температуры и высокая устойчивость к её перепадам.
Выбирая материал нужно знать и его недостатки. У металлочерепицы это:
- Склонность к образованию на поверхности листа конденсата от разницы температур наружного воздуха и чердачного помещения. Для материала, основой которого является металл, это может стать причиной коррозионных процессов.
- Шумность при попадании на неё атмосферных осадков (дождя, града) и от контакта с раскачиваемыми ветром ветками деревьев.
Обе проблемы значительно сглаживаются обязательным утеплением кровли со стор
Услуги по установке металлической кровли «Сделай сам и сделай для вас»
Услуга «Сделай сам и сделай для вас» Услуга по установке металлической кровлиЗапрос цитаты
Начните планировать крышу своей мечты сегодняПожалуйста, заполните поля, отмеченные красным
У кровли своими руками много преимуществ, самое главное, она сокращает расходы, связанные с новой кровлей. установка и дает вам лучшее представление о состоянии вашей крыши в целом.Хотя негативы заключаются в том, что, будучи неопытным установщиком кровли, вы потенциально можете столкнуться с проблемами при установке металлических крыша.
Зачем это делать самому?
Когда вы покупаете комплект для металлической кровли своими руками, вы получаете все по цене. Если вы работаете над небольшим бюджет, это идеально. Укладка металлической кровли относительно проста, а сами материалы легко транспортировать. Если вам комфортно работать с металлом, это может быть интересный проект с большим количеством награда в конце.В качестве кровельного материала металл высокого качества, отлично смотрится и прослужит вам лет пятьдесят или Больше. Существует множество вариантов цвета и профилей, и мы можем помочь вам, когда дело доходит до установки. Для работы вам потребуются только подходящие инструменты! Опять же, в конце дня, если вы не чувствовать себя комфортно, устанавливая металлическую крышу самостоятельно, обратитесь к кровельщику за консультацией и узнайте, подходит ли вам DYI ..
СОЗДАЕМ ДЛЯ ВАС НАБОР!
Стандартный комплект для сборки состоит из 250 панелей, площадь которых составляет около 3000 квадратных футов.
Каждая крыша отличается размером и дизайном.Вот почему мы создаем для вас индивидуальный комплект для металлической кровли. Получите все материалы, необходимые для правильной установки крыши, включая все, от кровельных панелей до винты вам нужны. Кроме того, мы можем даже отрегулировать размер металлических кровельных панелей, чтобы они соответствовали вашему строению. установка требует. Если у вас есть вопросы по установке, вы можете позвонить нам. Обратите внимание, с Что касается панелей, наш стандартный кровельный комплект DIY включает 250 панелей, которые покрывают примерно 3000 квадратный фут.В зависимости от того, нужно ли вам больше или меньше, можно внести корректировки.
Самовывоз и доставка
После того, как вы решили купить металлический кровельный комплект своими руками, у вас есть два варианта: самовывоз или доставка. Доставка возможна в рабочее время с понедельника по пятницу. Мы также открыты Суббота для тех, кто ищет проекты выходного дня. Заказчик может зайти на любую нашу продукцию места и возьмите в руки все, что им нужно, чтобы приступить к их установке.В качестве альтернативы, если доставка менее сложна или более удобна, ваш комплект может быть доставлен к клиенту.
Выбор цвета и материала
Одним из больших преимуществ выбора металла в качестве кровельного материала является количество цветов и стилей, которые вы получаете. выбирать из. Независимо от того, выбрали ли вы сталь или алюминий, выберите один из нескольких цветов и настройте его. в соответствии с желаемым внешним видом или внешним видом того, что окружает ваш дом.Обуздать апелляцию в этот день и возраст, что способствует общей стоимости вашего дома. Обязательно выберите то, что представляет вас и ваш район лучший. Обратите внимание: выбор цвета не влияет на огнестойкость металла или способность кровельных панелей работать в суровых погодных условиях. Когда дело доходит до выбора цвета, это все о взгляде — не о производительности.
Принадлежности для установки
Посмотреть / скачать PDF-файл с принадлежностями для установки — Большой файл.
Вы также найдете чертежи, поясняющие, как устанавливаются эти аксессуары.
КРОВЕЛЬНЫЙ ИНСТРУМЕНТ
Независимо от того, являетесь ли вы профессионалом или энтузиастом-домовладельцем, вам нужны подходящие инструменты для работа
Мы можем помочь, когда дело доходит до инструментов, необходимых для установки металлической крыши в вашем доме.Есть три варианта вы выбираете из
- Получите список инструментов, необходимых для установки крыши, и вы можете приобрести их самостоятельно в любом оборудовании. магазин..
- Купите кровельный инструмент прямо у нас. Сделать это можно в одном из наших салонов.
- Если вы купили у нас кровельные инструменты и пока они не повреждены, мы выкупим их обратно. от вас после завершения установки.Некоторые клиенты предпочитают этот вариант, поскольку он сводит к минимуму их стоимость. Тем не менее, если вам понадобится выполнить техническое обслуживание или ремонт в будущем, вы можете оставить свой кровельный инструмент.
Из них мы рекомендуем покупать инструменты непосредственно у нас. Таким образом, вы знаете, что у вас есть все необходимое выполнить свою работу и у вас не будет никаких догадок относительно того, как использовать тот или иной инструмент или как он применим к вашим монтажные материалы. Мы предоставляем лучшие инструменты и советы, так как наши бригады используют эти инструменты для установки крыш. повседневная.
Другие услуги
Помимо того, что мы специализируемся на наборах материалов для металлической кровли своими руками, у нас также есть ряд других продуктов и услуг. может быть интересно:
- Плоский прокат.
- Рулоны алюминия и стали производства Канады и Европы.
- Материалы гибки по индивидуальному заказу.
Для получения более подробной информации по конкретному запросу на материал или услугу, пожалуйста, свяжитесь с представителем, который может предоставить вам следующий шаг!
ECO-TILE (однопанельная) — пример профиля, предназначенного для разнорабочих.Эти небольшие панели легко транспорт и установить. Они идеально подходят для домов, коттеджей, сараев, скатных крыш и других подобных работ.
Мы стараемся предлагать новые инновационные продукты и решения, а также предлагаем специальные предложения и скидки на кровельные продукты. или аксессуары.
Финансирование
London Eco-Metal предоставляет финансирование для самостоятельных проектов. Все финансирование подлежит одобрению кредита. Позвоните нам, чтобы поговорить с одним из наших специалистов по кровле по поводу вашего проекта DIY и финансирования.
Семинары
Если вы заинтересованы, вы можете перейти на страницу семинаров и заполнить форму заявки на сеанс DIY. Место для семинаров ограничено, они будут предлагаться либо на начальном, либо на продвинутом уровне и будут проводиться по субботам с 9:00 до 13:00 на нашем заводе в Дорчестере — 531 Shaw Road. Перейдите на страницу контактов, чтобы увидеть точное местоположение
Торговые точки / выставочные залы
Мы в восторге от торговых точек компании, подразделения London Eco-Metal Manufacturing Inc.
Мы работаем как универсальный магазин для всех, от человека, который делает все, до опытных профессиональный. В наших магазинах установлены крупномасштабные дисплеи, позволяющие покупателям понять, что готовая крыша будет выглядеть. Дисплей является интерактивным, что позволяет клиенту фактически прикоснуться к кровле. материалы.
London Eco-Metal может предоставить вам расходные материалы для любой работы и любого бюджета. Кроме того, в наших выставочных залах работают дружелюбные и знающие сотрудники, которые всегда готовы ответить на ваши вопросы.Наши сотрудники также смогут предоставить вам информацию о мансардных окнах и солнечных батареях. Если он идет на крышу вашего дома, вы найдете его в наших выставочных залах.
Все местоположения указаны на странице контактов, включая карту адреса и контактные телефоны.
Вы также можете посетить веб-сайт Eco-Metal Express для Дополнительная информация.
ГОЛОВНОЙ ОФИС И ПРОИЗВОДСТВО ЮГО-ЗАПАД ОНТАРИО
ЛОНДОН / ДОРЧЕСТЕР531 Shaw Road
Дорчестер, Онтарио, Канада
N0L 1G4
Телефон: 519-451-7663
Факс: 519-451-7669
Бесплатная линия: 1-855-838-9393
Часы работы:
ПРОИЗВОДСТВО
ВОСТОК
ONTARIO
ОТТАВА 960 гл.Burton Road
Варс, Онтарио, Канада
K0A 3H0
Телефон: 613-443-9393
Факс: 613-443-9399
Бесплатная линия: 1-844-778-9393
Часы работы:
НАШ
ВЫСТАВОЧНЫЙ ЗАЛ
МЕСТА
ЛОНДОН 531 Shaw Road
Дорчестер, Онтарио, Канада
N0L 1G4
Телефон: 519-659-3224
Часы работы:
1759 Britannia Rd.E. Блок № 6/7
Миссиссауга, Онтарио,
L4W 4E1
Телефон: 905-564-7663
Бесплатный звонок: 1-833-377-9393
Часы работы:
960 гл.Burton Road
Варс, Онтарио,
K0A 3H0
Телефон: 1-613-443-9393
Бесплатный звонок: 1-844-778-9393
Часы работы:
Обзор обшивки из медно-никелевого сплава для корпусов судов и морских сооружений
Дейл Т.Петерс, Технический отчет семинара Ассоциации разработчиков меди 7044-1919; Применение медно-никелевых сплавов в морских системах; 1992
Обшивка корпуса корабля
Фон
Морские инженеры веками искали эффективные и экономичные средства защиты корпусов судов и морских конструкций от разрушительного воздействия морской воды и морской флоры и фауны. Корабли с деревянным корпусом обшивали свинцом бродячие прибрежные торговцы во времена Александра Великого. Свинец, как и медь, противостоит росту биообрастания.
Британское Адмиралтейство использовало листы меди, прибитые к деревянным кораблям, начиная с фрегата Alarm в 1761 году, для защиты от червей и обрастания. Гальваническая коррозия железных креплений и болтов привела к потере меди и ослаблению кораблей. Только в 1780-х годах с появлением медных застежек медная оболочка стала популярной. С появлением стальных корпусов медная обшивка уступила место необрастающим краскам на медной основе.
Идеальный материал корпуса для кораблей различных размеров и функций был предметом интенсивных исследований, и различные материалы корпуса используются или оцениваются.Медно-никелевый сплав в качестве материала корпуса впервые был использован еще в 1941 году при постройке Miss Revere, 13,7-метровой яхты с медно-никелевым корпусом толщиной 2 мм. Медно-никелевый сплав в качестве материала корпуса впервые был использован в середине 1960-х профессором Университета Алабамы после того, как он провел обширное исследование широкого спектра возможных материалов корпуса для своей яхты Asperida. Он искал материал с наилучшим сочетанием устойчивости к коррозии и биологическому обрастанию. Сплав C71500, медь-никель 70-30, был выбран вместо медно-никелевого сплава C70600 90-10, потому что большая прочность была преимуществом в его конкретной конструкции.
Это непосредственно привело к серии инженерных исследований Международной ассоциации исследователей меди (INCRA — теперь Международная ассоциация меди), International Nickel Company и Copper Development Association Inc., а также к строительству в 1971 году Copper Mariner ( Рисунок 1 ), промысловый креветочный траулер длиной 20,4 м с медно-никелевым корпусом. Основная цель заключалась в том, чтобы определить, обеспечит ли присущая сплаву C70600 устойчивость к биообрастанию и коррозии достаточную экономию топлива и техническое обслуживание, чтобы оправдать надбавку к стоимости медно-никелевого корпуса.
Рисунок 1 — Креветочный траулер, Copper Mariner
Copper Mariner был описан в другом месте (2) и не будет здесь подробно описываться. Этот траулер имеет корпус из сплава С70600 толщиной 6 мм, приваренный к стальному каркасу. Copper Mariner продемонстрировала рентабельность инвестиций в диапазоне от 12,9 до 16,7 процента после уплаты налогов за операции креветочного траулера у побережья Никарагуа. Эти цифры основаны на измеренных расходах на топливо и техническое обслуживание, а также на оценках увеличения потенциальной прибыли этой лодки благодаря дополнительным дням доступности по сравнению с аналогичными лодками со стальным корпусом.
