Работа с эпоксидной смолой | Журнал Ярмарки Мастеров
Здравствуйте, друзья. Перед созданием серии «Солнечный океан» мне удалось поработать с различными видами эпоксидной смолы. Возможно, полученный мною опыт окажется вам полезен.
Выбор материала:
Существуют различные типы смол, условно разделяемые на две группы: технические и декоративные. Приступая к задаче, выбирайте подходящий тип смолы. Нет необходимости заливать столешницу технической ЭД-20 или применять ювелирные марки для лодок и моделирования. Правильный выбор материала на подготовительной стадии избавит от множества проблем при заключительной обработке изделия.
Эпоксидная смола ЭД-20 — материал дешевый и доступный. Название смолы указывает на состав (эпоксидно-диановая), число 20 сообщает содержание в молекуле смолы эпоксидных групп. Чем меньше число, тем выше устойчивость смолы к температурному воздействию, т.е. термостойкость ЭД-8 > термостойкости ЭД-16.
ЭД-20 — наиболее популярная смола российского производства, продающаяся чаще всего в комплектах с отвердителем ПЭПА (300 граммов смолы и 30 граммов отвердителя).
Основное неудобство при работе с ЭД-20 — высокая вязкость, препятствующая выходу воздушных пузырьков из готовой смеси. При комнатной температуре смесь напоминает мёд, однако при разогреве вязкость материала значительно снижается, приближаясь к вязкости подсолнечного масла, что позволяет воздушным пузырькам легко подняться на поверхность.
Повысить температуру смеси можно несколькими способами:
1. Водяная баня. Поместите емкость с готовой смесью в резервуар с горячей водой.
2. Нагревание смеси в духовом шкафу.
3. Прогрев нанесенного слоя строительным феном или газовой горелкой.
4. Применение аэрозольного корректора, разжижающего верхний слой залитой смеси (рекомендуется при заливке больших объемов смолы для избежания перегрева и преждевременной полимеризации / выбраковки залитого слоя).
Повышение температуры у залитой смеси влияет на процесс полимеризации, значительно сокращая время жизни смешанного состава. Если смолу перегреть, то материал может не только затвердеть до начала отливки, но и вспениться, помутнеть, изменить цвет. Для экономии времени и денег, перед началом работы с незнакомым материалом проведите несколько тестовых заливок.
ЭД-20 — техническая смола, пригодная для склейки деталей, грунтовки поверхностей, ремонта. Однако данный тип смесей не предназначен для работ с высоким (художественным, декоративным) качеством покрытия. При работе с ЭД-20 неизбежен ряд недостатков: отсутствие абсолютной прозрачности и чистоты цвета у готового изделия, необходимость очищения смеси от воздуха, шлифовка готовой поверхности.
Перед заливкой:
1. Подложите под форму пищевую пленку или клеенку (бумага или картон пропитается смолой и испачкает рабочую поверхность).
3. Обезжирьте (подойдет обычный уайт-спирит или ацетон) и загрунтуйте поверхность, предназначенную для заливки.

4. При подготовке смеси тщательно перемешивайте компоненты. Лучше всего использовать две тары: половину времени смешивайте компоненты в одной емкости, затем переливайте и смешивайте в другой (при смешивании в одной емкости возле стенок и дна всегда останется исходный состав).
Гомогенность смолы — обязательное условие для хорошего результата, отсутствия разводов и волн на поверхности изделия.
При установке опалубки обязательно герметизируйте все линии соединения внешнего периметра:
1. Для герметизации опалубки у небольших изделий можно использовать пластилин.
2. Можно использовать воск (прокапывать каждый стык или растопить воск в металлической посуде и кистью промазать швы).
3. Можно воспользоваться монтажным пистолетом с термоклеем.
4. Или силиконовым герметиком — наиболее надежный способ для заливок значительного объема.
Установив опалубку, не забудьте про разделитель (слой, препятствующий адгезии смолы и опалубки). Лучший вариант — полиэтилен (для работ малого масштаба опалубку можно оклеить скотчем) или воск. Используйте любой вариант по вашему выбору, подбирая разделитель для конкретной марки смолы или воспользовавшись наиболее распространенным и дешевым вариантом — техническим вазелином.
Обязательно проверяйте герметизацию опалубки (например, просветив фонарем). Самого незначительного отверстия окажется достаточно, чтобы смола покинула форму и оказалась везде.
При использовании легких наполнителей (например, лепестков), залейте первый слой смолы тонким слоем, чтобы зафиксировать отдельные элементы перед добавлением основного объема, иначе незакрепленные детали поднимутся на поверхность смеси.
Про полимеризацию:
Процесс полимеризации разогревает смесь и смола расширяется. При завершения реакции с отвердителем смола «встает», постепенно остывая, из-за чего происходит процесс сжатия. Коэффициент сжатия зависит от множества факторов: используемой смолы, отвердителя, пластификаторов, характеристик окружающей среды и температурного режима в рабочем помещении.

ЭД-20 имеет значительный коэффициент сжатия, при полимеризации смолы можно наблюдать (в зависимости от площади основания и толщины залитого слоя): деформацию изделия, разрыв мелких деталей на линии соединительного шва, значительное выгибание/расслоение основы. Для снижения брака модифицируйте смесь пластификатором, подберите оптимальный тип отвердителя, хорошо просушите и загрунтуйте основу будущего изделия.
В процессе эксперимента возникла задача: залить деревянную поверхность смолой ЭД-20 так, чтобы полностью избежать искривления основы, допустив, что коэффициент сжатия является величиной пренебрежительно малой при соблюдении технологии отливки. Тогда причиной деформации может служить избыточная влажность материала. Отвердев, смола сформирует непроницаемую для воды пленку, из-за чего дерево начнет раздаваться на открытой, «мягкой» стороне. Спустя неделю, обработанная доска полностью сохранила начальную форму.
На акрил нанесли смесь ЭД-20 и отвердителя ПЭПА (в пропорции 10:1, с толщиной слоя 5 мм). Спустя двое суток искривление основы достигло 6 мм на 40 см длинны.
Про шлифовку:
Шлифовка — необходимый этап при доводке изделия. Некоторые смолы не требуют финишной обработки, но даже при идеальной отливке требуется выравнивание соединительной кромки, возникающей при контакте смолы с опалубкой.
Начинайте шлифовку наждачной бумагой с зернистостью от 600, постепенно понижая размер фракции: 600 — 1200 — 2500. При использовании наждачной бумаги смачивайте поверхность смолы. Смола эффективно «замыливает» наждак, вода отводит снятый материал и сглаживает обрабатываемую поверхность.
После наждака используйте жесткую поролоновую насадку с абразивной мазью, финишная полировка выполняется мягкой поролоновой насадкой с полиролем.
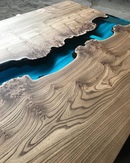
Не рекомендуется использовать войлочные насадки — волокнистый материал оставляет рельефные выемки на поверхности смолы.
При работе обязательно соблюдайте правила безопасности: избегайте контакта кожи со смолой, используйте перчатки и респиратор, работайте в помещении с хорошей вентиляцией.
При шлифовке изделия обязательно защищайте дыхательные пути: смола инертна и не выводится из организма.
Про отвердители:
Отвердители бывают двух типов. Холодные (полимеризация происходит при комнатной температуре) и горячие (полимеризация происходит при температуре от +50 градусов). Ниже рассмотрены только холодные отвердители.
ПЭПА (полиэтиленполиамин) — технический отвердитель, разработанный в СССР во второй половине прошлого века.
Отвердитель обладает целым спектром недостатков, однако и сегодня пользуется популярностью, прежде всего, из-за крайней доступности и дешевизны.
Основные недостатки ПЭПА:
1. Окрашивание смолы. ПЭПА — жидкость насыщенного медного цвета.
2. Низкое качество исходного продукта. Около 70% отвердителя составляют примеси, не вступающие в реакцию и остающиеся в изделии.
3. Токсичность.
4. Неравномерная реакция при взаимодействии со смолой. При работе с большими объемами возможно закипание смеси.
5. Непригоден для работ в условиях повышенной влажности / низкой температуры (температурный минимум: +15 градусов).
Достоинства:
1. Крайне дешев.
2. Снисходителен к точной дозировке.
4. Высокая отверждающая способность.
ТЭТА (тетраэтиленпентамин) — отвердитель, отличающийся от ПЭПА лучшей дистилляцией (массовая доля активного вещества не менее 96%) и высокими требованиями к условиям работы.
Недостатки ТЭТА:
1. Минимальная температура окружающей среды для реакции в смеси: +25 градусов. При комнатной температуре смесь останется липкой (устраняется термообработкой).
2. Необходимо строгое соблюдение технологического процесса, точное соблюдение пропорций, очень тщательное перемешивание.
3. Токсичность.
4. Непригоден для работ в условиях повышенной влажности.
Достоинства:
1. Прозрачность. Отвердитель практически полностью бесцветен.
2. В случае успешного использования изделие получит высокую прочность и однородность состава (в сравнении с ПЭПА).
Этал-45 — продолжение линии аминных отвердителей, но, в отличии от ПЭПА и ТЭТА, Этал-45 практически не имеет недостатков.
Достоинства:
1. При добавлении в смесь также выступает в роли пластификатора (пропорция в смеси 2:1 / смола:отвердитель).
2. Нетоксичен.
3. Пригоден для работ в условиях высокой влажности.
4. Допустимая температура окружающей среды: от -7 до +45 градусов.
Недостаток один: густой, темно-коричневый цвет.
Для изготовления «Аурелии» ни один из упомянутых отвердителей не подходил. Первые два — в силу своего технического профиля, последний — из-за красящих свойств. После экспериментов с ЭД-20 проверена смола Этал Optic.
Характеристики смолы:
1. Низкая вязкость (воздух покинет смесь быстро и легко).
2. Прозрачность.
3. Использование одноименного отвердителя (10:4 / смола:отвердитель) хорошо пластифицирует смолу.
Для изготовления «Аурелии» данная смола подходила отлично, однако для получения эффекта волн требовался другой материал (см. «Изготовление морских волн» .
К сожалению, эксперименты с Этал Optic не сообщили такого спектра впечатлений, как работа с ЭД-20. Единственное полезное замечание: при окрашивании смолы обратите внимание на плотность полученной смеси и на вязкость компонентов, и не используйте краски на водной основе. Эпоксидка и вода не сочетаются, при контакте смола теряет прозрачность, мутнеет, приобретает белесый оттенок.
Про органику:
Заливая органику (цветы, листья, бутоны), обязательно просушите / стабилизируйте материал. Попадание воды в эпоксидную смолу может полностью испортить работу. Для стабилизации используйте воск, аэрозольный лак или глицерин. При использовании глицерина смешайте глицерин и воду в равной пропорции, затем погрузите цветок в жидкость и оставьте в прохладном месте на несколько недель (в зависимости от размера растения). В процессе стабилизации вода испарится, глицерин наполнит ткани, цветы сохранят упругость, форму и цвет.
Про силикон:
После завершения работы над скульптурной частью, с гипсового слепка снята силиконовая матрица. При работе с силиконом правило одно: соблюдайте пропорции и тщательно перемешивайте смесь. При точном следовании технологии испортить форму нельзя.
Перед началом работы:
1. Выберите силикон правильной твердости. Для обозначения твердости изделий из силикона используется шкала Шора «А». Диапазон шкалы от 0 до 100, чем выше число — тем тверже материал. Твердость материала в 30 единиц соответствует твердому ластику.
2. Подготовьте рабочее место. Как и с эпоксидной смолой, силикон крайне текуч и требует тщательной герметизации опалубки.
3. Обезжирьте / просушите мастер-форму.
4. Заливайте силикон на поверхность с минимальной адгезией, при необходимости — используйте разделительные смеси или материалы.
5. Чем тоньше слой залитого силикона, тем больше времени потребуется для завершения реакции. Объемная заливка и слой в миллиметр могут затвердеть с разницей в сутки. Время окончательного реагирования смеси — до 48 часов.
6 Используйте материал эффективно. При заливке сложных форм гораздо выгоднее наполнить опалубку до определенной высоты, затем окружить выступающие элементы новым периметром и долить полезный объем формы.
Изготовление морских волн, окрашивание смолы, работа в технике Resin Art.
До начала работы:
Для работы в технике Resin Art нельзя использовать любую смолу, даже самую лучшую, текучую, дистиллированную. Смола, дающая безупречный результат при заливке площадей или объемных поверхностей с однотонным или градиентным окрашиванием, для данной работы не пригодна. Здесь требуется смола с определенной вязкостью, сочетающая, если угодно, текучесть технических смол и чистоту ювелирных смесей.
Данная особенность необходима по двум причинам:
— Для исключения произвольного перемешивания слоев различного цвета.
— Для контролируемых манипуляций с окрашенной поверхностью.
Используйте марки, специально созданные для работы в данной технике.
