Устройство пиролизного котла отопления | Отопление дома и квартиры
Устройство пиролизного котла отопления, общая схема
Пиролизный котел отопления, как и все твердотопливные котлы, состоит из камеры сгорания и окружающей его водяной рубашки. Общая схема твердотопливного котла отопления, к которым относится пиролизный котел отопления, предполагает, что камера сгорания разделена на две части. Верхняя камера это топливная камера. В нее загружается твердое топливо, через верхний люк, и здесь же производится первичный поджог топлива.
В этой камере топливо, при недостатке кислорода, нагревается до температуры 450°C-600°C.При недостатке кислорода, горение не наступает, зато выделяется пиролизный газ. Под действием тяги воздуха в камере (тяга вниз) пиролизный газ поступает в нижнюю камеру, где смешиваясь с воздухом горит при температуре около 1000±200 °.
Образованные при горении газы поступают в дымоотвод с вентилятором. По пути движения газы проходят через теплообменник и охлаждаются до температуры 140-150 °C.
Качественные характеристики пиролизного котла отопления
- В пиролизном котле отопления топливо сгорает очень медленно, поэтому для беспрерывной работы пиролизного котла достаточно двух загрузок топлива в сутки
- Коэффициент Полезного Действия (КПД) пиролизного котла очень высок и составляет 85-95 %.
- Мощность котла легко регулируется изменением потока подачи воздуха в топливную камеру сгорания. Подача воздуха регулируется открыванием и закрыванием воздушных заслонок. В некоторых моделях пиролизных котлов, этот процесс автоматизирован.
- Охлаждение газов образующихся при сгорании пиролизного газа, охлаждается, а, следовательно, для труб дымоотвода не требуются особые пожаропрочные и корозийноустойчивые характеристики.
- Главным положительным свойством пиролизного котла отопления является минимальное количество сажи и золы при горении. Также горение пиролизного газа выделяет сравнительно меньшее количество вредных веществ выделяемых в атмосферу.
Пиролизный котел отопления можно определить по белому, а не черному дыму, поднимающемуся из дымохода.
Минусы пиролизного котла отопления
Пиролизный котел относится к энергозависимым котлам отопления. Основным условием работы пиролизного котла является постоянное движение воздуха в камере горения. Для этого нужны вентиляторы, а для работы вентилятора нужен постоянный источник электроснабжения. При некоторых обстоятельствах это может затруднить использование пиролизного котла отопления.
Хотя стоит отметить, что производители не стоят на месте и есть пиролизные котлы, работающие без источника электропитания. На этом об устройстве пиролизного котла отопления все! Тепло вашему дому!
©obotoplenii.ru
Другие стать раздела: Котлы отопления
разновидности, плюсы и минусы, самостоятельное изготовление
Меню- Главная
- Рубрики
- Все о крышах
- Все о лестницах
- Фундамент
- Стены
- Пол
- Потолок
- Отделка
- Интерьер
- Тепло в доме
- Ландшафт
- Недвижимость
- Своими руками
- Инвентарь
- Интересное
- Разное
- Другое
- Карта сайта
- Главная
- Рубрики
- Все о крышах
- Все о лестницах
- Фундамент
- Стены
- Пол
- Потолок
- Отделка
- Интерьер
- Тепло в доме
- Ландшафт
- Недвижимость
- Своими руками
- Инвентарь
- Интересное
- Разное
- Другое
- Карта сайта
Что такое пиролиз
Содержание
- 1 Что такое пиролиз
- 2 Что такое пиролизный котел?
- 3 Из чего состоит пиролизный котёл
- 4 Суть процесса пиролиза
- 5 Основные характеристики пиролизных котлов
- 6 Принцип работы
- 6.
1 Плюсы и минусы оборудования
- 6.
- 7 Конструкция и принцип работы
- 8 Процесс изготовления пиролизного котла своими руками
- 8.1 Схема пиролизного котла на отработке
- 8.2 Пиролизный котел для древесных отходов
- 8.3 Горизонтальная версия пиролизного котла
- 9 Как работает газогенераторное оборудование с верхней загрузкой?
- 10 Основные преимущества газогенератора
- 11 Как собрать своими руками пиролизный агрегат?
- 11.1 Перечень инструментов и материалов
- 11.2 Пошаговое изготовление пиролизного газогенератора
- 12 Как ввести котел в эксплуатацию?
- 13 Соблюдение
Как выбрать пиролизный твердотопливный котел отопления, принцип работы котла и особенности
Пиролизный котел, он же газогенераторный, появился на рынке несколько лет назад. Это одна из разновидностей твердотопливных котлов. В чем же их особенность и каков принцип работы?Как любой твердотопливный котел, пиролизный удобен в местах, удаленных от газовых магистралей. В качестве топлива используется недорогое привычное топливо — древесина. Конструкция котла включает две камеры, обеспечивающих особую организацию процесса горения.
Принцип работы
В одной камере котла происходит процесс, который идентичен технологическому процессу получения угля из древесины: высокая температура и ограниченный доступ кислорода заставляют дрова тлеть, при этом выделяется пиролизный газ. Пиролизный газ поступает через форсунку во вторую камеру — камеру сжигания и там смешивается с воздухом. В итоге сжигаются одновременно в разных камерах и древесный уголь, и выделившийся пиролизный газ. Такая схема горения максимально увеличивает КПД и длительность горения одной закладки топлива.
Стабильную мощность обеспечивает прогорание топлива не сразу в полном объеме заложенного, а только части, необходимой для процесса горения. Некоторые модели пиролизных котлов имеют дополнительно установленный тепло-электронагреватель.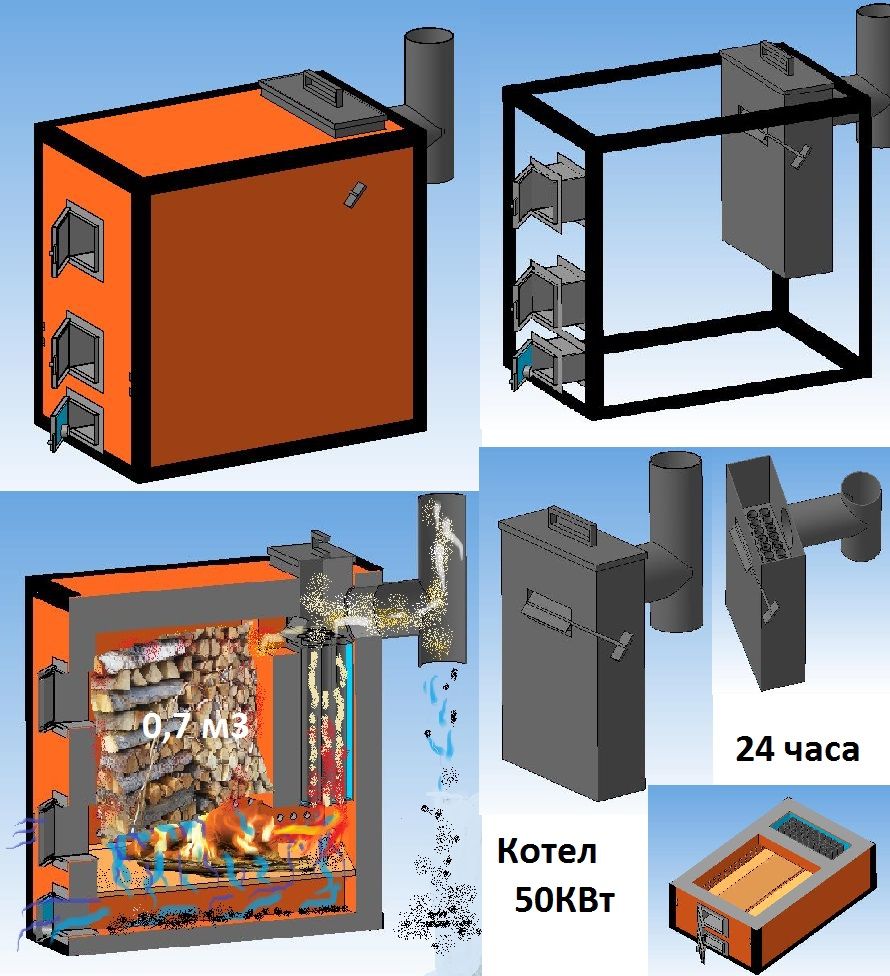
Также к положительным особенностям относятся их экологические характеристики. Пиролизные котлы, по сравнению с обычными дровяными или угольными котлами, имеют меньшие выбросы угарного газа.
К недостаткам относятся необходимость регулярной чистки золы, а также высокая стоимость и особые требования к качеству топлива (влажность должна быть не выше 18%). Максимальное КПД достигается при использовании хорошо просушенной древесины. Использование сырой древесины может сократить срок службы котла и стального дымохода.
Пиролизные котлы делятся на две категории по требованиям к топливу:
- К первой категории относятся пиролизные энергонезависимые котлы, достаточно прихотливые к используемому топливу.
Влажность древесины не должна превышать 25%. Макулатуру, хворост, древесную щепку, отходы коры, ДСП — запрещено использовать в энергозависимом типе.
- Вторая категория — утилизаторы древесных отходов потребляют и торф, и древесину, и уголь. Влажность топлива может быть в пределах 50%.
Как выбрать пиролизный котел длительного горения
При выборе котла необходимо оценить:
- Внешний вид котла, в том чи
полный разбор устройства и принципов работы, что можно своими руками
Пиролизный котел – один и самых перспективных отопительных приборов на ближайшую перспективу: его КПД может превышать 90%, топливо (преимущественно пеллеты) дешево и экологично, оно изготавливается из отходов растительной биомассы. Современные технологии позволяют производить пиролизные котлы, пригодные для установки в городской квартире, но устройство таких агрегатов (см. рис.) весьма сложно, а цена высока. Поэтому наличествует большой интерес к теме: можно ли и как сделать такой полезный отопительный прибор своими руками?
Устройство пиролизного котла
Зачем эта статья?
Пиролизный котел – не печка с водогрейкой. В нем закручен, в буквальном смысле слова, целый клубок сложных процессов. И разработка работоспособного котла – серьезнейшая инженерно-конструкторская задача, требующая солидных знаний, опыта, месяцев, если не лет, напряженного труда и немалых затрат на эксперименты и обкатку готовой конструкции. Векового опыта и проверенных поколениями технических решений, как для традиционных печей, тут нет.
Примечание: Информацию о более простых печах длительного горения, эффективность работы которых основана на пиролизе, можно найти по ссылке.
Чертежи пиролизного котла в свободной раздаче если и найдутся, то лишь 2-3 общих вида плюс 3-4 разреза. Имея соответствующее образование, опыт работы и посидев месяц-другой в ACAD’e и CorelDraw, деталировку можно составить самому. Но спецификаций все равно нет, из какого материала делать ту или иную деталь, можно только догадываться, либо просчитывать весь агрегат заново.
Авторы конструкций за полный комплект техдокументации просят, как правило, не очень дорого. На кофе больше уйдет, если «доковыривать» самому. Но как по ознакомительным картинкам определить, будет ли оно работать вообще, насколько эффективно и подойдет ли мне, к моим конкретным условиям и требованиям?
Аналогичные вопросы возникают у тех, кто решил купить себе пиролизную печь или котел. Производители с продавцами предлагают их наперебой, по данным обследования и замеров на месте подберут подходящую модель. Но где гарантия, что у конкурентов не найдется дешевле, экономнее и надежнее? Обратите внимание на правую часть рисунка выше. Там разрезы топок двух моделей котла одной и той же фирмы, а внешний вид почти одинаков. Какая лучше подойдет вот для этого именно дома? С холодильниками-стиралками более-менее понятно, это бытовуха привычная, а котел как выбирать?
Так вот, данная статья как раз и предназначена для того, чтобы дать и неподготовленному читателю ясное представление: что же это такое – пирокотел, что там у него внутри находится, что происходит, как все взаимосвязано и взаимодействует, на что и как влияет конструкция каждого из составляющих агрегат узлов.
Примечание: понятие котел отопления означает, что водогрейный контур, во-первых, полнопоточный, т.е. котел выдает расход горячей воды, необходимый для непрерывной работы системы отопления. Во-вторых, водогрейный регистр – неотъемлемая часть конструкции. В шведскую печь, к примеру, можно встроить водогрейку, но только для ГВС, и с накопительным баком. А можно потом и убрать, печь как грела и варила-жарила, так греть-стряпать и будет. А из котла водогрейку не уберешь, без нее, или с пустым контуром, он без аварийной автоматики прогорит или взорвется. В-третьих, варочной поверхности в котле нет и быть не может, все тепло уходит на обогрев.
Пиролиз и газогенерация
Принцип работы пирокотла основан на явлении пиролиза – термического (при повышенной или высокой температуре) разложения веществ сложного химического состава без участия дополнительных реагентов. Попросту говоря, молекулы вещества от нагрева расщепляются на более простые и легкие части. Применительно к органике в топке это значит, что продукты пиролиза гореть будут легче, сгорать полнее и тепла дадут больше.
При чистом пиролизе распад закладки топлива происходит без доступа воздуха в специальном сосуде – реторте. Далее пиролизные газы собираются в накопитель – ресивер и по мере надобности используются. По такой схеме были построены немецкие, итальянские и французские пиролизные установки для автомобилей времен войны. Для нагрева реторты использовалось тепло выхлопных газов.
КПД чистого пиролиза не очень высок, т.к. при остывании пиролизных газов часть горючих компонент осаждается. Гореть они могут, но через карбюратор их не протолкнешь. Кроме того, перед выездом нужно было довольно долго греть реторту от постороннего источника, а в поездке не забывать поддавать газку, чтобы давление в ресивере не упало, иначе не заведешься после остановки.
У нас твердого топлива и сейчас в избытке, а тогда было вообще хоть завались, поэтому наши топливные автоагрегаты строились газогенераторными: в реактор загружались деревянные чурки, разжигались чем попало и тлели еле-еле. Тепло для пиролиза давала часть самого топлива, пиролизные газы поступали прямо в карбюратор, а при длительной стоянке просто стравливались в атмосферу.
Важным достоинством газогенераторных установок было то, что их можно было подтапливать на ходу и они работали на любом виде твердого топлива. Автору известен случай, когда водитель полуторки с едва уже дышащим газогенератором (его родной дядя) на прифронтовой дороге попал под обстрел «мессера». В реактор тут же полетели валенки, ватник, ватные штаны, ушанка. Взбодрившийся движок опять потянул как следует, и водила с машиной спаслись. На хохот однополчан водила отвечал по-солдатски философски: «Жить захочешь – и … туда сунешь!»
