Производство топливных пеллет — техника и технология
Последнее десятилетиевсё большее значение на мировом топливном рынке придают древесным гранулам — пеллетам. Они — наиболее распространенный тип гранулированного топлива и, как правило, сделаны из отходов деревопереработки – опилки, стружка, горбыль, обрезки. В общем, гранулы, как новый и прогрессивный вид топлива, широко используются во многих странах за счет их явных преимуществ:
- Разнообразие сырья
В прошлом как классическое топливо всегда рассматривалась цельная древесина . По сравнению с цельной древесиной, древесные гранулы могут быть изготовлены из любых органических материалов, таких как солома, опилки, травы… - Экологическая эффективность
После производства гранулы имеют низкую влажность и высокую плотность. Это гарантирует, что при их сжигании будет выброшено меньше углекислого газа в атмосферу.. То есть, гранулы производят меньше золы и меньше дыма. - Низкая себестоимость
При сравнении со многими видами топлива древесные гранулы немного дороже, чем обычное дерево, опилки и т.п., ведь они требуют производственного процесса Однако, если сравнивать с другими видами топлива, такими как нефть, природный газ и т.д., то они оказываются намного дешевле, а если учесть доступность сырья в виде отходов на лесопильном и лесоперерабатывающем производстве, то экономическая эффектичность пеллет очевидна.
Таблица 1. Сравнение стандартных видов топлива | |
Одна тонна пеллет равняется: | |
455 литрам мазута | 0,45 м³ природного газа |
644 литрам пропана | 4,775 КВт/ч электроэнергии |
Производственный цикл в малом бизнесе и домашнем хозяйстве
Маленькие грануляторы чаще всего используются при производстве топливных брикетов из биомассы. На рынке такие грануляторы называют грануляторами с плоской матрицей. Они используются для домашнего хозяйства, собственных нужд и малого бизнеса. Например, в отопительной системе собственного жилья вы можете использовать свои собственные древесные гранулы, модернизировав имеющийся или приобретя новый котел. Кроме того, для того, можно гранулировать корма для различных животных.
Производственный процесс включает в себя 3 этапа:
Первый этап: Подготовка сырья
Сырье может быть различным, например, древесные отходы (опилки, древесная стружка и т.д.), отходы сельскохозяйственного производства (солома, кукурузные стебли, лузга и т.д.), органические остатки (трава, листья и т.д.), и другие биомассы.
Размер сырья перед загрузкой в гранулятор не должен превышать 5 мм, так что, для уменьшения размеров до минимальных, сырье нужно пропустить через молотковую дробилку. Молотковые дробилки могут работать на высоких скоростях — от 3000 об/мин до 8000 об/мин. Размер на выходе контролируется за счет отверстий сит, которые могут быть от 1 мм до 10 мм. Молотковые дробилки очень популярны для измельчения сырья при производстве пеллет, т.к. благодаря большому ассортименту сит могут использоваться практически для любого сырья.
Второй этап: Гранулирование
Высушенное сырье направляется в прессующий узел гранулятора, где роликом создается высокое давление. В общих чертах, самыми распространенным являются D-тип (тип с вращающейся матрицей) и R-тип (тип с вращающимися роликами). В грануляторах используются различные виды привода — электродвигатели, дизельные двигатели, бензиновые двигатели, вал отбора мощности.
Третий этап: Упаковка
По окончанию процесса древесные гранулы пакуют в пластиковые пакеты для защиты от влажности и удобства транспортировки.
Стандартный производственный процесс в больших грануляторах
В промышленном производстве используются пеллетные заводы и линии для производства пеллет.
Производственный процесс включает в себя 8 этапов:
Первый этап: Первичное измельчение древесины
Перед началом производства сырье должно быть предварительно обработано. Первичное измельчение является важным моментом в процессе гранулирования, т.к. оно может стать ограничивающим фактором в производстве пеллет, а также является самым затратным этапом всего процесса. Для предварительной обработки сырья используются дробилки для древесных отходов – щепорезы, валковые дробилки. По завершению дробления фракция должна быть подходящих размеров – 6-25 мм
Второй этап: Сушка
Перед загрузкой в грануляторы сырье должно быть тщательно высушено (5-20% в зависимости от фракции и типа сырья). Стандартным оборудованием в линии является барабанная сушилка – максимально простое в обслуживании и обращении оборудование с неплохим КПД за невысокую цену. Альтернативным выбором является аэродинамическая сушилка – намного более эффективная и компактная.
Третий этап: Очистка от примесей
В целях обеспечения качества гранул, сырье должно быть очищено от примесей, таких как металлы, камни или другие. Крупные камни и другие материалы убираются в ручную или с помощью камнеуловителей. От металлов сырье очищают с помощью магнита на конвейерной ленте или металлоуловителя.
Четвертый этап: Вторичное измельчение
Пятый этап: Гранулирование
На данном этапе сырье формируется в пеллеты. Через фильеры матрицы гранулятора под высоким давлением опилки прессуются в древесные гранулы. На выходе гранулы горячие и относительно мягкие.
Шестой этап: Охлаждение
Охлаждение является важной частью процесса производства качественных древесных гранул. Оно необходимо для отвердения готовых пеллет — они горячие и пластичные, легкодеформируемые до полного остывания.
Седьмой этап: Контроль продукции
На данном этапе сформированные и охлажденные гранулы проверяются на наличие превышающих требуемый размер пеллет. Тщательность проверки зависит от условий местного рынка и индивидуальных особенностей производства.