Еще раз: использование смол, предназначенных для ювелирной работы, заливки полов или изготовления столешниц не гарантируют предсказуемого результата. Это факт, неоднократно проверенный на собственном опыте с различными марками смол и красителями (от порошковых пигментов и акриловых красок до специализированных красителей для эпоксидной смолы).
Рабочее место:
Застелите рабочее пространство пленкой, наденьте перчатки, приготовьте строительный фен, емкости для смешивания смолы, пигмент.
Подготовьте основу:
Не рекомендуется использовать для основы холст или схожий материал. Основа должна быть жесткой, иначе материал провиснет. Оклейте изнанку основы малярным скотчем. При работе смола образует подтеки, после застывания смеси скотч поможет легко очистить материал.
Опалубка при работе в данной технике не требуется. При формировании рисунка окрашенная плоскость периодически наклоняется в нужном направлении, слои перемещаются на поверхности, любые преграды только ограничат свободное течение краски. Кроме того, отсутствие опалубки избавит работу от формирования внешней кромки. После застывания смеси поверхность сразу имеет чистый, гладкий, глянцевый вид. Работа без шлифовки — большой плюс.
Заранее продумайте рисунок и подготовьте необходимое количество емкостей для каждой краски. Удобно действовать так: смешайте общий объем компонентов А / В в одной емкости, затем разделите готовую смесь по отдельным резервуарам (постарайтесь заранее посчитать, какой объем смолы потребуется для каждого цвета), затем окрасьте смолу и приступайте к заливке.
Процесс:
Научившись работать с исходной смесью, можно перейти к сложным модифицированным составам, формирующим прихотливый рисунок из гранулированных, ячеистых цветовых зон. Для получения таких ячеек можно использовать:
Естественное смешивание слоев:
Залейте основной цвет нижним слоем, затем добавьте тонкий разделительный слой чистой смолы, поверх добавьте слой с дополнительным цветом.
Использование модификаторов (например, Resi Blast):
Модификатор добавляется как в готовую окрашенную смолу перед началом заливки, так и на поверхность изделия с разложенной плоскостью. Может использоваться при работе в технике «грязной заливки» (смешивания цветов в одной емкости непосредственно перед заливкой). Некоторые модификаторы активно взаимодействует со смолой, оставляя на изделии углубления, ямки.
Добавление спирта к смоле (чистота спирта должна быть >90%).
Техника используется как при «грязной заливке», так и при работе традиционным методом. Спирт добавляется к смеси смолы и красителя, ячейки проявляются постепенно, по мере распределения слоев на плоскости. Нет необходимости добавлять спирт к каждому цвету — разбавьте основной цвет для взаимодействия с остальными цветами. После завершения реакции на твердой поверхности не остается следов, разводов или пятен, спирт полностью испаряется.
Использование силикона:
Желательно использовать чистое силиконовое масло. В крайнем случае можно распылить силиконовый спрей в емкость (не на готовую смесь), затем смешать жидкий осадок с краской. Далее действовать как при работе с любым модификатором.
Также для создания эффекта глубины можно последовательно окрашивать и заливать несколько слоев смолы, сообщая каждому уровню необходимые свойства.
Наконец, при случайной помарке (например, проверили твердость слоя и оставили отпечаток пальца на поверхности): просто нагрейте поврежденный участок, смола перейдет в жидкое состояние и поверхность вновь станет гладкой.
Общее время работы над «Аурелией» составило две недели. С учетом тестовых заливок и проверки материалов — почти два месяца.
Главный опыт: учитесь на чужих ошибках (если вы прочли весь текст — вы так и поступаете). Но если все-таки случилось ошибиться — проанализируйте ситуацию и запомните урок. Только упорство и труд приводят к успеху.
Мастер-класс смотреть онлайн: Мастер-класс по работе с эпоксидной смолой
Чуть информации об этом чудо-материале.
Главной особенностью эпоксидки является то, что она застывает не сама собой, за счет испарения компонентов (такой принцип у лаков), а засчет химической реакции, которая происходит между смолой и отвердителем. В результате этой реакции происхоодит полимеризация состава и он становится твердым (необратимо). Благодаря тому, что не происходит испарения компонентов, эпоксидка не дает усадки, то есть какую линзу вы налили на заготовку, такую же и получили после застывания. Лак же дает усадку — если налили выпуклую лужицу, то после высыхания она превратиться в пленочку, потеряв часть объема.
Итак начнем!
1. Для работы нам потребуется эпоксидная смола, отвердитель к ней, два шприца без катереров, одноразовый стаканчик, палочка для перемешивания.
2. Одним шприцом отмеряем смолу, вливаем в стаканчик, то же самое делаем с отвердителем. Рекомендуется вливать отвердитель в смолу, не наоборот. Осторожно! отвердитель обычно достаточно жидкий и может брызнуть, если надавить на шприц резко.
Пропорции для смешивания смолы и отвердителя у разных производителей отличаются, поэтому внимательно изучайте инструкцию и отмеряйте именно столько, сколько рекомендует производитель, так как при неправильных пропорциях эпоксидка застынет плохо.
3. Тщательно перемешиваем две жидкости, пока содержимое стаканчика не станет однородным. Делаем это медленно, чтобы не образовывались пузырьки. Если эпоксидка и отвердитель жидкие, то образовавшиеся пузырьки быстро выходят на поверхность и лопаются, а если компоненты достаточно густые, то пузырьки остануться, где были (степень густоты компонентов зависит от производителя). Если эпоксидка перемешана недостаточно хорошо. она плохо застынет.
4. Ждем пока содержимое стаканчиика приобретет необходимую для работы консистенцию (полимеризация происхдит не сразу, эпоксидка постепенно становится более густой).
Условные стадии застывания и что удобно делать на каждой из них:
1) сначала эпоксидка достаточно жидкая и легко стекает с палочки, которой ее перемешивали — подходит для заливки в формы, благодаря своей жидкости она затекает во все уголки (более густая может не затечь в крохотные углубления и тогда рельеф будет уже не тот, если форма рельефная).
2) позже она начинает держаться на ней, как жидкий мед — подходит для создания выпуклой линзы на плоской основе, если делать линзы, когда эпоксидка более жидкая, то она будет легко стекать с заготовки вниз, не формируя линзу. На этой стадии также можно зпливать формы, если в них нет ярко выраженнного рельефа (например полусферы.)
3) потом как густой мед — эта стадия лично мне кажется наименее подходящей для работы — при набирании на палочку образуются пузырьки, которые очень сложно достать. Подходит разве что для приклеиваня деталей друг к другу. Эпоксидка имеет хорошую адгезию (хорошо прилипает) к большинству материалов, поэтому может использоваться, как клей 🙂 Не прилипает к полиэтилену, полипропилену, силикону, резине, от этих материалов она легко отслаивается (поэтому формы для заливки нужно выбирать и этих материалов). Не прилипает еще к жирным поверхностям (поэтому, если нет формы из подходящего материала, то можно любую смазать растительным маслом и заливать в нее. Но сначала обязательно нужно протестировать, как ваша эпоксидка отреагирует именно на это масло).
4) через некоторое время отделить палочкой часть эпоксидки от основной массы становится проблематично. Она еще липкая, но уже очень густая. Честно, не знаю, что на этой стадии можно делать =)
5) резиновая фаза — эпоксидка уже не липнет, но она еще не приобрела окончательной твердости, она гнется как разина. На этой стадии эпоксидку можно гнуть, мять и тд, что открывает просторы для плета воображения 🙂 ) Если вы хотите, чтобы она застыла в деформированном положении — закрепите ее в нем, иначе она распрямится обратно.
6) твердая, оконательно застывшая эпоксидка. Ногтем не продавливается, на ощупь — твердый пластик.
У разных производителей время застывания отличается, поэтому определить время этих стадий можно только опытным путем.
ВАЖНО! если мягкие эпоксидные смолы. Они остаются резиновыми (гнуться-мнуться) после полного застывания, твердость пластика не приобретают. Для некоторых изделий — самое оно. 🙂
5. Собственно, применяем эпоксидку (заливаем форму, делаем линзу и тд).
6. На эпоксидку отлично липнет вся пыль, которая летает поблизости, поэтому на время застывания ее нужно защитить от попадания разной грязи. Я делаю свои заготовки в пластиковой коробке из под конфет, можно накрывать заготовки крышками для банок, или придумать удобный для вас способ.
7. Ждем указанное производителем количество часов до полного застывания и любуемся красотой! 🙂
Нюансы:
— рабочее место я застилаю полиэтиленом, он не даст эпоксидке протечь на на стол (бумагу она пропитывает и стол пачкается), + к полиэтилену эпоксидка не прилипает, то есть если эпоксидка стечет с заготовки, то оно не прилипнет намертво к поверхности на которой лежит
— эпоксидку можно подкрашивать. Чем: специальными тоннерами (обычно они дорогие), чернилами от ручек (обычных и гелевых, чернил нужно совсем чуточку), краской, которая внутри фломастеров и маркеров, витражными красками
— НЕЛЬЗЯ допускать попадания воды в эпоксидную смолу или отвердитель, или в уже смешанные компоненты. Поэтому не стоит раотать с эпоксидкой при высокой влажности воздуха (она плохо застынет)
— не стоит работать с эпоксикой при температуре воздуха ниже 22х градусов — есть риск того, что она плохо застынет
— от холода (если зимой на балконе держать) в смоле могут появится крупинки или хлопья, тогда смолу нужно нагреть до 40-60градусов и тогда она прийдет в изначальное состояние
— ускорить врямя застывания эпоксидки можно повысив температуру воздуха (поставить на батарею, например). Не делайте температуру слишком высокой, иначе эпоксидка может закипеть, образуя много пузырьков
— эпоксидка очень текучая, она стремиться стечь вниз, поэтому ее нельзя использовать в качестве лака для рельефных объектов
— если вы делаете линзы на плоских заготвках — следите, чтобы поверхность на которой это все происходит была абсолютно горизонтальной, иначе с одной стороны линзы будет выше, чем с другой
— если линза не покрывает края заготовки, а как бы сползается к центру, значит либо эпоксидки было налито мало, либо и мало и слишком жидкой. Можно исправить залив еще одним слоем 🙂
— если близко к поверхности эпоксидки появился пузырек — подуйте на это место через трубочку для напитков, или что-то аналогичное (я использую раскрученную ручку :)) и пузырек лопнет
— некоторые эпоксидные смолы со временем желтеют (от солнечных лучей и тепла), если вы этого не хотите — покупайте эпоксидку с УФ-фильтром
— ВАЖНО!!! Эпоксидка токсична (некоторые менее токсичны, некоторые более), поэтому работать нужно в хорошо проветриваемом помещении или под вытяжкой. Это важно! Но не стоит очень паниковать, так как в рукоделии мы испольуем мизерные количества (не промышленные масштабы), и вряд ли это более вредно, чем любой лак или краска на основе растворителей (это мое мнение), но окно открыть в любом случае не помешает. Чтобы совсем себя обезопасить — можно купить респиратор, вам понадобится фильтр от паров органических веществ.
— если эпоксидка попала на руки, то оттереть ее легко с помощью спирта, а потом вымыть руки с мылом, при попадании в глаза — рекомендуется обратиться к врачу, ну понятно, что пить ее тоже не стоит.
Удачного творчества и экспериментирования! И не забывайте про технику безопасности. 🙂
Покрытие дерева эпоксидной смолой, пропитка древесины
Сразу может возникнуть вопрос: Зачем это делать, если есть лакокрасочные материалы? Но, во-первых, существуют ЛКМ и из эпоксидок, а во-вторых, иногда нужно сохранить дерево как бы в первозданном виде. «Как-бы» здесь и подразумевает его пропитку эпоксидными составами, но сделанную таким образом, чтобы смола была незаметной. Для этого нужно применить ее в том минимальном количестве, когда древесные клетки ею пропитаются, но на поверхности глянцевых следов от застывшей смолы не будет. Задача не из простых, но вполне разрешимая.
Для чего делают пропитку
Неоднородность структуры дерева, особенно у северных пород, которые зимуют, сбрасывая листья, или, в случае с хвойным породами, замедляют в холодное время года свои жизненные процессы. У них на поперечных спилах и срезах отчетливо видны годовые кольца, а на продольных распилах чередование тангенциальных узоров из светлых и более темных участков древесины.
При высушивании (естественный для изделий из древесины процесс) срезы и распилы становятся немного ребристыми, это результат неравномерного испарения из них влаги, когда более плотные светлые участки начинают выступать над поверхностью, а более рыхлые темные проваливаться вглубь из-за более быстрого испарения влаги из них.