Современные бытовые твердотопливные пиролизные котлы все без исключения газогенераторные. Иначе получить КПД выше 65-70% не получается. Но название «пиролизные» отнюдь не ошибочно: более 90% вырабатываемого тепла дает сгорание пиролизных газов. Поэтому далее в тексте выражения «пиролизный» и «газогенераторный» употребляются как синонимы, кроме случаев, когда иное специально оговорено.
Примечание: по умолчанию пиролизным считается также любой котел длительного горения на твердом топливе; там большую часть тепла дает также пиролиз. В масляных приборах длительного горения (печи на отработке или темном печном топливе, к примеру) более половины тепла дает сгорание испарившихся легких фракций, а самые тяжелые, тоже пригодные для пиролиза, оседают в шлам на дне резервуара. Поэтому считать масляные печки пиролизными можно только с большой натяжкой.
Как устроены пирокотлы?
На рис. показано устройство пиролизных котлов самых употребительных типов. Две верхних позиции – котлы с принудительной циркуляцией в рабочем (воздушно-газо-дымовом) тракте, т.е. с принудительной тягой. Две нижние – пиролизные котлы на естественной тяге. Разберемся вначале, что у них у всех общего, а затем перейдем к частностям.
Схемы устройства пиролизных котлов разных типов
О терминологии
У печников свой язык. Хайло, к примеру, не грубое ругательство, а устье топки специальной конструкции. На рисунках боров – горизонтальная часть дымохода. Шиберы – дроссельные заслонки, регулирующие поток воздуха/газов. Иногда для определенности воздушный дроссель так и оставляют дросселем, а шибером называют его же в газоходе/дымоходе. Применительно к пиролизным котлам газоход и дымоход различают: в дымоходе все уже прогорело до углекислого газа и воды, но еще горячее. В газоходе еще идут термохимические реакции.
Примечание: в других источниках вам может встретиться название «творило». В печном деле это не мешалка-колотушка для теста, а просто-напросто дверца с задвижкой. Вспомните: отворять, затворить. Еще у печников ход печи – это ее рабочий цикл или режим горения в ней. Т.е. двух- или многоходовая печь на самом деле двух- или многорежимная.
Общее
Общий у всех пирокотлов рабочий цикл; любой пиролизный котел работает следующим образом:
- Первичный наружный воздух поступает в камеру газификации, где тлеет топливо.
- Небольшая часть его кислорода расходуется на поддержание тления, обеспечивающего температуру газификации в 200-800 градусов.
- Пиролизные газы поступают через сопло (иногда его по-печному называют хайлом, хотя работает оно совсем не так, как хайло печи) в камеру сгорания.
- В нее же поступает вторичный воздух, и пиролизные газы горят.
- Некоторая часть пиролизных газов при наличии катализатора – частиц свободного углерода из топлива – восстанавливается до угарного газа и окислов азота, на что расходуется тепло.
- Восстановленные компоненты окисляются в камере дожигания, отдавая обратно тепло.
- Прореагировавшие дымовые газы проходят через теплообменник водогрейного регистра, а затем уходят в дымоход.
- Система терморегулирования поддерживает в камере сгорания оптимальную для полного сгорания температуру.
Примечание: не вполне забывшим химию из этого ясно – отбор тепла на этапах газификации, сгорания и догорания неизбежно резко ухудшит КПД установки и даст на выходе вредные и опасные газы.
В пирокотле непрерывно крутится огромное количество тепловой энергии, и нам доступно только то, что уже не нужно для самоподдержки рабочего цикла. Самодельный пиролизный котел должен проектироваться с полным знанием и пониманием этого обстоятельства, иначе получится очень плохая и опасная печь. Если где-то увидите чертежи в теплообменником в газификаторе, камере сгорания или дожигателе – в игнор без разглядывания.
Общие для пирокотлов также режимы работы. Их всего три, см. рис.
Режимы работы пиролизного котла
- Розжиг. Заслонка (дроссель, шибер) прямого хода открыта. Дымовые газы уходят прямо в дымоход – слева на рис.
- Рабочий режим, в центре. Заслонка прямого хода закрыта, идет пиролиз. Тяга в газоходе обеспечивается либо принудительно, либо естественным образом.
- Догрузка топлива, справа. Заслонка прямого хода открыта, но тяга в газооходе сохраняется некоторое время: он разогрет, и вентилятор, если он есть, не выключается. Пиролиз не прекращается.
Догрузку нужно производить быстро – кроме того, что цена топлива вылетает в трубу, может пойти угар.
И, наконец, общими для бытовых пирокотлов является также привередливость к топливу и материалам конструкции:
Из термохимии процессов в пирокотлах следует еще один их недостаток: небольшие пределы регулировки мощности при условии сохранения высокого КПД. Форсировать котел по теплу более чем на 50% не выйдет – топливо в газификаторе вспыхнет, и КПД упадет. И снизить ее более чем вдвое тоже не получится: пиролиз затухнет, КПД опять упадет, пойдет угар. Но в средних широтах тепловая мощность систем отопления по сезону должна меняться в 10-15 раз. Так что системы отопления на пирокотлах нужно проектировать в расчете на циклический режим прогрева, и крайне желательно при этом хорошенько утеплиться снаружи ЭППС. Пиролизный котел – детище века энергосберегающих технологий, в избе с земляным полом от него толку не будет.
О материалах
Самодельщику и покупателю нужно знать, что газификатор, камеры сгорания и дожигатель без жаростойкой футеровки долго не протянут. К примеру, на широко рекламируемые и, действительно, очень дешевые котлы на естественной тяге (см. далее) «Буржуй» имеется множество нареканий: за один-два отопительных сезона под камеры сгорания прогорает, литые из чугуна колосники корежатся.
Дешевизна «Буржуя» как раз и объясняется тем, что он не футерован. А состав и технология нанесения футеровки – главный секрет любой котлостроительной фирмы. И немалая доля стоимости готового изделия.
О топливе
Предпочтительные виды твердого топлива для пирокотлов – топливные пеллеты (именно под них проектируются промышленные модели) или дрова. Пиролизный котел на угле с высоким КПД проработает, пока не выйдут все летучие, их же в каменном угле не так-то много, а в древесном почти нет. Затем пойдет простое горение углерода с печным КПД. Высокоэффективный котел длительного горения на угле должен строиться на комбинированном рабочем цикле (на совмещенном ходу), при котором закладка топлива тлеет с поверхности, пиролизный цикл совмещен с горением и происходит непосредственно на гранулах топлива.
Сушилка для топлива
Примечание: влажность воздушно-сухой древесины может доходить до 50% Воздушно-сухая значит, что сушилась она на открытом воздухе под навесом; по
Пиролизные котлы длительного горения с водяным контуром
Когда в загородном доме, находящемся вдали от благ цивилизации, планируется организовать водяную систему отопления, то одним из способов теплоснабжения может стать котёл на твёрдом топливе с водяным контуром. Однако данный агрегат имеет как минимум два серьёзных недостатка: низкий КПД и быстрое прогорание топлива. А это значит, что, во-первых, необходимо постоянно хранить значительный запас энергоресурсов, а во-вторых, каждые 3-4 часа «подкармливать» своё огнедышащее чудо, подбрасывая в ненасытное жерло очередную порцию дров (угля, торфяных брикетов и т.п.). Хорошо, что нашлись умные люди и придумали агрегат, избавляющий от упомянутых неприятностей. Имеется в виду пиролизный (он же газогенераторный) котёл длительного горения, о котором и пойдёт речь.
Lavoro eco C-22.
Что собой представляет пиролизные котлы длительного горения с водяным контуром и как он работает?
Пиролиз является экзотермическим процессом, требующим создания особых условий, а именно высоких температур и ограниченной подачи кислорода, чтобы добиться медленного горения. Очевидно, что конструкция газогенераторного котла должна соответствовать этим требованиям.
Этот отопительный прибор является разновидностью твёрдотопливного котла, внутри которого происходит раздельное горение твёрдого топлива и сопутствующих газов. Из этого определения следует, что пиролизный котёл эффективно работает только на топливе, дающем высокий выход летучих веществ. К такому топливу относятся, прежде всего, древесина, торф и бурый уголь, имеющие органическую основу.
Топливный брикет.
Газогенераторный котел на твердом топливе имеет две камеры сгорания: верхнюю и нижнюю. Эти камеры разделены между собой колосниками. В верхней камере (топке) сжигается твёрдое топливо, при этом подача воздуха регулируется специальными задвижками (шиберами) таким образом, чтобы обеспечить медленное горение при достаточно высокой температуре (не менее 200 °C). В результате топливо разлагается на две фракции: древесный уголь (кокс) и смесь газов, состоящую, главным образом, из окиси углерода.
принцип работы, плюсы и минусы
Что такое пиролизный котел?
Содержание статьи
При значительном росте цен на энергоносители, вопрос об экономии денег в период отопительного сезона становится на первом месте. Как заставить твердотопливный котел гореть дольше при минимальной закладке дров? Где можно сэкономить, а где не получится?В последнее время, всё большее предпочтение отдается пиролизным котлам, которые как раз и обладают вышеперечисленными характеристиками. Помимо высокого КПД, пиролизные котлы способны очень долго поддерживать требуемую температуру теплоносителя, при этом образуя минимальное количество сажи.
О том, что такое пиролизный котел, в чём его преимущества и недостатки, будет рассказано ниже, в статье строительного журнала samastroyka.ru.
Что такое пиролизный котел: принцип работы
Пиролизный котел или как его ещё называют газогенераторный котел, существенно отличается по своей конструкции и принципу работы от обычного твердотопливного котла отопления. В работе пиролизного котла лежит принцип сухой перегонки топлива.
Для этого, топливо в пиролизном котле нагревается до очень высоких температур (600 и более градусов с плюсом). Однако, полноценно ему разгораться, и сгореть на считаные часы, не даёт отсутствие воздуха в камере сгорания.
При этом, образуется большое количество газа выделенного топливом при нагреве, который попадая во вторую камеру пиролизного котла, уже там начинает свое полноценное сгорания, вступая в реакцию с кислородом и углеродом. Такой подход позволяет уменьшить выброс вредных веществ в атмосферу почти на 5 раз, увеличить КПД пиролизного котла (до 95%), и время его работы.
Кроме того, как было сказано выше, в процессе работы пиролизного котла практически не остается отходов сгорания. Всё это позволяет максимально эффективно использовать энергоносители и сделать работу системы отопления полностью автономной.
Конструкция пиролизного котла
Для изготовления пиролизных котлов используется 4-6 мм сталь, вследствие чего вес котлов существенно утяжеляется. В конструкции котла имеется две камеры, расположенные одна над другой, и разделённые между собой специальными керамическими форсунками.
Неотъемлемой частью пиролизного котла, является и система управления, которая позволяет регулировать работу котла, не допуская его перегрева или наоборот, остановки. С этой целью в пиролизном котле установлены вентиляторы, коллектор, через который из котла удаляются продукты сгорания, и терморегуляторы.
Пиролизные котлы — это полностью автономное оборудование, которое позволяет автоматизировать работу системы отопления, как в частном доме, так и на предприятии. Для нормального функционирования пиролизного котла, используется древесина имеющая влажность не больше 20 процентов. В противном случае, КПД пиролизного котла существенно снижается.
Плюсы и минусы пиролизных котлов
Пиролизные котлы работают за счет термического разложения древесины, что даёт возможность получить дополнительную выгоду. Во-первых, при работе газогенераторного котла отсутствует зола и сажа, поэтому обслуживать такой твердотопливный котел приходится намного реже, чем обычный.
Во-вторых, за счет того, что древесина не горит в пиролизном котле, как в обычном котле, а только разлагается, выделяя при этом газ, удается существенно увеличить время работы котла. Только представьте себе, пиролизный котел при одной закладке дров способен проработать целые сутки, без какого-либо участия в этом человека.
В-третьих, как было сказано выше, КПД пиролизного котла на порядок выше, чем КПД обычного твердотопливного котла. В свою очередь, это позволяет максимально эффективно использовать энергоноситель, в качестве которого выступает древесина.
В-четвертых, при сгорании топлива в пиролизном котле, существенно уменьшается выброс вредных веществ в атмосферу. Ну и последнее, благодаря установленной автоматике, пиролизные котлы являются полностью автономным оборудованием в системах отопления.
Что же касается минусов, то их у пиролизных котлов, не так уж и много. К недостаткам, можно отнести высокую стоимость, требовательность котлов к качеству сжигаемого топлива, а также зависимость от электричества.
Так, например, средняя стоимость пиролизного котла варьируется в пределах 1000 $. Древесина для сжигания в газогенераторном котле должна быть не слишком влажная, поскольку в противном случае, серьезно пострадает КПД котла.
Ну и зависимость подобного рода оборудования от электричества, вполне понятна, ведь для работы вентиляторов и автоматики пиролизного котла, обязательно понадобится электропитание.
Пиролиз: устойчивый способ получения энергии из отходов
1. Введение
Лигноцеллюлозная биомасса рассматривается как многообещающий экологически чистый ресурс-заменитель углеродного топлива и химикатов. Существующие мировые поставки энергии зависят от невозобновляемых видов топлива, таких как нефть, газ и уголь, которые образуются естественным образом под земной корой. Однако сейчас количество ископаемого топлива ограничено. Из-за роста населения мира увеличивается потребление энергии на душу населения.Таким образом, очевидна неизбежность продолжения альтернативы генерации возможных источников энергии. Исследователи уделяют большое внимание использованию биомассы для производства продуктов с добавленной стоимостью. Кроме того, неорганическая составляющая биомассы незначительна и содержит незначительное количество азота, серы и золы. Следовательно, сжигание биотоплива является выгодным, поскольку оно производит менее токсичный газ, такой как оксиды азота (NO x ), диоксид серы (SO 2 ) и дым по сравнению с другими традиционными видами топлива. Даже выбросы углекислого газа (CO 2 ) можно контролировать, повторно используя его путем фотосинтеза [1]. Хотя многие теоретические методы были применены для преобразования в краткосрочной перспективе; то, что требуется, — это практическая фаза применения и демонстрация с соответствующим расчетом материального и энергетического баланса. Налажено промышленное термохимическое производство жидкостей, бионефти с помощью быстрого или мгновенного пиролиза, но до сих пор не реализовано для коммерциализации общей практики.