Скорость коррозии корпуса была меньше 0,00125 мм / год, о которой сообщалось при длительном воздействии C70600 (3) . Интересно, что измерения толщины листа корпуса после 52 месяцев эксплуатации показали отсутствие различий в потерях металла в зонах термического влияния корпуса, где произошло повторное растворение осажденного железа, по сравнению с горячекатаным листом с осажденным железом. Большая часть корпуса была покрыта пленкой продуктов коррозии темного цвета; зоны термического влияния имели светло-золотистый цвет.Скорость Copper Mariner находится в диапазоне 4-10 узлов.
Медно-никелевый корпус Copper Mariner очень устойчив к обрастанию (, рис. 3, ). Сравнение со стальным корпусом аналогичного судна непосредственно перед его третьей очисткой после 18 месяцев эксплуатации поразительно (, рис. 2, ).
Рис. 2 — Морское обрастание лодки со стальным корпусом, Jinotega, перед третьей очисткой после 18 месяцев эксплуатации
Рисунок 3 — Copper Mariner не имеет обрастания
Copper Mariner исполнилось 20 лет в этом году † .Он все еще находится в эксплуатации, и, по последним словам министра национальной рыбной промышленности Никарагуа, медно-никелевый корпус никогда не нуждался в обслуживании. Осмотр корпуса в сухом доке для обслуживания гребного винта и вала не выявил заметных признаков общей или точечной коррозии. Четыре аналогичные лодки с корпусом из сплава С70600 толщиной 4,8 мм были построены в начале 1970-х годов для службы в Шри-Ланке.
Несколько очень успешных кораблей с медно-никелевым корпусом были построены с использованием композитного материала из медно-никелевого сплава 90-10, плакированного на стали.Второй креветочный траулер Copper Mariner II был построен в 1976 году с листом корпуса из стали толщиной 8 мм, плакированной 25% сплава C70600. Этот корпус продемонстрировал технологичность и свариваемость с использованием плакированного материала и методов сварки, описанных Prager et. al. (4) . Совсем недавно министерство внутренних дел Италии закупило несколько пожарных катеров для порта в Неаполе и других местах. Эти лодки имеют корпуса из 2 мм сплава 90-10, плакированного медно-никелевым покрытием на 6 мм стали, длиной 22,56 м и водоизмещением 72 тонны.Эти медно-никелевые корпуса обеспечивают максимальную доступность пожарных катеров, устраняя необходимость в обслуживании корпуса любого вида.
Два лоцманских катера с металлическим корпусом были построены в 1987 году для Управления навигации Финляндии. Эти две лодки были запланированы для сравнения аустенитной нержавеющей стали и медно-никелевой стали 90-10 для использования в Балтийском море, где лед является серьезной проблемой. Обе лодки, как сообщается, работают хорошо.
Две известные лодки были построены в Японии.Хотя у нас нет подробностей, нам сообщили о яхте Akitsushima, построенной Furukama Electric Co., Ltd., с медно-никелевой оболочкой толщиной 4 мм, приваренной к стальному корпусу. Сообщалось, что в 1989 году эта лодка пересекла Тихий океан в Викторию, Британская Колумбия, Канада. Корпорация NKK сообщила о строительстве экспериментального корабля Cupro со стальным корпусом, плакированным медно-никелевым покрытием. Эти японские корабли представляют большой интерес, и нам было бы очень интересно узнать об их характеристиках и деталях конструкции.Сводная информация о судах, построенных на сегодняшний день с медно-никелевым корпусом, представлена в Таблице 1 . Эта концепция привлекла значительное внимание небольших коммерческих судов, но судно длиной более 25 м построено не было.
† Статья написана в 1991 г.
Емкость | Длина корпуса (м) | Спущен на воду | Построен | Толщина (мм) | Эксплуатация |
---|---|---|---|---|---|
Мисс Ревер | 13.7 | 1941 | США | 2 | – |
Асперида II | 16 | 1968 | Голландия | 4 | США |
Илона | 16 | 1968 | Голландия | 4 | Кюрасао |
Медный порт | 22 | 1971 | Мексика | 6 | Никарагуа |
Розовый лотос | 17 | 1975 | Мексика | 4 | Шри-Ланка |
Розовый жасмин | 17 | 1975 | Мексика | 4 | Шри-Ланка |
Розовая роза | 17 | 1975 | Мексика | 4 | Шри-Ланка |
Pink Orchard | 17 | 1975 | Мексика | 4 | Шри-Ланка |
Медь Марина II | 25 | 1977 | Мексика | 6 + 2 * | Никарагуа |
Зиглинде Мари | 21 | 1978 | UK | 6 | Великобритания / Карибский бассейн |
Pretty Penny | 10 | 1979 | UK | 3 | UK |
Sabatino Bocchetto | 21.5 | 1984 | Италия | 6 + 2 * | Италия |
Романо Росати | 21,5 | 1984 | Италия | 6 + 2 * | Италия |
Альдо Филиппини | 21,5 | 1987 | Италия | 6 + 2 * | Италия |
Пожарный катер VF544 | 21,5 | 1897 | Италия | 6 + 2 * | Италия |
Лоцманский катер | 14.4 | 1988 | Финляндия | 7 + 2,5 * | Балтика |
Акицвусима | NA | 1989 | Япония | сталь + 4 ** | Япония |
Купро | NA | 1991 | NKK Япония | 4,5 + 1,5 * | Верфь Асано |
* Стальная пластина, плакированная медно-никелевым покрытием ** Стальной корпус в медно-никелевой оболочке NA = недоступно |
Облицовка и оболочка
Очевидно, что для больших судов цельные медно-никелевые корпуса нецелесообразны.Практические способы облицовки стали медно-никелевым покрытием включают как плакировку, так и оболочку. Под плакированием мы подразумеваем композиционный материал, имеющий металлургическую связь между сталью и медно-никелевым сплавом. Как горячее соединение валков, так и формование взрывом были использованы для создания этого металлургически надежного интерфейса. Обшивка относится к прикреплению относительно тонкого медно-никелевого листа к корпусу с помощью сварки или использования клея. Таким образом, обшивка применима как для модернизации существующих судов, так и для новой постройки.Обшивка, с изоляционным слоем между медно-никелевым покрытием и без него или без него, также применима к морским нефтегазовым сооружениям, а также к широкому спектру мостов, доковых конструкций и систем забора морской воды на энергетических или химических заводах для защиты от коррозии защита и предотвращение биообрастания. Обшивка из медно-никелевого сплава является основным направлением этой статьи из-за ее очевидной относительно привлекательной экономики, а также ее гибкости и применимости к широкому спектру морских конструкций в дополнение к корпусам судов.
Как отмечалось в начале этой статьи, обшивка — это старая концепция. Медно-никелевый сплав в качестве материала корпуса судна, как было подтверждено на опыте многих небольших судов, построенных на сегодняшний день, действительно, как было заявлено, обеспечивает защиту от коррозии и устраняет засорение корпуса, что способствует снижению требований. Но эти концепции еще не были объединены на большом океанском судне, чтобы получить преимущества, наблюдаемые при применении концепции к меньшим судам. Это может быть связано с тем, что ряд технических и экономических вопросов остаются нерешенными в сознании членов судостроительного сообщества.
Мы рассмотрим два часто возникающих вопроса, связанных с коррозионным поведением медно-никелевых корпусов судов, а именно эрозионно-коррозионную способность медно-никелевых сплавов и вероятные последствия гальванической коррозии стального корпуса в случае повреждения. к ножнам. Более сложный вопрос экономики жизненного цикла оболочки будет проанализирован для конкретного корабля. Рассмотрены результаты исследования методов обшивки и стоимости больших судов, использованных в данном анализе.Судостроительная компания США будет пересмотрена.
Оценка морской службы
Эрозия-коррозия медно-никелевого сплава и вопрос ограничения скорости
Copper Mariner и многие другие суда, перечисленные в Таблице 1, имеют максимальную скорость в диапазоне 10-12 узлов (5-6 м / с). Несомненно, сплав C70600 продемонстрировал превосходную коррозионную стойкость как к точечной коррозии, так и к эрозии-коррозии в морской воде при таких скоростях на корпусах этих судов. Оставалось продемонстрировать, что сплав C70600 имеет адекватный допуск на скоростях в диапазоне 25 узлов (12.5 м / с) требуется для крупных танкеров или грузовых судов. Хотя максимальная скорость, рекомендованная для трубы диаметром 100 мм и более, составляет 3,5 м / с, были указания на то, что скорость коррозии в трубах очень большого диаметра или на по существу плоской геометрии пластин корпуса судна может быть вполне приемлемой при очень больших расстояниях. более высокие скорости.
Эксперименты на больших кораблях были выполнены, чтобы попытаться напрямую оценить этот эффект скорости (5) . Во-первых, полный руль был обшит и установлен на Великой Земле, 24-узловом судне катания / откатывания.Руль направления — это область сложного и турбулентного течения. Испытания показывают, что сплав C70600 и сплав Cu-Ni-Cr C72200 чрезвычайно долговечны даже в условиях залива Кука у побережья Аляски, где в воде встречаются лед и абразивный ил. Руль направления с оболочкой из медно-никелевого сплава площадью 74 м2 показан на Рис. 4 .
Рисунок 4 — Руль Великой Земли в медно-никелевой оболочкеСкорость коррозии определялась путем измерения толщины оболочки через интервалы от нескольких месяцев до 14 месяцев эксплуатации.Потеря толщины во многом зависела от положения руля направления, как и следовало ожидать, но ни в одном из положений уменьшение толщины не превысило 0,1 мм за 14-месячный период испытаний. Что еще более важно, средний уровень потерь уменьшался со временем, как показано на Рисунок 5 . Средняя скорость коррозии менее 0,025 мм / год в течение 14 месяцев наблюдалась для обоих сплавов. Это означает, что на обшивке руля направления образовывалась устойчивая защитная пленка, предотвращающая потенциально катастрофические высокие скорости коррозии, которые некоторые люди считали возможными в этом турбулентном режиме с высокой скоростью.
Средний уровень потерьмил / год
Время (месяцы после поставки)
Рисунок 5 — Средняя скорость коррозионных потерь в зависимости от времени для медно-никелевой оболочки Великой ЗемлиПоскольку гальваническое взаимодействие между корпусом Great Land и его обшитым рулем направления могло повлиять на результаты коррозии, испытания были проведены с медно-никелевыми панелями, прикрепленными к корпусу и рулю, но электрически изолированными от них. Панели с открытыми поверхностями 250 x 125 мм, изолированные тефлоном и эпоксидной смолой (, рис. 6, ), были собраны и прикреплены к кораблю в четырех местах 4.6 м ниже ватерлинии. Измерения показали, что некоторые панели частично заземлены на корпус, а это означает, что в этих случаях абсолютное значение скорости коррозии, вероятно, ниже, чем было бы, если бы изоляция оставалась неповрежденной. Результаты, полученные путем измерения толщины, не показали значительной разницы в скорости коррозии панелей в различных местах корпуса. Панели руля показали более высокую скорость эрозии и коррозии, чем панели корпуса (менее чем в 2 раза), и скорость была выше на изолированных панелях руля, чем на соответствующих испытательных участках с кожухом руля.Катодная защита обшитого корпусом руля направления снизила скорость коррозии примерно в три раза, как показано здесь:
Скорость потерь (мм / год) | ||
---|---|---|
Сплав | Резиновая оболочка | Изолированные панели на руле |
C70600 | 0,02 | 0,08 |
C72200 | 0,04 | 0,10 |
Рисунок 6 — Схема метода изоляции и крепления медно-никелевых панелей к корпусу Great Land.
Cr-содержащий сплав C72200 неизменно показывает несколько более высокую скорость коррозии. Это было не так, как ожидалось, и нет уверенности в том, что наблюдаемая разница является значительной. Данные о скорости коррозии для изолированных панелей показали определенную тенденцию к снижению со временем, что снова указывает на формирование стабильной защитной пленки в течение 14-месячного периода испытаний. Скорости имеют тенденцию к значениям от 0,02 до 0,1 мм / год (и предположительно ниже, если измерения после более длительного времени воздействия были возможны), что было бы вполне приемлемо в этом приложении.
На основании этих наблюдений считается, что 12,5 м / с (24 узла) ниже скорости отрыва для медно-никелевых сплавов в условиях корпуса судна. Следует отметить, что скорость отрыва, определенная испытанием на удар струей в лаборатории для сплава C70600, составляла приблизительно 5 м / с (10 узлов). Не исключено, что различия в лабораторных результатах и результатах по корпусу корабля можно объяснить такими факторами, как:
- Прерывистый поток на корпусе корабля по сравнению с непрерывным воздействием в лаборатории;
- Различия в гидродинамических условиях потока в двух ситуациях; и
- Различия в растворенном кислороде и температуре морской воды в лаборатории по сравнению с фактическими условиями воздействия на корпус.