По завершению процесса производства для обеспечения удобства использования, транспортировки и привлекательного внешнего вида, гранулы расфасовываются по пластиковым пакетам, так гранулы менее подвержены истиранию во время доставки.
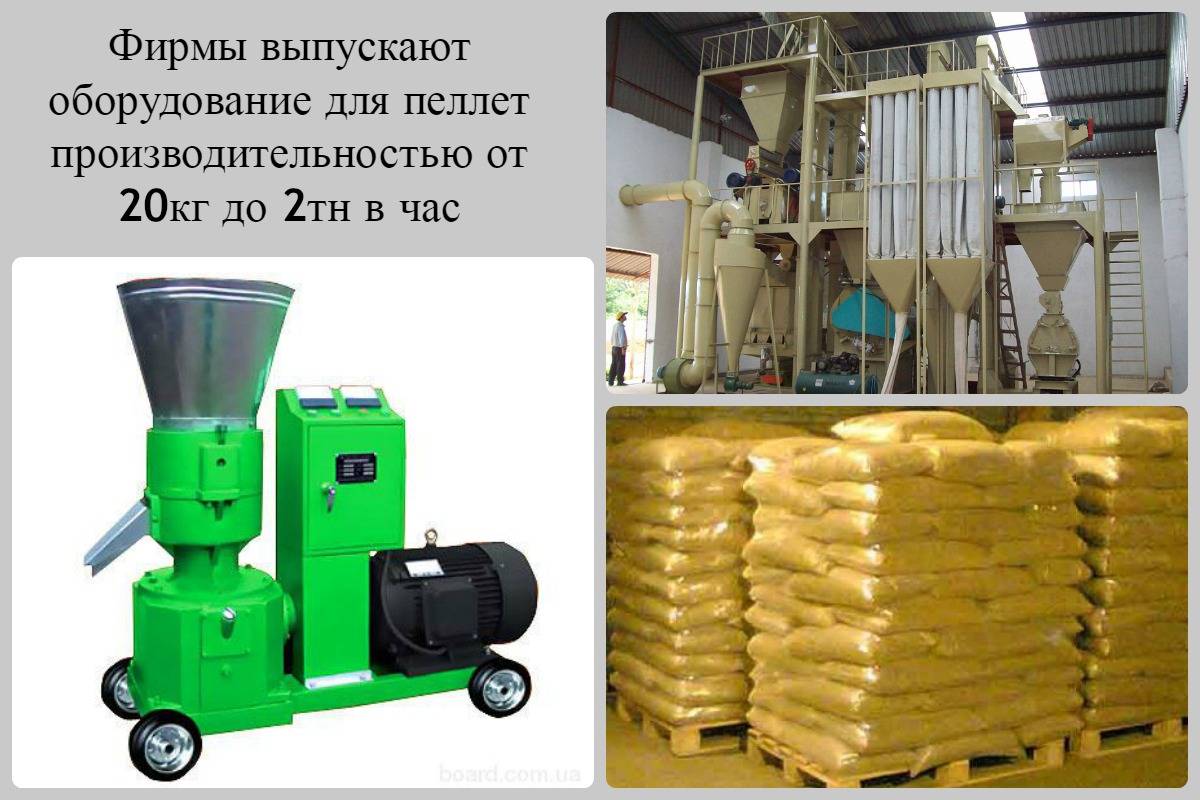
Линия для производства древесных гранул.
Глобальный спрос на древесные топливные гранулы
Благодаря исследованиям последних лет стало понятно, что рынок древесных гранул перспективен и набирает оборот. Более того, древесные гранулы более безопасны для окружающей среды, чем традиционные виды топлива, поскольку могут быть изготовлены из отходов. Это является важным элементом защиты окружающей среды. К тому же, древесные гранулы, как новый вид топлива, могут повысить КПД использования топлива. Не имеет значения для домашнего использования или для коммерческого, древесные пеллеты, в любом случае, весьма перспективное направление.
Секреты производства пеллет — ТехноМашСтрой
Сегодня идет речь о полной и глубокой переработке древесины, и особенно актуальным является вопрос по утилизации отходов деревообработки. Мы считаем, что одной из самых наилучших технологий переработки древесных отходов является – производство пеллет. Вот несколько критериев по которым данная технология переработки отходов превосходит другие:
- Технология довольно проста.
- Для обслуживания работы оборудования необходимо минимальное количество персонала.
- Себестоимость производства довольно небольшая, а вот отдача от бизнеса высокая.<
- Возможность переработки отходов различных размеров. Но как мы уже знаем, чтобы эффективно работать, необходимо знать технологию производства продукции от А до Я. И здесь к технологии производства относится:
- Сырье, с его размерами и влажностью.
- Процесс работы оборудования и режимы работы.
- Качество получаемых пеллет.
- Правильная упаковка пеллет.
При этом в интернете имеется достаточно большое количество информации про оборудования различных фирм. Но вот как работать на таком оборудовании никто не говорит, какое сырье предпочтительнее, какие нормы расхода сырья, как увеличить ресурс работы линии.
Сырье для производства пеллет
Сырьем для пеллет является измельченная древесина размером около 1 мм толщиной и до 3-4 мм длиной. Преимуществом производства пеллет является тот факт, что здесь не требуется специально подготовленная стружка как к примеру для дсп. В сырье не допускается наличие минеральных примесей и металлических включений. Сырье для производства пеллет оказывает влияние на цвет готовых гранул:
- Черные пеллеты получают из древесины с наличием коры, и возможным наличием гнили несоблюдением технологии…
- Серые пеллеты получают из неокоренной древесины. На фото видно что пеллеты имеют включения коры. При уменьшении размера стружки включения могут быть и не видны, но пеллет будет иметь темноватый оттенок.