Для преобразования биомассы в продукты с добавленной стоимостью были приняты различные типы термохимических и даже биологических процессов. Среди этих процессов пиролиз более удобен, поскольку он имеет несколько преимуществ хранения, транспортировки и гибкости в обращении, таких как турбины, приборы для сжигания, котлы, двигатели и т. Д. В некоторых случаях твердую биомассу и отходы сложно переработать для исследований пиролиза . До сих пор он находится на предварительной стадии с точки зрения расширения и все же требует устранения многочисленных практических препятствий для борьбы с традиционными процедурами, ориентированными на ископаемое топливо [2, 3]. Получение жидкого биотоплива, включая другие продукты, такие как твердый уголь и газ, путем пиролиза различных остатков лигноцеллюлозы, было всесторонне исследовано ранее. Некоторые из этих видов биомассы — это древесина бука [4], жома [5], древесная биомасса [6, 7], солома [8], жмыхи [9] и твердые бытовые отходы (ТБО) [10, 11]. На рисунке 1 показаны различные типы существующих процессов преобразования биомассы с соответствующими выходными данными.
Рис. 1.
Процесс преобразования биомассы для получения продуктов с добавленной стоимостью.
Пиролиз определяется как термическое разложение производных лигноцеллюлозы в инертных условиях в среде с дефицитом кислорода. Это слово происходит от двух греческих слов: «пиро», что означает огонь, и «лизис», что означает распад на составные части. Технология пиролиза очень старая, и раньше она была впервые использована для приготовления древесного угля на Ближнем Востоке и в Южной Европе до 5500 лет назад [12]. Египтяне использовали эту технику для производства смолы для запечатывания лодок [13]. Впоследствии практика процессов пиролиза расширилась и широко применяется для производства древесного угля и кокса. Сжигание древесного угля может производить интенсивно высокую температуру плавления олова с медью с получением бронзы. Следовательно, пиролиз получил дальнейшее рассмотрение как эффективный метод преобразования биомассы в бионефть на протяжении современных эпох [14]. Конечная цель пиролиза — получение ценных энергетических продуктов для борьбы с невозобновляемым ископаемым топливом и постепенного вытеснения его.Тем не менее, распространение прогрессивных ноу-хау является следующей задачей для исследователей в достижении поставленных целей. Требуется превратить биомассу в биотопливо для непрерывного использования в транспортных средствах, поездах, кораблях и самолетах для замены дизельного топлива и бензина [15, 16]. Дальнейшее усовершенствование технологии пиролиза позволяет производить твердое топливо, такое как уголь или углеродсодержащие материалы, синтез-газ и т. Д. Обычно установка системы пиролиза содержит оборудование для предварительной обработки остатков лигноцеллюлозы, реактор пиролиза и последующую установку для последующей обработки.
В основном его можно классифицировать как агрегаты, производящие только тепло и биоуголь (с использованием медленного пиролиза), или агрегаты, производящие биоуголь и биомасла (с использованием быстрого пиролиза). На рисунке 2 представлена простая компоновка пиролизной установки с ее основными продуктами.
Рисунок 2.
Упрощенная блок-схема типовой установки пиролиза. (а) Производство биоугля и бионефти. (б) Биочар и производство тепла.
В последние годы было проведено большое количество исследований термохимического преобразования биомассы в биотопливо (бионефть, биочар и биогаз) с использованием технологии пиролиза.По сравнению с другими технологиями термохимической конверсии процесс пиролиза имеет множество преимуществ, основанных на оптимизации параметров процесса. Однако эта технология все еще нуждается в обновлении с точки зрения ее коммерческих приложений. В этой главе особое внимание уделялось обсуждению текущего состояния технологии пиролиза и ее перспектив для коммерческого применения для производства биотоплива, синтетического газа и биоугля. Представлены такие аспекты технологии пиролиза, как типы пиролиза, принципы пиролиза, состав и характеристики биомассы, конструкция реактора пиролиза, продукты пиролиза и их физико-химические свойства, а также экономика производства биотоплива.Мы указали на некоторые неотъемлемые свойства биомасла, которые вызывают осложнения при конечном использовании продуктов. Наконец, мы кратко рассмотрим некоторые процессы, включая процесс каталитического пиролиза, которые направлены на повышение ценности бионефти путем преобразования в более ценные жидкие топливные продукты.
2. Основные принципы пиролиза
Процесс термического разложения при пиролизе с использованием лигноцеллюлозной биомассы происходит в отсутствие кислорода в инертной атмосфере. В качестве инертной атмосферы обычно требуется поток газообразного аргона или азота.Основная химическая реакция очень сложна и состоит из нескольких этапов. Конечные продукты пиролиза биомассы состоят из биоугля, био-масла и газов. В процессе пиролиза в основном выделяются метан, водород, оксид углерода и диоксид углерода. Органические материалы, присутствующие в субстрате биомассы, начинают разлагаться примерно при 350–550 ° C, и это может продолжаться до 700–800 ° C без присутствия воздуха / кислорода [17, 18]. Биомасса в основном состоит из длинной полимерной цепи целлюлозы, лигнина, гемицеллюлозы, пектина и других.Более крупные молекулы органических материалов начинают разлагаться с образованием более мелких молекул, которые выделяются из технологического потока в виде газов, конденсируемых паров (смол и масел) и твердого угля во время процесса пиролиза. Доля каждого конечного продукта зависит от температуры, времени, скорости нагрева и давления, типов прекурсоров, конструкции и конфигурации реактора. На рисунке 3 показан процесс разложения основных остатков лигноцеллюлозы при различных температурах. Влажность биомассы также играет жизненно важную роль в процессах пиролиза.Влажность сырья во время процесса быстрого пиролиза должна составлять около 10% [18]. Из-за высокого содержания влаги основные продукты становятся жидкими, а при низком уровне воды высок риск того, что в процессе будет образовываться огромное количество пыли вместо масла.
Таким образом, ил, полученный из потока отходов и отходов мясопереработки, требует сушки, прежде чем подвергать их окончательному воздействию среды пиролиза. Менее 450 ° C при медленной скорости нагрева, основной выход — биоуголь. Однако при более высокой температуре, превышающей 800 ° C, при высокой скорости нагрева образуется большая часть золы и газообразных продуктов.Бионефть можно производить при промежуточной температуре с использованием относительно высоких скоростей нагрева. В начале процесса около температуры 250–300 ° C летучие вещества высвобождаются почти в 10 раз быстрее, чем на последующем этапе [20].
Рисунок 3.
Поведение при разложении компонентов биомассы при различных температурах [19].
Древесная биомасса изначально использовалась для производства древесного угля. Уголь на основе древесины при нагревании выделяет незначительное количество дыма.Ранее он широко использовался для плавки руды с целью извлечения железа. Однако у этого процесса были недостатки, заключающиеся в меньшем проценте выхода, меньшем количестве энергии и чрезмерном загрязнении воздуха. После этого была разработана современная технология извлечения максимально возможной энергии из биомассы с использованием сжигания (экзотермического), газификации (экзотермического) и пиролиза (эндотермического) [21]. Сжигание — это сжигание биомассы в присутствии кислорода для получения тепла. Компетентность этой практики не вызывает нареканий [22, 23]. Газификация также происходит в насыщенной кислородом атмосфере, что дает газообразное топливо.Тем не менее, пиролиз является ведущей фазой как для процессов газификации, так и для сжигания [24, 25]. Следовательно, пиролиз можно рассматривать как часть газификации и сжигания [26]. Выход продуктов разложения биомассы при пиролизе представлен на Рисунке 4 [27].
Рисунок 4.
Продукты разложения пиролиза биомассы [27].
В таблице 1 приведен список основных реакций пиролиза при различных температурах.
5″ border-bottom=».5″ border-left=»0″ border-right=»0″ align=»left»> Температура | Тип реакции | Конечные продукты |
---|---|---|
Менее 350 ° C | Потеря влаги, деполимеризация, образование свободных радикалов | Производство карбонильных и карбоксильных групп, CO и CO 2 Газовыделение, образование биоугля |
Между 350 ° C и 450 ° C | Замена для разрыва гликозидной цепи полисахарида | Производство смолы, содержащей левоглюкозан, ангидриды и олигосахариды |
Выше 450 ° C | Дегидратация, перегруппировка и деление сахарных единиц | Производство ацетальдегида, глиоксалина и акролеина |
Выше 500 ° C | Смесь всех вышеуказанных процессов | Смесь всех вышеуказанных продуктов |
5″ border-left=»0″ border-right=»0″> Конденсация | Конденсация ненасыщенных продуктов и прилепиться к углю | A высоко r остаток активного угля, содержащий захваченные свободные радикалы |
Таблица 1.
Реакции пиролиза при разной температуре [28].
3. Сырье для лигноцеллюлозной биомассы
3.1. Тип и состав сырья биомассы
Структура биомассы сложна и обычно состоит из трех основных природных биомакромолекул: целлюлозы, гемицеллюлозы и лигнина. Кроме того, он также содержит экстрактивные вещества и некоторые минералы. Пропорция и эти основные составляющие варьируются от биомассы к биомассе [11, 29, 30]. Во время пиролиза целлюлоза и гемицеллюлоза выделяют конденсируемые пары или жидкости и газ.Лигнин разлагается с образованием жидкого, газообразного и твердого полукокса. Экстракты также производят жидкость и газ из-за простого улетучивания или разложения. Зольная фракция внутри обугленной матрицы содержит минералы. Такое распределение компонентов по продуктам схематично показано на рисунке 5.
Рисунок 5.
Распределение продуктов во время пиролиза [29].
Пары, образующиеся при первоначальном разложении биомассы, подвергаются вторичным реакциям с образованием сажи, которая также изменяется из-за медленного и быстрого процесса пиролиза.Щелочные металлы действуют как катализатор, увеличивая выход полукокса. Присутствие минералов влияет на воспламеняющие свойства матрицы биоугля [11]. Было замечено, что био-масло в основном получают из целлюлозного субстрата при температуре около 500 ° C [31], тогда как биочар можно экстрагировать из лигнина. Таким образом, субстрат биомассы, который содержит большую долю производных лигнина, может давать больший выход биомасла. В таблице 2 приведен список выбранной биомассы, содержащей различное количество целлюлозы, гемицеллюлозы и лигнинового субстрата [11, 32–37].
Сырье | Лигнин (%) | Целлюлоза (%) | Гемицеллюлоза (%) |
---|---|---|---|
Древесина | 25–30 | 35–50 | 20–30 |
Пшеничная солома | 15–20 | 33–40 | 20–25 |
Переменная трава | 5–20 | 30–50 | 10–40 |
Жмых сахарного тростника | 23–32 | 19–24 | 32–48 |
Мискантус | 17 | 24 | 44 |
Кукурузная солома | 16–21 | 28 | 35 |
Скорлупа фундука | 42.![]() | 28,8 | 30,4 |
Оливковая шелуха | 48,4 | 24 | 23,6 |
Початок кукурузы | 15 | 50,5 | 31 |
Отходы чая | 40 | 30,20 | 19,9 |
Скорлупа грецкого ореха | 52,3 | 25,6 | 22,7 |
Скорлупа миндаля | 20,4 | 50,7 | 28,9 |
Скорлупа подсолнечника | 17 | 48.4 | 34,6 |
Скорлупа ореха | 30–40 | 25–30 | 25–30 |
Бумага | 0–15 | 85–99 | 0 |
Рисовая солома | 18 | 32,1 | 24 |
Хранимые отходы | 20 | 60 | 20 |
Листья | 0 | 15–20 | 80–85 |
Волосы семян хлопка | 0 | 80–95 | 5–20 |
Солома ячменя | 14–15 | 31–34 | 24–29 |
Солома овсяная | 16–19 | 31–37 | 24–29 |
Бамбук | 21–31 | 26–43 | 15–26 |
Ржаная солома | 16–19 | 33–35 | 27–30 |
Прибрежные Бермудские острова трава | 6.![]() | 25 | 35,7 |
Джутовое волокно | 21–26 | 45–53 | 18–21 |
Отходы бананов | 14 | 13,2 | 14,8 |
Таблица 2
Химический компонент выбранной биомассы.
3.2. Физиохимические свойства биомассы
Исходя из параметров процесса и конструкции реактора, наличие влаги может существенно повлиять на выход продуктов [11].Процесс производства древесного угля состоит из двух этапов: сушки и пиролиза. Во время начальной фазы сушки объединенная вода в порах, представленная свободной водой, удаляется при температуре около 110 ° C. Чем больше воды присутствует, тем больше энергии требуется для испарения. После этого между температурами 150 и 200 ° C количество воды, содержащейся в целлюлозной цепочке древесины, уменьшится. На ранней стадии карбонизации вода испаряется в виде белого дыма из угольной печи. Процесс быстрого пиролиза эффективен для сушки сырья, так что скорость повышения температуры не ограничивается испарением воды [38].Обычно в древесине содержится 15–20% влаги [11]. При производстве активированного угля влага также может существенно повлиять на свойства конечного образца угля [39]. Размер частиц матрицы биомассы будет иметь большее влияние на выход полукокса и жидкости. Большая часть полукокса образуется при больших размерах частиц. Более крупные частицы ограничивают скорость распада, что приводит к увеличению объема вторичной реакции обугливания [11]. Таким образом, частицы большего размера хороши для получения большего выхода углерода, тогда как частицы меньшего размера требуются для максимизации жидких фракций в процессе быстрого пиролиза.
Более высокая доля лигнина и связанного углерода также может способствовать лучшему выходу субстрата из биоугля, если пиролиз проводится при средней температуре 500 ° C, тогда как более высокий процент летучих материалов может дать более высокий выход биомасла и синтез-газа (Таблица 3) [28 ]. Следовательно, такие прекурсоры, как скорлупа лесного ореха, косточка оливы, скорлупа грецкого ореха, лучше подходят для производства биоугля хорошего качества из-за содержания в них лигнина (Таблица 2). Биомасса, такая как солома зерновых, травы, энергетические культуры, такие как древесная биомасса, погибающая из-за низкого содержания минералов и азота, подходит для производства бионефти и синтез-газа (Таблица 4) [40].