Независимо от того, какой фактор или факторы преобладают, считается, что панельные испытания лучше предсказывают фактические характеристики корпуса, чем лабораторные испытания, поскольку панели корпуса дублируют фактические условия эксплуатации судна.
Способы крепления оболочки
В начале 1980-х годов был проведен еще один эксперимент с панелями корпуса для проверки методов крепления и, опять же, для оценки характеристик медно-никелевых панелей на корабле, находящемся в эксплуатации. (6) .Группа панелей была прикреплена к корпусу танкера для перевозки сырой нефти Arco Texas во время постройки этого корабля в Newport News Shipbuilding, Inc. Это судно было спроектировано и фактически является самым большим танкером для сырой нефти, способным перевозить сырую нефть. проход через Панамский канал. Хотя изначально это и не входило в план воздействия, серьезное истирание и ударные нагрузки, сопутствующие проходу через канал, обеспечили реалистичную, возможно, «наихудшую» испытательную ситуацию.
Двенадцать медно-никелевых панелей, каждая 0.9 x 3 м и 3 мм толщиной были разделены на четыре комплекта по три для установки на корпусе рядом с легкой грузовой маркой, как показано на рис. 7 . Таким образом, панели были подвергнуты воздействию полностью погруженных в воду, попеременно влажно-сухих условий и зон брызг. Одна группа была прикреплена периферийной сваркой с использованием электродов ENiCu-7 SMAW, усиленных путем приклеивания к корпусу эпоксидной смолой Boskik M-890. Вторая группа была прикреплена периферийной сваркой без внутреннего усиления. Третья группа использовала периферийную сварку, усиленную эластомерным клеем 3M XB-5354.Последняя группа была прикреплена с помощью периферийных сварных швов, поддерживаемых массивом сварных швов, расположенных на одинаковом расстоянии друг от друга по лицевой стороне каждой панели.
Рисунок 7 — Расположение медно-никелевых панелей на Арко ТехасПосле двух лет эксплуатации в широком спектре морских условий эксплуатации, включая теплые воды Персидского залива, несколько поездок через Панамский канал и воды Западного побережья от Южной Калифорнии до Аляски, все панели были целы. Все панели и сварные швы плотно прилегали к корпусу и не протекали.По большим показаниям было доказано, что эпоксидные и эластомерные клеи в некоторой степени расслоились во время эксплуатации. Таким образом, эти формы усиления не рассматривались. На некоторых панелях были довольно серьезные царапины и вмятины от контакта с берегами канала, доками или буксирами. Измерения толщины до и после обслуживания показали, что потери от коррозии составляют менее 0,025 мм, что соответствует максимальной скорости коррозии менее 0,0127 мм в год. Судя по всему, коррозионная стойкость панелей намного превышает срок службы судна.
Никаких следов биообрастания на медно-никелевых панелях по прошествии двух лет не обнаружено. Тот факт, что медно-никелевый сплав оставался противообрастающим, означает, что он также подвергался быстрой коррозии в течение этого периода, хотя и с очень низкой скоростью. Следовательно, панели не могли быть обеспечены значительной катодной защитой со стороны окружающего стального корпуса, и они не могли способствовать коррозии стального корпуса, даже несмотря на то, что система окраски корпуса непосредственно вокруг панелей, отремонтированная после установки, в некоторой степени вышла из строя. .На корпусе образовались обрастания, и через два года на нем было много водорослей, длиной в несколько дюймов.
Повреждение обшивки / обшивки и гальваническая коррозия корпуса
Вопрос о быстрой и потенциально опасной коррозии стального листа корпуса в случае повреждения медно-никелевой оболочки или оболочки был поднят с тех пор, как впервые были введены концепции облицовки и оболочки. Средний потенциал свободной коррозии стали аноден по сравнению с медно-никелевым примерно на 300 мВ.Дродтен и Пирчер из Thyssen Steel AG в Германии провели испытания для оценки этой проблемы, установив медно-никелевую оболочку на стальные испытательные образцы в зоне погружения испытательного стенда на острове Гельголанд и на корпус морского буксира (7). .
Испытательные образцы были смонтированы так, чтобы быть электрически изолированными от стального испытательного стенда или корпуса буксира. Отверстия и щели были обработаны через медно-никелевый сплав, чтобы обнажить сталь, чтобы обеспечить различные размеры дефектов и диапазон соотношений площадей катода и анода.Были выставлены и бездефектные образцы. Было обнаружено, что они не имеют ржавчины и загрязнений после воздействия. Буксир эксплуатировался в устье реки Эмс и в течение периода холодной зимы 1986-87 гг. Также использовался для разрушения льда. Тестовые пластины оценивались в сухом доке с интервалом в несколько месяцев. Отдельные образцы были удалены для лабораторного исследования и добавлены новые. Некоторые образцы подвергались воздействию в течение всего периода испытаний, составлявшего 16 месяцев.
Образцы для испытаний с более крупными дефектами, такими как щели 5 x 100 мм2, были обнаружены после трех месяцев выдержки с обильной ржавчиной и загрязнением.Из-за катодной поляризации медно-никелевого сплава, вызванной обнажением стали на щели, стойкость медно-никелевого сплава к загрязнению, как и ожидалось, была потеряна. Поперечное сечение корродированного щелевого дефекта показало, что сталь подверглась коррозии примерно вдвое большей ширины щели в медно-никелевой оболочке.
После 4,5 месяцев эксплуатации на испытательных образцах не было сильной ржавчины и загрязнения. И снова образцы для испытаний были удалены и разрезаны на корродированный дефект в медно-никелевом элементе.Обнаружены явные различия в глубине коррозии и поднутрении в зависимости от размера дефекта. Дефекты диаметром 5 и 10 мм показали глубину коррозии около 6-7 мм. А вот при диаметре дефекта 50 мм глубина коррозии составляла всего 1,5-2 мм.
Спустя еще восемь месяцев испытания буксира были завершены, и все испытательные образцы были исследованы в лаборатории. Были измерены глубина коррозии и поднутрение. На самом медно-никелевом покрытии после 18 месяцев эксплуатации судна не наблюдалось уменьшения толщины, вызванного коррозией, эрозией или истиранием.Исходные поверхности с неглубокими бороздками от пробоподготовки практически не изменились.
В Гельголанде образцы для испытаний были подвергнуты однолетнему непрерывному воздействию в зоне погружения без промежуточных исследований. При удалении на поверхности обнаружены легкие обрастания ракушек. Поверхность более крупных дефектов имела плотный морской рост и была покрыта темными продуктами коррозии.
Измеренные скорости коррозии и значения плотности анодного тока, рассчитанные по закону Фарадея, нанесены на график , рис. 8, в зависимости от отношения площадей.Влияние отношения площадей Sc / Sa безошибочно. Скорость коррозии увеличивается до предельного значения примерно Sc / Sa = 140. Скорость коррозии образцов для испытаний буксира зимой выше, по-видимому, из-за более высокого уровня кислорода в более холодной морской воде. Зимой вода в устье реки Эмс содержит 11-13 частей на миллион кислорода при температуре около 0 ° C и только около 5 частей на миллион при температуре воды 18-20 ° C летом. Скорости коррозии находятся почти в том же соотношении, что и сезонный уровень кислорода, что позволяет предположить, что реакция коррозии контролируется скоростью катодного восстановления реакции кислорода.
i a (мА · см -2 )
Вт (ММА -1 )
Сб / Сб
Рисунок 8 — Плотность анодного тока в зависимости от отношения площади поверхности катода к аноду для плакированных медно-никелевых / стальных образцов с механически обработанными дефектами для обнажения сталиАвторы приходят к выводу, что вероятность возникновения сквозного повреждения корпуса очень мала и возможна только в случае очень небольшого дефекта.
Соответствующая ситуация с дефектами обшитого корпуса несколько иная, как показывает эксперимент по коррозии стали вблизи дефекта обшивки стальной сваи (28) .Небольшой дефект в медно-никелевой оболочке позволит тонкому слою воды проникнуть в пространство стрелы между оболочкой и стальным корпусом, ограниченным периферийными сварными швами оболочки к стали. Отношение площади Sc / Sa будет намного меньше кажущегося геометрического отношения. Коррозия стали будет происходить быстро в течение очень короткого периода времени, пока не будет израсходован кислород, поскольку захваченная пленка воды имеет очень плохой контакт с внешней морской водой. Похоже, что эта ситуация менее угрожает целостности корпуса и даст более чем достаточно времени для ремонта обшивки.
Шероховатость корпуса
Самая важная причина использования медно-никелевого покрытия на корпусе корабля, будь то обшивка или обшивка, заключается в достижении экономии топлива за счет уменьшения шероховатости корпуса, достигаемого с помощью медно-никелевого сплава. Шероховатость корпуса напрямую связана с мощностью вала, необходимой для преодоления простого трения корпуса; остальная часть мощности расходуется на создание волн.
Было подсчитано, что судовладелец платит штраф, эквивалентный увеличению потребляемой мощности на один процент, за увеличение шероховатости корпуса на 10 мкм (в диапазоне 0–230 мкм) и 0.5 процентов на каждые 10 мкм сверх этого (8,9) . Основываясь на британском исследовании 400 судов, средняя шероховатость нового корпуса составляет 125 мкм, максимально достижимая шероховатость — 75 мкм, а среднее ежегодное увеличение шероховатости составляет от 50 до 70 мкм. Таким образом, обычный корпус начинает терять эффективность со дня его спуска на воду, в то время как медно-никелевый корпус, если есть какие-либо изменения, со временем способствует повышению эффективности.
Данные о шероховатости позволяют рассчитать вероятные характеристики судна, если вся смачиваемая поверхность была покрыта медно-никелевым покрытием.В конце периода испытаний средняя шероховатость окрашенного стального корпуса составила 250 мкм. Соответствующая шероховатость медно-никелевого сплава составляла всего 53 мкм. Разница в 197 мкм означает повышение эксплуатационной эффективности, достижимое, если обшить весь корпус. Если предположить, что приведенная выше оценка штрафа мощности верна, покрытие полностью смоченной поверхности медно-никелевыми панелями приведет к повышению эффективности на 19,7%. Независимое исследование, проведенное Институтом Уэбба, подтверждает эти выводы (10) .
Измерения шероховатости 12 панелей в эксперименте Arco Texas показали, что медно-никелевый сплав вначале значительно более гладкий, чем окрашенный стальной корпус, и, что представляет значительный интерес, медно-никелевый сплав стал немного более гладким после ходовых испытаний. Окрашенная сталь, конечно, становится все более грубой в эксплуатации. Данные о шероховатости корпуса, измеренные в конце экспозиции Arco Texas, показаны на рис. .
Относительная частота,% Рисунок 9 — Окончательные данные о шероховатости в конце эксплуатационных испытаний медно-никелевых панелей C70600 на Arco TexasМедно-никелевый лист для оболочки, поскольку он холоднокатаный, несколько более гладкий, чем горячекатаный плакированный материал.Холоднокатаный материал обычно имеет среднюю шероховатость около 40 мкм; тогда как горячекатаный плакированный материал обычно имеет среднюю шероховатость около 60-55 мкм. Определение шероховатости медно-никелевой оболочки руля направления Great Land показало, что шероховатость неизменно ниже 20 мкм. Для сравнения: шероховатость окрашенного стального корпуса судна, измеренная при постановке в сухой док через 14 месяцев, в среднем составила около 210 мкм.
Методы обшивки и анализ затрат
Современный метод определения исходных условий
Чтобы эффективно проанализировать потенциальную экономию при эксплуатации и техническом обслуживании большого судна, связанную с устойчивым к коррозии и загрязнению медно-никелевым корпусом, необходимо иметь точную оценку стоимости обшивки.Этот анализ был проведен судостроительной компанией Ньюпорт-Ньюс для Ассоциации разработки меди в соответствии с контрактом с Морской администрацией США (MARAD) (11) .