- Светлый пеллет получают из качественной окоренной древесины.
Светлый пеллет обладает большей теплоотдачей, меньше крошится и соответственно дороже стоит чем серые и черные гранулы.
Кроме цвета пеллет, от сырья зависит и качество склеивания пеллет. Дело в том что связующим веществом в процессе прессования пеллет является природный лигнин, который содержится в древесине. Но содержание лигнина в каждой породе разное, и соответственно чем больше лигнина содержится в древесине тем качественнее пеллет.
Еще одним важным технологическим фактором при производстве гранул является такой параметр древесины как твердость. Дело в том что чем жестче древесина, тем больший износ режущего инструмента, матрицы и пуансона пресса.
Как влияет сырье на получение пеллет
Сегодня рассмотрим сырье для пеллет получаемых из опилок. Мы знаем что опилки могут быть разными и различаться по породе, по размерам, по влажности… Также мы рассмотрим какие параметры и как влияют на производство пеллет и это особо важно как нам кажется при производстве пеллет своими руками, так как промышленное оборудование не столь чувствительно как небольшой станок с малой мощностью.
Влияние породы древесины на склеиваемость пеллет из опилок
Теперь переходим к основной теме этой статьи. Пеллеты могут производиться из разных пород древесины, я же хочу рассказать из какой древесины пеллеты будут получаться лучше, какая древесина подходит оптимально, в общем рассмотрим некоторые критерии сырья для пеллет…
Как всем известно связующим в производстве пеллет выступает лигнин из древесины. Так вот чем больше природного лигнина в древесине, тем проще получить качественные пеллеты из опилок. Итак нам необходима табличка на содержание лигнина в древесине:
Сосна–27,05%.
Ель–27,00%.
Пихта–29,89%.
Бук–27,72%.
Береза–19,10%.
Осина–21,67%.
В среднем в древесине хвойных пород лигнин содержится в пределах 26-30%, в лиственных породах 19-28 % от общей абсолютно сухой массы древесины. Ну и конечно чем ниже содержание лигнина, тем большее количество отсевов мы получаем, а это большие затраты электроэнергии и незначительные снижения производительности.
Влияние твердости дерева на получение пеллета
Еще одним интересным фактором в производстве пеллет является твердость древесины, чем тверже древесина, тем более сложно ее переработать в стружку, сложнее спрессовать в пеллет. Повышается расход электроэнергии, увеличиваются нагрузки и соответственно расход инструмента (ножи, матрица, ролики). Предлагаю вам сравнить твердость некоторых пород.древесины:
Сосна–260кГ/см2.
Ель–235кГ/см2.
Пихта–255кГ/см2.
Бук–555кГ/см2.
Береза–425кГ/см2.
Осина – 240 кГ/см2.
Опять же один кубометр пеллет из опилок более плотных пород будет обладать большей насыпной плотностью и большей теплотой сгорания. К примеру один кубометр пеллет из березы выделит больше тепла чем один кубометр пеллет из опилок сосны.
Работа линии по производству пеллет
Итак, прессование осуществляется за счет продавливания через матрицу мелких опилок. Опилки просыпаются на матрицу и затем вдавливаются в отверстия роликами катающимися по матрице. износ роликов пуансона и матрицы огромное влияние оказывает очень интересная технология запуска пресса
Пресс пеллет – подготовка к работе
В свое время когда я только начал изучать изготовление гранул, я и не думал что это производство именно с таким количеством нюансов, и технология производства пеллет так чувствительно к настройке пресса. Очень часто можно встретить такую ситуацию что пеллет не идет или вообще пресс для пеллет невозможно запустить, иначе говоря он запускается, но матрица сразу забивается. Но сначала про запуск пресса (при условии что матрица уже притерта).
Пресс для изготовления пеллет запускается в следующем порядке:
- Включатся основной двигатель вращения пуансона, стружка не подается
- Подается первичная смесь. Под первичной смесью мы понимаем состав масло и опилки.
Дело в том что для более мягкого запуска и остановки пресса, а также для увеличения работы матрицы, подается смесь пеллетов или опилок с маслом. Если остановить пресс пеллет с обычной стружкой без масла (в матрице опилки стандартной влажности без масла), то уплотненная стружка как бы прикипает к стенкам матрицы и потом при запуске необходимо очень большое усилие чтобы продавить эту стружку, при этом данного усилия во многих случаях как правило не хватает и пресс просто забивается, в это время идет повышенная нагрузка и соответственно повышенный износ двигателя и передающих механизмов пресса. Теперь более подробно про смесь, как вы понимаете ее функция более мягкий запуск пресса и меньший износ пресса. Специалисты производящие матрицы и пресса, рекомендуют смешивать опилки с чистым дизельным, автомобильным маслом, дабы снизить силу трения между смесью и стенками быстроизнашивающейся матрицы, и конечно же образовавшийся пеллет с маслом потом выкидывать, приготавливая новый раствор на новые остановки и запуски.
Народные умельцы или по другому наши русские специалисты приспособились вместо чистого и относительно дорогого масла смешивать стружку с дешевой отработкой от автомобилей, от редукторов или других механизмов, при этом получившийся пеллет с маслом после запуска, убирают до остановки и вместо новой смеси используют много много раз, засыпая данную смесь и на остановку пеллет, и на запуск, при необходимости добавляя в смесь немного отработанного масла. При этом засыпая первый раз стружку с маслом мы получаем пеллет с маслом, затем уже используем при запусках и остановках пеллет с маслом. Плюсом такого “усовершенствования” является значительная экономия на масле, минусом может служит более быстрый износ матрицы, так как отработка и еже с ней содержит большое количество металлических примесей.