Сырье | 5″ border-bottom=».5″ border-left=»0″ border-right=»0″ align=»left»> Плотность (кг / м 3 ) | Содержание влаги (%) | Содержание золы (%) | Летучие вещества (%) | Связанный углерод (%) ) |
---|---|---|---|---|---|
Дерево | 1186 | 20 | 0,4–1 | 82 | 17 |
Каменный уголь | 11 | 8–11 | 35 | 45 | |
Гибридный полярный | 150 | 45 | 0.![]() | — | — |
Просо | 108 | 13–15 | 4,5–5,8 | — | — |
Мискантус | 70–100 | 11,5 | 1,5– 4,5 | 66,8 | 15,9 |
Багаж из сахарного тростника | 1198 | 3,2–5,5 | — | — | |
Солома ячменя | 210 | 30 | 6 | 46 | 18 |
Пшеничная солома | 1233 | 16 | 4 | 59 | 21 |
Датская сосна | 8 | 1.![]() | 71,6 | 19 | |
Рисовая солома | 200 | 6 4,3 | 79 | 10,7 | |
Дрова | — | 7,74 | 1,98 | 80,86 | 17,16 |
Grateloupia filicina | — | 4,93 | 22,37 | 55,93 | 17,01 |
Береза | 125 | 18,9 | 0,004 | — | 20 |
Сосна | 1700124 | 0.03 | — | 16 | |
5″ border-left=»0″ border-right=»0″> Полярный | 120 | 16,8 | 0,007 | — | — |
Таблица 3.
Физические свойства выбранного сырья биомассы [41–44].
Сырье | Углерод (%) | 5″ border-bottom=».5″ border-left=»0″ border-right=»0″ align=»left»> Водород (%) | Кислород (%) | Азот (%) | Зола (%) | |||||
---|---|---|---|---|---|---|---|---|---|---|
Древесина | 51.6 | 6,3 | 41,5 | 0,1 | 1 | |||||
Cypress | 55 | 6,5 | 38,1 | — | 0,4 | |||||
Оливковый багаж | 66,9 | 9,2 | 21,9 | — | 2 | |||||
Солома пшеницы | 48,5 | 5,5 | 3,9 | 0,3 | 4 | |||||
Солома ячменя | 45,7 | 6.![]() | 38,3 | 0,4 | 6 | |||||
Шотландцы | 56,4 | 6,3 | — | 0,1 | 0,09 | |||||
Береза | 44 | 6,9 | 49 | 0,1 | 0,004 | |||||
Сосна | 45,7 | 7 | 47 | 0,1 | 0,03 | |||||
Полярный | 48,1 | 5,30 | 46,10 | 0.14 | 0,007 | |||||
Ива | 47,78 | 5,90 | 46,10 | 0,31 | 1,30 | |||||
Просо | 44,77 | 5,79 | 49,13 | 0,31 | 4,3058 | ed54 банка трава45,36 | 5,81 | 48,49 | 0,34 | 5,10 |
Dactylis lomarata | 42,96 | 5,70 | 49.![]() | 1,90 | 7,50 | |||||
Festuca arundinacea | 42,22 | 5,64 | 50,65 | 1,50 | 7,30 | |||||
Lolium perenne | 43,12 | 5,80 | 6,80 | 49,8 |
Таблица 4.
Химические характеристики некоторых выбранных материалов биомассы [35, 41, 44].
В зависимости от состава, физико-химических свойств, а также механизма трансформации остатки лигноцеллюлозы могут давать различные продукты с добавленной стоимостью, как показано на Рисунке 6.
Рис. 6.
Преобразование биомассы в продукты с добавленной стоимостью.
3.3. Управление температурным профилем и значениями нагрева биомассы
Для оптимизации выхода продукта наиболее важным фактором является контроль температурного профиля, поскольку он может частично влиять на давление, скорость нагрева, пиковую температуру и время контакта между твердой и газовой фазами. Для сведения к минимуму степени вторичных реакций при быстром пиролизе требуется высокая скорость нагрева и охлаждения.Это снизит выход жидкости, но качество продукта снизится. Даже это даст более сложную смесь, имеющую более высокую вязкость [38]. С другой стороны, медленный процесс пиролиза использует медленные скорости нагрева, которые приводят к более высокому выходу полукокса, но это не согласуется [11]. Более высокая температура может обеспечить высвобождение более летучих фракций для увеличения содержания углерода в полукоксе. Однако более длительное время пребывания при более высокой температуре значительно снизит выход продукта. Влияние температуры на жидкую и газообразную фракции гораздо сложнее.Когда температура пиролиза достигает 400–550 ° C, выход жидкости выше. Выше этой температуры происходят вторичные реакции за счет разложения конденсируемого пара, что в конечном итоге дает меньшие жидкие фракции. Для быстрого пиролиза максимальная жидкость получается около 500 ° C [18]. Сообщалось также, что выход жидкости составлял 28–41% при температурах от 377 до 577 ° C, в зависимости от сырья в процессе медленного пиролиза [13]. Около 42–45% жидких фракций было получено при температуре 385–400 ° C с использованием различных кормов из соломы [45].
3.4. Влияние скорости потока газа
Скорость потока газа в процессе пиролиза влияет на степень вторичного обугливания. Более низкая скорость потока благоприятна для образования полукокса во время процесса медленного пиролиза, тогда как более высокие потоки газа обеспечиваются во время процесса быстрого пиролиза для эффективного удаления паров, как только они образуются. Более высокое давление усиливает активность паров внутри реактора и на поверхности частиц угля, что увеличивает вторичное образование угля.И наоборот, пиролиз в вакууме дает мало полукокса и дает больше жидких фракций. При пиролизе под давлением влага в паровой фазе может систематически увеличивать образование углерода. Потому что в этом случае вода действует как катализатор, уменьшая энергию активации реакций пиролиза [46]. Скорость потока газа существенно влияет на термодинамику процесса. При более высоком давлении реакция более экзотермична при более низких расходах газа. Более высокие выходы полукокса могут быть обеспечены, когда процесс пиролиза является экзотермическим, и такие условия будут способствовать общему энергетическому балансу процессов, в которых углерод или полукокс являются основным продуктом.Таким образом, можно сделать вывод, что любой фактор условий пиролиза, который увеличивает контакт между первичными парами и поверхностью горячего полукокса, включая высокое давление, меньшую скорость потока газа, больший размер частиц или медленный нагрев, как ожидается, будет способствовать образованию полукокса с более низким содержанием жидкости. Уступать.
4. Существующий процесс пиролиза
4.1. Быстрый пиролиз
4.1.1. Чугунный пиролиз
Пиролиз, особенно пиролиз угля, — это вековая деятельность, но пиролиз биомассы — это совершенно новое явление.Процесс направлен на производство биотоплива. В чердачном процессе твердые отходы (биомасса) могут смешиваться с горячим углем и горячим рециркулирующим газом в специально разработанной камере. Затем следует пиролиз при высокой температуре, обычно выше 800 ° C, и времени выдержки около 10 с. После пиролиза полукокс удаляется, а жидкая часть собирается. Образовавшаяся смола затем отделяется и дополнительно обрабатывается для получения технологического тепла, а также сырья для дальнейшего пиролиза.Как правило, ожидается, что процесс приведет к получению не менее 40% жидкости, но было обнаружено, что при температуре и времени карбонизации выделяется больше газа, что делает процесс неэкономичным [47]. Весь процесс можно кратко разделить на три основных этапа: формирование турбулентного газового потока путем смешивания газа-носителя, твердой биомассы и горячего полукокса с использованием специально разработанной зоны смешивания, пропускания газообразного пара в камеру пиролиза и прохождения пиролиза. при температуре около 800 ° C в течение около 10 с и, наконец, удаление потока пиролизованного газа из камеры пиролиза [47].
4.1.2. Технологический институт Джорджии. Процесс с увлеченным слоем
В этом процессе основное сырье (биомасса) измельчается и просеивается на частицы размером около 1 мм. Затем предшественник сушат до содержания влаги примерно 10% и подают в реактор, где он подвергается пиролизу с использованием предварительно нагретого инертного газа. При температуре пиролиза около 500 ° C ожидается максимальный выход около 50% жидкости и 30% газа. Время выдержки карбонизации обычно рассчитывается на основе высоты реактора и расхода газа, но обычно составляет несколько секунд [48].Одной из основных проблем этого метода является низкое количество тепла, выделяемого увлекающим газом, что обычно приводит к низкому выходу жидкости, поскольку биомасса требует большого количества тепла для высокого выхода жидкости. Другая проблема заключается в том, что свежие твердые отходы оказывают каталитическое воздействие на крекинг бионефти, приводя к образованию большего количества полукокса и газа [49].
4.2. Процессы пиролиза в псевдоожиженном слое
Процесс пиролиза в псевдоожиженном слое обладает превосходными массообменными характеристиками, поскольку он предлагает эффективные и высокоэффективные средства быстрого нагрева мелко измельченной биомассы для достижения температуры пиролиза до желаемого уровня.Это хорошо зарекомендовавший себя метод пиролиза, который можно использовать в крупномасштабном процессе пиролиза, поскольку он способен обрабатывать сотни тонн биомассы в день. Преимущества этого метода по сравнению с обычным методом пиролиза включают улучшенные характеристики системы, а также более низкую вязкость в сочетании с более высоким содержанием энергии в производимой биомасле.
4.2.1. Процесс мгновенного пиролиза Ватерлоо (WFPP)
Процесс мгновенного пиролиза Ватерлоо включает производство органических жидкостей из материалов биомассы с использованием постоянного атмосферного давления в отсутствие кислорода.Как правило, это тщательно контролируемый процесс, обеспечивающий высокий выход жидкости. Этот процесс был широко продемонстрирован с использованием твердых древесных отходов для производства жидких органических веществ, достигающих 70% от исходного материала [50]. Это процесс, в котором реактор пиролиза работает по очень уникальному принципу, при котором не допускается накопление полукокса в слое, в то время как обработка песка может не потребоваться. Одним из больших преимуществ процесса является то, что получаемый жидкий продукт обычно кислый и легко разливается с относительной стабильностью [51].
4.2.2. RTI-процесс
Чтобы удовлетворить определенные критерии, которые не были удовлетворены другими методами быстрого пиролиза, был разработан RTI-процесс. Это включает использование глубокого псевдоожиженного слоя с использованием очень низких температур с умеренными скоростями нагрева и относительно длительным временем выдержки пиролиза. Удовлетворительные результаты были получены при пиролизе большей части биомассы с использованием этой технологии, которая эффективно приводит к высокому выходу жидкости в диапазоне температур от 400 до 450 ° C с временем выдержки летучих около 0.8 с [52]. В качестве теплоносителя слоя обычно используется мелкий песок. Это обеспечивает очень низкий расход газа, что в сочетании с косвенным нагревом приводит к очень эффективному тепловому КПД. Это очень большое преимущество с экономической точки зрения, если учесть капитальные и эксплуатационные затраты [52].
4.2.3. Динамотивный процесс
Эта технология, внедренная в 1991 году, направлена на производство продуктов с добавленной стоимостью из бионефти, особенно для производства биолима. Рабочая теплота пиролизера обычно исходит от газа или полукокса, то есть побочных продуктов пиролиза, тогда как псевдоожижающий газ выделяется из пиролизного газа [53].Полученный жидкий продукт затем используется в производстве таких материалов, как биолим, гашеная известь, и для контроля SO x и NO x во время сжигания угля [53].
4.2.4. Ensyn process
Этот процесс включает использование древесины и других лигноцеллюлозных материалов для производства сбраживаемого сахара. Процесс включает в себя следующие важные этапы: обработка материала биомассы разбавленной кислотой (обычно для растворения гемицеллюлозы используется разбавленная серная кислота, в то время как содержание целлюлозы не изменяется), отделение твердого остатка, содержащего целлюлозу, пиролиз отделенного твердого остатка при контролируемая температура (400–600 ° C), атмосферное давление с коротким временем выдержки пара в реакторе с псевдоожиженным слоем, образование водной фазы путем контролируемого регулирования содержания сырого продукта и, наконец, разделение водной фазы [53].
5. Типы пиролиза
В целом процесс пиролиза можно разделить на медленный и быстрый в зависимости от скорости нагрева. В процессе медленного пиролиза время нагревания субстрата биомассы до температуры пиролиза больше, чем время удерживания субстрата при характерной температуре реакции пиролиза. Однако при быстром пиролизе начальное время нагревания предшественников меньше, чем конечное время удерживания при пиковой температуре пиролиза. В зависимости от среды пиролиз может быть еще двух типов, а именно водного пиролиза и гидропиролиза.Медленный и быстрый пиролиз обычно проводят в инертной атмосфере, тогда как водный пиролиз проводится в присутствии воды, а гидропиролиз — в присутствии водорода. Время пребывания пара в среде пиролиза больше для медленного процесса пиролиза. Этот процесс в основном используется для производства угля. Его можно дополнительно классифицировать как карбонизацию и обычную. Напротив, время пребывания пара составляет всего секунды или миллисекунды. Этот тип пиролиза, используемый в основном для производства бионефти и газа, бывает двух основных типов: (1) мгновенный и (2) сверхбыстрый.В таблице 5 приведены некоторые основные характеристики различных типов процесса пиролиза.
5.1. Быстрый пиролиз
В процессе быстрого пиролиза остатки биомассы нагреваются в отсутствие кислорода при высокой температуре с более высокой скоростью нагрева. Исходя из исходного веса биомассы, быстрый пиролиз может обеспечить 60–75% жидкого биотоплива с 15–25% остатков биоугля [54]. Он также может давать 10–20% газовой фазы в зависимости от используемой биомассы [54]. Процесс характеризуется малым временем удержания паров.Однако быстрое охлаждение паров и аэрозолей может обеспечить более высокий выход биомасла [54]. Он может обеспечить жидкое биотопливо для турбин, котлов, двигателей, источников питания для промышленного применения. Технология быстрого пиролиза становится неприемлемой для производства жидких топлив из-за определенных технических преимуществ [55–57]:
Она может обеспечить предварительную дезинтеграцию простых частей олигомера и лигнина из лигноцеллюлозной биомассы с последовательным обогащением.
Расширение масштабов этого процесса экономически целесообразно.
Он может утилизировать сырье биомасла второго поколения, такое как лесные остатки, городские и промышленные отходы.
Обеспечивает удобство хранения и транспортировки жидкого топлива.
Обеспечивает вторичное преобразование моторного топлива, добавок или специальных химикатов.
5.2. Мгновенный пиролиз
Мгновенный пиролиз биомассы может давать твердые, жидкие и газообразные продукты. Производство бионефти может достигать 75% с помощью мгновенного пиролиза [58].Эта процедура осуществляется путем быстрого удаления летучих веществ в инертной атмосфере с использованием более высокой скорости нагрева и высоких температур пиролиза около 450 и 1000 ° C. В этом процессе время пребывания газа (менее 1 с) слишком мало [59]. Тем не менее, этот процесс имеет плохую термическую стабильность. Из-за каталитического действия полукокса масло становится вязким, а иногда и содержит твердые остатки [60].