Корабль был впервые выбран для анализа. Чтобы соответствовать цели этого исследования, было определено, что судно, которое может быть отнесено к обоим концам спектра высокоскоростных и низкоскоростных судов, было бы желательным выбором. Для своего анализа Newport News Shipbuilding выбрала флот-масленку класса T-A0 187, корабль серии T-A0 191 в качестве базового корабля для исследования.Коэффициент блочности, увлажненная поверхность и базовая конфигурация корабля хорошо поддаются сравнению с другими типами судов для определения приблизительной стоимости обшивки других кораблей. Размеры и соответствующие характеристики масленки показаны на рис. 10 . Максимальная грузоподъемность 38 футов (11,6 м) выше базовой линии была принята в качестве демаркационной линии для обшивки; то есть, весь корпус ниже этой линии будет обшит, включая руль направления и морские сундуки. Однако морские сундуки в расчет не включались.Это дает 83 042 фута 2 (7715 м 2 ) корпуса, подлежащего обшивке.
Длина Общая | 677 ‘- 6 дюймов |
Длина между перпендикулярами | 650 ‘- 0 « |
Балка максимальная | 97 ‘- 6 « |
Осадка по проектной ватерлинии | 34 ‘- 6 « |
CB | 0.643 |
Рабочий объем | 40140 Длинные тонны |
В качестве сплава оболочки был выбран медный сплав С70600. При выборе размера листа необходимо было учитывать возможность обработки и размещения имеющихся в продаже форматов. Для первоначального анализа был выбран лист обшивки размером 48 дюймов x 144 дюйма x 0,1 дюйма (122 см x 366 см x 2,5 мм). Каждый лист будет весить 223 фунта (101 кг).Общая необходимая сварка составила приблизительно 55 000 погонных футов (16 764 м). Всего потребуется 1731 полноразмерный лист весом 424 874 фунта (193 тонны). С учетом обрезки, подходящей для носа и кормы, было подсчитано, что в общей сложности потребуется 2000 листов.
На основе описанных выше исследований сварного соединения изначально рассматривалась возможность ручной сварки сварочным электродом с использованием сварочных электродов ENiCu класса AWS A5.11. Расстояние между горизонтальными пластинами должно быть 3/8 дюйма (9,5 мм) и 5/8 дюйма (15.9 мм) на вертикальных швах.
Массив швов с пазами 1 дюйм x 3/8 дюйма (25 мм x 9,5 мм) будет использоваться для усиления крепления пластины, чтобы предотвратить вздутие оболочки. Раздел 6 Правил постройки и классификации судов Американского бюро судоходства был использован для определения изгибных напряжений балки корпуса. Эти анализы проводились на 1/4, средней и 3/4 секциях корпуса. Рассчитанные изгибающие моменты в сочетании с модулем упругости сечения на миделе обеспечили величину напряжений, действующих на судно вокруг нейтральной оси.Частота выполнения щелевых сварных швов зависит как от расчетного напряжения, так и от прочности медно-никелевого шва со сталью. Эти расчеты показали, что частота щелей может уменьшаться по мере приближения листов к нейтральной оси. Результаты показали, что на двух третях поверхности корпуса расстояние между пазами должно составлять 12 дюймов (300 мм), а на оставшейся одной трети расстояние можно увеличить до 16 дюймов (406 мм). В результате получается в общей сложности 26 468 сварных швов на судне и, по крайней мере в первом приближении, сводится к минимуму количество требуемых сварных швов.
Представители-консультанты различных строительных отделов Newport News Shipbuilding установили следующую последовательность строительства обшивки:
- Док-судно
- Пескоструйная обработка и покрытие — дробеструйная / пескоструйная обработка и нанесение тонкого слоя антикоррозийного средства
- Прямая постановка — потребуется полная семиуровневая постановка
- Отшлифовать существующие сварные швы заподлицо — приблизительно 17 000 погонных футов (5 182 м)
- В некоторых случаях может потребоваться неразрушающий контроль существующих сварных швов — стоимость не включена в эту оценку
- Установить обшивку — разметить, удалить покрытие, прихватить
- Обшивка под сварку — периферийные устройства и пазы
- Шлифование швов обшивки заподлицо — 27000 погонных футов (8230 м)
- Удалить постановку
- Судно флота
- Неразрушающий контроль Обшивка — испытание под вакуумом
- Отстыковать судно
Были определены время и персонал, необходимые для каждой операции.Как показано на рис. 11 , период в 21 неделю считался реалистичным для обшивки. Затем были оценены затраты на каждый из описанных выше шагов. Требовалась информация о человеко-часах на выполнение задачи, продолжительности пребывания в сухом доке, единицах времени на квадратный фут площади, цене на материал оболочки и сварочный электрод и т. Д. Результаты с разбивкой по процентам от общей стоимости показаны на Рисунок 12 . С точки зрения цены за единицу, стоимость была рассчитана как 56,54 доллара за квадратный фут. 2 (608,59 $ / м 2 ) (в долларах 1986 г.). Если потребуется неразрушающий контроль существующих сварных швов стального корпуса, это может добавить 0,30 доллара за фут 2 . (3,23 $ за кв.м) зоны покрытия.
Посмотреть полный размерРисунок 11 — Первоначальный (исходный) график строительства
Улучшенный метод обшивки
Было признано, что использование некоторых инновационных технологий для критических частей передового подхода, использованного выше, может существенно снизить стоимость.Пять основных факторов, влияющих на стоимость: материал обшивки — 25%; установить обшивку, 22%; оболочка сварного шва — 15%; постановка — 11%; и сухой док, 9%, были проанализированы на предмет возможных улучшений. Три другие области были исследованы и выбраны в качестве второстепенных областей для улучшения: шлифовка существующих сварных швов корпуса и обшивки и подготовка стального корпуса.
Во-первых, замена рулонных медно-никелевых листов на отдельные листы приведет к сокращению материальных затрат и преимуществ при снятии корпуса с производства и размещении материала на судне.Катушка шириной 24 дюйма и весом 7000 фунтов (, 3176 кг) будет иметь длину более 750 футов (229 м) и может управляться специальной установкой для поддержки катушки и обеспечения возможности разматывания материала относительно корпуса во время установка ( Рисунок 13 ). Такая буровая установка должна быть спроектирована так, чтобы ее можно было прикрепить к типичному гидравлическому телескопическому крану грузоподъемностью 15–18 тонн, а также к моторным транспортным средствам с низкой платформой, используемым на большинстве верфей. Это оборудование свело бы к минимуму потребность в детальной компоновке корпуса и облегчило бы первоначальное размещение обшивки на корабле.Снижение стоимости этих изделий и материала будет частично компенсировано увеличением погонных футов сварки (примерно 20%) из-за меньшей ширины. Полуавтоматические сварочные аппараты могут использоваться вместе с этими установками для прихваточной сварки оболочки на месте. Еще одна значительная область экономии, присущая использованию материала оболочки змеевика, заключается в том, что это позволяет исключить большую часть затрат на этапы. Мобильные надземные платформы, поддерживающие змеевики, также позволят рабочим получить доступ к любой части судна и позволят работать без задержек для монтажа подмостков.
Текущие исследования методов сварки показали, что метод сварки балкой в среде инертного газа (MIG) является потенциально жизнеспособным методом (12) . Процесс MIG Beam представляет собой полуавтоматический метод с рулонной подачей, для которого требуется только зазор 1/8 дюйма (3,2 мм), который можно заполнить за один проход, а не за три прохода, необходимые для более широких зазоров в процессе SMAW. Использование полуавтоматического оборудования и однократного прохода сокращает трудозатраты на выполнение задачи.
Дальнейшее исследование напряжения изгиба балки корпуса этого судна показало области пониженных напряжений, где требования к креплению обшивки к судну будут менее строгими.Как показано на рис. 14 , приблизительно 30% зоны покрытия требовали периферийных сварных швов, только если использовалась оболочка шириной 24 дюйма (0,61 м). В средней части корпуса судна можно было использовать материал шириной 36 дюймов (0,91 м). Для этой области потребуется серия щелевых сварных швов, состоящая из межцентрового расстояния 12 дюймов (0,61 м) для примерно 80% покрытия и 18 дюймов (0,46 м) для оставшихся 20%. Эта конфигурация уменьшает количество необходимых слотов с 48 468 до 34 878. 1 дюйм x 3/8 дюйма (25 мм x 9.5 мм) с помощью ручного SMAW.
Посмотреть полный размерРисунок 14 — Устройство оболочки змеевика улучшенным методом
Еще одно возможное улучшение — использование точечной сварки. Метод импульсной точечной сварки MIG, разработанный (12) , доказал свою эффективность во всех положениях. Пробивается отверстие диаметром 3/16 дюйма (4,8 мм) с конусом 82 °. Три точечных сварных шва для каждого щелевого шва должны выдерживать одинаковую нагрузку, но сварка может выполняться полуавтоматически.Это позволит исключить всю ручную сварку обшивки и обеспечить более быстрый и эффективный процесс крепления, требующий минимум высококвалифицированного персонала.
Еще одна область, в которой можно снизить затраты, — это отказ от шлифовки сварных швов. Процесс MIG Beam не создает больших сварных швов и не вызывает значительного ухудшения характеристик корпуса. Что касается сварных швов стального корпуса, то медно-никелевая оболочка достаточно гибкая и по существу соответствует форме корпуса.Шлифовать нужно только большие возвышенности.
Наконец, можно сэкономить на подготовке корпуса. Первая оценка стоимости этого исследования включала пескоструйную очистку всего корпуса (ниже 38 футов ватерлинии) до белого или почти белого металла с последующим нанесением тонкого покрытия для предотвращения ржавчины перед обшивкой. В зависимости от возраста судна и состояния поверхности корпуса на момент установки обшивки, только те области, которые необходимо сваривать (стыки, швы и щели / пятна), необходимо очистить до белого металла.Снятие корпуса перед установкой медно-никелевой оболочки (для указания точного местоположения свариваемых участков) и последующая очистка только этих участков облегчили бы процесс установки.
Последние разработки, использующие концепцию воды под высоким давлением в качестве среды для очистки корпуса судна, привели к созданию технологии, которая позволяет очищать определенные области. Эта система работает за счет использования ручной самовосстанавливающейся насадки, которая может быть ограничена зоной покрытия всего в несколько дюймов.Использование этой или подобной системы позволило бы очистить свариваемые участки непосредственно перед установкой оболочки и, следовательно, не потребовало бы какой-либо специальной обработки для предотвращения ржавчины.
Пересмотренный график обшивки корабля был рассчитан на основе нескольких усовершенствованных методов, упомянутых выше. Общая продолжительность обшивки сосуда сокращена с улучшением до 17 недель ( Рисунок 15 ). Был проведен новый анализ затрат с учетом этих улучшений.Затраты на различные этапы в процентах от общей стоимости показаны на Рис. 16 . Окончательная оценка затрат, основанная на улучшенном методе, была сначала установлена для сценария, который включает серию сварных швов с пазом 1 дюйм x 3/8 дюйма (25 мм x 9,5 мм), сваренных с использованием ручной технологии SMAW.
Рисунок 15 — График строительства улучшенного метода % Элементы общих затратРисунок 16 — Оценка затрат улучшенного метода
Это приводит к стоимости обшивки единицы в 35 долларов.28 / фут² (379,61 долл. США / м²). Если щелевые сварные швы заменяются серией точечных сварных швов диаметром 3/16 дюйма (4,8 мм) с использованием полуавтоматической импульсной технологии MIG, стоимость единицы снижается до 33,18 долларов США / фут² (357,02 доллара США / м²). Третий сценарий, на который стоит обратить внимание, касается обшивки во время первоначального строительства судна, когда исключаются определенные затраты, в том числе установка в сухой док, относящаяся к установке обшивки. В этом случае расчетная стоимость обшивки составляет 25,40 долларов США / фут² (273,30 долларов США / м²). Все эти удельные затраты указаны в долларах 1986 года и не включают неразрушающий контроль в размере 0 долларов.30 / фут² (3,23 доллара США / м²).
Влияние улучшенных методов на отдельные операции обшивки проиллюстрировано на Рис. 17 . Значительная процентная экономия достигается за счет снижения требований к шлифовке сварных швов стального корпуса и сварных швов крепления оболочки. Стоимость испытания оболочки в этой новой конфигурации — единственная операция, которая стоит дороже.
% Общих затрат- Для сравнения двух анализов затрат, Staging и Equipment Operation рассматриваются как один и тот же вид затрат
- Скорость движения судна остается одинаковой в обоих анализах и поэтому не показана на этой диаграмме
- Разница в процентах основана на Базовом анализе затрат по сравнению с Улучшенным анализом затрат на метод цифр затрат
Экономика эффективности жизненного цикла
Целью этих исследований было определение влияния следующих трех систем покрытия корпуса на общую экономику морского судна.