- Ждем когда пойдет пеллет, при этом пеллет с маслом мы убираем или выкидываем (в зависимости от того будете ли вы использовать повторно данную смесь).
- После того как начал продавливаться пеллет через матрицу, включается минимальная подача стружки в пресс, при этом подача стружки с маслом прекращается.
Стружка убирается до тех пор пока не появится только пеллет без масла.
- После появления только чистых пеллет без масла скорость подачи опилок в пресс для изготовления пеллет увеличивается, пресс выводится на проектную мощность.
Почему забивается пресс для изготовления гранул
Если пеллет не идет, вы не смогли продавить матрицу, не стоит крутить и мучить пресс, необходимо останавливать всю систему и пробивать или просверливать отверстия матрицы.
Пресс для производства пеллет очень часто забивается опилками, предлагаю вам рассмотреть основные причины его забивания, когда через матрицу не продавливаются гранулы. Будем считать что все технологические параметры в норме:
- Давление пуансона на матрицу в норме
- Влажность стружки 12-15%
- Фракционный состав в норме
Это случается довольно часто, когда пресс для пеллет работал, работал и вдруг нагрузка на двигатель полезла, двигатель выбивает и весь пресс завален опилками. Оператор все очищает, подготавливает матрицу, запускает пресс и после двух трех часов все повторяется снова, пресс останавливается, оператор очищает, при этом все нормально, замечаний по технологии как бы нет. На самом деле когда начинают разбираться выявляются казалось бы незначительные причины, но именно они так негативно влияют на работу пресса:
- Если один из роликов немного болтается или подклинивает – пресс работать не будет
- Если давление пуансона хотя бы немного не стабильно, то есть случается так что по какой то причине (пропускает клапан) с пуансона уходит давление, в таком случае датчик может и не показывать сразу падение давления, так как в это время сила прижима пуансона уменьшается и на матрицу начинает накатываться слой опилок. Пуансон поднимается над матрицей и давление остается на прежнем уровне.
Немаловажную роль в оптимизации производства древесных гранул играет автоматизация и визуализация производственного процесса. Конечно же для контроля процесса в настоящее время просто необходимо каждую смену отслеживать какое количество отсева, после сортировки готового пеллета на сите, уходит в повторную переработку, какой коэффициент получается после работы каждой смены (для этого устанавливаются весы измеряющие массу подаваемой стружки на пресс). Необходимо видеть какие скорости пресса были в процессе смены. Очень полезно следить за временем остановки и запуска линии, количеством простоев за смену, стоит понимать что на производстве пеллет каждый запуск и остановка пресса это критические нагрузки и максимальные износы матрицы и роликов, поэтому их просто необходимо отслеживать и сводить к минимуму. Предлагаю вам ознакомиться с ориентировочными нормами расхода при производстве пеллет. При установке новой матрицы и новых роликов для изготовления высококачественных гранул требуется какое то время для притирки рабочих механизмов, поэтому часто на новых механизмах можно не получить желаемое качество. Также существует искусственный вариант выхода из строя матрицы и роликов – попадание твердых инородных частиц (камней, металла), на рабочих механизмах образуются впадины и прессование на данных участках не происходит.
Качественное прессование это когда гранулы выдавливаются из всей поверхности матрицы, а не частями. Выдавливание гранул только из некоторых частей матрицы говорит о том что пресс настроен неправильно, причин может быть множество это и выход из строя матрицы или роликов, колебания матрицы в посадочном месте, выход из строя подшипников на роликах и т.д..
Все качественные показатели гранул между собой взаимосвязаны. И как правило при несоблюдении каких то технологических параметров (влажность, давление, фракционный состав) сразу снижаются все качественные показатели окатышей (так ласково их называют в Европе).
Качество пеллет зависит от:
- Правильно выбранной влажности сырья (окатыши со стружки повышенной влажности будут иметь больший объем чем гранулы со стружки пониженной и средней влажности при одинаковой массе)
- От фракционного состава сырья (чем крупнее стружка тем труднее ее спрессовать, при этом готовый окатыш с крупной стружкой может рассыпаться из за восстановления формы спрессованной стружки)
- От породы сырья (хвойные пеллеты получаются более качественные чем из пород лиственной древесины)
- От износа матрицы и роликов (при износе стружка не прессуется а накатывается на матрицу)
- От правильно настроенных зазоров между роликами и матрицей.
- От диаметра прессуемых пеллет (чем меньше диаметр пеллет тем лучше качество пеллет при одинаковых условиях прессования)
ТЕХНОЛОГИЯ ПЕЛЛЕТ ДУМАЮ ТЕПЕРЬ МНОГИМ СТАЛА БОЛЕЕ ПОНЯТНА.
Особенности производства древесных пеллет! | Курский завод грануляторов
Какие пеллеты бывают и какое дополнительное оборудование требуется для производства древесных пеллет?
Производство топливных гранул (пеллет) из любых составов это технологический процесс требующий подготовки сырья (древесины), настройки оборудования и конечно же понимание физических и химических свойств конкретных гранулируемых составов.