5.3. Медленный пиролиз
Медленный пиролиз позволяет получать древесный уголь хорошего качества при низкой температуре и низкой скорости нагрева.Время пребывания пара в этом процессе может составлять около 5–30 минут. Летучие органические фракции, присутствующие в паровой фазе, продолжают реагировать друг с другом с образованием полукокса и некоторых жидких фракций [61]. Качество продукции бионефти в этом процессе очень низкое. Более длительное время пребывания инициирует дальнейший крекинг, что снижает выход бионефти. Процесс страдает низкими значениями теплопередачи с более длительным временем удерживания, что приводит к увеличению затрат за счет более высоких затрат энергии [62, 63]. Стехиометрическое уравнение для производства древесного угля показано в [11].
C6h20O5 → 3.74C + 2.65h3O + 1.17CO2 + 1.08Ch5E1В таблице 6 ниже приведены теоретические равновесные выходы целлюлозы при различных температурах с использованием медленного пиролиза [11].
Типы пиролиза | Время удерживания | Скорость нагрева | Конечная температура (° C) | Продукты |
---|---|---|---|---|
Быстрый | <2 с | Очень высокий | 500 | Bio-oil |
Flash | <1 с | High | <650 | Bio-oil, химикаты и газ |
Ultra-quick | <0.5 с | Очень высокая | 1000 | Химическая промышленность и газ |
Вакуум | 2–30 с | Среда | 400 | Бионефть |
Гидропиролиз | <10 с | Высокая | <500 | Биомасло |
Карбонизация | дней | Очень низкая | 400 | Древесный уголь |
Обычный | 5–30 мин | Низкий | 600 | Обугленный, био ‐Нефть и газ |
Таблица 5.
Различные виды процессов пиролиза.
% продукции | Температура (° C) | ||||
---|---|---|---|---|---|
200 | 300 | 400 | 500 | 600 | |
C | 32 | 28 | 27 | 27 | 25,2 |
H 2 O | 36,5 | 32,5 | 27 | 27 | 22.5 |
CH 4 | 8,5 | 10 | 10 | 10 | 9 |
CO 2 | 23,9 | 28 | 35 | 35 | 36 |
CO | 0 | 0 | 1,2 | 1,2 | 4,5 |
Таблица 6.
Равновесная концентрация газообразных продуктов при различных температурах.
6.Каталитический пиролиз
Смесь углеводородов производилась ранее из метанола над цеолитами, такими как ZSM-5 [64]. В другом патенте предлагалось пропускать пары из пиролизера над слоем цеолита ZSM-5 для получения углеводородов с короткой цепью [65]. Сообщалось, что катализатор ZSM-5 может преобразовывать биомасла, произведенные в пиролизере, в алкилированный бензол [66]. Недостатком использования ZSM-5 в качестве катализатора было образование кокса [66]. Исследователи пришли к выводу, что низкое соотношение H / C в бионефти вызывает быструю дезактивацию катализатора, что приводит к образованию значительного количества кокса в качестве отходов [66].Однако эти недостатки могут быть преодолены путем использования технологии циркулирующего псевдоожиженного слоя, при которой псевдоожиженный слой может быть приготовлен с использованием различных типов катализатора вместо песка [53]. Уровень мелкомасштабной пилотной установки (от 0,1 до 0,35 кг / ч) также был разработан RTI international [53]. Этот завод может успешно проводить пиролиз местной биомассы сосны для производства бионефти. Этот завод также пытается проводить каталитический пиролиз древесной стружки, при котором из 1 тонны остатков биомассы можно получить 60 галлонов пиролитического масла в день [53].Недавно были предприняты другие попытки получить ароматические соединения, особенно бензол, ксилол и толуол, из субстрата биомассы [53]. Недавно компания KiOR Inc. в Техасе, США [53], заявила о прогрессе в случае расширения масштабов использования этого вида технологий [53].
Недавно была предпринята попытка разработать катализатор из возобновляемых источников. Зола, образующаяся из газифицированной биомассы, содержит 70–87% кремнезема в аморфной форме, который был использован исследователями для производства катализаторов ZSM-5 и ZSM-48 для повышения качества биомассы [67].Биочаг, полученный из ряски, продемонстрировал превосходную каталитическую активность в отношении риформинга CH 4 -CO 2 при температуре около 800 ° C [68]. Катализаторы можно смешивать с лигноцеллюлозным субстратом перед процессом пиролиза или отдельно с газообразными реагентами для получения желаемых продуктов. Выявлено, что разделение катализатора и биомассы более оперативно для превращения необходимых продуктов [69]. В этом исследовании в качестве катализатора использовался хромит (FeCr 2 O 4 ), и оно продемонстрировало благоприятные результаты с точки зрения ограничения производства воды.В таблице 7 представлена сводная информация о катализаторах на основе цеолита, которые до сих пор использовались для облагораживания лигноцеллюлозных остатков.
Катализатор | Темп. (° C) | Исходное сырье | Каталитическое действие | Ссылки. |
---|---|---|---|---|
HZSM ‐ 5 с различным соотношением Si / Al 2 O 3 | 500–764 | Крафт-лигнин | Уменьшение отношения SiO 2 / Al 2 O 3 от От 200/1 до 25/1 и увеличение соотношения катализатор: лигнин с 1: 1 до 20: 1 уменьшало содержание оксигенатов и увеличивало ароматические углеводороды.Выход ароматических углеводородов увеличивался с 500 до 650 ° C, а затем снижался при более высоких температурах. В оптимальных условиях реакции выход ароматических соединений составлял 2,0% (EHI 0,08) и 5,2% (EHI 0,35). | [70] |
HZSM ‐ 5, Na / ZSM5, HBeta и H ‐ USY | 650 | Щелочной лигнин | H ‐ USY имел самый большой размер пор и самое низкое соотношение Si / Al (7) и имеет лучший выход жидкости 75% и выход ароматических веществ 40%. | [71] |
ZSM ‐ 5, Al / MCM ‐ 41, Al ‐ MSU ‐ F, ZnO, ZrO 2 , CeO 2 , Cu 2 Cr 2 O 5 , Критерий-534, стабилизированный оксидом алюминия оксид церия MI-575, сланец, уголь и зола, полученные из полукокса и биомассы | 500 | Корневище маниока | ZSM-5, Al / MCM-41, тип Al-MSU-F, 534, стабилизированный оксидом алюминия церий-MI-575, Cu 2 Cr 2 O 5 и зола, полученная из биомассы, были селективными в отношении восстановления большинства кислородсодержащих производных лигнина.Катализаторы ZSM-5, Criterion-534 и Al-MSU-F усиливали образование ароматических углеводородов и фенолов. Не было обнаружено единого катализатора для восстановления всех карбонильных продуктов, но ZSM-5, Criterion-534 и MI-575 могли восстанавливать большинство карбонильных продуктов, содержащих гидроксильные группы. ZSM ‐ 5, Criterion ‐ 534, Al / MCM ‐ 41, Al ‐ MSU ‐ F, хромит меди, полукокс и зола с повышенным содержанием уксусной, муравьиной и молочной кислот. MI-575 не увеличивал кислотность. | [72] |
Доломит | 500–800 | Отработанная шелуха оливок | Доломит увеличивает крекинг и образование газа. | [73] |
HZSM ‐ 5, Al / MCM ‐ 41, Al ‐ MSU ‐ F и стабилизированный оксидом алюминия оксид церия MI ‐ 575, размер пор 5.5, 31, 15 и NA соответственно | 500 | Корневище маниоки | HZSM-5 был наиболее эффективным катализатором для производства ароматических углеводородов, фенолов и уксусной кислоты и восстановления кислородсодержащих соединений, производных лигнина, и карбонилов, содержащих гидроксильные группы боковых цепей. Только MI-575 показал снижение выхода уксусной кислоты. MI-575 также показал наибольший прирост метанола, на втором месте оказался HZSM-5. | [74] |
Таблица 7.
Краткое описание катализаторов на основе цеолита, используемых для обогащения биомассы.
7. Каталитический гидропиролиз
Каталитический гидропиролиз — это разновидность каталитического пиролиза, при котором пиролиз осуществляется с использованием реактора с псевдоожиженным слоем в потоке водорода. В этом процессе псевдоожиженный слой заменяется катализатором из переходного металла. Сообщалось, что замена инертного песка катализатором на основе никеля при атмосферном давлении может преобразовать бионефть в углеводороды с низким молекулярным весом за короткое время контакта [75]. Недавно Институт газовой технологии , Иллинойс, США, сообщил о новом процессе, в котором весь процесс осуществляется под давлением 7–34 бар [76]. Из-за высокого давления выделяются газы C1 – C3, которые после риформинга выделяют большое количество водорода. Однако система также очень сложна, поскольку представляет собой комбинацию гидропиролиза и риформинга. Необходимо решить некоторые технические проблемы, такие как подача твердых частиц биомассы в пиролизер под давлением под водородом. В целом создание этого процесса также требует больших затрат.
8. Типы реакторов
Нельзя недооценивать важность соответствующего реактора в любом процессе, включающем пиролиз. Реакторы были спроектированы таким образом, чтобы удовлетворять конкретным условиям с учетом таких параметров, как температура нагрева, время пребывания парообразного продукта и требуемое давление, для получения высокого выхода биомасла. Учитывая вышеизложенное, исследователи разработали много типов реакторов для конкретных задач. К этим реакторам относятся:
8.1. Реактор с неподвижным слоем
Это очень простая технология, которая дает приоритет производству бионефти, которые относительно однородны по размеру с низким содержанием мелких частиц [42]. Он состоит из двух основных компонентов: отсека охлаждения газа и системы очистки путем фильтрации через циклон, мокрые скрубберы и сухие фильтры. Во время реакции твердый образец проходит через вертикальный вал, где он встречает движущийся вверх противоточный газовый поток. Этот реактор может быть выполнена с использованием либо стали, или огнеупорных кирпичей и бетона, состоящего из блока подачи (топлива), блок для удаления золы и блок утечки газа [77].Реактор, который имеет приоритетное значение для применений, связанных с малым производством тепла и электроэнергии, обладает высокой способностью сохранять углерод и может работать в течение длительного времени в твердом состоянии, с низкой скоростью газа и, конечно, с низким уносом золы. Его ограничение связано с проблемой, обычно возникающей при удалении смол [78].
8.2. Реактор с псевдоожиженным слоем
Этот реактор состоит из смеси двух фаз, твердой и жидкой, и обычно осуществляется путем пропускания жидкости под давлением через твердый материал.Он очень популярен для быстрого пиролиза, так как имеет следующие преимущества [79]:
Обеспечивает быструю передачу тепла.
Обладает хорошим контролем реакции пиролиза и времени выдержки пара.
Он имеет достаточно большую площадь поверхности для контакта между двумя фазами в смеси.
Теплопередача в системе примерная, а
Относительная скорость между фазами очень высока.
Существуют различные типы реакторов с псевдоожиженным слоем, в том числе с барботажным псевдоожиженным слоем, с циркулирующим псевдоожиженным слоем, абляционный реактор, вихревой реактор, реактор с вращающимся диском, реактор вакуумного пиролиза, реактор с вращающимся конусом, реактор PyRos, шнековый реактор, плазменный реактор, микроволновая печь. реактор и солнечный реактор, каждый из которых разработан с разными операционными системами и для конкретных приложений.
8.2.1. Реактор с барботажным псевдоожиженным слоем
Конструкция и работа этого реактора очень просты и показаны на Рисунке 7 [80].Высокая плотность твердого вещества в слое обеспечивает лучший контроль температуры, плавный контакт между газом и твердым телом, хорошую теплопередачу и отличную аккумулирующую способность. Биомасса нагревается в среде, лишенной кислорода, и разлагается на газ, пар, аэрозоли и уголь, и эти компоненты, наконец, собираются из реактора. В то время как древесный уголь собирается с помощью циклонного сепаратора и хранится, пар быстро охлаждается, конденсируется в высококачественное биомасло и хранится с выходом около 70% от веса биомассы (сухой вес) [80].
Рис. 7.
Реактор с барботажным псевдоожиженным слоем [80].
8.2.2. Реакторы с циркулирующим псевдоожиженным слоем
Характеристики этого реактора аналогичны характеристикам описанного выше реактора с псевдоожиженным слоем, за исключением того факта, что время пребывания паров и полукокса меньше. Это увеличивает скорость газа и содержание угля в биомасле. Однако он имеет большое преимущество в пропускной способности. Доступны одинарные и двойные типы этого реактора [81].Принципиальная схема этого реактора показана на рисунке 8 [80].
Рис. 8.
Реактор с рециркуляционным псевдоожиженным слоем [80].
8.3. Абляционный реактор
В этом реакторе нагрев осуществляется через расплавленный слой на поверхности горячего реактора и в отсутствие псевдоожижающего газа. Плавление биомассы осуществляется путем механического прижатия биомассы к стенке нагретого реактора, и когда расплавленный образец перемещается, пары пиролиза испаряются в виде масла. Хотя этот реактор позволяет получать частицы биомассы большого размера (до 20 мм), материалы не требуют чрезмерного измельчения [82].Однако конфигурация реактора несколько сложна из-за механической природы процесса. Реактор не получает выгоды от того же масштаба экономии, что и другие реакторы, из-за того, что масштабирование линейно зависит от теплопередачи, поскольку оно контролируется площадью поверхности. Обычно используются два типа этого реактора: абляционный вихрь и абляционный вращающийся диск [82].
8.4. Вакуумный реактор пиролиза
Это реактор медленного пиролиза с очень низкой скоростью теплопередачи.Это приводит к более низкому выходу бионефти, обычно в диапазоне 35–50 мас.% [83]. Конструкция очень сложна, и требования к капиталовложениям и техническому обслуживанию всегда высоки, что делает технологию неэкономичной. Биомасса подается в вакуумную камеру с высокой температурой с помощью конвейерной металлической ленты с периодическим перемешиванием биомассы механическим перемешиванием [83]. Теплоноситель обычно состоит из горелки, а биомасса плавится путем индукционного нагрева с использованием расплавленных солей.Он имеет возможность перерабатывать биомассу с более крупными частицами, но требует специальных устройств для подачи твердых частиц, специальных разгрузочных устройств, чтобы всегда иметь эффективную герметизацию [83]. Базовая схема этого типа реактора показана на рисунке 9 [83].