- Обычная медьсодержащая противообрастающая краска с грунтовкой и системой CP
- Система необрастающих составов из органо-оловянного сополимера (ОСА)
- Медно-никелевая оболочка
Было рассмотрено два сценария обшивки:
- Обшивка на весь срок службы корабля; т.е. обшивка при строительстве
- Обшивка в качестве модернизации после 10 лет эксплуатации
В представленном здесь анализе использовались затраты на обшивку, описанную выше, для обновления более раннего экономического исследования, проведенного в 1983 г. (10) .В этом исследовании, проведенном Институтом Уэбба, рассматривалось другое судно, грузовое судно C-4, а не танкер T-AO. Сухогруз С-4 устарел, но по нему существует большой объем эксплуатационных данных. Анализ экономики эксплуатации этого корабля был достаточно подробным и рассматривал сравнение ряда факторов, влияющих на эксплуатационные расходы и доходы, в зависимости от выбора метода защиты корпуса.
Стоимость обшивки была скорректирована для меньшего судна с учетом сокращения времени установки из-за меньшей смачиваемой площади, 46 370 футов² (4313 м²).Доллары 1983 года были завышены до покупательной способности 1986 года, а стоимость мазута была принята равной 18 долларам за баррель.
При анализе обшивки во время нового строительства экономика жизненного цикла была основана на сравнении таких факторов, как: стоимость двигателя (конкретные комбинации двигатель-гребной винт были выбраны на основе ожидаемых характеристик покрытия), стоимость самих методов нанесения покрытия. , расход топлива, обычные затраты на сухой док в течение 20-летнего срока службы и выручку от утилизации. Доходы от грузовых перевозок оставались неизменными для всех систем покрытия, что является следствием выбора размера комбинации двигатель-гребной винт для каждого метода покрытия, чтобы обеспечить одинаковую скорость во всех случаях.Эффективность покрытия отражается на размере двигателя (фактор капитальных затрат) и результирующем расходе топлива.
В случае модифицированной установки экономическое сравнение жизненного цикла трех методов защиты корпуса основывалось на стоимости метода нанесения покрытия, стоимости дополнительной подготовки поверхности, необходимой для нанесения покрытия во время модернизации, тайм-аут обслуживания, расход топлива (который будет отличаться для трех методов после установки), затраты на постановку в сухой док во время установки, обычные затраты на постановку в сухой док в течение оставшихся лет службы после нанесения покрытия, затраты на техническое обслуживание покрытия и добавленную стоимость утилизации медно-никелевого сплава на окончание срока службы корабля.При модернизации размер двигателя не меняется, но на расход топлива будут влиять рабочие характеристики покрытия; т.е. скорость. Таким образом, выручка от груза зависит от типа покрытия и включается в анализ для модернизации установки покрытия / оболочки.
Результаты экономического анализа дисконтированных денежных потоков обобщены в Таблице 2 и Таблице 3 . При установке во время нового строительства экономия 1 814 000 долл. США достигается за счет меньшего объема двигателя, необходимого для корабля с медно-никелевой оболочкой.Это частично компенсирует существенно более высокую стоимость применения медно-никелевого сплава (даже для сценария с наименьшими затратами). Но очень большая экономия топлива за 20-летний срок службы приводит к привлекательной общей экономии.
Все затраты в тысячах долларов 1986 года | ||||||
---|---|---|---|---|---|---|
Корпус | Стоимость двигателя | Стоимость покрытия | Стоимость топлива | нормальный D.D. Стоимость | Остаточная стоимость | Общая экономия |
Базовый (конв.) | 9 200 | 102 | 20 263 | 715 | – | – |
OCA | 8 237 | 163 | 17 438 | 961 | – | 3,481 |
Cu-Ni @ 56,54 долл. США | 7 359 | 2,622 | 14 841 | 440 | 19 | 5 037 |
Cu-Ni @ 35 долларов США.28 | 7 359 | 1,636 | 14 841 | 440 | 19 | 6 014 |
Cu-Ni по 25,40 долл. США | 7 359 | 1,178 | 14,941 | 440 | 19 | 6,481 |
Все затраты в тысячах долларов 1986 г., за исключением дополнительного груза | ||||
---|---|---|---|---|
Корпус | База (Конв.) | OCA | Cu-Ni @ 56,54 $ | Cu-Ni 35,28 $ |
Стоимость покрытия для модернизации | 72 | 133 | 2 157 | 1 603 |
Extra Sufrace Prep. | 115 | 115 | 115 | 115 |
Время O / O svc. для покрытия | 42 | 42 | 1,214 | 983 |
Стоимость топлива | 20 242 | 20 212 | 18 394 | 18,445 |
Покрытие сухого дока Стоимость | 21 | 21 | 607 | 482 |
Обычный сухой док стоит | 165 | 165 | 83 | 83 |
Повторное покрытие в сухом доке> 10 лет. | 327 | 510 | 220 | 220 |
Extra cargo rev. | 129 020 | 130 270 | 131 570 | 131 570 |
Общая экономия | (60) | 976 | 343 | 1,562 |
* Итого CU-NI включает бонус за утилизацию в размере 19 000 долларов США |
Обычные расходы в сухом доке возникают из-за того, что Американское бюро судоходства требует два раза в год проверки хвостового вала, для чего требуется установка в сухой док.Для медно-никелевой оболочки в этих сухих доках потребуется только гидроструйная очистка. Но из соображений консервативности была добавлена небольшая стоимость материала и применения, равная двум процентам от стоимости обшивки всего корабля, чтобы учесть возможность повреждения поверхности. Затраты на ремонт органо-оловянных и обычных систем выше.
Таким образом, применение медно-никелевой оболочки корпуса во время нового строительства приведет к чистой экономии от 5 037 000 до 6 481 000 долларов, в зависимости от стоимости первоначальной установки.Что касается оболочки в качестве модернизации в середине срока службы после 10 лет эксплуатации, то экономия, полученная за счет оболочки и других систем покрытия, конечно, не так велика.
«Базовый» случай, рассматриваемый здесь, был взят как полная очистка стального корпуса до «белого металла» с последующим нанесением обычной антикоррозийной и необрастающей системы окраски стоимостью 72 000 долларов. Затраты на обшивку снова рассчитываются с использованием описанных выше удельных затрат. Время простоя для модернизации этого судна включено в стоимость из расчета 14 000 долларов в день.Затраты на сухой док были разбиты на те затраты, которые связаны с самим процессом нанесения покрытия, а также те обычные затраты на сухой док, которые различные системы нанесения покрытия будут вызывать за последние 10 лет эксплуатации. Для медно-никелевой оболочки потребуется только половина времени нахождения в сухом доке, необходимого для обычной окраски или покрытия ОСА, что приведет к экономии на срок службы 83000 долларов в пользу медно-никелевой.
Аналогичным образом трудозатраты, необходимые для поддержания покрытий («Повторное покрытие в D.D. «- Таблица 3 ) будет считаться менее дорогостоящим для медно-никелевой оболочки. Экономия топлива в этом случае модернизации достигается только за последние 10 лет эксплуатации и, следовательно, не так велика, как в случае новой конструкции. . Но существенные дополнительные доходы от грузов будут получены в результате более гладкого корпуса для данной комбинации двигателя и гребного винта из-за более высокой скорости пропаривания и меньшего количества дней нахождения в сухом доке для обслуживания. За последние 10 лет эксплуатации медно-никелевый сплав добавляет 210 000 долларов к судну. доход по сравнению с традиционной системой покрытия.
Чистый экономический результат применения медно-никелевой модификации в качестве модернизации указан в крайнем правом столбце таблицы 3 . Обшивка корпуса из медно-никелевого сплава сэкономит владельцу судна от 343 000 до 1562 долларов США по сравнению с традиционной краской. Система OCA позволит сэкономить 976 000 долларов. Повторное нанесение обычной необрастающей краски в состоянии «как новая» фактически приведет к потере 60 000 долларов США, поскольку стоимость не полностью компенсируется улучшенной экономичностью и увеличенным объемом груза.Таким образом, даже в случае модернизации через 10 лет, оказывается, что медно-никелевая оболочка может обеспечить более высокую экономию, чем обычные системы или системы OCA, при условии использования технологических усовершенствований, обсужденных ранее.
Обшивка корпуса судна — выводы
В этом разделе сделана попытка проанализировать историю и опыт работы с медно-никелевыми корпусами судов и обсудить технологию, относящуюся к обшивке больших судов. Эксперименты с обшивкой руля направления и размещением медно-никелевых панелей на корпусах грузовых судов и танкеров послужили основанием для снятия опасений по поводу допуска скорости сплава C70600.Было показано, что гальваническая коррозия стального корпуса имеет управляемую скорость при использовании стали, плакированной медно-никелевым покрытием, с дефектами, обнажающими сталь. Предполагается, что обшитые корпуса будут еще менее подвержены коррозии стального корпуса в случае разрыва оболочки. Обшивка с использованием существующих методов, а также легко применяемых передовых подходов была описана с указанием соответствующих затрат на единицу площади. Наконец, экономическое сравнение трех методов защиты корпуса сравнивается с точки зрения начальных капитальных затрат и экономии на обслуживании и топливе в течение 20-летнего срока службы судна или в течение 10-летнего срока службы в случае модернизации обшивки в середине. жизнь корабля.В обоих случаях показано, что медно-никелевая оболочка приводит к значительной экономии затрат в течение жизненного цикла.
Мы надеемся, что этот обзор побудит мировых судостроителей изучить потенциал медно-никелевой обшивки больших судов и приведет к крупному демонстрационному проекту по продвижению концепции медно-никелевой обшивки корпуса судна.
Обшивка морских сооружений
Введение
В то время как обшивка корпусов судов для защиты от коррозии и биологического обрастания — это концепция, ожидающая окончательной демонстрации и испытаний, обшивка различных морских конструкций — доказанное применение для медно-никелевых сплавов и никель-медного сплава Сплав Монель (15) 400.Это связано с тем, что морские платформы для бурения и добычи нефти и газа должны сохранять свою структурную целостность и противостоять воздействию не только агрессивной морской воды, но также погодных условий и волн.
Со стабилизацией цен на нефть коммерческий климат для разработки месторождения улучшился. Сообщается, что в период 1990-1995 годов планируется разработать более 700 морских месторождений. Около 188 из этих месторождений с участием 275 платформ находятся в Азии (13) .
Опубликован ряд сводных статей и обзоров обшивки морских сооружений (14-19) .Эта обработка суммирует основные моменты в отношении преимуществ обшивки больших морских сооружений по сравнению с уменьшением стоимости конструкции за счет устранения загрязнения и допуска на коррозию из-за коррозии в зоне разбрызгивания и дает некоторое представление об экономических преимуществах.
Сопротивление обрастанию и защита от коррозии медно-никелевой оболочки имеют решающее значение для защиты морских сооружений. Прикрепление и рост морских организмов могут добавить значительный вес конструкции; но, что более важно, увеличение боковых нагрузок на конструкцию из-за течений, ветра и волн является основным соображением при проектировании.Наблюдается рост морской среды от 0,7 до 1,2 м. Чрезмерные морские заросли часто достигают высоты примерно от 1 м над средним уровнем моря до примерно 10 метров ниже. Меньший рост распространяется на более низкие уровни. Необходимо предусмотреть очень большое количество дополнительной стальной конструкции, чтобы противостоять возникающим силам. Также требуется регулярное и дорогостоящее удаление морских наростов водолазами с использованием воды под высоким давлением. Как будет показано ниже, обшивка может значительно снизить эти затраты и обеспечить общую экономию для владельца платформы.
Коррозия и защита стальных конструкций в морской воде
Интенсивность коррозии незащищенной стальной конструкции в морской воде заметно меняется в зависимости от положения, как показано на Рис. 18 . Зона брызг и брызг над средним уровнем прилива является наиболее подверженным атакам регионом из-за постоянного контакта с сильно аэрированной морской водой и эрозионного эффекта брызг и приливов. Сообщается, что скорость коррозии достигает 0,9 мм / год в заливе Кука, Аляска, и 1,4 мм / год в Мексиканском заливе.Катодная защита в этой области неэффективна из-за отсутствия контакта с морской водой и, как следствие, отсутствия тока в течение большей части времени. Скорость коррозии часто очень высока в месте чуть ниже среднего прилива в регионе, который является очень анодным по отношению к приливной зоне из-за мощных ячеек дифференциальной аэрации.