- Белые пеллеты
- Серые пеллеты
- Агро пеллеты
Белые пеллеты: самые покупаемые и соответственно самые продаваемые, должны иметь зольность 0,30-0,35% эти пеллеты производят из чистой древесиной муки фракцией до 1мм и влажностью не более чем 20%, как правило без добавления различных связующих веществ которые могли бы повлиять на цвет и зольность. Цены на такие пеллеты выше в связи с особенностями их производства и необходимостью использовать дорогостоящие оборудование для подготовки сырья. Для производства данных пеллет используется только свеже измельченная древесина без содержания коры и камбия. Связующим веществом данных пеллет должен является исключительно “лигнин” который содержится в межклеточной структуре древесины который выделяется при распиле и дроблении древесины. Лежалый, прелый и разнородный опил не подходит для производства белых пеллет с зольностью до 0,35%. Так же для производства белых пеллет используют производственные линии содержащие в своей технологической цепочке дополнительное оборудование для подготовки сырья в том числе обязательно требуется “парогенератор” (зачем нужен парогенератор читайте в низу статьи). Дробилка древесины, сушильный комплекс, смесители и накопители входного сырья, а так же охладители и транспортеры готовых пеллет.
Серые пеллеты: их стоимость немного ниже, но они не менее популярны среди конечного потребителя хоть и имеют зольность 0,7-1%. Требование к сырью не такое жесткое как при производстве “белых пеллет”допускается добавление коры, камбия, листья и иголки деревьев так же возможно добавление отработанных индустриальных и растительных масел. Процесс производства серых пеллет для производителя дешевле так как не требует сортировки сырья и допускается использование лежалого и прелого опила который абсолютно не подходит для производства белых пеллет в этом их неоспоримый плюс для производителя. Производство серых пеллет так же требует подготовки сырья и обязательное наличие пара! Зачем пар читайте ниже↓
Агро пеллеты: их стоимость примерно такая же как и серых древесных пеллет но зольность может достигать 2% и более в зависимости от конкретного состава сырья. Сырьем для агро пеллет могут быть разные отходы аграрного производства это и лузга подсолнечника и различные отходы от производства злаковых, например солома. Так же агро пеллетами можно считать пеллеты в составе которых присутствует древесина, а в качестве связующих используется крахмалосодержащие, отличным связующим для агро пеллет является измельченные: сено, камыш, жмых подсолнечника и практически любые измельченные тростниковые или крахмало содержащие отходы.
Какое оборудование требуется для производства пеллет?
Как минимум для производства пеллет из чистой свеже измельченной древесины фракцией до 1мм и влажностью не более 20%. потребуется сам пеллетайзер (гранулятор) дозатор (питатель) и охладитель-просеиватель пеллет смотрите рис ↓
Шнековый дозатор требуется для стабильной равномерной подачи сырья в пеллетайзер, а так же для поддержания одинакового уровня опила в прессующем узле (дозатор это важный узел без которого невозможно производство пеллет!)
Гранулятор (пеллетайзер) “Сердце” линии производства пеллет: служит прессующим узлом формирующем сами пеллеты под высоким давлением сырье проходит через отверстия в “матрице” и за счет собственного связующего вещества древесины “лигнина” происходит “спайка” волокон, когда пеллета достигает определенной длинны происходит ее “обламывание” за счет специального механизма который позволяет отрегулировать нужную длину пеллет как правило 25-30 мм.
Охладитель просеиватель пеллет: выполняет не менее важную функцию и крайне необходим для производства любых пеллет, его задача просеять не за гранулированный остаток тем самым получить на выходе только чистую пеллету (без пыли), пеллета выходит горячая и если ее быстро не остудить останется лишняя влага которая не позволит долго храниться пеллетам тем более в герметичных мешках.
Это минимальный набор оборудования который требуется для производства любых пеллет только из подготовленного сырья!
Подготовка сырья (древесины) для производства пеллет:
Основополагающим в процессе производства пеллет из чистой древесины является наличие природного связующего “ЛИГНИН” это бесцветный иногда желтоватый полимер который скрепляет клетки древесины, лигнин высвобождается при распиле древесины, а так же является “клеем” для пеллет и смазкой для пеллетайзера, коварная особенность лигнина в том что он окисляется под действием кислорода содержащегося в воздухе и кристаллизуется, именно по этой причине лежалый даже несколько дней опил может быть не пригоден для производства пеллет в чистом виде, но есть выход: Использование генератора пара в технологической цепочки производства пеллет.
Опил фракцией не более чем 1 мм проходя через “паровую баню” в шнековом питале размягчается, закристаллизованный лигнин снова становится пластичным и вновь начинает обладать клеющими свойствами для этого требуется перегретый пар температурой выше 120 гр.(С)
Оборудование для производства пеллет из опилок: пеллетная линия, технология
Развитие рынка пеллет – достойной альтернативы традиционным видам топлива – началось в нашей стране относительно недавно. Увеличение на данном рынке числа потребителей, использующих данное топливо для работы твердотопливных котлов высокой мощности, применяемых для обогрева промышленных объектов и крупных жилых строений, привело к тому, что все большее количество компаний, работающих в различных сферах, задумывается над приобретением оборудования для производства пеллет. По прогнозам специалистов, спрос на пеллеты в России будет только расти. Прежде всего это относится к топливным гранулам из опилок.
Мини-линия для изготовления топливных гранул состоит из нескольких технологических участков
При организации пеллетного производства (впрочем, как и любого другого) следует в первую очередь изучить все его нюансы, а также познакомиться с оборудованием, которое применяется для его практической реализации.
Технологический процесс производства пеллетного топлива
Для того чтобы изготовить пеллеты из опилок, с исходным материалом необходимо совершить целый перечень технологических манипуляций, каждая из которых решает определенные задачи.