Рисунок 9.
Вакуумный реактор [83].
8.5. Реактор с вращающимся конусом
В отличие от реактора с псевдоожиженным слоем, реактор с вращающимся конусом требует, чтобы смешивание биомассы и горячего песка производилось механически и не требовало использования инертного газа.Функциональные возможности показаны на Рисунке 10 [74]. Подача и горячий песок подаются снизу конуса, в то время как они транспортируются к кромке конуса во время прядения с использованием центробежной силы, и когда они достигают вершины, образующийся пар конденсируется конденсатором [74]. Обугленный и песок сжигаются, при этом песок снова нагревается и снова вводится для повторного смешивания со свежим сырьем на дне конуса. Хотя конструкция этого реактора может быть сложной, его высокий выход бионефти делает его желательным.
Рис. 10.
Реактор с вращающимся конусом [74].
8.6. Реактор PyRos
Целью этого реактора является производство биомасла, не содержащего никаких частиц. В нем используется циклонный реактор, интегрированный с фильтром горячего газа. Как сырье биомассы, так и инертное тепло подаются в циклон в виде частиц, в то время как рециркулируемые пары заставляют транспортировать твердые частицы во время процесса. Частицы движутся вниз в нижнюю часть циклона под действием центробежной силы, в течение которого одновременно происходит сушка, нагрев и удаление летучих веществ.Температура нагрева обычно составляет 450–550 ° C при времени выдержки 0,5–1 с. Реактор очень экономичен с точки зрения инвестиций и выхода бионефти [84].
8.7. Шнековый реактор
В этом реакторе используется шнек для перемещения исходной пробы через цилиндрическую трубу, которая нагревается и лишена кислорода. В ходе этого процесса сырье подвергается пиролизу, дегазации и газификации при температуре от 400 до 800 ° C, что приводит к образованию полукокса и конденсации газов в бионефть [30].
8.8. Плазменный реактор
Этот реактор состоит из кварцевой трубки цилиндрической формы с двумя медными электродами. Подача сырья осуществляется посередине с помощью шнека с регулируемым винтом в верхней части трубы [85]. Газовые потоки в трубке питаются тепловой энергией, вырабатываемой электродами, подключенными к источнику электроэнергии. Инертный газ используется для удаления кислорода из отсека, а также для производства плазмы. Помимо высокого потребления энергии, он демонстрирует способность препятствовать образованию смол, что можно было наблюдать при медленном пиролизе [86].
8.9. СВЧ реактор
Это одна из последних разработок в области пиролиза. Здесь передача энергии происходит в результате взаимодействия между молекулами и атомами с помощью микроволн. Весь процесс сушки и пиролиза происходит в камере микроволновой печи, подключенной к источнику электроэнергии. Газ-носитель инертен и также используется для создания бескислородной камеры. Реактор доказал свою высокую эффективность в регенерации химических веществ из биомассы [87]. Среди его преимуществ — эффективность теплопередачи, способность эффективно контролировать процесс нагрева, а также способность предотвращать образование нежелательных побочных продуктов.Его можно эффективно использовать в промышленных масштабах [87].
8.10. Солнечный реактор
В данной технологии предусмотрено хранение солнечной энергии в виде химической энергии. Он состоит из кварцевой трубки с непрозрачной внешней стенкой, обычно подвергающейся воздействию высокой концентрации солнечного излучения, способной генерировать высокие температуры (> 700 ° C) в реакторе [88, 89]. Загрязнение в этом реакторе снижено, поскольку сырье никогда не вмешивается в процесс нагрева, в отличие от медленного пиролиза, когда технологическое тепло генерируется частью сырья.Время запуска и выключения также очень быстрое.
В таблице 8 показаны преимущества и недостатки различных типов реакторов.
Тип реактора | Преимущества | Недостатки |
---|---|---|
Неподвижный слой | Простота конструкции Надежные результаты Не зависит от размера биомассы | Сохранение высокого углерода Длительное время пребывания в твердом состоянии Низкий вынос золы более Трудно удалить уголь |
Пузырьковый псевдоожиженный слой | Простая конструкция Простые рабочие процедуры | Хороший контроль температуры Подходит для крупномасштабного применения Требуются частицы небольшого размера |
Циркуляционный псевдоожиженный слой | Скважина- Понятная технология Лучше Температурный контроль Можно обрабатывать частицы большего размера | Крупномасштабное производство затруднено Сложная гидродинамика Обугленный слишком мелкий |
Вращающийся конус | Центробежная сила перемещает горячий песок и субстрат биомассы Н o требуется газ-носитель | Сложный производственный процесс Требуются частицы меньшего размера Сложно крупномасштабное применение |
Вакуум | Масло чистое Может обрабатывать более крупные частицы размером 3–5 см Газ-носитель не требуется Более низкая температура требуется Конденсация жидкого продукта легче | Медленный процесс Время пребывания твердого вещества слишком велико Требуется крупномасштабное оборудование Низкая скорость тепло- и массообмена Создает больше воды |
Абляционный | Инертный газ не требуется Более крупные частицы могут | Система более интенсивная Требуется умеренная температура Реактор дорогостоящий Более низкая скорость реакции |
Шнек компактный | Газ-носитель не требуется | Более низкая температура процесса Движущиеся части в горячей зоне Теплопередача в более крупном масштабе не подходит |
PyRos | Компактность и низкая стоимость Эффективная теплопередача Короткое время пребывания газа | Сложная конструкция Твердые частицы в масле Щелочь, растворенная в масле Требуется высокая температура |
Плазма | Высокая плотность энергии Высокая теплопередача Эффективная Управление процессом Высокое потребление электроэнергии | Высокие эксплуатационные расходы Требуются мелкие частицы |
Микроволновая печь | Эффективная теплопередача Экспоненциальное управление Компактная структура Более высокая скорость нагрева Возможность обработки биомассы большого размера Равномерное распределение температуры | Высокая температура Высокое потребление электроэнергии Высокие эксплуатационные расходы |
Солнечная энергия | Использование возобновляемых источников энергии Более высокая скорость нагрева | Высокая температура Высокие затраты В зависимости от погоды |
Таблица 8.
Преимущества и недостатки различных типов реакторов [52, 90, 91].
9. Продукты пиролиза
9.1. Biochar
Biochar — это твердые аморфные углеродные материалы, полученные в результате термического разложения лигнина и полимера гемицеллюлозы в процессе пиролиза. Физико-химические свойства матрицы биокара сильно зависят от типа и конструкции реактора, состава биомассы, размера частиц и степени сушки, химической активации, скорости нагрева, времени реакции, давления, скорости потока инертного газа, и т. Д. [29, 92–96]. Если используется более высокая скорость нагрева до 105–500 ° C / с для меньшего времени удерживания и более мелкого размера частиц, более мелкий биоуголь производится в процессе быстрого пиролиза, тогда как сырье с более крупными частицами во время медленного пиролиза приводит к более грубому биоугля. Обычно древесная биомасса дает более крупнозернистый биочуголь, тогда как пожнивные остатки и навоз дают более хрупкий биочуголь [97]. Более ранние исследования показали, что выход биоугля в реакторе пиролиза с псевдоожиженным слоем варьируется в зависимости от температуры [98].Результаты показали, что при низкой температуре около 450–500 ° C выход biochar был высоким, а скорость удаления летучих — низкой. При температуре около 550–650 ° C выход биоугля снижался. При этой температуре достигается максимальный выход около 8–10% [98]. Однако при более высокой температуре, около 650 ° C, выход биоугля был очень низким. Biochar преимущественно содержит большую часть фиксированного углерода вместе с влагой, летучими веществами, водородом и различными другими составляющими в двух структурах: стопке кристаллических листов графена и случайно упорядоченных аморфных ароматических структурах [99].Ароматическая часть biochar содержит H, O, N, P и S. Эти неорганические соединения оказывают заметное влияние на физические и химические свойства biochar [100]. Процентное содержание этих компонентов зависит от типа биомассы и процесса пиролиза [101–103]. Biochar можно использовать в качестве твердого топлива в котлах. После предварительной каталитической обработки его можно использовать для производства активированного угля, углеродных нанотрубок, газовых фракций и т. Д.
9.2. Синтез-газ
В зависимости от состава биомассы и параметров процесса пиролиза состав синтез-газа варьируется.Обычно газообразные продукты, полученные после пиролиза, в основном состоят из H 2 и CO. Он также содержит незначительную долю CO 2 , N 2 , H 2 O, смесь алканов, алкенов и алкинов, например, CH . 4 , C 2 H 4 , C 2 H 6 , смола, зола и т. Д. [104]. Более высокая температура пиролиза приводит к эндотермической реакции. С увеличением пиролиза сначала происходит испарение влаги из биомассы.После этого происходит термическое разложение и улетучивание. На этом этапе производится деготь и высвобождаются летучие вещества. Для получения смеси синтез-газа имеет место серия вторичных реакций, таких как декарбоксилирование, декарбонилирование, дегидрогенизация, деоксигенация и крекинг. Следовательно, более высокая температура инициирует разложение смолы, что приводит к производству синтез-газа с пониженным выходом масла и полукокса. При заданной температуре сухая биомасса дает наибольшее количество газа на ранней стадии пиролиза, тогда как влажная биомасса дает максимальное количество газа позже в процессе.Это очевидно и ожидается, поскольку увеличение влажности приводит к увеличению времени высыхания. При крекинге углеводорода водород образуется при более высокой температуре. Из-за наличия кислорода в биомассе образуются CO и CO 2 . Присутствие кислородсодержащего полимера, которым является целлюлоза, определяет выделение образующихся карбонизированных оксидов [105]. Более легкие углеводороды, такие как CH 4 , C 2 H 4 , C 2 H 6 и т. Д., Образуются в результате риформинга и крекинга более тяжелых углеводородов и гудрона в паровой фазе [106].Плазменный реактор, использующий радиочастоты, может производить до 76,64% синтез-газа [85]. Преимущества использования синтез-газа заключаются в том, что он производит значительно меньшее количество несгоревших углеводородов (HC) и монооксида углерода (CO) с более высокими выбросами оксидов азота (NO x ). Сообщается, что CO и H 2 в синтез-газе имеют сравнительно повышенную скорость пламени и температуру, которые вызывают более высокие температуры в двигателях, чтобы увеличить скорость производства CO 2 и NO x [97–109].Медленные процессы пиролиза дают около 10–35% биогаза. При более высокой температуре мгновенный пиролиз дает больше синтез-газа [110]. Прокаленный доломит использовался при 750–900 ° C в качестве катализатора в реакторе с неподвижным слоем для получения синтез-газа [110].
9.3. Bio-oil
Нефть, экстрагированная после пиролиза, представляет собой смесь примерно 300–400 соединений [111]. Масло, полученное после пиролиза, имеет тенденцию становиться вязким из-за старения, поскольку происходят многочисленные физические и химические изменения с последующей потерей летучих веществ.Однако процесс старения можно замедлить, храня их в прохладных местах [35]. Ранее было обнаружено, что энергетические культуры могут давать масло с высоким содержанием золы / металлов и воду [112]. Присутствие воды снизит теплотворную способность, а также затруднит разделение фаз [112]. Таким образом, при коммерческом применении необходимо тщательно контролировать наличие золы и лигнина внутри субстрата из биомассы. Ранее термический КПД пиролизных масел сравнивали с дизельным топливом, но они демонстрировали неоправданную задержку воспламенения [113].С другой стороны, количество, качество и постоянство пиролизного масла также можно улучшить с помощью переменных метода, таких как скорость нагрева, температура и время удерживания [114]. Различные типы реакторов (абляционные и фиксированные), размер частиц и обугливание могут влиять на количество и характеристики пиролизного масла. До сих пор не проводилось всеобъемлющих исследований, которые могли бы уменьшить эти вещи. Следовательно, необходимы дополнительные исследования, чтобы получить полное представление о процессах термохимического превращения для получения пиролизного масла высшего качества.Биомасло, которое следует использовать в коммерческих целях, должно сохранять свои химические и физические свойства, такие как постоянство и вязкость. Если масло содержит низкомолекулярные соединения, это возможно. Масло содержит высокомолекулярные соединения, если исходная биомасса содержит большую долю лигнина.
10. Технология пиролиза: текущее состояние
Использование пищевых культур, таких как соя, кукуруза и сахарный тростник, для производства этанола и биодизеля может не продолжаться долго, поскольку эти культуры в основном выращиваются для потребления.Поэтому возникает необходимость в более устойчивых способах получения этих материалов из других источников, таких как материалы биомассы, в дополнение к другим, уже исследуемым. Тем не менее, ни один из них еще не является экономически целесообразным, но есть большие надежды на использование лигноцеллюлозной биомассы для этой цели посредством процесса пиролиза, хотя он все еще сталкивается с некоторыми проблемами прорезывания зубов. Компании Ensyn и Dyna Motive предприняли некоторые ощутимые усилия по коммерциализации использования материалов биомассы и других сельскохозяйственных отходов в производстве биотоплива посредством процесса быстрого пиролиза.Эти материалы легко доступны по низкой цене или бесплатно, что делает их использование очень экономичным. В то время как Dyna Motive концентрируется на том, как сделать энергетические системы из производимого топлива более экологически чистыми, Ensyn, с другой стороны, стремится использовать химические вещества, которые могут производиться из системы, в качестве побочных продуктов для других целей, таких как копчение пищи. Эти усилия с тех пор привели к производству биотоплива из материалов биомассы. Другими известными пиролизными компаниями, которые участвовали в этой деятельности, являются Pyrovac и Renewable Oil International, которые используют технику вакуумного пиролиза в дополнение к другим более мелким пиролизным установкам, доступным по всему миру.Из имеющихся данных ясно, что реакторы с псевдоожиженным слоем в основном используются для производства бионефти с использованием биомассы, тогда как за ним следуют другие технологии.
11. Выводы
Изучение литературы показало, что преобразование биомассы в продукты с добавленной стоимостью все еще требует решения некоторых испытаний, таких как определение связи между исходными прекурсорами или исходным сырьем и общей работой пиролизной установки, модернизация согласованность реакций пиролиза с точки зрения полного энергетического и материального баланса для обеспечения устойчивости для прибыльных применений.В этой главе подробно описан принцип технологии пиролиза, включая выбор эффективных параметров пиролиза, типов реакторов, и т. Д. , в зависимости от предпочтительного выхода (биомасло, биоуголь или синтез-газ) из процесса. Однако полное понимание типового процесса позволит получить максимальную отдачу. В этой главе освещены полученные выводы и рекомендации для дополнительных исследований:
Основной задачей процесса пиролиза является улучшение процесса за счет повышения качества и количества продукта, а также снижения затрат и снижения вредного воздействия на окружающую среду.