Но рыхловатую структуру имеют и светлые участки, просто пор в них меньше, чем в темных. Со временем это вызывает проблемы с сохранностью изделий из дерева. В них проникают паразиты-древоточцы, да и грибковое или бактериальное заражение не стоит сбрасывать со счетов. Итогом становится превращение дерева в труху и в гниль. Чтобы избавится от таких разрушительных факторов, и делают всевозможные пропитки: бактерицидные, консервирующие и цементирующие структуру древесных клеток.
Как использовать полимер
Давайте сразу условимся, если возникла идея сохранить надолго какое-то изделия из дерева, но оно еще ничем не пропитано и не покрыто (имеется в виду лак или, краска), то этот шаг продуман, спешить не нужно. Потому что спешка в таком деле приведет к очень нехорошим результатам, а именно:
Если покрыть древесину слоем эпоксидки, то в силу ее высокой адгезии (способности прилипать в любому предмету, если он не из силикона, полиэтилена или тефлона) смола неминуемо быстро проникнет во все поры деревяшки. В порах находится воздух, и этот воздух неминуемо начнет выдавливаться смолой наружу в виде пузырьков в толще эпоксидки, если смолы избыток и эта «толща» осталась еще и снаружи. Особенно этот процесс интенсифицируется, если в этот момент дерево подвергается нагреву, пусть даже лучами солнца.
Отсюда вывод: работы такого рода нужно проводить в прохладном помещении окнами на север.
Но этот же процесс можно использовать и против воздушных пузырьков, в целях их удаления. Нужно всего лишь прогреть строительным феном пропитанную эпоксидкой поверхность. Смола под влиянием высокой температуры, конечно же, начнет процесс полимеризации быстрее обычного. Но не сразу, время для ее предварительного разжижения от действия нагрева у нее будет, и в эти считанные минуты пузырьки воздуха успеют выйти наружу, достичь граничащего слоя смолы с воздухом и благополучно лопнуть.
Процесс нагрева нужен и в том случае, когда требуется максимально глубокая пропитка древесины без какого бы то ни было следа эпоксидки снаружи, то есть чтобы дерево выглядело естественным, не лакированным, а смола неминуемо придаст изделию вид покрытого лаком. Для этого ее излишки, если она вся не успела впитаться, убирают холщовым тампоном, смоченном в ацетоне.
Если не стоит задача сохранения дерева в первозданном виде, а наоборот, нужен защитный (видимый) слой снаружи, тогда делают сначала максимальную пропитку, прогревают древесину на предмет выхода всех возможных воздушных пузырьков, дожидаются полного застывания смолы в течение 24 часов, и только потом покрывают изделие нужной толщины слоем.
Если деревяшка плоская и ее можно расположить горизонтально, это очень удобно. В случае же объемного изделия толстый слой эпоксидки на него нанести не получится, она неминуемо стечет под действием силы тяжести. Поэтому в таком случае применяют послойное нанесение тонким слоями раз за разом, притом с полными сроками засыхания, которые не могут быть меньше 24 часов на каждый, пока не будет достигнут удовлетворяющий вас результат.
Дерево и эпоксидная смола: как залить
На чтение 6 мин. Опубликовано
Эпоксидная смола – популярный инструмент для современных дизайнеров. На ее основе домашние мастера изготавливают оригинальные и эксклюзивные изделия. Очень красиво и необычно смотрится дерево и эпоксидная смола – смолистая субстанция отлично сочетается с опилами, древесиной различных пород, отдельными веточками.
Преимущества и недостатки эпоксидки при работе с деревом
Работа с деревом и эпоксидной смолой – увлекательное занятие. Зная, как правильно работать с эпоксидкой, можно создать удивительные по красоте вещи. Если раньше такой материал использовали при заливке различных поверхностей, то сейчас ее активно применяют в своей работе и дизайнеры. Популярность смолистая субстанция получила благодаря своим многочисленным достоинствам:
- низкому уровню истираемости;
- высокой прочности изделий и их долговечности;
- универсальность – эпоксидке можно придать любую форму;
- после полимеризации готовое изделие легко подвергается любой дополнительной обработке;
- возможность применения различных красителей.
Но эпоксидная смола для дерева обладает и некоторыми недостатками. Например, эпоксидка начинает проявлять свои заявленные качества только после соединения ее со специальным отвердителем. Смолистое вещество становится полностью безопасным только после отвердевания. В процессе работы необходимо использовать личные средства защиты и постоянно проветривать рабочее помещение.
Для дизайнерских работ лучше использовать ювелирную эпоксидку, она намного качественнее, но и обладает более высокой стоимостью.
Технологические особенности
Разбирая вопрос, как залить дерево эпоксидной смолой, нужно учитывать некоторые особенности такого материала. Структура дерева неоднородная, и внутри нее могут скапливаться воздушные пузырьки. А при смене температурного режима древесина начинает изменяться (расширяться либо сжиматься). Скопившийся воздух начинает выходить на поверхность, портя готовую работу.
Чтобы этого не допустить, при заливке смолой дерева, необходимо учитывать температуру рабочего помещения: а именно спустя 2–3 часа после окончания работ обеспечить температурный режим в +20–25⁰С. Если запланировано заливать толстый эпоксидный слой, то весь процесс нужно сделать в два этапа – так минимизируется риск появления и выхода воздуха.
Как правильно пропитывать древесину
Прежде чем использовать эпоксидные смолы для заливки древесины, рабочий материал (дерево) необходимо нагреть. Такой процесс приводит к расширению древесных пор, и более качественному проникновению смолы. После отвердевания поверхности заливку подвергают необходимой финишной обработке.
Качество итоговых работ непосредственно зависит и от правильного соотношения пропорций смолы и отвердителя. В классическом варианте на 10 частей эпоксидки добавляют 1 часть катализатора.
Как устранить появление воздушных пузырьков
Если все меры были предприняты, но на поверхности смолистой субстанции возникли пузырьки воздуха, их можно удалить. Подогревать поверхность не стоит – это приведет к появлению новых воздушных карманов. Стоит использовать один из следующих вариантов:
- С помощью тонкой иглы аккуратно проткнуть пузырь.
- Обрызгать поверхность спиртовым раствором, используя пульверизатор.
- Слишком крупные воздушные карманы просверливают. Образовавшиеся полости вычищают, поверхность обезжиривают и наносят второй слой заливки.
Варианты использования эпоксидки в дизайне
Для дизайнерской работы с деревом лучше использовать прозрачные эпоксидные смолы. Такой состав выделяет все элементы и подчеркивает красоту дерева. Очень оригинально смотрятся изделия, где использовалась заливка смолы с добавлением к ней пигмента.
Совет. При работе с красками лучше выбирать колеровочные составы той же марки, что и используемая эпоксидка.
Существует множество различных дизайнерских приемов для работы с деревом и смолой. Например, добавление к составу опилок, блесток, сухоцвета. А при использовании люминесцентных красок изделие станет просто фантастическим (светящиеся в темноте ступени не дадут оступиться, а различные подсвеченные украшения подчеркнут любой образ). Для получения эффекта нежно-молочных разводов к смоле при заливке добавляют водяные капельки. Что можно сделать?
- Оригинальная мебель. Необычными становятся мебельные элементы с заливкой из эпоксидки. Столы, стулья, даже двери можно выделить и сделать эксклюзивными. При работе можно использовать любые творческие задумки.
- Необычные полки.
Также можно создать оригинальные и необычные полочки. Сделать их можно и самостоятельно, опираясь на заданные размеры и подчеркивая общий стиль комнаты.
- Барные стойки или столешницы. Такие модели не просто подчеркивают стиль помещений, но и могут создавать отдельные
что такое бесцветная эпоксидка для заливки дерева? Двухкомпонентная безусадочная смола с отвердителем и другие варианты
Эпоксидная смола представляет собой материал, который широко применяется в различных сферах. Его используют для заливания столешниц, создания напольных покрытий, а также красивых глянцевых поверхностей. Рассматриваемый материал застывает после перемешивания со специальным веществом – отвердителем. После этого он получает новые свойства – большую прочность и неподверженность к воздействию влаги. Лучше всего обрабатывается прозрачная эпоксидная смола для заливки. В данной статье рассмотрим все о прозрачной эпоксидной смоле для заливки.
Описание
Эпоксидная смола либо как ее многие называют «эпоксидка» относится к олигомерам. Они содержат эпоксидные группы, что при воздействии отвердителей создают сшитые полимеры. Большая часть смол продается в магазинах в качестве средств, которые состоят из двух компонентов. В одной пачке обычно находится смола, обладающая вязкими и тягучими свойствами, а в другой – вышеупомянутый отвердитель, который представляет собой вещество на основе аминов либо карбоновых кислот. Обычно смолы рассматриваемой категории создаются при помощи такого процесса, как поликонденсация эпихлоргидрина с бисфенолом А, которые называют эпоксидно-диановыми материалами.
Прозрачная бесцветная смола отличается от других типов тем, что она оптически-прозрачная.
Она похожа на стекло и не задерживает световые лучи.
В данном случае оба компонента являются бесцветными, что дает возможность использовать их для литья и создавать напольное или настенное покрытие. Если продукция действительно высококачественная, то она не станет желтой или мутной даже через несколько лет после применения.
Химический состав и компоненты
Чтобы получить состав с определенными свойствами, в процессе его создания следует использовать специальные добавки. Речь идет о 2 категориях веществ.
- Отвердители и пластификаторы. Если говорить об этой группе, то в смолу добавляют отвердитель, чтобы сделать реакцию полимеризации. Для этого обычно используют такие вещества, как третичные амины, фенолы или их альтернативу. Количество отвердителя будет зависеть от характеристики основного компонента и результата, который требуется получить. А добавление пластификаторов производится, чтобы в процессе использования готовый продукт не трескался и имел хорошую гибкость. Использование данного компонента также позволяет предупредить растрескивание полученного состава в процессе просушивания изделия, которое имеет большой объем. Обычно, как пластификатор, применяется вещество, в основе которого присутствует дибутилфталат.
- Растворители и наполнители.
Растворители добавляют в случаях, когда требуется сделать состав менее вязким. Но количество растворителя должно быть минимальным, ведь по мере его добавления снижается прочность создаваемого покрытия. А если требуется придать составу какой-либо оттенок или цвет, то добавляются различного рода наполнители. Чаще всего используют следующие типы веществ:
- микросфера, что увеличивает вязкость;
- алюминиевая пудра, которая придает характерный серо-серебристый цвет;
- двуокись титана, что существенно увеличивает стойкость материала к воздействию ультрафиолета и придает покрытию белого цвета;
- аэросила, которая позволяет не допустить появление подтеков на поверхностях, что расположены вертикально;
- графитовый порошок, что дает возможность получить необходимый цвет и выравнивает структуру материала почти до идеала;
- тальк, что позволяет сделать поверхность крайне прочной и довольно ровной.
Сферы использования
Составы, где используется двухкомпонентная прозрачная эпоксидная смола, часто используются в различных сферах жизни, например, для создания брелоков, ювелирных изделий, разного рода кулонов, а также элементов декоративного характера. Кроме того, она применяется для создания продукции рекламной направленности, столешниц, наливных полов, сувениров, сантехнических деталей и изделий, что используются в ванной комнате. Очень популярны наливные напольные покрытия с необычными рисунками. Данное средство применяется для объемного декупажа, мозаики и прочих.
Вообще, применение этого материала ограничивается исключительно фантазией самого человека. Эпоксидку применяют для дерева, камня, кофейных зерен, бисера и других материалов.
Слэбы — как правильно использовать эпоксидную смолу
Эпоксидная смола является идеальным вариантом для заливки полостей и пустот в древесине (например, шпон), а также когда необходимо выровнять слэб или столешницу. Затвердевая, данный двухкомпонентный материал формирует прочную, прозрачную и одновременно с этим идеально ровную поверхность. В состав компаунда могут добавляться красители и разные наполнители с целью создания дополнительных эффектов.
Решив слэб купить, в процессе её заливки эпоксидной смолой важно соблюдать следующие требования:
- температура при работе не ниже 18 градусов Цельсия;
- умеренная влажность внутри помещения;
- толщина заливки — 20 мм вне зависимости от площади;
- соотношение смолы и отвердителя по весу: 100 к 45;
- допускается толстослойная заливка, если количество отвердителя снизить до 30%.
Как смешивать компоненты?
Перемешивание должно осуществляться в два этапа: сначала в одной емкости в течение 3-5 минут, а затем повторно 2-3 минуты в другой емкости. Полученная масса должна получиться однородной и не иметь разводов.
Как убрать пузыри воздуха?
После заливки нет необходимости удалять воздушные пузыри, поскольку воздух будет выходить самостоятельно благодаря специальным добавкам в составе. Однако если у изделия имеются углубления, воздух с поверхности придется убирать через некоторое время после завершения процесса заливки.
Эффективным решением в данном случае станет газовая портативная горелка, мгновенно убирающая пузырьки при поднесении к отливке.
Убрать воздух можно и с помощью иголки, путем прокалывания, либо выгоняя его за пределы отливки.