Относительная потеря толщины металлаРисунок 18 — Профиль потери толщины в результате коррозии незащищенной стальной конструкции в морской воде
Защита стальной конструкции может осуществляться различными способами; каждую зону коррозии следует рассматривать отдельно.Три общепринятых метода: катодная защита, окраска или нанесение покрытий и оболочка. Обшивка оказалась очень успешным подходом при применении в области через зону брызг / брызг на небольшое расстояние ниже приливной зоны. Сплав монель 400 был применен для этой задачи еще в 1949 году на морской платформе в Мексиканском заливе у побережья Луизианы (20,21) . Центр LaQue в Райтсвилл-Бич, Северная Каролина, США, провел обширные испытания обшивки с использованием стальных свай, поддерживающих причалы для испытаний на коррозию морской водой в лаборатории в качестве образцов для испытаний.Испытанные защитные и защитные материалы включали монель, нержавеющую сталь AISI 304, медно-никелевую сталь 70-30, а также сталь с никелевым и монелевым покрытием. Все они показали очень хорошие результаты после 36 лет воздействия (18) . Также было испытано большое количество запатентованных покрытий, включая цинкование и напыление цинка и алюминия; все они обладают конечным эффективным сроком службы, достигающим 13 лет (16) .
Медно-никелевый сплав 90-10 не был включен в эти ранние испытания оболочки, поскольку его состав по отношению к железу и марганцу еще не был установлен.
На ранних этапах испытаний оболочки из медно-никелевого сплава 70-30 и 70-30 приваривались непосредственно к стали. Можно предположить, что коррозия анодной стали ниже среднего отлива будет ускоряться, потому что она находится в прямом контакте с гораздо более благородным материалом оболочки. В LaQue Center был проведен ряд экспериментов, чтобы выяснить это. Кирк суммировал эти скважины (18) . Оказывается, что в приливной зоне сталь, безусловно, является наиболее катодным материалом, а более благородные сплавы для оболочки приводят к более низким токам и коррозии погруженной стали, чем отсутствие оболочки вообще.
Этот вывод хорошо иллюстрируется результатами испытаний на гальваническую коррозию, проведенных для определения воздействия на погруженную сталь, соединенную с другими сплавами в приливной зоне, как показано на Рис. 19 . Пластины из сплавов, помещенные в приливную зону, соединяются с погруженными стальными пластинами, и общий ток за прилив периодически измерялся в течение 14 месяцев воздействия. Ток уменьшался со временем, но результаты ясно показали, что самая серьезная гальваническая пара — это сталь к стали.Это связано с тем, что даже несмотря на то, что разность потенциалов, возникающая в парах благородного сплава и стали, значительно больше, чем между двумя стальными панелями, более быстрая и почти полная поляризация благородных металлов приводит к значительному снижению гальванического тока. Совсем недавно Международная ассоциация исследований меди (ныне Международная ассоциация меди) провела несколько исследовательских программ, уточняющих и уточняющих эти более ранние результаты (22-24) . Таким образом, сталь под водой меньше подвержена коррозии при контакте с благородными металлами в приливной зоне, чем при соединении с другой панелью стали в приливной зоне.
Рисунок 19 — Зависимость суммарного тока за прилив от времени между плитами в испытании на имитацию сваиЗащита от обрастания
Как обсуждалось в других частях этой серии, медно-никелевый сплав 90-10 обеспечивает наилучшее сочетание коррозионной стойкости и защиты от биологического обрастания. Прикрепление этого материала оболочки к стальной конструкции с помощью сварки или механических креплений приведет к катодной поляризации материала оболочки и снижению противообрастающей способности медно-никелевого сплава 90-10.Следовательно, необходимо электрически изолировать оболочку от элементов стальной оболочки, чтобы в полной мере использовать свойства сплава. Изоляция может быть достигнута путем закачки цемента или эпоксидной смолы в кольцевое пространство между компонентом и оболочкой или, проще говоря, с помощью эластомера или изолятора на резиновой основе. Медно-никелевый сплав может быть в форме листа, проволочной сетки, частиц (25) или пламенного напыления. Склеивание поверхностей раздела сталь-эластомер-медь-никель может осуществляться вулканизацией, применением эпоксидных клеев, механическими средствами или комбинацией методов.Сметные затраты в 1986 году варьировались от 18 до 30 долларов за квадратный фут (от 194 до 322 долларов за квадратный метр) (17) .
Долгосрочное воздействие на сваи в оболочке для оценки эффективности защиты от коррозии и биологического обрастания и измерения тока катодной защиты, необходимого для нескольких ситуаций, спонсировалось Международной ассоциацией меди и Ассоциацией разработки меди в Центре коррозионных технологий LaQue, Райтсвилл. Бич, Северная Каролина (26) .Более 50 свай ASTM Тип A-36 диаметром 17 см были обшиты оболочкой C70600 толщиной 4,6 мм и длиной 3 м. Некоторые оболочки были непосредственно приварены к стали, другие были изолированы из стали с бетоном или 6 мм бутилкаучуковой смесью. Некоторые сваи были катодно защищены анодами Galvalum III, тогда как другие остались незащищенными. Сваи были удалены после двух и пяти лет воздействия для изучения коррозии стали и отложений.
Результаты накопления биообрастания на этих сваях обобщены в Таблице 4 ниже.Масса, накопленная на голой стальной свае, была более чем в два раза больше, чем на непосредственно приваренной C70600, и более чем в 50 раз больше, чем на изолированной оболочке. Через пять лет на незащищенных медно-никелевых оболочках было замечено лишь несколько разбросанных ракушек.
Сваи | кг / м² | процентов | |
---|---|---|---|
Сталь без покрытия | 18.00 | 100,0 | |
Бетонная изоляция | 0,36 | 1,9 | Только разбросанные ракушки ракушек |
Непосредственная сварка | 7,95 | 44,3 | |
С резиновой изоляцией | 0,26 | 1,4 | Только разбросанные ракушки ракушек |
Резиновая изоляция с гальванической парой (одноточечный контакт) | 4,59 | 25,5 | |
Обнаруженные биообрастающие организмы — ракушки, устрицы, кодий, оболочка, колониальная оболочка, корковые и нитчатые мшанки |
Гальванические аноды, используемые на свае с катодной защитой, были очищены и взвешены; скорости потери массы и расхода приведены в таблице ниже.В течение двух лет экспозиции непосредственно сваренная сваи показывала меньший расход анода, чем голая сталь; показатели расхода изолированного бетона были сопоставимы с расходом чистой стали. После пяти лет воздействия как непосредственно сваренные, так и бетонные изолированные сваи показали снижение расхода. Считается, что снижение расхода анода для непосредственно сварной сваи связано с благоприятными поляризационными характеристиками медно-никелевого сплава C70600. Уменьшение расхода анода для бетонной изолированной сваи, скорее всего, связано с высоким сопротивлением пути через бетон к лежащей под ним стали.
Сваи | Потеря веса (г) | Норма расхода (кг / год) |
---|---|---|
ДВУХЛЕТНИЙ СНЯТИЕ | ||
Голая сталь | 716,4 | 0,36 |
Изолированный бетон | 755,3 | 0,38 |
Прямая сварка | 414.1 | 0,21 |
УДАЛЕНИЕ ПЯТИ ЛЕТ | ||
Голая сталь | 1880,6 | 0,38 |
Изолированный бетон | 1256,6 | 0,25 |
Прямая сварка | 687,6 | 0,14 |
* Два анода на свай |
Общее снижение расхода анода для обоих методов покрытия может быть связано с уменьшением тока, необходимого для поддержания известковой пленки, сформированной на медно-никелевом сплаве C70600.
Также было замечено, что даже в методе обшивки с прямым сварным швом, когда сваи были обнажены без катодной защиты в течение пяти лет, не было сильно ускоренного разрушения стали непосредственно над или под оболочкой. Средняя скорость коррозии в стали, прилегающей к оболочке ниже средней точки отлива, не превышала 0,25 мм / год, что не превышает скорости коррозии в свободно корродирующих стальных контрольных сваях без оболочки. Конечно, обнажение стальных свай без катодной защиты не рекомендуется.
Запатентованная система под названием «Bio-Shield», разработанная Shell Development Company, имела значительный успех на морских установках у побережья Калифорнии (27) . Биообрастание может быть довольно серьезным вдоль побережья Южной Калифорнии. Bioshield состоит из медно-никелевого сплава 90-10 толщиной 1-1 / 2 мм и эластомера высокой плотности с торговым названием Splashtron, производимого компанией Mark Tool из Лафайета, штат Луизиана. После программы лабораторных испытаний эта система была применена при проектировании платформы Eureka глубиной 214 м с 60 кондукторами (0.6 м OD). В общей сложности было исключено 152 тонны конструкционной стали, которая в противном случае требовалась бы для обработки погрузки с морской установки. Платформа была установлена в июле 1984 года. Через несколько лет на медно-никелевой поверхности Bioshield не осталось загрязнений, в то время как незащищенные участки были покрыты слоем ракушек и мидий толщиной от 8 до 13 см. Снижены отклики платформы: волновые силы -6%; базовый сдвиг -10%; момент опрокидывания -10%; прогиб деки -10%; и нагрузка на свай -7%. Уменьшение значений отклика платформы является причиной того, что предотвращение роста морской среды может существенно снизить затраты платформы.Деньги были сэкономлены на уменьшенном количестве стали для допуска на коррозию и улучшенных усталостных характеристиках основных узлов платформы. Предполагаемая экономия, полученная за счет установки системы обшивки на 60 проводов от среднего низкого уровня воды +1,5 м до -4,9 м для конструкции длиной 214 м, составила в (1983-84):
Проводники — 55 тонн x 1000 долларов США за тонну | = | 55 000 долл. США |
Краска — 10 600 кв. Футов x 3 долл. США / кв. Фут | = | 32 000 долл. США |
Аноды — 1250 долл. США каждый x 4 | = | 5000 долларов США |
Структурные узлы — 114 тонн x 2500 долларов США за тонну | = | 285 000 долл. США |
Итого | = | 377 000 долл. США |
Предполагаемая экономия от 50 000 до 100 000 долларов на одну уборку также должна была быть достигнута.Затраты на установку этой системы на платформе Eureka составили 250 000 долларов или около 31,60 доллара за фут² (340 долларов за м²). Очевидно, что установка системы медно-никелевой оболочки в этом примере была очень рентабельной.
Exxon Economic Analysis
Компания Exxon Production and Research провела обобщенную экономическую оценку (26) для INCRA с помощью компьютерного исследования традиционной стальной конструкции, как показано на Рис. 20 .Были рассмотрены только изолированные системы оболочек из медно-никелевого сплава, поскольку они давали полную экономическую выгоду в результате предотвращения как загрязнения моря, так и коррозии. Расчетные модели были разработаны для ряда ситуаций, охватывающих три разных глубины воды, условия окружающей среды (ветер, волна и течение) от умеренных до тяжелых, а также рост морской среды от легких до тяжелых. Всего было рассмотрено 29 сценариев. Возможная экономия затрат была рассчитана на основе экономии веса установленной стали.Стоимость обшивки и ее установки не были включены в анализ из-за их изменчивости в зависимости от способа крепления.
FiКак установить кровлю из металлической черепицы
Если вы относитесь к тому типу домовладельцев, которые хотят приступить к установке новой кровли, проще всего установить кровельную систему из металлической черепицы.
Большинство систем металлической черепицы имеют четырехстороннюю конструкцию блокировки, а панели обычно достаточно малы, чтобы их можно было легко установить без использования каких-либо сложных инструментов.
Подготовка колоды:
Первый шаг — подготовка настила крыши. В новой конструкции кровля из металлической черепицы может быть установлена поверх любого типа твердого покрытия, такого как фанера или деревянные доски / доски, между которыми нет промежутков.
В качестве альтернативы, крышу из металлической черепицы можно установить поверх старой битумной черепицы, если вы не хотите ее срывать, при условии, что на крыше имеется только один слой существующей черепицы.
Установка подкладки:
Следующим шагом в подготовке настила крыши является использование специального материала, называемого кровельной подложкой.Он изготовлен из дышащего синтетического материала и предназначен для обеспечения дополнительного уровня защиты от конденсации, а также для того, чтобы крыша имела легкий ветерок, чтобы предотвратить гниение древесины.