Технологический процесс производства пеллетов из опилок – это последовательность определенных действий, выполняемых при помощи соответствующего оборудования.
Такими действиями, в частности, являются:
- очистка опилочной массы от посторонних примесей;
- предварительное измельчение очищенного материала;
- сушка сырья для пеллет;
- финишное измельчение уже высушенных опилок;
- доведение уровня влажности подготовленного материала до требуемого значения;
- процесс гранулирования опилочной массы;
- охлаждение готовой продукции и ее упаковка.
Промышленная схема производства пеллет
Поскольку все вышеперечисленные этапы технологического процесса производства топливных гранул осуществляются с определенной целью и имеют большое значение для получения качественной продукции, на каждом из них следует остановиться более подробно.
Оценка качества исходного сырья
Основное влияние на качество пеллет оказывают характеристики сырья. Важными в данном случае являются такие параметры, как тип древесины, из которой были получены опилки, степень их загрязненности посторонними примесями, влажность и размер фракций.
Хранилище для опилок должно быть сухим, вместительным и соответствовать нормам пожарной безопасности
Качественные характеристики материала для изготовления пеллет и степень его подготовки к производственному процессу определяют технологию получения готовой продукции, а также выбор оборудования. При этом необходимо учитывать следующие нюансы.
- В том случае, если влажность исходного материала достаточно высокая, для приведения ее к нормальным показателям потребуются мощные сушилки.
Применение такого оборудования в процессе производства пеллет приведет к увеличению как энерго-, так и трудозатрат при реализации технологического процесса.
- Если в составе исходного сырья содержится много древесных частиц крупного размера, то в составе производственной линии по изготовлению пеллет должна присутствовать не только дробилка, но и оборудование для сепарации измельченной массы. Эксплуатация такой производственной линии также будет связана с повышенными энергозатратами.
- Эффективность технологического процесса и стабильность работы линии по производству пеллет во многом зависят от того, насколько однородным по породе древесины является исходный материал.
- Оценивая качество опилочной массы, которую планируется использовать для производства пеллетного топлива, следует обращать внимание на наличие в ее составе древесной коры, гнили и отходов от переработки старой древесины. Большое количество подобных включений в общей массе для производства топливных гранул снижает их энергетическую ценность и, соответственно, уменьшает стоимость готовой продукции.
- В составе исходного сырья могут содержаться такие посторонние примеси, как песок и камни. В этом случае пеллетная линия должна быть оснащена специальными улавливающими устройствами. Решает проблему с такими примесями и предварительная промывка материала, но в любом случае это увеличивает производственные расходы и, соответственно, себестоимость готовой продукции.
Таким образом, следует оценить характеристики опилочной массы, прежде чем пустить ее на производство пеллетов.
Для измерения влажности опилок используются влагомеры, состоящие из электронного блока и датчика, зонд которого размещается на конвейере или в бункере
Процесс предварительного измельчения опилок
В большинстве случаев для производства пеллет используются отходы деревообрабатывающих предприятий, которые поступают на пеллетное производство без предварительной сортировки. Естественно, что в таких отходах, кроме самих опилок, содержатся и другие составляющие – древесная кора, крупные щепки, бруски, горбыль и др.
Рабочими органами дробилок, используемых для грубого измельчения материала, являются вращающиеся молотки
Для того чтобы привести сырьевую опилочную массу в однородное состояние по размеру содержащихся в ней фракций, используется измельчитель. В качестве такого оборудования на стадии предварительного дробления сырьевой массы применяются молотковые дробилки, относящиеся к дековому типу. Дробилка данного типа может успешно использоваться для опилок, влажность которых доходит до 80 %, при этом практически не происходит их налипания на элементы внутренней конструкции оборудования.
Устройство молотковой дробилки для древесины
Процесс сушки
На пеллетное производство может поступать сырьевая масса с различной степенью влажности, при этом непосредственно при прессовании значение данного параметра не должно превышать 8–12 %. Таким образом, линия по производству пеллет должна содержать в своем составе установку для сушки сырья, в качестве которой, как правило, используется сушильный барабан. Для подачи влажного сырья в такое оборудование используются транспортеры шнекового типа, что является наиболее экономичным вариантом решения данного вопроса.
Схема многоконтурной аэродинамической сушилки
Аэродинамическая сушилка опилок, основу которой составляет сушильный барабан с возможностью регулирования скорости вращения, включает в свой состав несколько технических устройств:
- источник генерации и подачи горячего воздуха, работающий на природном газе или на любом другом виде топлива;
- циклон, в который опилочная масса поступает после сушки;
- бункер-накопитель, из которого опилки подаются в рабочую камеру сушильного барабана;
- циклоны, в задачи которых входит очистка топочных газов от пыли, а также улавливание частиц мелкой фракции, содержащихся в просушиваемом сырье;
- дымосос, обеспечивающий проход горячего воздуха с определенной скоростью через камеру сушильного барабана и воздушные каналы циклонов;
- шнековые транспортеры – оборудование, обеспечивающее подачу влажного сырья в камеру сушильного барабана и транспортировку уже высушенных опилок в бункер-накопитель.
Сушильный комплекс производительностью до 1000 кг/час с печью, работающей на дровах, опилках или щепе
Процесс сушки опилок, для осуществления которой используется сушилка аэродинамическая, выглядит следующим образом.