Также подойдет бытовой или строительный фен. При нагреве поверхности пузырьки будут быстро лопаться.
Нюансы работы с эпоксидной смолой и деревом
Места, где древесина контактирует со смолой нужно предварительно загрунтовать. Эпоксидная композиция из грунта и отвердителя станет оптимальным вариантом. После грунтования воздух самостоятельно будет выходить при заливке. Без грунтовки пузыри воздуха могут скапливаться на краях обрабатываемого материала.
Правила смешивания
- количество компонентов нужно подбирать не по объему, а по весу;
- допускается перемешивание как вручную, так и с помощью миксера.
Мебель из древесно-полимерного композита с низкой горючестью — ScienceDaily
Дерево — популярный материал в дизайне интерьеров, но его водопоглощение ограничивает его использование в ванных комнатах, где натуральное дерево легко обесцвечивается или покрывается плесенью. Ученые и партнеры Fraunhofer разработали древесно-полимерный композиционный материал для мебели, устойчивый к влажности и обладающий низкой горючестью.
Ресурсосберегающие древесно-полимерные композиты (ДПК) — это последняя тенденция в материалах для садовой мебели и других наружных применений, особенно для настилов террас, а также для обшивки и ограждений. В рамках спонсируемого ЕС проекта LIMOWOOD исследователи из Института исследования древесины им. Фраунгофера, Wilhelm-Klauditz-Institut WKI в Брауншвейге теперь сотрудничают с промышленными партнерами в Бельгии, Испании, Франции и Германии в разработке материалов, подходящих для прессования в влагостойкие плиты WPC для изготовления внутренней мебели.
Эти плиты состоят примерно на 60 процентов из древесных частиц и на 40 процентов из термопластического материала, обычно полипропилена или полиэтилена.Как деревянные, так и пластмассовые компоненты могут быть получены из вторичного сырья. Древесный компонент в плитах WPC может быть заменен другими продуктами из лигноцеллюлозы, полученными из волокнистой части растений, таких как конопля или хлопок, или шелухой рисовых зерен и семян подсолнечника. Все эти материалы полностью пригодны для вторичной переработки. Более того, прессованные плиты WPC, произведенные исследователями WKI, не содержат формальдегид. «Спорный вопрос о выбросах формальдегида из-за связующего вещества, используемого в обычных прессованных деревянных изделиях, в данном случае не является проблемой», — говорит исследователь WKI д-р. Арне Ширп.
Испытания демонстрируют низкую горючесть плит ДПК
Выбрав соответствующие добавки, исследователи смогли улучшить огнезащитные свойства своих плит из ДПК. Первоначально они разработали свою формулу в лабораторных масштабах, используя коммерчески доступные антипирены, не содержащие галогенов, которые добавляли к смеси древесины и полимера во время фазы плавления. Первый шаг заключался в определении предельного кислородного индекса испытуемого объекта: этот параметр определяет поведение пластмасс или древесно-наполненных пластиковых компаундов при воздействии огня.Он представляет собой минимальную концентрацию кислорода, при которой материал будет продолжать гореть после возгорания. Чем выше это значение, тем ниже воспламеняемость материала. Ширп и его коллеги получили наилучшие результаты с комбинацией антипиренов, таких как красный фосфор и расширенный графит. Предельный кислородный индекс плит WPC, обработанных таким образом, увеличивается до 38 процентов при условии, что содержащиеся в них древесные частицы также являются огнестойкими. Для сравнения, предельный кислородный индекс стандартной древесностружечной плиты составляет 27 процентов, а необработанной плиты ДПК — 19 процентов.Даже в испытании с одним источником пламени, в котором горелка Бунзена прижимается к испытательному образцу, обработанные плиты из ДПК продемонстрировали высокую огнестойкость. Даже после 300-секундной выдержки доски не загорелись. Напротив, контрольные образцы — стандартной древесно-стружечной плиты и необработанной плиты ДПК — загорелись и продолжали гореть.
Другой особенностью нового материала WPC является то, что он очень мало впитывает воду и поэтому хорошо подходит для использования в ванных комнатах и кухнях.Даже после погружения в кипящую воду на пять часов материал остается неповрежденным, тогда как обычная древесно-стружечная плита в этом испытании была полностью разрушена. Единственным ограничивающим фактором при применении WPC является его неспособность выдерживать высокие статические нагрузки. Но даже здесь оказалось возможным повысить ее прочность на изгиб до уровня, намного превышающего аналогичный показатель у обычных древесностружечных плит, за счет разумного сочетания компонентов материалов.
Древесно-полимерные композиты можно производить разными способами.Наиболее часто используемые процессы — это литье под давлением и экструзия, в которых различные компоненты — древесные волокна, термопластические материалы и добавки — плавятся под высоким давлением при высокой температуре и формуются в непрерывной форме. Команда Арне Ширпа сосредоточила свое внимание на технологии прессования, потому что это лучший способ производить плиты для использования в мебельном строительстве. «Полученные плиты имеют такой же внешний вид, как и цельнодеревянные изделия, и их можно склеивать или скреплять шурупами для создания красивой мебели.Они подходят для всех декоративных, ненесущих элементов ». Но есть много других применений древесно-полимерных композитов, включая наружную облицовку зданий, строительство выставочных стендов и внутреннюю отделку домов и кораблей. партнеры по проекту LIMOWOOD стремятся заполнить пробел между высокими и низкими сегментами мебельного рынка, который колеблется между дорогими и необязательно экологически безопасными материалами и дешевыми продуктами из ДСП или древесноволокнистых плит, которые в настоящее время в основном производится с использованием связующих на основе формальдегида. Исследователи WKI представят прототипы своих огнеупорных плит WPC на выставке Interzum в Кельне с 5 по 8 мая.
История Источник:
Материалы предоставлены Fraunhofer-Gesellschaft . Примечание. Содержимое можно редактировать по стилю и длине.
Древесно-наполненные пластмассы: им нужны правильные добавки для прочности, хорошего внешнего вида и долгого срока службы
Смазочные материалы необходимы для предотвращения разрыва кромок плит WPC.(Образец без смазки любезно предоставлен Crompton Corp.)
Связующие агенты, такие как Equistar’s Integrate малеинированный полиолефин, связывают полярное древесное волокно с неполярной полиолефиновой матрицей. Внизу: несвязанный деревянный настил из ПНД показывает отсутствие сцепления (пространство вокруг древесного волокна). Вверху: соединенное дерево-HDPE с плотным склеиванием.
Ferro разработала специальные смазочные материалы для преодоления отрицательного взаимодействия между стеаратами металлов и связующими веществами.
Палубная доска Wood-HDPE, обработанная боратом цинка (вверху), не показывает признаков грибкового разложения по сравнению с необработанной доской (внизу), у которой есть пустоты, где грибок поглотил древесные волокна.
Предыдущий следующийДревесно-пластиковые композиты, или ДПК, уже 1.3-миллиардный рынок и растет на 20% ежегодно. Этого достаточно, чтобы привлечь повышенное внимание поставщиков добавок к особым потребностям применения ДПК в жилых палубах, перилах, ограждениях, дверях, оконных рамах, открытых спа и беседках. Также ведутся работы по сайдингу и кровле. Поставщики заняты определением оптимального выбора существующих добавок и разработкой новых, чтобы улучшить физические свойства, внешний вид поверхности и долговечность WPC.
Правильный выбор добавок для WPC имеет решающее значение как для производительности, так и для обработки.Профнастил не оказался таким «необслуживаемым», как изначально рекламировалось. В некоторых случаях возникали проблемы коробления, расслоения, окрашивания и изменения цвета. По мере того, как WPC пытаются перейти к более структурным нагрузкам, добавки, повышающие механическую прочность, становятся неотложной задачей. А на экструзионной линии технологические добавки необходимы как для достижения экономичной скорости линии, так и для получения гладких поверхностей без так называемого разрыва кромок.
Наиболее важными областями выбора добавок для WPC являются связующие, смазочные материалы и красители, за которыми не отстают химические пенообразователи и биоциды.Выбор конкретных типов для WPC зависит от основной смолы. Древесные композиты на основе полиэтилена — в основном переработанный HDPE — составляют 80% рынка. Дерево-ПВХ составляет от 10% до 13%, а дерево-полипропилен — 8%. Древесно-полистирол составляет от 1% до 2%.
Муфта для прочности
Связующие агенты связывают древесное волокно с полимерной матрицей. Они повышают прочность на изгиб и жесткость, обычно называемые модулем разрыва (MOR) и модулем упругости (MOE), соответственно, которые используются в деревообрабатывающей промышленности.Связующие агенты также улучшают стабильность размеров, ударопрочность и дисперсию волокон, снижая при этом ползучесть. Дополнительная прочность важна для ограждений, ступеней лестниц, ограждений и строительных конструкций. Но в настиле связующие вещества используются в основном для уменьшения водопоглощения, которое разбухает древесные волокна у поверхности плиты, вызывая напряжения, которые могут привести к растрескиванию.
Связующие агенты особенно ценны в полиолефиновых WPC, поскольку они преодолевают несовместимость между полярным химическим составом древесины и неполярной матрицей из смолы.Лидируют химически модифицированные (обычно малеинированные) полиолефины, полученные путем прививки малеинового ангидрида на основную цепь полимера посредством реактивной экструзии. Обычно они продаются по цене около 1,50 доллара за фунт и используются на уровнях от 1% до 2%.
Новые разработки включают химически модифицированные полиолефины, которые не получают прививкой, длинноцепочечный хлорированный парафин и реактивные связующие для древесины и ПВХ.
Crompton Corp. недавно выпустила на рынок Polybond 3029MP, малеинированный полиэтилен высокой плотности с новым меньшим размером частиц — микропеллетами 20 меш, который, как утверждается, улучшает дисперсию.Сообщается, что при 2% он может удвоить свойства древесины на изгиб и растяжение 60% из HDPE.
Crompton также имеет запатентованный малеинированный полипропилен, который, как сообщается, превосходит связующие агенты, полученные путем реакционной экструзии, отчасти благодаря способности включать более высокие уровни малеинового ангидрида (МА). Утверждается, что испытания показали значительно более высокую прочность на растяжение, изгиб и ударную вязкость с этой присадкой, меньшую подверженность влиянию смазочного материала и снижение водопоглощения на 40%.
Equistar Chemical предлагает серию Integrate связывающих агентов на основе малеинированного полиэтилена для композитов на основе полиэтилена, а также новые полипропилены с малеинированным полипропиленом для полипропилена из дерева и полипропилена.Джим Крон, менеджер по развитию бизнеса, утверждает, что древесно-полиэтиленовые пиломатериалы обычно показывают, по крайней мере, на 50% более высокую MOR и на 20% более высокую MOE с этими добавками.
DuPont предлагает привитый МА Fusabond MB-226D для дерева-PE и MD-353D для дерева-PP. Предел прочности на разрыв древесины из полиэтилена высокой плотности (HDPE) на 200–300% выше, чем у несвязанных составов. DuPont также разработала новую химию, которая заменяет прививку запатентованными сополимерами, изготовленными из мономеров с ангидридными функциональными группами, которые, как говорят, хорошо работают с древесным полиэтиленом.
Eastman Chemical предлагает связующие агенты с привитым эполеном МА, такие как эполен G-2608 на основе полиэтилена и более новые марки E-43, G-3003 и G-3015 на основе полипропилена. «Мы наблюдаем увеличение на 70% общих свойств растяжения, увеличение MOR на 30-35%, удар по Изоду без надрезов более чем на 200%, улучшение HDT примерно на 20% и резкое повышение влагостойкости», — говорит менеджер по развитию бизнеса Дэймон. Холлис.
Dover Chemical предлагает длинноцепочечный хлорированный парафин (LCCP) в качестве нереактивного связующего агента, который, по-видимому, улучшает сохранение прочности HDPE и PP WPC во время круговорота влажности.В отличие от малеинированных олефинов, которые имеют тенденцию ухудшать смазочные свойства, LCCP, как сообщается, увеличивает смазку, а также устойчивость к ультрафиолетовому излучению и влаге. Согласно данным Dover, LCCP дает более высокий модуль упругости и прочность на разрыв, чем стандартный состав стеарата цинка / EBS, содержащий 60% древесины в HDPE; однако крутящий момент экструдера был выше при использовании LCCP. Но в сочетании с фирменной смазкой в однокомпонентной системе (Doverbond DB 4300) были достигнуты как более низкий крутящий момент, так и более высокие физические характеристики. Фактически, смазанная система имеет более высокую жесткость и прочность, чем несмазанный контроль, в отличие от образца стеарата / EBS.MOR PP и HDPE с 60% древесины на 40% выше для DB 4300, чем для стеарата / EBS, добавляет коммерческий директор Том Келли. Цена 1,50 доллара за фунт, однокомпонентная упаковка может использоваться с содержанием от 3% до 5% вместо 1-2% обычного связующего агента плюс 3-5% традиционных смазочных материалов.