При установке подкладки всегда необходимо, чтобы на карниз и фронтон настила крыши оставалось примерно полдюйма мембраны. Сначала мембрана закрепляется на одной стороне / конце крыши, затем она раскатывается горизонтально, пока не достигнет другой стороны крыши, где она также закрепляется специальными гвоздями с цветными (обычно ярко-оранжевыми или зелеными) пластиковыми заглушками.
По мере продвижения по настилу крыши к коньку каждый последующий уровень / ступень мембранного материала должен перекрывать предыдущий слой примерно на шесть дюймов.
Установка металлических планок и деталей отделки
После того, как настил крыши подготовлен, следует установить начальную планку или водосточную кромку. Он установлен напротив лицевой панели. Расстояние должно составлять полдюйма, и ваша начальная / водосточная планка должна быть закреплена подходящими гвоздями (алюминиевыми гвоздями, если вы устанавливаете алюминиевую черепицу) с соответствующими шайбами на расстоянии примерно 12 дюймов.
Обратите внимание, что если вы устанавливаете стальную черепицу, вам необходимо использовать гвозди из оцинкованной стали, чтобы избежать коррозии из-за использования несовместимых металлов / сплавов.
Как соединить бытовую проводку для удлинения цепей
По коду количество проводов в коробке ограничено в зависимости от размера коробки и калибра провода. Подсчитайте общее количество проводов, разрешенных в коробке, перед добавлением новой проводки и т. Д. Перед началом электромонтажных работ ознакомьтесь с местными нормативными актами и требованиями разрешений.Пользователь этой информации несет ответственность за соблюдение всех применимых норм и передовых методов при выполнении электромонтажных работ. Если пользователь не может самостоятельно выполнить электромонтажные работы, следует проконсультироваться с квалифицированным электриком. Как читать эти диаграммы
При ремонте может потребоваться сращивание проводов для перемещения цепей или добавления новых устройств. Соединение — это соединение двух или более проводов путем их скручивания. Пластиковый соединитель, называемый проволочной гайкой, используется для изоляции и фиксации стыка.Используйте размер гайки для проволоки, соответствующий количеству и калибру проводов, которые вы используете.
Соединения для сращивания проводов должны быть размещены внутри закрытой электрической коробки, известной как распределительная коробка. Распределительная коробка обычно квадратная и металлическая. После установки коробку нельзя скрывать внутри стен или потолка, чтобы она оставалась доступной в любое время.
По коду общее количество проводов, разрешенных в розетке, известное как заполнение коробки, ограничено размером коробки и калибром проводов.К проводникам относятся не только провода, но и такие устройства, как переключатели, розетки и некоторые другие металлические детали. Сумма всех проводников должна быть меньше кубического дюйма емкости розетки.
Для расчета заполнения коробки каждый провод 14awg, входящий в коробку, умножается на 2. Двенадцать проводов калибра умножаются на 2,25. Все заземляющие провода считаются как 1, умноженная на самый большой калибр провода в коробке. Например, все провода заземления, входящие в коробку, равны 1 X 2,25 для провода 12AWG.
Количество устройств, включая переключатели и розетки, умножается на 2-кратный размер самого большого диаметра провода в коробке.Любые металлические зажимы учитываются как 1-кратная длина самого большого провода. Пигтейлы и другие соединения, которые находятся в коробке, не учитываются. Для более подробного объяснения того, как точно подсчитать количество проводников, проверьте это перед добавлением новых проводов или устройств.
Распределительная коробка
Распределительная коробка имеет несколько отверстий со съемными заглушками по бокам и сзади. Выберите отверстия, удобно расположенные для соединяемых кабелей, и снимите заглушки. Имейте кабельный зажим для каждого и ослабьте винты, чтобы открыть хомут.Протяните около 8-10 дюймов кабеля через зажим и затяните вокруг него хомут, чтобы он крепко держался, но не зажимал пластик.
Разорвите оболочку кабеля, оставив около 1/4 дюйма, покрывающего провода. Обрежьте оболочку, чтобы удалить ее, и снимите примерно 3/4 дюйма пластиковой изоляции с конца каждого провода. Избегайте надрезов и царапин на медном проводе при снятии изоляции.
Вставьте зажим с присоединенными проводами в отверстие распределительной коробки и изнутри коробки наденьте прилагаемую гайку на провода и на резьбу зажима.Поверните гайку до упора на резьбу, а затем с помощью отвертки и молотка постучите по ней до упора.
Соединение проводов
Лучший способ удалить изоляцию, не повредив медь, — это использовать инструмент для зачистки проводов. У большинства стрипперов есть набор резаков для самых обычных калибров. Осторожно поверните стриптизерши назад и вперед один или два раза и снимите изоляцию прямо с конца.
Удерживайте провода вместе так, чтобы концы совпали, и скрутите их вместе по часовой стрелке с помощью плоскогубцев.Сделайте 1 или 2 оборота, чтобы образовалось прочное соединение, стараясь не врезаться в медь губками плоскогубцев.
Если концы проводов слишком далеко друг от друга, гайка не закрепится должным образом. Убедитесь, что концы совпадают, прежде чем скручивать их вместе. При необходимости отрежьте немного кончика, чтобы достать их еще до присоединения разъема.
Наденьте разъем по часовой стрелке на скрученные провода, убедившись, что внизу нет оголенной меди. Осторожно потяните за разъем, чтобы убедиться, что он надежно закреплен.Вы можете обернуть изолентой провода и колпачок для дополнительной безопасности или просто вставить стыки в заднюю часть коробки и прикрепить крышку.
Еще подобное на Do-It-Yourself-Help.com
Глоссарий электрических терминов — Do-it-yourself-help.com
Эта страница содержит алфавитный список бытовых электрических терминов и определений, помогающих определить инструменты, проводку и устройства, используемые для электромонтажных работ по всему дому.
Электроинструменты и материалы
- Ампер:
- Сокращение от ампера, единицы измерения тока или количества электричества, проходящего через цепь.Номинальный ток устройства или кабеля определяет величину тока, с которой он может безопасно работать. Типичные бытовые схемы начинаются с 15 ампер и доходят до 50 или 60 ампер.
- Армированный кабель:
- Электрический кабель в спиральной металлической оболочке. Ранний бронированный кабель, кабель BX, нес два электрических провода без заземления. Металлическая оболочка служила землей. Более поздние версии имели алюминиевый заземляющий провод, намотанный на спираль. Более новый армированный кабель включает изолированный провод заземления.
- Коробка:
- Электрические или розеточные коробки сделаны из металла или пластика и используются для размещения проводных соединений, в том числе таких устройств, как переключатели и розетки, а также распределительных коробок для защиты стыков проводов.Формы бывают: квадратные, круглые, восьмиугольные и прямоугольные. Доступны размеры до 4 квадратных дюймов. Используйте коробку самого большого размера, чтобы обеспечить необходимое NEC пространство для проводов и других проводников.
- Шина:
- Длинная медная шина внутри сервисной панели или коробки выключателя. Все нейтральные и заземляющие провода присоединены к шине заземления, чтобы завершить электрический путь. В некоторых случаях сервисная панель может иметь отдельные шины для нейтрали и земли.
- BX Cable:
- См. Армированный кабель.
- Кабель:
- Два или более провода, заключенных в защитную оболочку, называются электрическим кабелем. Armored, UF и NM — все названия бытовых электрических кабелей. Каждый тип кабеля доступен для разного калибра провода. Стандартные бытовые электрические кабели варьируются от 14 AWG (американский размер провода) до 6 AWG, причем 14 имеют наименьшие жилы, а 6 — самые большие. В бытовых электрических системах провод 14 калибра используется для цепей на 15 ампер, калибра 12 для цепей на 20 ампер, 10 AWG для 30 ампер, 8 AWG для 40 ампер и 6 AWG для цепей 50 и 60 ампер.
- Электрический кабель доступен с 3 или 4 проводами, проходящими через оболочку. Кабель с 3-мя жилами обозначается такими ярлыками, как 14/2 и 12/2, где два обозначают черный и белый токоведущие провода в кабеле. Другой провод, заземляющий, в этой маркировке не учитывается. 4-жильный кабель называется кабелем 14/3 или 12/3. Здесь 3 провода несут электричество: черный, красный и белый. Все бытовые кабели выпускаются с 2 или 3 токоведущими жилами и одним заземлением.
- Автоматический выключатель:
- Мощный выключатель цепи, расположенный на сервисной панели и предназначенный для мгновенного отключения электричества в случае перегрузки или короткого замыкания. Автоматические выключатели рассчитаны на ток, который они могут выдерживать. Автоматические выключатели на 15 А используются с кабелем калибра 14 для общего освещения и цепей розеток. Для более тяжелых нагрузок, таких как микроволновые печи и посудомоечные машины, используются автоматические выключатели на 20 ампер с кабелем калибра 12. Для электрического водонагревателя или сушилки для белья используются выключатели на 30 ампер с проводом 10 калибра.Для большой кухонной плиты потребуется выключатель на 50 А и провод 6 калибра.
- Проводник
- Все, что позволяет электричеству проходить через него, является проводником. Металлы обычно являются хорошими проводниками, а медь — одним из лучших.
- Кабелепровод:
- Труба, по которой проходит электрический кабель для защиты от повреждений. Доступны трубы из металла и ПВХ. Трубопровод требуется в таких местах, как недостроенные подвалы, где электрическая проводка оголена и, следовательно, уязвима для повреждения.
- Непрерывность:
- Бесперебойный путь электричества. Провод от одного конца до другого имеет непрерывность, установите переключатель между двумя концами и выключите его, чтобы разорвать путь и прервать целостность.
- Ток
- Электричество, которое течет из одного места в другое, называется током. Сила электрического тока измеряется в амперах или амперах.
- Двухконтурная розеточная коробка:
- Настенная розетка, в которой два устройства расположены рядом, как два настенных выключателя у двери.Также обычно доступны трехгнездные коробки для размещения трех устройств в одном месте.
- Дуплексная розетка:
- Настенная розетка с двумя розетками. Они доступны с номиналом 15 и 20 ампер, а также со специальными прерывателями цепи замыкания на землю (gfci) и изолированными розетками заземления.
- Fish Tape:
- Жесткая плоская металлическая лента, используемая для прокладки электрического кабеля через готовую стену или потолок. Жесткая природа ленты позволяет проталкивать ее через большинство препятствий в полости стены, поворачивая катушку в любую сторону.См. Раздел «Выполнение новой проводки» для получения дополнительной информации о рыболовном кабеле.
- Предохранитель:
- Защитное устройство, используемое для прерывания электрического тока в случае короткого замыкания или перегрузки. Они могут быть изготовлены из стекла с резьбовым основанием для цепей на 120 вольт или в виде картриджа с медными крышками на каждом конце для цепей на 240 вольт. Предохранители чаще всего встречаются в старых домах с небольшими сервисными панелями на 60 А.
- Greenfield:
- Гибкий металлический канал для прокладки новой электропроводки.Другое название бронированного кабеля, указанное выше.
- Заземляющий провод
- Предохранительный провод, включенный в бытовую электрическую цепь, для передачи тока непосредственно на землю в случае короткого замыкания. Заземляющий провод в бытовом электрическом кабеле обычно выполняется из чистой меди, но также может быть покрыт зеленой пластиковой изоляцией.
- Прерыватель цепи защиты от замыкания на землю (GFCI):
- Устройство безопасности, предназначенное для мгновенного прерывания электрического пути при обнаружении изменений в потоке электрического тока.Розетки GFCI необходимы в ванных комнатах, кухнях, гаражах и недостроенных подвалах, а также при любой внешней установке. Также доступны автоматические выключатели GFCI для защиты всей ответвленной цепи.
- Hot Wire
- Токоведущий провод в электрической цепи. В бытовой электросети может быть один или два горячих провода. Эти провода всегда изолированы и могут быть окрашены в черный или красный цвет, а в случае некоторых потолочных вентиляторов горячий провод также может быть окрашен в синий цвет.
- Изолятор
- Все, что препятствует электрическому потоку, является изолятором. Изоляторы необходимы в электрических цепях для сдерживания прохождения тока и предотвращения короткого замыкания или поражения электрическим током. Виниловый пластик используется как изолятор для бытовых электропроводов.
- Распределительная коробка:
- Электрическая розеточная коробка с кабельным сращивателем, закрытая для защиты соединения.