Правильный выбор биомассы является решающим фактором для получения высоких урожаев биомассы. Можно выбрать биомассу с высоким содержанием целлюлозы, поскольку биомасла в основном получают из нее, тогда как биомасса на основе лигнина может использоваться для производства биоугля. Кроме того, биомасса с низким содержанием влаги подходит для снижения затрат на сушку и повышения качества добытого масла.
Кинетика пиролиза биомассы может протекать по нескольким параллельным путям.Однако применение низкой температуры приведет к снижению энергии активации, что приведет к получению в основном полукокса и газа. Напротив, повышенная температура приведет к более высокой энергии активации с образованием в основном конденсируемых паров, масел и жидких аэрозолей. Чтобы получить максимальное количество жидкого топлива, необходимо быстро нагреть биомассу до подходящей повышенной температуры. Тем не менее, для быстрого нагрева биомассы требуются частицы прекурсоров меньшего размера, что может вызвать постоянный нагрев частиц.В этом случае
ПРИМЕСЬ | В результате | ВЫБРАТЬСЯ ОТ 4 | 16 9164 169164 |||
Сероводород (H 2 S) | Вода пахнет тухлыми яйцами: имеет неприятный вкус для большинства металлов и вызывает коррозию. | Аэрация, фильтрация и хлорирование. | Встречается в основном в подземных водах и загрязненных ручьях. | ||
Двуокись углерода (CO 2 ) | Коррозионно, образует угольную кислоту в конденсате. | Деаэрация, нейтрализация щелочами. | Пленка, нейтрализация аминов, используемых для предотвращения коррозии конденсатопровода. | ||
Кислород (O 2 ) | Коррозия и точечная коррозия труб котла. | Деаэрация и химическая обработка (сульфит натрия или гидразин) | Точечная коррозия труб котла и лопаток турбины, выход из строя паропроводов, фитингов и т. Д. | ||
Взвешенные твердые частицы | |||||
Осадки и мутность | Унос шлама и окалины. | Уточнение и фильтрация. | Допуск ок. 5ppm макс. для большинства применений 10 ppm для питьевой воды. | ||
Органические вещества | Унос, пенообразование, отложения могут засорить трубопроводы и вызвать коррозию. | Разъяснение; фильтрация и химическая обработка | Встречается в основном в поверхностных водах, вызванных гниением растительности и сточными водами хозяйств.Органические вещества распадаются с образованием органических кислот. Приводит к низкому уровню pH питательной воды котла, который затем разрушает трубы котла. Включает диатомовые водоросли, плесень, бактериальные слизи, железо / марганцевые бактерии. Взвешенные частицы собираются на поверхности воды в котле и затрудняют выделение пузырьков пара, поднимающихся на эту поверхность. Пенообразование также можно отнести к воде, содержащей карбонаты в растворе, в котором на поверхности образуется легкий хлопьевидный осадок. вода. Обычно это связано с избытком карбоната натрия, используемого для лечения других проблем, когда в котел попадает животное или растительное масло. | ||
Растворенные коллоидные твердые вещества | |||||
Масло и консистентная смазка | Пенообразование, отложения в бойлере 04 | 166204||||
Твердость , кальций (Ca) и магний (Mg) | Накипные отложения в котле, препятствуют теплопередаче и термической эффективностиВ тяжелых случаях это может привести к перегоранию трубы котла и выходу из строя. | Умягчение и внутренняя обработка в котле. | Формы — это бикарбонаты, сульфаты, хлориды и нитраты в указанном порядке. Некоторые соли кальция обратимо растворимы. Магний реагирует с карбонатами с образованием соединений с низкой растворимостью. | ||
Натрий, щелочность, NaOH, NaHCO 3 , Na 2 CO 3 | Пенообразование, карбонаты образуют угольную кислоту в паре, вызывая возврат конденсата в линии возврата конденсата и коррозию конденсатоотводчика , может вызвать хрупкость. | Деаэрация подпиточной воды и возврат конденсата. Ионный обмен; деионизация, кислотная обработка подпиточной воды. | Натриевые соли встречаются в большинстве водоемов. Они очень растворимы и не могут быть удалены химическим осаждением. | ||
Сульфаты (SO 4 ) | Твердая окалина, если присутствует кальций | Деионизация | 100-3000 Пределы допуска Ca 3 | ||
Хлориды, (Cl) | Грунтовка, т.е.е. неравномерная подача пара из котла (отрыжка), перенос воды в пар, снижающий паропроизводительность, может отлагаться в виде солей на пароперегревателях и лопатках турбин. Вспенивание при большом количестве. | Деионизация | Заливка, или прохождение пара из котла в «отрыжках», вызывается концентрацией карбоната натрия, сульфата натрия или хлорида натрия в растворе. Сульфат натрия содержится во многих водах США, а также в водах, где кальций или магний осаждаются кальцинированной содой. | ||
Железо (Fe) и | Отложения в котле в больших количествах могут препятствовать передаче тепла. | Аэрация, фильтрация, ионный обмен. | Наиболее распространенной формой является бикарбонат железа. | ||
Кремнезем (Si) | H окалина в котлах и системах охлаждения: отложения на лопатках турбин. | Деионизация; известково-содовая обработка, известково-цеолитовая обработка. | Кремнезем соединяется со многими элементами с образованием силикатов. Силикаты образуют в трубах котла очень вязкие отложения. Очень трудно удалить, часто только фтороевой кислотой. Наиболее важным соображением является перенос летучих веществ в компоненты турбины. |
Обработка и кондиционирование питательной воды котла должны удовлетворять трем основным задачам:
Внешний Обработка — это уменьшение или удаление примесей из воды вне котла.Как правило, внешняя очистка используется, когда количество одной или нескольких примесей в питательной воде слишком велико, чтобы их могла выдержать рассматриваемая котельная система. Существует множество видов внешней обработки (умягчение, испарение, деаэрация, мембранные подрядчики и т. Д.), Которые можно использовать для адаптации питательной воды для конкретной системы. Внутренняя очистка — это кондиционирование примесей в котельной системе. Реакции происходят либо в линиях подачи, либо в самом котле.Внутреннее лечение может использоваться отдельно или в сочетании с наружным лечением. Его цель — правильно реагировать на жесткость питательной воды, кондиционировать ил, улавливать кислород и предотвращать пенообразование котловой воды. внешний Внешний вид | | Некоторые натуральные и синтетические материалы обладают способностью удалять минеральные ионы из воды в обмен на другие. Например, при пропускании воды через простой катионообменный умягчитель все ионы кальция и магния удаляются и заменяются ионами натрия. Поскольку простой катионообмен не снижает общее содержание твердых веществ в воде, его иногда используют в сочетании с умягчением осадочного типа. Одна из наиболее распространенных и эффективных комбинированных обработок — это процесс горячей извести-цеолита.Это включает в себя предварительную обработку воды известью для снижения жесткости, щелочности и, в некоторых случаях, кремнезема, и последующую обработку катионообменным смягчителем. Эта система очистки выполняет несколько функций: смягчение, уменьшение щелочности и кремнезема, некоторое снижение содержания кислорода, а также удаление взвешенных веществ и мутности. Внутренняя очистка Внутренняя очистка может составлять уникальную обработку, когда котлы работают при низком или умеренном давлении, когда в качестве питательной воды используется большое количество конденсированного пара или когда доступна сырая вода хорошего качества. Целью внутренней обработки является обеспечение реакции 1) с питательной водой любой жесткости и предотвращения ее осаждения на металле котла в виде накипи; 2) кондиционировать любые взвешенные вещества, такие как твердый осадок или оксид железа, в котле и делать их не прилипающими к металлу котла; № 3) обеспечивает защиту от пены, позволяющую обеспечить разумную концентрацию растворенных и взвешенных веществ в котловой воде без уноса пены; 4) удаляет кислород из воды и обеспечивает достаточную щелочность для предотвращения коррозии котла. Кроме того, в качестве дополнительных мер внутренняя обработка должна предотвращать коррозию и образование накипи в системе подачи воды, а также защищать от коррозии пароконденсатные системы. Во время процесса кондиционирования, который является важным дополнением к программе очистки воды, в воду добавляются определенные дозы кондиционирующих веществ. Обычно используемые продукты включают:
| Общие внутренние методы подачи химикатов включают использование резервуаров для химических растворов и дозирующих насосов или специальных питателей для шарового брикетирования.Как правило, смягчающие химические вещества (фосфаты, кальцинированная сода, каустик и т. Д.) Добавляются непосредственно в питательную воду в месте возле входа в корпус котла. Их также можно подавать через отдельную линию, отводящую в емкость питательной воды котла. Химикаты должны сливаться в секции подпиточной воды котла, чтобы реакции происходили в воде до того, как она попадет в паропроизводящую зону. Смягчающие химикаты можно добавлять непрерывно или периодически, в зависимости от жесткости питательной воды и других факторов.Химические вещества, добавляемые для реакции с растворенным кислородом (сульфат, гидразин и т. Д.), И химические вещества, используемые для предотвращения накипи и коррозии в системе питательной воды (полифосфаты, органические вещества и т. Д.), Должны подаваться в систему питательной воды как можно более непрерывно. . Химические вещества, используемые для предотвращения коррозии конденсатной системы, могут подаваться непосредственно в пар или в систему подачи воды, в зависимости от конкретного используемого химического вещества. Предпочтительна непрерывная подача, но в некоторых случаях достаточно прерывистой подачи. Посетите нашу веб-страницу, посвященную производству высокочистой воды с помощью электродеионизации (EDI). Щелкните здесь, чтобы получить более подробную информацию о деаэрации (деаэрационные нагреватели или мембранные подрядчики). Ссылки |
Необходимость очистки питательной воды котла
Характеристики питательной воды котла | Характеристики котловой воды
Котловая вода — это термин, используемый специально для обозначения воды, которая нагревается внутри самого бойлера. Котловая вода обеспечивается питательной водой котла из котла в виде нагретой воды или пара.
Питательная вода котла : Вода, которая напрямую поступает в котел. Питательная вода котла состоит из подпиточной воды и возвратного конденсата.
Подпиточная вода: Подпиточная вода — это исходная неочищенная вода, полученная из скважины или любого другого источника и очищенная до необходимой степени.
Возвратный конденсат : Возвратный конденсат — это вода, которая проходит через котел, превращается в пар и после определенного использования конденсируется обратно в жидкую воду и возвращается в резервуар питательной воды.
Котельная — важная часть промышленного концерна.В любой обрабатывающей промышленности парогенераторы играют жизненно важную роль. Чистота котловой воды и пара является одним из важнейших критериев обеспечения доступности компонентов и надежности в энергосистемах.
Перенос : Влага, твердые частицы, диоксид кремния и другие связанные твердые вещества, выходящие из котла с паром, называются переносом
Сырая вода:
Из химического анализа сырой воды мы получаем всю информацию о качестве сырой воды.Это может варьироваться от источника к источнику.
Ниже приведены различные типы примесей, которые обычно присутствуют в любых типах воды. Типы и процентное содержание примесей варьируются в зависимости от источника воды, например реки, озера, скважины и т. Д.
Ионный и растворенный | Неионогенные и нерастворенные | газообразный | |
Катионный | Анионный | ||
Са ++ мг ++ Na + К + Nh5 Fe ++ Fe +++ Mn +++ | HCO 3 _ CO 3 _ HO _ _ СО 4 _ Класс _ НЕТ 3 _ PO 4 _ SiO 2 _ | Мутность, ил, грязь Грязь Цвет Органические вещества Коллоидный диоксид кремния Микроорганизмы Бактерии масло | CO 2 H 2 NH 3 CH 4 О 2 N 2 Класс 2 |
Примеси сырой воды и их влияние на котел:
1.Общая щелочность:
В сырой воде общая щелочность в первую очередь относится к бикарбонату. Также может присутствовать небольшое количество карбоната. Ионы гидроксида отсутствуют в сырой воде. Общая щелочность сырой воды важна, поскольку она представляет собой потенциальный источник накипи.
2. Бикарбонат — карбонат
Основным источником щелочности сырой воды являются бикарбонат-ионы. При нагревании ионы бикарбоната разлагаются на карбонаты и диоксид углерода.Если в результате образуется растворимая соль, дальнейшее нагревание разложит карбонат до каустика (ОН) и диоксида углерода
2 HCO 3 → CO 3 + H 2 O + CO 2
CO 3 + h3O → 2 OH + CO 2
Щелочь в котловой воде может быть нежелательной в зависимости от рабочего давления. Двуокись углерода является основным источником коррозии конденсатопровода.
3. Кальций:
В большинстве случаев сырой воды кальций является основным источником жесткости.В системах котельной и охлаждающей воды соли кальция являются основной причиной образования накипи.
4. Хлорид:
Накипь не является проблемой для хлоридных солей, но они очень агрессивны в окислительной среде. Хлориды играют важную роль в щелевой коррозии и точечной коррозии. Во всех случаях проектирования или эксплуатации следует принимать меры для предотвращения концентрации хлоридов.
5. Утюг:
Железо обычно находится в растворимой форме двухвалентного железа.При контакте с воздухом или окислителями железо превращается в форму трехвалентного железа и образует нерастворимые гидроксиды или оксиды. Если содержание железа превышает 0,3 промилле или больше, его следует уменьшить или контролировать.
6. Магний:
Магний обычно образует гидроксиды или силикаты в котловой воде , , которые являются желательными типами ила. Если щелочность котловой воды низкая, часто образуется нежелательный фосфат магния, который становится липким и образует накипь. В системе охлаждающей воды магний осаждается только при pH выше 10.0.
7. pH:
pH сырой воды будет в диапазоне от 5,5 до 8,0. Низкий pH может привести к коррозии, а высокий pH может привести к образованию накипи.
8. Кремнезем:
Обычно встречается в грунтовых водах, и содержание кремнезема составляет 70-80 частей на миллион. не является необычным. В высокой концентрации диоксид кремния может вызвать образование накипи в системах водяного охлаждения, а также в котлах.
Контроль диоксида кремнияважен, особенно в котлах высокого давления, поскольку диоксид кремния может испаряться и откладываться в областях низкого давления турбины , а также в пароперегревателях.