- Опилочная масса, которую необходимо просушить, подается в камеру сушильного барабана, ось вращения которого расположена в горизонтальной плоскости. При вращении такого барабана контролируется равномерность распределения в его рабочей камере загруженной сырьевой массы. Чтобы обеспечить безопасность процесса сушки опилок в барабане, в его конструкции предусмотрен специальный взрывной клапан.
- Ворошение опилок в сушильном барабане, что позволяет более оперативно и равномерно просушить их в потоке горячего воздуха, обеспечивают специальные лопатки, закрепленные на стенках рабочей камеры устройства.
- После просушивания до требуемого уровня влажности опилки из барабана поступают в циклон, где происходит их осаждение и дозированная подача в накопительный бункер.
- Очистка использованного горячего воздуха от древесной пыли также обеспечивается при помощи циклонного оборудования.
- За соблюдение всех режимов работы сушильного оборудования отвечает блок автоматики.
Технология дробления
Технология производства пеллет из опилок предусматривает, что сырье, поступающее в гранулятор, не должно содержать в своем составе частиц, длина которых превышает 4 мм. Большинство современных моделей оборудования для производства топливных пеллет работает на сырье, размеры частиц которого составляют не более 1,5 мм, а насыпная масса находится в пределах 150 кг/м3. Для достижения таких параметров сырья перед его подачей в прессовальное оборудование используется измельчитель. Как правило, это дробилка молоткового типа, которая способна работать с опилочной массой, имеющей влажность не выше 25 %.
Измельчитель, при помощи которого выполняется финишное дробление опилочного сырья, должен соответствовать определенным показателям производительности как по перерабатываемому сырью, так и по создаваемому воздушному потоку.
Объясняется это тем, что измельчитель, которым оснащается линия для производства пеллет, не только выполняет функции дробления, но и формирует воздушный поток, удаляющий измельченное сырье из рабочей камеры оборудования. Именно поэтому, выбирая измельчитель, следует ориентироваться на характеристики управляющего циклона.
Роторно-молотковая дробилка, предназначенная для измельчения древесной массы в процессе производства топливных пеллет
Подача сырья в накопительный бункер
Подача в циклонное оборудование измельченного в молотковой дробилке опилочного сырья, как уже говорилось выше, обеспечивается за счет давления воздуха, создаваемого при вращении молотков в рабочей камере. Задача циклона, которым оснащается практически любая современная линия производства пеллет, заключается в том, чтобы отделить опилки от потока воздуха, транспортирующего их из измельчительного устройства. Работает такая установка следующим образом.
- Поток воздуха, поступающий в циклон вместе с измельченными опилками, закручивается по спирали.
- Под действием центробежной силы опилки, двигающиеся вместе с потоком воздуха, прижимаются к стенкам рабочей камеры оборудования.
- Постепенно теряя скорость, опилки под действием силы тяжести осаждаются в нижней части камеры циклона, а воздух, вместе с которым они перемещались, выходит через выхлопную трубу.
- Накапливающиеся в нижней части камеры оборудования опилки выгружаются в накопительный бункер.
В состав линии производства пеллет входит входит циклон отвода сухой биомассы
Доведение влажности опилочной массы до требуемого уровня
После нескольких этапов предварительной подготовки опилки могут стать слишком сухими, что не позволит сформировать из них гранулы с плотной и однородной внутренней структурой. Производство пеллет из опилок предполагает, что их влажность непосредственно перед прессованием должна находиться в пределах 8–12 %. Если данное требование не выдерживается, прессуемое сырье необходимо дополнительно увлажнить.
Современное оборудование для производства пеллет из опилок оснащается шнековыми смесителями, в которых повышение влажности сырья осуществляется при помощи подаваемого в них под давлением пара. При выполнении такого технологического процесса следует постоянно мониторить уровень влажности опилочного сырья, чтобы вовремя прекратить обработку паром.
Формирование топливных гранул
Основная технологическая операция, которую выполняет для производства пеллет оборудование, – это формирование из рассыпчатого опилочного сырья гранул с плотной и однородной внутренней структурой. Для осуществления такой процедуры на современных линиях по производству пеллет устанавливают устройства с матрицами круглого или плоского типа. Оборудование, оснащенное матрицами круглого типа, больше подходит для того, чтобы прессовать материалы, не отличающиеся высокой твердостью. На таком оборудовании, в частности, производят не топливные гранулы, а пеллеты из более упругих и мягких материалов, которые применяются в химической, комбикормовой и пищевой промышленности.
Пресс-гранулятор с матрицей кольцевого типа
Изготовление древесных пеллет, оборудование для производства которых по принципу своего действия мало чем отличается от устройств, предназначенных для прессования более мягкого сырья, осуществляется при помощи матриц плоского типа. Производственный процесс по формированию пеллет, выполняемый на оборудовании как с круглыми, так и с плоскими матрицами, выглядит следующим образом. Катки с ребристой рабочей поверхностью, перекатываясь по поверхности матрицы, продавливает через отверстия в ней рассыпчатое сырье, формируя из него плотные гранулы цилиндрической формы. Длина готовых пеллет, выходящих с обратной стороны матрицы, регулируется при помощи специального ножа, совершающего возвратно-поступательные движения.
Толщина стенки матрицы зависит от диаметра рабочих отверстий
Заключительные этапы технологического процесса
Поскольку пеллеты, выходящие из прессового оборудования, разогреты до значительной температуры, их необходимо принудительно охладить, чтобы не допустить их «запаривания» в герметичной упаковке, что приведет к их насыщению влагой. Пелетами, которые подвергнутся такому процессу, нельзя будет пользоваться в качестве топлива. На современных производственных линиях по производству пеллетного топлива для осуществления технологической операции охлаждения применяется специальное оборудование, представляющее собой прямоточные колонны, в которых через готовые гранулы пропускается поток охлажденного воздуха.