Clariant Additive Masterbatches предлагает два концентрата компатибилизатора. Cesa-mix 8611 представляет собой функционализированный сополимер для использования в полиэтилене и полипропилене, а Cesa-mix 8468 представляет собой высокофункциональную систему, которая, как утверждается, улучшает качество поверхности древесины и полипропилена.Новые разработки для улучшения совместимости древесины и ПВХ находятся в разработке в Crompton. Проблемы другие, чем с полиолефинами, потому что и дерево, и ПВХ полярны. «Но древесина имеет много кислоты на поверхности, которая разрушает ПВХ, а ПВХ образует соляную кислоту, которая разрушает древесину», — объясняет доктор Питер Френкель, директор по исследованиям и разработкам виниловых добавок. Одним из решений является обработка древесных волокон стабилизатором проклейки перед компаундированием. Mark W15 — это новый запатентованный проклеивающий агент для древесины, который действует как улучшающий совместимость и термостабилизатор, а также значительно улучшает прочность на растяжение и изгиб.
Crompton также разрабатывает новый реактивный компатибилизатор для древесины и ПВХ. Он предназначен для смешивания с матрицей ПВХ, чтобы сделать его совместимым с древесным волокном и улучшить свойства.
Смазочные материалы необходимы
Смазочные материалы увеличивают производительность и улучшают внешний вид поверхности WPC. WPC могут использовать стандартные смазочные материалы для полиолефинов и ПВХ, такие как этилен-бис-стеарамид (EBS), стеарат цинка, парафиновые воски и окисленный полиэтилен.
EBS со стеаратом цинка широко используется в древесине-HDPE.Однако существуют новые альтернативы, поскольку известно, что стеараты металлов отделяют малеиновый ангидрид малеиновых связующих агентов, снижая эффективность как смазки, так и связующего агента. Эти новые смазочные материалы продаются по цене около 1 доллара за фунт против 70–90 центов за фунт для EBS и стеарата цинка.
В WPC используется примерно в два раза больше смазки, чем в стандартных пластмассах. Для HDPE с типичным содержанием древесины от 50% до 60% уровень смазки может составлять от 4% до 5%, в то время как для аналогичного композита дерево-ПП обычно используется от 1% до 2%.Общий уровень смазки в дереве и ПВХ составляет от 5 до 10 частей на 100 частей.
Struktol предлагает новый запатентованный пакет смазочных материалов TPW 104 для древесно-полиолефиновых композитов. Он содержит стеарат цинка и поэтому не рекомендуется для использования с связующими агентами на основе малеинового ангидрида. Также новинкой является TPW-113, пакет с неметаллической смазкой для древесных полиолефинов. Для дерева и ПВХ Struktol предлагает пакеты смазочных материалов TPW-012 и TR-251, в которых стандартные смазочные материалы из жесткого ПВХ сочетаются с «уникальным химическим составом», — говорит менеджер по продукции Майк Фулмер.
Lonza Group разработала более совершенную альтернативу своему стандартному EBS (Acrawax C) плюс стеарат цинка. Glycolube WP-2200 — это новая запатентованная амидная смазка, не содержащая стеаратов металлов. Сообщается, что он хорошо показал себя в полевых испытаниях дерево-HDPE и имеет потенциал для композитов дерево-ПП и дерево-ПВХ. Недавние испытания показали снижение общего использования смазки с 4,5% до 3% при увеличении производительности экструдера более чем в два раза.
Crompton предлагает смазочные материалы на основе жирных кислот для древесных полиолефинов.К ним относятся стеараты металлов, амиды и сложные эфиры. Смазочные материалы для композитов дерево / ПВХ включают как внутренние, так и внешние смазочные материалы Marklube.
Clariant Additive Masterbatches предлагает Cesa-process 9102, фторэластомер для экструзии древесных полиолефинов. Cesa-process 8593 и 8633 — запатентованные смазочные системы для экструзии древесины и полиолефина. Cesa-process 8477 — это высоконагруженная система жирных эфиров для экструзии и литья под давлением древесины и полиолефина.
Полимерные добавки Ferro Corp., разд.разработала две новые серии смазочных материалов для WPC. Серия SXT 2000 смешивает металлические стеараты с неметаллическими смазочными материалами для древесных полиолефинов. Серия SXT 3000 не содержит стеаратов металлов. По словам технического менеджера по смазочным материалам Луи Брандевиде, несмотря на то, что SXT 3000 стоит дороже за фунт, он настолько эффективен, что позволяет снизить нагрузку на смазку при одновременном повышении производительности и качества продукции. Оба семейства смазочных материалов показали значительный рост производительности — до 50% по сравнению с традиционными показателями.
Reedy International, поставщик эндотермических химических пенообразователей Safoam, предлагает три новых смазки для вспененных композитов из ДПК. Safoam WSD — это смазка и антиоксидант, наносимый на древесную муку. Он предназначен для полипропилена и ПВХ с содержанием древесины до 70%.
Safoam WLB — уникальная внешняя смазка на основе парафина из полиэтилена высокой плотности для композитов из ПВХ, полипропилена и полиэтилена высокой плотности. Сообщается, что он допускает очень низкие уровни использования. Третий продукт — это сильно разветвленная внутренняя смазка на основе сложноэфирного воска, предназначенная для лучшего смачивания древесных волокон, чем при использовании комбинаций EBS / стеарат металла.
Красители для WPC
Красители используются для придания как вида дерева, так и устойчивости к ультрафиолетовому излучению. Поставщики маточных смесей используют стойкие к цвету, хорошо отражающие и погодостойкие пигменты, чтобы удовлетворить спрос на лучшую стойкость к выцветанию при минимально возможных затратах. Уровни пигмента должны быть от 1% до 3% или выше, чтобы избежать окрашивания древесины. Цветные концентраты, специально предназначенные для WPC, обычно включают смазку и часто представляют собой индивидуализированные многофункциональные упаковки, которые могут включать связующие агенты, противомикробные средства и УФ-стабилизаторы.
Accel Corp., которая работает в сфере производства композитных материалов более 10 лет, предлагает индивидуальные красители и суперконцентраты добавок для композитов дерево-ПЭ и дерево-ПВХ.
Красители для пластмасс Ferro’s Div. представила стандартные цвета дерева и полиолефина, такие как коричневый тик, кедр, выветрившийся серый и красное дерево, а также индивидуальный подбор цвета концентратов, жидкостей и непылящих гранул.
Clariant Masterbatches предлагает стандартные суперконцентраты коричневого, темно-красного, серого и дубового цветов, а также индивидуальные цвета для композитов из полиэтилена, полипропилена, ПВХ и полистирола.Красители рассчитаны на содержание древесины от 30% до 70%.
Techmer PM представила красители из красного дерева, кедра, коричневого, белого и черного цветов для древесных композитов из полиолефина и ПВХ.
Химическое вспенивание растет
Существует большой интерес к химическому вспениванию WPC для снижения веса и стоимости материалов, а также для улучшения внешнего вида поверхности, скорости обработки, а также простоты пиления, прибивания гвоздей, привинчивания и окраски готовой продукции. Около 20% всех изделий из ДПК, в основном из дерева и ПВХ, в настоящее время вспенены.
Используются как эндотермические, так и экзотермические химические пенообразователи (CFA). Вспенивание кристаллических полимеров, таких как ПЭ и ПП, более жесткое, чем для аморфных полимеров, таких как ПВХ и ПС, поскольку последние обычно имеют лучшую прочность расплава. Когда в смесь добавляется большее количество древесины, как в продуктах для настила из полиолефина, задача становится особенно сложной.
Говорит Билл Кростич, президент компании Onaga Composites, производящей древесно-полиолефиновые компаунды: «Мы видим, что CFA находят свою нишу в досках для заборов и внешней отделки, и в меньшей степени — в настиле, где содержание древесины может достигать 70%.«Он отмечает, что чем больше древесины, тем меньше смолы нужно вспенить.
Хотя это непросто, Майк Риди из Reedy International говорит, что вспенивание ДПК с более высоким содержанием древесины можно осуществить с помощью подходящих материалов, добавок, и условий обработки. Он приводит в пример новый продукт для настила из полипропилена с 65% -ным содержанием древесины, произведенный с использованием Safoam CFA и смазочных материалов на коническом двухшнековом экструдере, вращающемся в противоположных направлениях. Результатом является плотность 0,788 г / см 3 — от 30% до 35%. ниже, чем невспененные древесные полиолефины.
Подразделение Clariant’s Additives Masterbatches Business предлагает серию CFA Hydrocerol PLC, которая включает эндотермические, экзотермические и эндо-экзотермические смеси для древесных композитов из полиолефина, ПВХ и полистирола. По словам нового менеджера по развитию бизнеса Денниса Хаффа, «Люди, использующие наши пенообразователи, обычно имеют содержание древесины ниже 50%, что обеспечивает значительный потенциал пенообразования».
Bergen International отметила, что его Foamasol CFA используются в древесных композитах из ПВХ, полиолефина и полистирола, в первую очередь для декоративной лепнины, такой как облицовочные доски для сайдинга, перила и панели для спа, где потеря физических свойств из-за вспенивания не является проблемой.«Большинство наших клиентов используют древесину с содержанием древесины от 20% до 30%. Мы стремимся снизить вес на 5-10%, — говорит президент Деннис Кин.
Crompton предлагает свое семейство экзотермических CFA Celogen, которые можно использовать для вспенивания древесно-полиолефиновых и ПВХ-композитов. Techmer PM предлагает три новых стандартных суперконцентрата CFA для древесных полиолефинов. Обычно это индивидуальные рецептуры, включающие красители и другие добавки. Продукты включают экзотермические типы и эндо-экзотермические смеси с различными загрузками и температурами разложения.
Accel Corp. предлагает как эндотермические, так и экзотермические CFA, как правило, в виде многофункциональных добавок и красителей для настилов и ограждений из дерева-ПЭ, дерева-ПВХ, а в последнее время — настилов и ограждений из дерева-ПП.
Борьба с плесенью и плесенью
Плесень, плесень и пятна на некоторых настилах из ДПК побуждают производителей рассматривать противогрибковые биоциды, которые защищают пластмассовый компонент и сохраняют его внешний вид или предохраняют деревянную деталь от гниения, а также уменьшают влажность абсорбция.Многие продукты предназначены для обоих.
Было показано, что атмосферные воздействия и ультрафиолетовое излучение разрушают поверхность WPC в течение нескольких недель после воздействия. «Они имеют тенденцию становиться светлее после первоначальной установки, так как цветные экстрактивные вещества и лигнин из древесных волокон удаляются дождем. При продолжительном воздействии разрыхление древесных волокон и разрушение пластмассового компонента сопровождается изменением цвета. Кроме того, влага может привести к потере механических свойств и создания более благоприятной среды для роста грибков », — объясняет Джерри Капоччи, менеджер по маркетингу компании Ciba Specialty Chemicals.
Ciba предлагает Irgaguard F3000, тиазолилбензимидазол, который считается широко эффективным фунгицидом для композитов дерево-полиолефин и дерево-ПВХ. Разработанный EB 43-25 сочетает в себе Irgaguard F3000 с запатентованной присадкой. Это фунгицид широкого спектра действия, который может устранить или уменьшить пятна из-за взаимодействия железа, танина и влаги.
U.S. Borax предлагает борат цинка Borogard ZB в качестве консерванта для композитов дерево-полиолефин и дерево-ПВХ. По словам технического менеджера Марка Мэннинга, он обладает широким спектром действия против разрушающих древесину организмов, а также устойчивостью к нагреванию и ультрафиолетовому излучению, а также устойчивостью к выщелачиванию и атмосферным воздействиям.
«Лабораторные оценки коммерческих продуктов из ДПК против разрушающих древесину организмов, таких как гниющие грибы и термиты, показали потерю веса от 10% до 20% всего за четыре месяца, что соответствует потере веса от 20% до 40% за 50 / 50 древесно-пластиковых WPC », — говорит Мэннинг. Но когда Borogard ZB был добавлен к настилу из ПНД с содержанием древесины от 50% до 70%, потеря веса составила менее 1,1%, сообщает он.
Rohm and Haas продает биоциды винизен на основе дихлороктилизотиазолона (DCOIT) для композитов дерево-ПВХ.Недавно коммерческий Vinyzene SB27 представляет собой концентрат DCOIT на виниловом носителе.
Компания также проводит полевые испытания нового SB27-ELV, который содержит 10% DCOIT в полиолефиновом тройном сополимере, предназначенном для композитов дерево-полиолефин. Этот устойчивый к выщелачиванию и УФ-устойчивый продукт считается эффективным при содержании от 0,04% до 0,1%.