9. Сульфат:
Большинство неочищенных вод содержат сульфаты. Присутствие сульфатов усугубляет коррозию, и сульфаты обнаруживаются в отложениях обычно в виде сульфата кальция.
10. Общее количество растворенных твердых веществ (TDS) :
Это общий показатель коррозионной активности сырой воды. Тест на проводимость, хотя и не точный, является удобным методом проверки TDS . Любое изменение состава сырой воды отражается в изменении проводимости.
11. Твердость:
Жесткость воды выражается в частях карбоната кальция на миллион частей воды. Он также выражается в зернах CaCo3 на галлон воды. 14,28 части CaCo3 соответствует одной степени жесткости.
Вода бывает двух типов жесткости.
Временная твердость :
Temporary Hardness обуславливает карбонатную жесткость , которая является мягкой и пористой.
Постоянная твердость :
Постоянная жесткость в воде вызывает негарбонатную жесткость , которая является твердой по своей природе.
Почему необходима очистка питательной воды котла:
Вода — основная среда для производства пара . Правильное кондиционирование может повысить эффективность котла, а также продлить срок его службы. Очистка котловой воды также обеспечивает безопасную и надежную работу.Без надлежащей обработки сам котел может быть разрушен.
Проблема с котловой водой обычно делится на два класса: , связанные с отложениями и связанные с коррозией . Есть много случаев, когда отложения вызывают коррозию, а коррозия вызывает отложения.
Требуется очистка питательной воды котла
а) Для предотвращения коррозии котла и паровой системы.
б) Для предотвращения образования накипи и на поверхности нагрева.
Поддерживайте высокий уровень чистоты пара.
Также важно поддержание чистоты пара т. Некоторые примеси могут переноситься или растворяться в паре и могут осаждаться в пароперегревателе или на лопатках турбины. Газообразные примеси нежелательны, если пар конденсируется после использования или используется в системе отопления. Благодаря этим условиям произойдет вспенивание и грунтование.
Характеристики питательной воды котла:
Питательная вода котла Свойства в зависимости от рабочего давления котла.В соответствии с рабочим давлением котла технические характеристики питательной воды следующие как
Рабочее давление барабана котла кг / см 2 (G) | ||||||
Параметры | ЕД | до 20 | 21-40 | от 41 до 60 | от 61 до 100 | 101 выше |
Твердость | частей на миллион | 1 | 1 | 0.5 | ND | ND |
pH | 8,5–9,5 | 8,5–9,5 | 8,5–9,5 | 8,5–9,5 | 8,5–9,5 | |
P. Щелочность | частей на миллион | Нет | Нет | Нет | Нет | Нет |
M. Щелочность | частей на миллион | Нет | Нет | Нет | Нет | Нет |
Кислород | частей на миллион | 0.05 | 0,07 | 0,07 | 0,07 | 0,07 |
Кремнезем | частей на миллион | 1 | 0,02 | 0,02 | 0,02 | 0,02 |
TDS | частей на миллион | 25 | 10 | 3 | 3 | <3 |
Гидразин | частей на миллион | 0,02 | 0,02 | 0.02 | 0,02 | 0,02 |
Медь | частей на миллион | 0,02 | 0,02 | 0,02 | 0,02 | 0,02 |
Утюг | частей на миллион | 0,02 | 0,02 | 0,02 | 0,02 | 0,02 |
Хлориды | частей на миллион | Нет | Нет | Нет | Нет | Нет |
Сульфиты | частей на миллион | Нет | Нет | Нет | Нет | Нет |
Нитраты | частей на миллион | Нет | Нет | Нет | Нет | Нет |
Удельная электропроводность при 25 ° C, измеренная после катионита в форме Н + и после удаления CO2 максимум | мкг / см | 10 | 5 | 2 | 0.5 | 0,3 |
Проблемы в котле из-за низкого качества котловой воды:
a) Вспенивание: Вспенивание является причиной большинства проблем уноса в котлах и обычно является результатом слишком высокой концентрации твердых веществ в котловой воде.
b) Коррозия: Наиболее распространенным примером является воздействие на сталь кислорода. Это происходит в системах водоснабжения, предпусковых котельных, котлах, обратных линиях конденсата.Кислородная атака ускоряется высокой температурой и низким pH. 4h3O + 3Fe → Fe3O4 + 4h3.
c) Из-за образования накипи в котле теплопередача замедляется, пластины и трубки перегреваются, вздуваются и ломаются.
d) Из-за электрохимического воздействия присутствие кислорода в котловой воде вызывает точечную коррозию и коррозию.
e) CO2 в котловой воде образует карбонат железа и преобразует его в гидроксид железа, а затем в оксид железа, называемый ржавчиной.
е) Из-за гидролиза образуются нестабильные соли Ca и Mg, минеральные кислоты и трубы перегреваются.
г) Из-за неочищенной воды точечная коррозия и утонение стенок или пластин трубок возникают со стороны воды.
h) Растворенный кислород вызывает коррозию поверхностей из-за избыточной концентрации водородных или гидроксильных ионов со стороны воды, соответствующей снижению или увеличению pH соответственно.
i) pH: Коррозионное действие воды минимально, при этом pH явно находится в щелочной области.т.е. 8 и выше при pH 9,0 образуется защитная пленка гидроксида двухвалентного железа. Иногда конденсаты обязаны своей щелочностью растворенному Nh4, который высвобождает Nh4 с падением pH.
Процесс очистки котловой воды:
Очистка питательной воды котла может быть разделена на две широкие классификации — внешняя и внутренняя очистка.
Внешнее лечение:
a) Сырая вода перед подачей в котел проходит очистку. Это известно как Внешнее лечение .Цель состоит в том, чтобы улучшить качество воды перед ее использованием в качестве питательной воды котла .
б) Технически методы обработки направлены на снижение щелочности, жесткости, кремнезема, железа, марганца, мутности, бактерий, органических штейнов р и других. В очистке питательной воды котла помогает предотвратить коррозию, накипь, перегрев.
c) Один из критических параметров — Hardness , который является одним из основных факторов масштабирования.Твердость удаляется с помощью процесса ионного обмена или другой внешней обработки, такой как сода извести или обратный осмос (RO) .
Внутренняя обработка или химическая обработка:
a) Помимо внешней обработки, было разработано несколько программ обработки воды (внутренняя обработка ) для решения проблем образования накипи и коррозии котлов. Фактор, который необходимо учитывать при выборе программы
c) В случае внутренней очистки химикатов вводятся в котловую воду , а осажденные соли удаляются в продувке .
Для
Морская техника: испытание котловой воды
Цели испытания котловой воды 1) Контролировать состояние котловой воды.
2) Для управления дозированием химикатов в котле.
3) Поддерживать котел в исправном состоянии, при любых возможных загрязнениях морской воды.
Первым этапом испытания котловой воды является отбор пробы питательной воды из соответствующего котла. Образец воды, отобранный из бойлера через соединение, будет относительно чистым и не отражает истинного сквозного соединения, будет относительно чистым и не отражает истинное состояние котловой воды, который считается хорошим образцом.
Это связано с тем, что горячие частицы образца смываются паром, в результате чего растворенное твердое вещество в образце выше, а большое количество летучих веществ, таких как гидразин, снижает показатель концентрации в программе испытаний.
Отбор проб:
Требуется репрезентативная проба воды. Всегда отбирайте пробу воды из одного и того же места. Дайте воде вытечь из пробоотборного крана перед тем, как отбирать пробу для тестирования, чтобы убедиться, что линия свободна от отложений.
Идеальное место в котле для отбора пробы — от клапана салинометра, после прохождения через охладитель пробы, убедившись, что линия отбора пробы промыта, а бутыль для пробы тщательно промыта.Дайте воде вытечь из бутылки с образцом, чтобы предотвратить попадание воздуха внутрь бутылки и сохранить герметичность бутылки для тестирования. Следуйте процедурам тестирования, рекомендованным Unitor Chemical Services Анализатором качества воды Spectrapak 311. Возьмите тестовый образец для:
1. pH
2. Щелочность
3. Хлориды
4. Фосфаты
5. Общая жесткость
Некоторые иногда рекомендуют проведение испытаний на электропроводность. производители.
Тест на щелочность
Тест на щелочность проводится в два этапа:
1) Тест на щелочность фенолфталеина
2) М-щелочность
P- Тест на щелочность (CaCO3)
Цель .Это дает щелочность образца из-за гидроксидов и карбонатов.
2. Предупреждает о высокой концентрации гидроокиси натрия и последующем повреждении котла из-за образования щелочи.
Процедуры:
1. Возьмите пробу воды 200 мл в остановленную бутыль.
2. Добавьте одну таблетку P-Alkalinity и встряхните или измельчите до растворения.
3. Если присутствует P-щелочность, образец станет синим.
4. Повторите добавление таблеток по одной (давая время таблетке раствориться), пока синий цвет не станет постоянно желтым.
5. Подсчитайте количество использованных таблеток и выполните следующий расчет:
P-Щелочность, ppm CaCO3 = (Количество таблеток x 20) — 10
например, 12 таблеток = (12 x 20) — 10 = 230 CaCO3
6. Запишите полученный результат в предоставленном журнале с датой проведения теста.
7. Сохраните пробоотборник M-щелочности.
M-тест на щелочность
Цель:
1. Показывает щелочность за счет бикарбонатов, включая бикарбонаты, образовавшиеся во время теста P-щелочности.
2. Результат предостерегает нас от возможного образования углекислоты внутри котла, а также в линиях пароконденсата из-за высокой концентрации бикарбонатов.
Процедуры:
1. К образцу P-Щелочности добавьте одну таблетку M. Щелочность и встряхните или измельчите до разложения.
2. Повторяйте добавление таблеток по одной (давая время таблетке раствориться), пока образец не станет постоянно красным / розовым.
3. Подсчитайте количество использованных таблеток и выполните следующий расчет: M- Щелочность, ppm CaCO3 = (Количество P.& M. Таблетки x 20) — 10 например Если 12 п. 5 М. Таблетки щелочности.
4. Запишите полученный результат в предоставленном журнале с датой проведения теста.
PH Test
Растворы, частью которых является вода, содержат ионы водорода и ионы гидроксила, когда они присутствуют в равных количествах, раствор считается нейтральным. При избытке ионов водорода он кислый, а при избытке гидроксильных ионов — щелочной. Слабощелочная вода снижает коррозию.Уровень кислотности или щелочности обычно выражается через значение pH. Это в основном мера концентрации ионов водорода в растворе; для удобства задействованные очень маленькие значения выражаются в логарифмах их обратных величин.
PH = логарифм обратной величины иона водорода в растворе
Следует отметить, что по мере использования обратной величины значение pH увеличивается по мере уменьшения фактической концентрации ионов водорода.
Тест значения pH (взаимный или ионный водород)
7.5 — 14,0 для котловой воды
6,5 — 10,0 для конденсатной воды
Назначение:
1. Для предупреждения о кислотности или щелочности пробы котловой воды.
2. Результат поможет установить дозировку котельного состава для борьбы с коррозией.
Процедуры:
1. Возьмите пробу воды для анализа объемом 50 мл в прилагаемый пластиковый контейнер для проб.
2. С помощью белого 0,6 грамм. Лопаткой, входящей в комплект поставки, добавьте одну мерку реагента pH в пробу воды, дайте ей раствориться — при необходимости перемешайте.
3. Выберите правильный диапазон pH тест-полоски и погрузите ее в образец воды на одну минуту.
4. Извлеките полоску из образца и сравните полученный цвет с цветовой шкалой на контейнере для индикаторных полосок pH.
5. Запишите полученное значение pH в прилагаемом журнале относительно даты проведения теста.
Хлориды, промилле CI Test
Назначение:
1. Дает предупреждение о любом загрязнении морской водой системы питания котла.
2. Помогите установить эффективный контроль продувки котла.
Процедуры:
Диапазон проверяемых хлоридов определяет размер используемой пробы воды. Чем выше уровень хлорида, тем меньше размер используемой пробы воды — это экономит таблетки. Например. для низкого уровня хлоридов используйте 100 мл. образец воды. Для более высоких уровней хлоридов пробы воды объемом 50 мл.
1. Возьмите пробу воды из прилагаемой пробки.
2. Добавьте одну таблетку хлорида и встряхните, чтобы она растворилась. Образец должен стать желтым, если присутствуют хлориды.
3. Повторяйте добавление таблеток по одной (давая время таблетке раствориться), пока желтый цвет не изменится на постоянный красный / коричневый.
4. Подсчитайте количество использованных таблеток и выполните следующий расчет:
Для 100 мл пробы воды: ч / млн хлоридов = (количество таблеток x 10) — 10, например, 4 таблетки = (4 x 10) — 10 = 30 ч / млн хлорида
Для пробы воды объемом 50 мл: хлорид ppm = (количество таблеток x 20) — 20, например, 4 таблетки = (4 x 20) — 20 = 60 ppm хлорида
Для малых значений ppm хлорида используйте образец большего размера.
Для более высоких концентраций хлорида ppm используйте образец меньшего размера.
5. Запишите полученное значение pH в прилагаемом журнале относительно даты проведения теста.
Тест на содержание фосфатов (PO4)
Назначение:
1. Помогает поддерживать запас фосфатов в котле для предотвращения любого возможного загрязнения котловой воды коррозионными и солеобразующими солями. Однако слишком много фосфата в котле может также способствовать вспениванию и грунтованию.
Процедуры:
1.Возьмите компаратор с предоставленными ячейками на 10 мл.
2. Вставьте фосфатный диск в компаратор.
3. Отфильтруйте пробу воды в обе ячейки до отметки 10 мл.
4. Поместите одну ячейку в левый отсек.
5. В другую ячейку добавьте одну таблетку фосфата, измельчите и перемешайте до полного растворения.
6. Через 10 минут поместите ячейку в правый отсек компаратора.
7. Держите компаратор на свет.
8. Вращайте диск, пока не получите совпадение цветов.
9. Запишите полученный результат в предоставленном журнале с датой проведения теста.
Китай производитель котлов, паровой котел, поставщик водогрейных котлов
Тип бизнеса:
Производитель / Завод
Год основания:
2010-06-18
Сертификация системы менеджмента:
ISO 9001, ISO 9000, ISO 14001, ISO 14000, HACCP
OEM / ODM Сервис
Зарубежный агент / филиал
Котел, паровой котел, производитель / поставщик водогрейных котлов в Китае, предлагающий электрические паровые котлы WDR 1, 2, 4 тонн, дизельные термомасляные котлы, работающие на природном газе, паровые котлы на природном газе и т.