- Плоскогубцы линейного мастера:
- Инструмент для резки проволоки для тяжелых условий эксплуатации, необходимый для резки толстых кабелей.
- Мультиметр:
- Проверка целостности цепи, напряжения, тока и сопротивления. Доступны как аналоговые, так и цифровые измерители. Цифровой счетчик прост в использовании, легко читается и недорого. Аналоговые счетчики не так просты в использовании или считываются, и они устаревают.
- Плоскогубцы:
- Удобны для работы в ограниченном пространстве. При подсоединении к винтовым клеммам на светильниках, переключателях и розетках загните провода в крючок.
- NM Кабель:
- (Неметаллический кабель) Бытовой электрический кабель с виниловой пластиковой оболочкой, используемый для прокладки электропроводки через внутренние стены.
- Нейтральный провод
- Токоведущий провод в электрической цепи, также называемый проводом заземленной цепи , он служит обратным путем для тока и подключается к заземлению на сервисной панели. В бытовых электрических цепях нейтральный провод окрашен в белый или серый цвет. В некоторых схемах белый или серый провод используется в качестве горячего провода, когда это будет сделано, он будет помечен черной лентой или краской, чтобы идентифицировать его как горячий.
- Пигтейл
- Короткий отрезок провода, прикрепленный к проводам цепи и закрытый гайкой.Используется для соединения с клеммным винтом на устройстве, таком как розетка, или с клеммой заземления внутри электрической коробки.
- Розетка
- Розетка для подключения к электрической цепи, обычно с вилкой прибора. Дуплексные настенные розетки являются наиболее распространенным типом, но более крупные розетки также встречаются в бытовых электрических системах.
- Анализатор розеток:
- Вставное устройство, которое определяет конфигурацию проводки электрической розетки.С помощью системы индикаторов этот тестер подтвердит, что розетка правильно подключена, а также укажет на проблему с проводкой и в чем проблема. Это важно для поляризованных заземленных розеток, которые могут быть неправильно подключены и по-прежнему питать лампу или другое простое испытательное устройство.
- Модернизация электрического шкафа
- Эти электрические коробки, также называемые старыми установками, имеют встроенные зажимы для крепления к готовым стенам. Все, что нужно для его установки, — это вырезать отверстие нужного размера в полой части стены и вставить коробку.Их можно использовать в гипсокартоне, штукатурке или панелях. Они лучше всего подходят для установки настенных розеток и выключателей. Поскольку старые рабочие боксы не предлагают большой поддержки, они не являются хорошим выбором для установки нового потолочного крепления.
- Сервисная панель:
- Автоматический выключатель или блок предохранителей. Электричество поступает в бытовую электрическую цепь через сервисную панель и распределяется оттуда через автоматические выключатели или предохранители в ответвленные цепи.
- Короткое замыкание:
- Непреднамеренный перетекание электричества из цепи в проводник вне цепи.Короткое замыкание может произойти, когда горячий провод цепи касается чего-либо, кроме предполагаемого контакта. Короткое замыкание приведет к тому, что автоматический выключатель, предохранитель или gfci мгновенно отключат электрический ток, чтобы предотвратить травму или пожар.
- Переключатель:
- Устройство для контролируемого прерывания тока в цепи. Однополюсный однопозиционный выключатель света (SPST) — наиболее распространенный тип, встречающийся в бытовых электрических цепях. Они имеют один набор контактов и могут быть включены или выключены. Однополюсный двухпозиционный переключатель (SPDT) имеет два набора контактов и может переключаться между ними для переключения тока между двумя отдельными путями.Трехпозиционный переключатель является примером бытового переключателя SPDT.
- Переключатель Loop:
- Двухжильный кабель, идущий от осветительной арматуры к выключателю на стене. Его единственная функция — управлять включением и выключением света.
- UF Cable:
- Подземный питающий кабель, используемый для прокладки электричества под землей. Оболочка этого кабеля толще и прочнее, чем у кабеля NM, используемого для внутренних работ.
- Напряжение:
- Сила или давление, которое вызывает прохождение электричества, измеряется в вольтах.Напряжение также называется электродвижущей силой (ЭДС) и возникает из-за разницы потенциалов в напряжении от одного конца цепи к другому. При 120 вольт на автоматическом выключателе и 0 вольт на осветительной арматуре щелчок переключателя заставит 120 вольт течь до 0 вольт.
- Мощность:
- Мера электрической мощности. Количество произведенной энергии, рассчитанное путем умножения тока цепи на напряжение цепи. (амперы X вольт = ватты)
- Гайка для провода
- Разъем для закрепления и изоляции стыка проводов, когда два или более оголенных провода скручены вместе для замыкания цепи.
- Кусачки:
- Используйте их для обрезки отдельных проводов. Используйте линейные плоскогубцы, чтобы отрезать NM, UF и другие толстые кабели.
- Инструмент для зачистки проводов:
- Удалите изоляцию с провода, не повредив медный провод. Большинство инструментов для зачистки имеют насечку для резки проволоки калибра от № 10 до № 18. У большинства устройств для зачистки проводов также есть режущая кромка для быстрой резки отдельных проводов.
DIY (Сделай сам) Инструкции по установке
1 DIY (Сделай сам) Инструкции по установке Детали набора для самостоятельной сборки: Необходимые инструменты: Отвертки Phillips №1 и №2 Два 2.Шестигранный ключ на 5 мм Плоскогубцы Маленькая отвертка с плоским лезвием Гаечный ключ на 10 мм Гаечный ключ на 11 мм 1) Отсоедините электрическое соединение педального узла G25 / 27 от рулевого колеса. ВНИМАНИЕ: Если попытаться выполнить установку с подключенным электричеством, это может привести к ПОВРЕЖДЕНИЮ G25 / G27 и вашего компьютера.
2 2) Снимите поверхности педалей с помощью шестигранного ключа на 2,5 мм. (Мы узнали, что неплохо иметь контейнер для небольших винтов и деталей, чтобы они не потерялись.) 3) Переверните педальный узел G25 / G27. 4) ПРИМЕЧАНИЕ. Если вы работаете на твердой поверхности, будьте осторожны, чтобы не повредить рабочую поверхность. Рекомендуется подложить под комплект полотенце, так как педали имеют острые края. 5) Выкрутите 4 черных винта в центре педального узла. (Это винты №2 с головкой под крестовую отвертку).
3 6) Затем удалите 14 серебряных винтов, включая 2 винта, под планкой ковра. (Это винты №1 с крестообразным шлицем.) 7) После того, как все винты будут удалены, снова переверните педальный узел так, чтобы он теперь оказался лицевой стороной вверх.8) Затем осторожно снимите переднюю крышку с педального узла; подъем с переднего края. ВНИМАНИЕ! Провода очень тонкие и хрупкие. Тормозной модуль G25 / G27 теперь свободен; положите его на бок так, чтобы провода были обращены вверх. 9) Затем найдите провода, идущие к тормозному модулю. Выкрутите винт заземления (головка Philips №2), которым черный провод крепится к педальному блоку.
4 ПРИМЕЧАНИЕ. Если вы сможете отодвинуть черную термоусадочную пленку от соединений, это упростит их снятие и повторное прикрепление.10) Возьмите плоскогубцы и осторожно извлеките 3 соединителя лопатки по одному из тормозного модуля. Снимите тормозной модуль. 11) Используя шестигранный ключ на 2,5 мм, открутите два винта, которые крепят красный пластиковый поршень к поверхности педали.
5 После того, как вы ослабите оба винта, если они продолжают вращаться и не выходят, попробуйте надавить на поверхность педали, поворачивая винты. 12) Снимите и сохраните латунный вал с красного пластикового поршня.13) Снимите оба болта с буртиком, которыми основание пластикового поршня и поверхность педали крепятся к раме педали.
6 14) Используйте небольшую отвертку, чтобы удалить стопорную шайбу на потенциометре. 15) Снимите черную пластиковую шестерню и пружину с потенциометра. 16) Снимите гайку 11 мм, крепящую потенциометр к основанию педали, затем снимите потенциометр и пружину.
7 17) Ослабьте винт с крестообразным шлицем, который удерживает черную пластиковую шестеренку на поверхности педали, и снимите ее.18) Очистите внутреннюю поверхность педали прилагаемой спиртовой салфеткой. ПРИМЕЧАНИЕ. В следующих шагах необходимо соблюдать осторожность при установке печатной платы. Как только лента входит в контакт, ее очень трудно переместить. 19) Снимите пленку с двух кусков двойной липкой ленты на обратной стороне печатной платы.
8 20) Совместите конец печатной платы с выходом проводов, совместите его с нижней стороной педали и плотно прижмите. 21) Отогните черную ленту на основании педали, чтобы открыть квадратное отверстие за ней.22) Проденьте небольшую соединительную плату через квадратное отверстие изнутри наружу. Не заставляйте его! При правильной ориентации он без сопротивления проскользнет через отверстие.
9 23) Приложите черную ленту к основанию педали. 24) Прикрутите соединительную плату к основанию педали, убедившись, что серебряные распорные шайбы расположены следующим образом. Две шайбы между печатной платой и металлическим каркасом и одна шайба между металлическим каркасом и гайкой.25) Затяните болт так, чтобы разъемы были обращены к задней части основания педали.
10 26) Вставьте белые пластиковые втулки обратно в лицевую часть педали и вставьте ее в основание педали. 27) Установите болт с буртиком, который удерживает поверхность педали в основании педали, убедившись, что провода проходят за болтом с буртиком. ВНИМАНИЕ: Если провода не проложены за болтом, они могут защемиться под лицевой стороной педали и повредиться. Гарантия НЕ распространяется на эти и любые последующие повреждения компьютера или электроники Perfect Pedal.
11 28) Убедитесь, что латунный вал, снятый с красного поршня, свободно проходит через отверстие в цилиндре Perfect Pedal. ПРИМЕЧАНИЕ: НЕ применяйте силу. Он должен свободно падать в отверстие без сопротивления. В некоторых редких случаях (педали с очень большим количеством часов) на концах латунного вала могут быть заусенцы. Если латунный вал не будет свободно скользить в отверстии цилиндра, необходимо удалить заусенцы на концах латунного вала с помощью напильника или мелкой наждачной бумаги.29) Убедившись, что латунный вал плавно входит в педаль Perfect Pedal, нанесите на латунный вал прилагаемую смазку и вставьте его в отверстие в цилиндре. ПРИМЕЧАНИЕ. Если в отверстие, в которое входит латунный вал на цилиндре Perfect Pedal, есть черная втулка, смазывать вал не нужно. Ваш комплект может иметь или не иметь прилагаемый пакет со смазкой.
12 30) Установите по одной белой пластиковой шайбе с каждой стороны латунного вала, затем осторожно вставьте узел в поверхность педали, убедившись, что пластиковые шайбы остаются на своих местах правильно.31) Выровняйте цилиндр так, чтобы вы могли видеть конец резьбовых отверстий латунных валов через отверстие на лицевой стороне педали, и завинтите винты пальцами. 32) С помощью двух шестигранных ключей на 2,5 мм затяните винты, убедившись, что ОБЕИХ СТОРОНЫ затянуты.
13 33) Вставьте болт с буртиком в основание педали, удерживая вал Perfect Pedal на месте. Убедитесь, что вы разместили две проставки, по одной с каждой стороны вала. Прокладки в вашем комплекте могут быть черными или серебристыми.34) Теперь ваш модуль Perfect Pedal собран и готов к установке в G25 / 27. ВНИМАНИЕ: Если вы используете кабель или устройство Bodnar, вам нужно будет подключить блок Perfect Pedal немного иначе. Пожалуйста, перейдите к инструкциям Bodnar для получения дополнительной информации. Несоблюдение инструкций Bodner может привести к повреждению педали Perfect Pedal и / или компьютера!
14 35) Возьмите модуль Perfect Pedal и положите его на бок в нижней части педального узла G25 / G27 разъемами проводов вверх.Осторожно установите 3 плоских разъема (белый к белому, красный к красному и черный к черному). 36) Затем снова прикрутите винт заземления и черный провод. Убедитесь, что конец провода направлен в сторону верхней части модуля Perfect Pedal. 37) Установите модуль Perfect Pedal на основание. Удерживая черную крышку под углом 90 градусов, защелкните жгут проводов на место и убедитесь, что провод, выходящий из педального узла, находится в предусмотренной выемке.