Новые разработки в области обработки досок из натуральной древесины также имеют потенциал для обработки древесной муки, используемой в ДПК, для предотвращения изменения цвета. Lonza представила альтернативу хром-медно-мышьяку (CCA), канцерогенному консерванту для древесины, запрещенному EPA в декабре.2003. Карбокват Lonza — это соединение четвертичного аммония, которое можно использовать для обработки древесной муки для производства ДПК. Ciba также предлагает новую запатентованную обработку древесины, готовую к отбору проб. Struktol работает над антикоррозийными смазками для древесины, которые нейтрализуют дубильные вещества.
Заменитель древесины тальком?
Замена части древесной муки и смол в изделиях из древесины-полиэтилена высокой плотности и древесины-полипропилена является одним из основных направлений исследований и разработок поставщика талька Luzenac America. Как сообщается, испытания HDPE с 60% -ной загрузкой наполнителя (33% древесины / 27% талька) показывают значительное улучшение MOE и MOR, HDT и характеристик ползучести.По словам Люзенака, производительность увеличивается на 15% при замене 10% древесины в рецептуре на тальк. Повышение производительности до 37% за счет замены талька на древесину на 50%. Поглощение влаги также намного ниже.
Основы до и после: шпатлевка для дерева — Design * Sponge
Всем счастливого четверга! Сегодня на Before & After Basics я хочу обсудить использование шпатлевки для дерева для ремонта повреждений и заполнения нежелательных отверстий в оборудовании.Это super важная часть покраски и ремонта мебели, которая может изменить вашу отделку или испортить ее! Процесс, который я описываю сегодня, предназначен для предметов, которые в конце концов будут окрашены, поэтому, если вы хотите украсить старую мебель, это ваш первый шаг. Давайте начнем! — Барб
НАЖМИТЕ ЗДЕСЬ, чтобы получить полное руководство после прыжка!
Материалы
- шпатлевка для дерева — я предпочитаю Elmer’s
- клей для дерева
- шпатель для шпатлевки
- Орбитальная шлифовальная машинка / шлифовальные губки
- тряпки
Инструкции
1.Убедитесь, что заполняемая область безопасна и не содержит мусора. Если у вас остались незакрепленные детали шпона, удалите их или приклейте клеем для дерева.
2. Выберите шпатлевку для дерева, которая лучше всего подходит для проекта, над которым вы работаете, и убедитесь, что он поддается окраске / окрашиванию.
3. Нанесите шпатлевку на поврежденный участок или нежелательные отверстия в оборудовании и выровняйте все это шпателем. Большую часть шпатлевки следует наносить на поврежденную часть вашей детали, а не на древесину за пределами повреждения, но, особенно при больших исправлениях, могут быть некоторые перекрытия.Я должен сказать, что, прочитав несколько «практических рекомендаций» по использованию шпатлевки, я согласен с некоторыми и — основываясь на большом личном опыте — не согласен с другими. Бывают моменты, когда вам нужно немного выйти за рамки, чтобы получить идеально гладкий вид. (Просто убедитесь, что после завершения все это кажется гладким на ощупь, иначе краска не станет гладкой.) Используйте шпатель, чтобы провести по поверхности и удалить излишки наполнителя. Очень важно использовать качественную шпатлевку для дерева, особенно при заполнении больших поврежденных участков, чтобы не было проблем с усадкой и растрескиванием.
4. Дайте ему полностью высохнуть. Время будет зависеть от размера залитой области, но отверстие для оборудования обычно высыхает через пару часов. Для высыхания более крупных поврежденных участков может потребоваться 24 часа.
5. Отшлифуйте заполненный участок вручную или с помощью орбитальной шлифовальной машины. После шлифовки поверхности убедитесь, что она полностью гладкая и заполнена до поверхности дерева. Если нет, нанесите еще шпатлевки, дайте высохнуть и снова отшлифуйте.
6.Когда поверхность будет полностью заполнена и отшлифована, загрунтуйте деталь. Я обнаружил, что древесный наполнитель и отшлифованные участки по-разному воспринимают краску, поэтому грунтовка детали обеспечивает ровную поверхность для красивой гладкой окраски.
7. Покрасьте!
Надеюсь, это будет полезно для всех вас! Увидимся на следующей неделе!
Наполненный полимер — Большая Химическая Энциклопедия
Композиты в виде частиц. Эти композиты охватывают широкий спектр материалов.Как следует из слова «частицы», армирующая фаза часто имеет сферическую форму или, по крайней мере, имеет размеры одинакового порядка во всех направлениях. Примерами являются бетон, наполненные полимеры (18), ракетное топливо soHd, а также металлические и керамические частицы, в том числе металлические матрицы (1). [Pg.4]Эта статья посвящена синтезу, свойствам и применению окислительно-восстановительных допируемых электронно-проводящих полимеров и представляет собой обзор области с использованием конкретных примеров для иллюстрации общих концепций. Был опубликован ряд отличных обзорных статей (1–13).Полимеры с металлическими частицами, где электрическая проводимость является результатом просачивания проводящих частиц наполнителя в изолирующую матрицу (14), и ионопроводящих полимеров, где перенос заряда является результатом движения ионов и, таким образом, представляет собой проблему массопереноса. (15), не обсуждаются. [Pg.35]
Слайды Микроструктуры стеклопластика, стеклонаполненного полимера, металлокерамики, деревянного элемента автомобильной шины, армированной кордом. [Pg.291]
ABS, поликарбонат и полисульфон), но сильно влияет на кристаллические полимеры.Особенно интересно и технически важно, что для многих кристаллических полимеров ненаполненный полимер имеет температуру теплового отклонения (при напряжении 1,82 МПа), аналогичную Tg, тогда как наполненные полимеры имеют значения, близкие к T (Таблица 9.2) . [Стр.189]
Армированные стекловолокном марки SAN демонстрируют модуль упругости в несколько раз больше, чем у ненаполненного полимера, и, как и в случае с другими стеклонаполненными полимерами, пониженный коэффициент теплового расширения и меньшую усадку при формовании. Таким образом, материалы представляют интерес из-за их высокой жесткости и стабильности размеров.[Pg.441]
Нейлоны из стекловолокна обладают сопротивлением ползучести, по крайней мере, в три раза большим, чем полимеры без наполнителя. В случае ударной вязкости ситуация сложная, поскольку нейлоны без наполнителя имеют тенденцию к разрушению, демонстрируя жесткое разрушение, тогда как полимеры с наполнителем ломаются с хрупким разрушением. С другой стороны, стеклонаполненные полимеры менее чувствительны к надрезам, и в некоторых испытаниях и условиях эксплуатации стеклонаполненные нейлоны могут оказаться более удовлетворительными. [Pg.498]
В случае стеклонаполненных полимеров формовочная усадка несколько ниже (0.003-0,005 см / см). [Pg.575]
Слои в пластинчатой структуре талька соединяются очень слабыми силами Ван-дер-Ваальса, и поэтому происходит расслоение при низком напряжении сдвига. Пластинчатая структура обеспечивает высокое удельное сопротивление и низкую газопроницаемость для наполненных тальком полимеров. Кроме того, тальк обладает рядом других уникальных свойств, связанных со структурой: низкая абразивность, смазывающий эффект и гидрофобный характер. Гидрофобность может быть увеличена путем покрытия поверхности стеаратом цинка.[Pg.633]
Следует еще раз отметить, что наполненные полимеры могут рассматриваться как трехфазные системы только номинально, поскольку термодинамически межфазная фаза не может рассматриваться как отдельная фаза. [Стр.16]
Альтернативная причина, по которой размер частиц может влиять на вязкость расплава полимера или раствора, состоит в агломерации наполнителя. Чем выше дисперсность наполнителя, тем выше его склонность к агломерации [138-140, 161]. Агломерация, как будет показано ниже, влияет на свойства наполненных полимеров.[Pg.24]
Nielsen предложил формулу [216] для оценки модуля упругости наполненного полимера … [Pg.30]
См. Также в источнике #XX — [ Стр.62 , Стр.64 , Стр.144 , Стр.195 ]
См. Также в источнике #XX — [ Стр.118 ]
См. Также в источнике №XX — [ Стр.10 ]
См. Также в источнике №XX — [ Стр.36 , Стр.37 ]
См. Также в источнике №XX — [ Стр.9 ]
См. Также в источнике №XX — [ Стр.36 , Стр.37 ]
См. Также в источнике №XX — [ Стр.99 , Стр.209 , Стр.215 ]
См. Также в источнике №XX — [ Стр.278 , Стр.279 , Стр.280 , Стр.281 , Стр.282 , Стр.283 , Стр.284 , Стр.285 , Стр.286 , Стр.287 , Стр.288 , Стр.289 , Стр.290 , Стр.291 , Стр.292 , Стр.293 , Стр.294 , Стр.295 , Стр.296 ]
См. Также в источнике №XX — [ Стр.278 , Стр.279 , Стр.280 , Стр.281 , Стр.282 , Стр.283 , Стр.284 , Стр.285 , Стр.286 , Стр.287 , Стр.288 , Стр.289 , Стр.290 , Стр.291 , Стр.292 , Стр.293 , Стр.294 , Стр.295 , Стр.296 ]
См. Также в источнике №XX — [ Стр.426 , Стр.427 , Стр.428 , Стр.429 , Стр.430 ]
Что такое полимер? | Живая наука
Полимеры — это материалы, состоящие из длинных повторяющихся цепочек молекул. Материалы обладают уникальными свойствами в зависимости от типа связываемых молекул и того, как они связаны. Некоторые полимеры сгибаются и растягиваются, например резина и полиэстер. Другие твердые и прочные, например, эпоксидные смолы и стекло.
Полимеры затрагивают практически все аспекты современной жизни.Скорее всего, большинство людей контактировали хотя бы с одним полимерсодержащим продуктом — от бутылок с водой до гаджетов и шин — за последние пять минут.
Термин «полимер» часто используется для описания пластмасс, которые являются синтетическими полимерами. Однако природные полимеры также существуют; каучук и дерево, например, являются натуральными полимерами, которые состоят из простого углеводорода, изопрена, согласно Британской энциклопедии. Белки — это природные полимеры, состоящие из аминокислот, а нуклеиновые кислоты (ДНК и РНК) — это полимеры нуклеотидов — сложных молекул, состоящих, например, из азотсодержащих оснований, сахаров и фосфорной кислоты.
Химические реакции
Герман Штаудингер, профессор органической химии Eidgenössische Technische Hochschule (Университет прикладных наук) в Цюрихе, является отцом разработки современных полимеров. Его исследования в 1920-х годах привели к современным манипуляциям как с натуральными, так и с синтетическими полимерами. По данным Американского химического общества (ACS), он придумал два термина, которые являются ключевыми для понимания полимеров: полимеризация и макромолекулы. Он был удостоен Нобелевской премии по химии в 1953 г. «за открытия в области химии макромолекул».«
Полимеризация — это метод создания синтетических полимеров путем объединения более мелких молекул, называемых мономерами, в цепочку, удерживаемую ковалентными связями, согласно ThoughtCo., Онлайн-образовательному ресурсу. Различные химические реакции, вызываемые теплом и давлением, для Пример — изменение химических связей, которые удерживают мономеры вместе, согласно сайту Scientific American. Этот процесс заставляет молекулы связываться в линейную, разветвленную или сетчатую структуру, в результате чего образуются полимеры.
Эти цепочки мономеров также называют макромолекулами. В основе большинства полимерных цепей лежит цепочка атомов углерода. По данным Учебного центра науки о полимерах, одна макромолекула может состоять из сотен тысяч мономеров.
Использование полимеров
Полимеры используются практически во всех сферах современной жизни. Пакеты для продуктов, бутылки с газировкой и водой, текстильные волокна, телефоны, компьютеры, упаковка для пищевых продуктов, автозапчасти и игрушки содержат полимеры.
Еще более сложная технология использует полимеры.Например, «мембраны для опреснения воды, носители, используемые для контролируемого высвобождения лекарств, и биополимеры для тканевой инженерии — все используют полимеры», согласно ACS.
Популярные полимеры для производства включают полиэтилен и полипропилен. Их молекулы могут состоять из 10 000–200 000 мономеров.
Во время реакции полимеризации большое количество мономеров соединяется ковалентными связями с образованием единой длинной молекулы, полимера. (Изображение предоставлено: LibreTexts)Будущее полимеров
Исследователи экспериментируют со многими различными типами полимеров с целью дальнейшего развития медицины и улучшения продуктов, которые мы уже используем.
Например, углеродные полимеры разрабатываются и улучшаются для автомобильной промышленности.
«Композиты из полимера, армированного углеродным волокном (CFRP), также называемые ламинатами из углеродного волокна, — это материалы следующего поколения, которые делают автомобили более легкими, более экономичными и безопасными», — говорится в колонке Live Science 2016 года Никхила Гупты. доцент, и Стивен Зельтманн, студент-исследователь, оба в лаборатории композитных материалов и механики факультета механической и аэрокосмической техники инженерной школы Тандон Нью-Йоркского университета.«Углеродный ламинат чрезвычайно прочный и жесткий из-за его тканых слоев из почти чистых углеродных волокон, скрепленных между собой затвердевшим пластиком, таким как эпоксидная смола». [Углеродное волокно: это больше, чем скорость]
Полимеры также используются для улучшения голограмм. Согласно исследованию, опубликованному в начале 2017 года в журнале Nano Letters, ученые из Пенсильванского университета создали голограмму на гибком полимерном материале под названием PDMA, в который были залиты золотые наностержни.Это новое голографическое устройство может содержать несколько изображений вместо одного.
«Мы задали вопрос:« Можем ли мы закодировать несколько битов информации в голограмме? »», — сказал Live Science Ритеш Агарвал, руководитель исследований и профессор материаловедения и инженерии Университета Пенсильвании. «Это важная работа, потому что это первый раз, когда кому-то показали, что вы можете записать несколько голографических изображений, и, просто растягивая полимер, вы можете в основном изменить изображение.»
Искусственная кожа из силиконового полимера может стать будущим антивозрастных усилий. В виде двух кремов полимер может подтягивать кожу человека, уменьшать появление морщин и уменьшать мешки под глазами, согласно исследованию, опубликованному в мае 2016 года в журнале Nature Materials. Такая искусственная кожа может также использоваться для помощи людям с кожными заболеваниями, такими как экзема, или использоваться в качестве солнцезащитного крема.
«Мы в восторге от этого; это совершенно новый материал », — сказал Live Science соавтор исследования Роберт Лангер, профессор Массачусетского технологического института.
Дополнительные ресурсы
Frontiers | Влияние свойств рисовой шелухи и древесной биомассы на производство нитей для моделирования наплавленного осаждения
Введение
Популярность включения лигноцеллюлозных биомасс в термопластические полимеры значительно возросла благодаря их преимуществам в устойчивости, низкой плотности, тепло- и шумоизоляции, а также характеристикам жесткости (Le Guen and Newman, 2007; Müssig, 2010; Gallos et al., 2017; Lammi et al., 2018). Свойства композитов связаны с (а) количеством включенной биомассы и (б) взаимодействиями между полимерной матрицей и лигноцеллюлозными частицами с точки зрения физических (например, площадь поверхности, соотношение сторон) и химических взаимодействий (например, интерфейс совместимость). Среди доступного лигноцеллюлозного сырья рисовая шелуха представляет особый интерес из-за ее нынешнего изобилия (т.е., по оценкам, от 128 до 148 миллионов тонн неиспользованных отходов) (Giddel and Jivan, 2007; Pode, 2016), а также химического состава.Он состоит примерно из 80–85 мас.% Лигноцеллюлозных материалов (например, целлюлозы, гемицеллюлозы, лигнина), 15–20 мас.% Аморфного кремнезема и 1,1–2,5 мас.% Белков (Juliano et al., 1987; Vadiveloo et al., 2009; Ummah et al., 2015). В предыдущих исследованиях сообщалось о его потенциальном применении в композитных структурах (Kumar et al., 2012), в качестве сырья для получения энергии (Chungsangunsit, 2009) или в качестве сырья для аморфного кремнезема (Yalçin and Sevinç, 2001). Параллельно сообщалось, что включение нанокремнезема в полимолочную кислоту (PLA) улучшает термическую стабильность и механические свойства композитов (Lv et al., 2016).
3D-печать (3DP) или аддитивное производство — это новая технология, которая позволяет создавать инновационные конструкции и комбинировать материалы, которые ранее было невозможно или непрактично производить. Включение наполнителей в 3DP продемонстрировало, что физические характеристики наполнителя могут быть перенесены на 3D-печатный объект (Montalvo Navarrete et al., 2018; Zeidler et al., 2018). Эти привлекательные свойства были продемонстрированы древесиной (Mirko et al., 2016; Tao et al., 2017), глины (Revelo, Colorado, 2018), металлов (Gibson et al., 2018) и ракушек (Graichen et al., 2017; Singamneni et al., 2018a; Zeidler et al., 2018).
Комбинация (а) свойств, присущих наполненным полимером компаундов, и (б) контроля направленности процесса 3D-печати, приводит к появлению новых функциональных возможностей для печатных объектов (Liles et al., 2018; Wang et al., 2018) . Примеры таких функциональных возможностей лигноцеллюлозного сырья включают гидроморфные свойства (Le Duigou et al., 2016; Sydney Gladman et al., 2016), электропроводности (Shao et al., 2018) и демпфирования колебаний (Zeidler et al., 2018).
В настоящем исследовании влияние порошка рисовой шелухи, интегрированного в матрицу PLA, исследуется для приложений 3DP моделирования методом наплавленного осаждения (FDM) и сравнивается с 3D-принтами из древесной муки PLA. Наблюдается и количественно оценивается влияние двух биомасс в процессе экструзионного компаундирования и на механические свойства трехмерных печатных прямоугольных параллелепипедов.
Материалы и методы
Биомассы и полимеры
шелухи риса Кармарг ( Oryza ) были поставлены из Silo des Tourelles — C omptoir Agricole du Languedoc (Aigues Mortes, Франция). Шелуху сначала просеивали с помощью сита 0,8 мм с помощью вибрационного сита 400 (Ritec, Франция) для удаления почвенной пыли и камней. Затем шелуху измельчали в шаровой вибрационной мельнице модели DM-1 (Sweco ® , США), состоящей из камеры измельчения из стойкого к истиранию эластомера объемом 36 л, заполненной керамическими цилиндрами на 25 кг (диаметр и длина 13 мкм).5 мм) и 25 кг керамических шаров (диаметр 13,5 мм). Движение камеры контролировалось вибрирующим механизмом, состоящим из пружин из высокопрочной стали. Один килограмм рисовой шелухи помещали в камеру и измельчали в течение 10 часов для получения тонкого порошка рисовой шелухи. Измельченный порошок сушили в печи при 60 ° C в течение 12 часов и хранили в вакуумных упаковочных пакетах из алюминиевой фольги перед использованием.
Древесная мука ( Pinus radiata D. Don) поставлялась фанерным заводом (Картер Холт Харви, Кинлит Милл, Токороа, Новая Зеландия).Только частицы размером менее 125 мкм использовали после разделения с использованием моторизованного ситового встряхивателя 43305 F (Humboldt, США) и сита 125 мкм (Endercotts, UK). Перед экструзией порошок древесной муки сушили при 100 ° C в течение не менее 24 часов.
PLA 3001D получали от Nature Works (США) и сушили в течение ночи перед экструзией. Перед экструзией соединения PLA и PLA сушили не менее 4 ч при 55 ° C.
Обработка
Компаундирование
Нити были изготовлены в два последовательных этапа: (а) смешивание полимера и биомассы до 10 мас.% в гранулы и (б) экструзия нити для FDM. Обе стадии были выполнены на 26-миллиметровом двухшнековом экструдере, вращающемся в одном направлении, LTE26-40 (Labtech Engineering Ltd, Таиланд), который имел отношение L / D 40 и был снабжен вакуумным зажимом. На этапе (а) материалы вручную смешивали в пластиковых пакетах и подавали в объемный питатель. Скорость питателя была установлена на 20 об / мин. Скорость шнека экструдера была установлена на 200 об / мин. Температура была установлена на 190 ° C в первых 5 зонах и 200 ° C в последних 5 зонах.Гранулы были нарезаны примерно до 2 мм в длину. На этапе (b) настройки двухшнекового экструдера были изменены (таблица 1), а гранулятор был заменен на намоточный блок, настроенный для получения нити диаметром 1,75 мм.
Таблица 1 . Настройки экструзии для этапа (b) для производства волокон FDM.
3D-печать
Объекты были напечатаны на принтере для моделирования наплавлением M2 (Makergear, США) с соплом 0,75 мм. Температура платформы была установлена на уровне 70 ° C, а температура сопла — 210 ° C.Прямоугольные балки (60 × 10 × 2,5 мм) для испытаний на изгиб были напечатаны с использованием программного обеспечения для резки (Simplify 3D ® , США) исходя из толщины слоев 0,2 мм и отсутствия перекрытия прядей. Направление 3D-печати было выполнено при 0 ° или 90 ° длины луча.
Характеристика биомассы
Физическая характеристика
Распределение частиц по размерам
Гранулометрический состав опасного порошка лузги и порошка древесной муки измеряли с помощью лазерного дифракционного анализатора размера частиц Hydro 2000S (Malvern Instruments Ltd., Великобритания) с раствором дистиллированная вода / этиловый спирт (50:50 по объему), чтобы обеспечить хорошее диспергирование порошка и избежать набухания. Результаты выражены с использованием метода Ми с показателем преломления 1,53, что соответствует показателям частиц опилок (Malvern, 2007). Результаты генерируются по объему, исходя из предположения, что частицы имеют сферическую форму. Для каждой биомассы было выполнено пять повторов, и указано среднее среднее распределение.
Сканирующая электронная микроскопия (СЭМ)
Рисовую шелуху и древесные порошки получали с помощью сканирующего электронного микроскопа Phenom Pro-X (Phenom, Франция) с использованием держателя образца для снижения заряда и ускоряющего напряжения 5 кВ (древесный порошок) и 10 кВ (порошок рисовой шелухи) соответственно.
Насыпная плотность и кажущаяся плотность
Кажущуюся плотность и плотность после утряски измеряли в двух экземплярах с использованием стандартного анализатора утряски (Autotap, Quantachrome instrument ® , США). Эксперимент состоял из заполнения градуированной пробирки 200 мл порошка и подачи ее на 1500 нажатий. Кажущуюся плотность и плотность утряски рассчитывали как отношение массы порошка к начальному и конечному объему соответственно.
Химическая характеристика
Измерения pH
Один грамм порошка биомассы размешивали в 15 мл дистиллированной воды при комнатной температуре.Четыре измерения pH в течение 4 часов регистрировали с помощью ph-метра (Mettler Toledo, США). Затем четыре измерения были усреднены.
Спектроскопия твердотельного ядерного магнитного резонанса (ЯМР)
Solid State CP-MAS (Cross Polarization-Magic Angle Spinning) 13 C Спектры ядерного магнитного резонанса были получены при 50,3 МГц на спектрометре Bruker Avance III 200 (Bruker BioSpin, Германия), оснащенном 4-миллиметровым твердотельным MAS-зондом ( Bruker BioSpin, Швейцария). Образцы упаковывались в ротор диаметром 4 мм и вращались с частотой 5 кГц.Каждые 3 мкс после импульса подготовки протона под углом 90 ° следовало время контакта 1 мс и время сбора данных 30 мс, с разделением протонов и задержкой рециркуляции 1,5 с. Все спектры были откалиброваны таким образом, что внутреннему пику C4 целлюлозы Iβ было присвоено значение 89,3 ppm относительно тетраметилсилана (Newman et al., 1993).
Зольность
Около 2 г порошка сначала сушили в печи при 130 ° C в течение 90 минут и взвешивали для определения сухой массы (m s ). Затем образец нагревали при 900 ° C в течение 2 часов и повторно взвешивали (m r ) после охлаждения в эксикаторе до комнатной температуры.Зольность рассчитывалась по:
. Зола = 100 · мр / мс (1)Где:
Ясень в процентах,
м с — навеска сухая масса в граммах,
м r — остаточная масса образца в граммах.
Эксперименты проводили в трех экземплярах и усредняли.
Химический состав
Содержание углеводов и лигнина в биомассах измеряли после концентрированного кислотного гидролиза. Содержание лигнина в образцах определяли по методу Класона.Вкратце, 100 мг высушенных образцов обрабатывали 72% об. / Об. H 2 SO 4 при температуре окружающей среды в течение 2 часов. Растворы разбавляли водой до 12% об. / Об. H 2 SO 4 и автоклавировали при 100 ° C в течение 3 часов. Гидролизаты фильтровали (10 мкм) и определяли содержание лигнина Класона как массу остатка после сушки при 105 ° C в течение 24 часов. Мономерные сахара глюкозу, ксилозу и арабинозу определяли с помощью жидкостной хроматографии высокого давления (ВЭЖХ).Для анализа использовали систему Waters с использованием колонки BioRad HPX-87H при 40 ° C и 0,3 мл / мин. Все анализы были выполнены в трех экземплярах.
Характеристика соединений биомассы
Реология
Комплексную вязкость чистого PLA и соединений измеряли на реометре AR 2000 (TA instruments, США). Эксперименты регистрировали в трех экземплярах с разверткой по частоте от 100 до 1 Гц при 200 ° C и деформации 1%. Линейная вязкоупругая область определялась при 1 Гц.
Молекулярный вес
Эксперименты по гель-проникающей хроматографии (ГПХ)проводили с использованием набора гелевых колонок с сополимером стирола и дивинилбензола (SDVB), состоящего из 2 аналитических колонок (SDV Lux Lin M; 5 мкм; 300 × 8 мм; PSS Polymer Standards Service GmbH, Германия. ) и преколонку (аналитическая преколонка SDV, 5 мкм; 50 × 8 мм; PSS Polymer Standards Service GmbH, Германия). Скорость потока была установлена на 1 мл / мин, систему кондиционировали до 30 ° C и использовали объем впрыска 100 мкл.Образцы готовили в трех экземплярах путем растворения от 6 до 8 мг образца в хлороформе до концентрации 2,0 мг / мл в течение ночи. Растворы фильтровали через фильтр из ПТФЭ 0,45 мкм. Калибровку прибора (Knauer, Германия) проводили с использованием 12 стандартов полистирола (стандарты ReadyCal Polystyrene; PSS Polymer Standards Service GmbH, Германия) в диапазоне от 370 до 2 520 000 г / моль. Обычная калибровочная кривая была построена путем измерения объема элюирования стандартов и построения его графика в зависимости от логарифма молярной массы.Данные калибровки были подобраны с помощью полиномиальной функции четвертого порядка ( r 2 = 1,00). Среднечисловую молекулярную массу (Mn), средневзвешенную молекулярную массу (Mw) и индекс полидисперсности (PDI) рассчитывали на основе отклика детектора с использованием программного обеспечения WinGPC UniChrom (PSS Polymer Standards Service GmbH, Германия).
Динамические и квазистатические механические испытания
Образцы для динамического механического термического анализа (DMTA) и механического анализа в режиме изгиба были испытаны в режиме трехточечного изгиба на RSA-G2 DMTA (TA instruments, США) с интервалом 40 мм.Образцы кондиционировали в течение 48 часов при 23 ° C (± 2 ° C) и относительной влажности 50% (± 5%).
Динамическое испытание проводилось от 23 до 80 ° C со скоростью 5 ° C / мин. Применяли колебания деформации 0,1% с частотой 1 Гц. Модуль накопления (E ‘) и тангенс угла δ записывали на протяжении всего испытания. Каждый состав и направление печати тестировали в трех экземплярах.
Испытание на изгиб проводили на универсальной испытательной машине Instron 5566 (Instron, США), оснащенной датчиком нагрузки 10 кН со скоростью 2 мм / мин.Модуль упругости при изгибе, прочность и деформация регистрировались на протяжении всего испытания. Было протестировано не менее 5 образцов для каждого состава.
Результаты
Характеристика частиц биомассы
Частицы древесного порошка были больше, чем частицы рисовой шелухи, со средним размером 209,9 мкм для древесного порошка и 28,1 мкм для порошка рисовой шелухи (Таблица 2). Оба порошка имеют широкое распространение с аналогичным SPAN около 3,3. SPAN выражает ширину распределения (D90-D10 / D50).Порошок рисовой шелухи содержит значительную долю мелких частиц размером менее 20 мкм, тогда как древесный порошок имеет высокое содержание крупных частиц (более 400 мкм), что видно на форме графика распределения частиц по размерам (рис. 1). В результате удельная поверхность, рассчитанная из гранулометрического состава, для порошка из рисовой шелухи примерно в 9 раз выше, чем для древесного порошка. Однако распределение частиц по размерам следует интерпретировать с осторожностью, поскольку расчеты модели лазерной дифракции предполагают сферические однородные частицы (Bohren and Huffman, 1983).
Таблица 2 . Физические характеристики порошков из древесины и рисовой шелухи, включая показатели гранулометрического состава, удельную поверхность и плотность (D10: 10-й процентиль, D50: средний размер, D90: 90-й процентиль).
Рисунок 1 . Гранулометрический состав древесного порошка (пунктирная линия) и порошка рисовой шелухи (пунктирная линия).
При изучении микроморфологии биомассы с помощью СЭМ в древесной муке видны крупные волокнистые структуры длиной> 125 мкм в отличие от частиц рисовой шелухи с низким соотношением сторон, которые подтверждают измерения лазерной дифракции (Рисунок 2) .Наличие частиц такого размера, несмотря на этап просеивания, объясняется их высоким соотношением сторон, которое позволяет им проходить через сетку. Размер и морфологические различия способствуют объяснению более низкой кажущейся плотности древесной биомассы за счет меньшей эффективности упаковки.
Рисунок 2 . СЭМ-изображения древесного порошка (а) и порошка рисовой шелухи (б) .
С точки зрения химического состава, определенного с помощью ВЭЖХ, две биомассы согласуются с литературными данными для лигноцеллюлозного сырья (таблица 3) (Müssig, 2010).Основные различия между порошками заключаются в (а) более высоком содержании лигнина в древесном порошке и (б) более высоком содержании золы в порошке рисовой шелухи (т.е. 15,7 мас.% По сравнению с 0,16 мас.% Для древесины). Более высокое содержание золы в рисовой шелухе объясняется присутствием кремнезема и вносит свой вклад в пятикратную разницу в плотности утряски (таблица 3) (Hamdan et al., 1997). Отсутствие 100% баланса массы объяснялось присутствием водорастворимых экстрактивных веществ. Было обнаружено, что они присутствуют в более высоких количествах в древесном порошке, чем в порошке рисовой шелухи.
Таблица 3 . Химический состав в процентах от массы биомассы.
Химический состав порошков, определенный с помощью твердотельного ЯМР 13 C, соответствовал лигноцеллюлозной биомассе. Основные пики, наблюдаемые в древесном порошке, были приписаны целлюлозе (C1-C6), метоксилу лигнина (56 частей на миллион) и ароматическим / фенольным группам, с незначительным вкладом гемицеллюлозы (рис. 3A) (Gil and Neto, 1999). Порошок рисовой шелухи показал аналогичные сигналы с добавлением пиков, относящихся к амидным карбонилам (~ 175 м.д.), и сигналы преимущественно от боковых цепей аминокислот C β / C γ (C γ 15-25 м.д. и C β 25-35 м.д.), перекрывающиеся с сигналами от ацетилированных гемицеллюлоз (рис. 3В) (Bruker BioSpin, 2018).Аминокислотные сигналы были отнесены к известному содержанию белка, присутствующему в рисовой шелухе (Juliano et al., 1987; Vadiveloo et al., 2009).
Рисунок 3 . Твердотельный ЯМР древесного порошка (A) и порошка рисовой шелухи (B) . Р, белок; H — гемицеллюлозы; L, лигнин; С, целлюлоза. Верхний левый спектр представляет собой увеличение в диапазоне 10–40 ppm.
Стабильность процесса экструзии
На стадии компаундирования давление в фильере для порошка из древесной и рисовой шелухи значительно различается.Он составлял от 68 до 73 полосок и от 22 до 24 полосок для соединений из древесины и рисовой шелухи соответственно. Во время компаундирования рисовой шелухи наблюдались низкое давление в фильере, значительный скачок давления в фильере и изменение цвета. Различия в обработке первоначально приписывались изменению кажущейся плотности и размера частиц, однако не учитывались различия в цвете. Известно, что смешивание биомассы лигноцеллюлозы с полимером может окислять углеводы, содержащиеся в биомассе, и приводить к потемнению соединений в зависимости от условий обработки (т.е.е., высокий сдвиг, высокая температура) (Muniyasamy, 2013; Gallos et al., 2017). Тем не менее, различия в цвете между сырым сырьем и соединениями были более интенсивными для рисового компаунда PLA, чем у древесины PLA, и усиливались в нити FDM (рис. 4). Известно, что шаровая мельница лигноцеллюлозной биомассы в течение длительного периода (т.е.> 120 мин) увеличивает площадь поверхности, снижает кристалличность целлюлозы и снижает степень полимеризации углеводов, что, следовательно, увеличивает реакционную способность поверхности частиц (Vaidya et al., 2016; Gao et al., 2017). Эта реакционная способность может объяснить разницу в окраске, вызванную химическими реакциями, запускаемыми рисовой шелухой по сравнению с древесным порошком.
Рисунок 4 . Фотографии волокон FDM из древесной муки (вверху) и рисовой шелухи (внизу).
Во время производства филамента FDM филамент из рисовой шелухи FDM показывал более низкую прочность расплава, и материал выбивался из фильеры, вызывая неравномерность формы нити. Эти эффекты обработки затрудняли производство волокна из рисовой шелухи.
Влияние биомассы на PLA
С точки зрения реологии, измерение комплексной вязкости PLA и соединений PLA / биомассы в зависимости от частоты показало, что (a) соединение PLA-древесина имеет более высокую вязкость, чем чистый PLA, и что (b) оба демонстрируют поведение при истончении сдвига (рис. 5). Полученные данные согласуются с литературными данными о полимерах, наполненных биомассой, и об общем влиянии биомассы в расплаве полимеров (Li and Wolcott, 2004; Bettini et al., 2013; Gallos et al., 2017; Chun et al., 2018). Напротив, рисовое соединение имело половину комплексной вязкости чистого PLA и показало плохую воспроизводимость (рис. 5). Было высказано предположение, что частицы рисовой шелухи действуют как твердый смазочный материал в полимерной матрице. Однако отсутствие воспроизводимости также предполагает дополнительные эффекты, такие как гидролиз полимера основной цепи.
Рисунок 5 . Комплексная вязкость как функция частоты для: PLA (квадрат), PLA-дерева (круг) и PLA-риса (треугольник).Были проведены трехкратные измерения, и все результаты представлены на графике.
При сравнении Mn и Mw PLA соединений биомассы, анализ GPC показал отсутствие существенной разницы между двумя наполнителями (Таблица 4). Более конкретно, анализ GPC дал Mw и Mn 98 020 г / моль и 52 473 г / моль для чистого PLA. После экструзии с порошками биомассы были зарегистрированы значительно более низкие средние молекулярные массы, т. Е. Mw = 66 790 г / моль и Mn = 33 780 г / моль для PLA-древесины и Mw = 59 853 г / моль и Mn = 31 463 для PLA-риса (Таблица 4, рисунок 6).Этот результат согласуется с литературными данными, поскольку известно, что PLA гидролизуется в присутствии влаги или кислотных групп в биомассе во время экструзии (Le Guen et al., 2017; Thumm et al., 2018). Это привело к уменьшению средней молекулярной массы на 32–39% для PLA, смешанного с порошками из древесной и рисовой шелухи. Существенной разницы между наполнителями не наблюдалось. Снижение также наблюдалось в профилях молекулярно-массового распределения (MWD) (таблица 4). Точно так же не наблюдали значительных изменений индексов полидисперсности (PDI) чистого PLA по сравнению с PLA с биомассами (таблица 4).
Таблица 4 . Значения молекулярной массы и индексы полидисперсности PLA в чистом виде и в смеси с биомассами.
Рисунок 6 . Профили молекулярно-массового распределения чистых соединений PLA (сплошная линия), PLA-древесина (пунктирная линия) и PLA-рис (пунктирная линия).
При сравнении воздействия наполнителей на PLA, анализ GPC показал, что оба результата приводят к аналогичному уровню гидролиза PLA, следовательно, различие реологических характеристик нельзя отнести к разнице в Mn / Mw.
Механические характеристики 3D-отпечатков при 0 ° и 90 °
Заполнение направления печати выполнялось под 0 ° и 90 ° длины прямоугольной балки (рис. 7). Направление печати влияло на механические свойства всех составов, показывая снижение модуля упругости при изгибе и прочности для напечатанных балок под углом 90 ° (рис. 8). Анизотропия вызывала различие в свойствах между продольным и поперечным направлением печати, которое составляло от 28 до 41% изменения прочности на изгиб, от 4 до 15% по деформации и от 27 до 33% по модулю.Аналогичные результаты по механическим свойствам были получены для прямоугольной деревянной балки из PLA, напечатанной на 3D-принтере, где направление печати (то есть 0 ° и 90 ° продольной оси балки) влияло на жесткость на растяжение и прочность на 20 и 35% соответственно (Le Duigou et al. др., 2016). Они предположили, что различия в механических свойствах между продольным и поперечным направлениями печати были вызваны отсутствием межслойного взаимодействия.
Рисунок 7 . Типичные прямоугольные балки, напечатанные на 3D-принтере, для испытаний на изгиб.Снизу вверх PLA 0 °, PLA 90 °, PLA-рис 0 °, PLA-рис 90 °, PLA-дерево 0 ° и PLA-дерево 90 °.
Рисунок 8 . Сравнение механических свойств напечатанных на 3D-принтере балок PLA, ( верхняя часть ) модуль упругости при изгибе ( средняя ) прочность на изгиб и ( нижняя ) деформация изгиба (полосы ошибок указывают доверительный интервал ± 95%).
Не было обнаружено значительных различий между древесиной и наполнителями из рисовой шелухи с точки зрения механических свойств, за исключением жесткости на изгиб в продольном направлении, где модуль упругости образца древесины PLA на ~ 25% выше, чем модуль PLA-
.