Гранулы из охладительной колонны по транспортеру поступают в бункер готовой продукции, а затем отправляются на фасовку
Современные мини-линии по производству топливных гранул и линии более высокой производительности также комплектуются дозирующими устройствами и оборудованием, позволяющим оперативно упаковывать готовую продукцию в тару требуемого объема и веса.
Оборудование для производства пеллет из древесных отходов в домашних условиях
В условиях постоянно растущей стоимости энергоресурсов рациональным видом топлива для индивидуальных систем отопления выступают пеллеты – гранулированный биоматериал. Из чего делают пеллеты? Из древесных отходов, соломы, лузги семечек подсолнуха, торфа.
Какие пеллеты лучше для отопительных систем в частных домах? Однозначно топливо, сделанное из отходов древесины. Популярность материала объясняется абсолютной экологической безопасностью и тепловыми характеристиками древесного топлива, за один час горения пелетты вырабатывают порядка 5 кВт тепловой энергии. Одна тонна биотоплива пеллеты при сжигании выделяет количество тепла, аналогичное 500 л дизтоплива либо 700 л мазута.
Важно! Для производства пеллеты в домашних условиях не стоит использовать древесные отходы от таких видов древесины, как липа, тополь и ива. Показатели «скрепления» у обозначенных пород древесины довольно низкие, и при любом механическом воздействии гранулированный материал рассыплется на мелкие частицы.
Сегодня наладить производство пеллетов в домашних условиях – задача вполне выполнимая, но для ее реализации потребуется специальное оборудование для производства пеллет. Чтобы организовать процесс по производству пеллет, необходимо знать технологию изготовления спрессованного биоматериала.
Технология производства
Технология производства пеллет состоит из шести основных процессов:
- подготовка сырья;
- дробление;
- сушка сырья;
- повторное дробление;
- прессование;
- расфасовка.
Первый этап по производству пеллет заключается в сортировке сырьевого материала (из древесных отходов изымают сторонние примеси). Затем отсортированный материал отправляется на линию первичного дробления. Конечный результат первичного дробления – щепа толщиной до 2 мм и длиной 30–50 мм. Для изготовления пеллет требуется древесина с влажностью не более 10%, поэтому задача третьего этапа состоит в удалении излишней влаги из сырьевого материала.
Следующий производственный этап заключается в доведении сырья до состояния мелкой стружки либо древесной муки. После тонкого дробления сырьевой материал подлежит прессованию, для более крепкого сцепления гранул древесную стружку перед отправкой на пресс для пеллет обрабатывают горячим паром. Полученный на выходе продукт охлаждают естественным способом и расфасовывают.
Технология изготовления: процессы дробления, сушки и гранулирования сырьевого материала, безусловно, требуют применения специализированного оборудования.
Производство пеллет: виды оборудования
Линия по производству гранулированного топлива в обязательном порядке должна включать такое оборудование, как:
- дробилка;
- сушилка;
- прессовочный агрегат.
Дробилки
Для измельчения исходного сырьевого материала используют дробилки. Производство пеллет в домашних условиях может быть налажено с использованием техники, приобретенной в торговой сети либо с применением самодельной дробилки. Описания, как делают дробилки собственными силами, можно найти в интернете.
Сушилки
Для сушки измельченных древесных отходов используют сушилки. Сегодня современный рынок предлагает несколько видов сушильного оборудования:
- пневматические сушилки;
- сушильные барабаны;
- аэродинамические сушилки;
- диспергаторы;
- агрегаты ленточного типа.
Сушку для домашнего производства биотоплива также можно изготовить своими руками. Наиболее простым вариантом для самостоятельного изготовления являются агрегаты барабанного типа.
Конструкция сушильного самодельного барабана состоит из нескольких металлических бочек, металлической рамы и лопастей, электродвигателя с редуктором, газовой либо электрической тепловой пушки. Металлические бочки соединяют между собой сваркой, к внутренней поверхности барабана приваривают лопасти. Металлическую раму изготавливают с наклоном в одну из сторон, на основу монтируют сваренные бочки. Горячий воздух подается в сушильную камеру посредством тепловой пушки. Вращение барабана обеспечивает электромотор, соединенный с редуктором.
Грануляторы
Ключевая роль в процессе производства биотоплива отводится прессу для изготовления пеллет или гранулятору. Принцип работы пеллетного пресса заключается в следующем – катки, входящие в конструкцию станка, передвигаясь по поверхности матрицы, выдавливают сырье через отверстия. В результате на выходе спрессованная масса приобретает форму маленьких цилиндров заданного диаметра. Вращение вала обеспечивает мощный электромотор, вращательный момент передается посредством редуктора или ременного привода. На выходе из матрицы предусмотрен нож, который срезает готовый продукт с матрицы.
В процессе производства биологического топлива может быть использован гранулятор для пеллет с плоской либо круглой матрицей. На рынке средств малой механизации присутствуют гибридные модели, конструкция которых предусматривает одновременное наличие двух типов матриц.
Цилиндрические матрицы
Станки с матрицами цилиндрической формы чаще всего используют в промышленном производстве. Круглая матрица представляет собой перфорированный цилиндр диаметром до 550 мм. Сырьевая масса засыпается внутрь цилиндра и выдавливается наружу посредством катков с насечками. Катки располагаются внутри цилиндра.
Прессы с плоскими матрицами
Плоские матрицы специально рассчитаны на работу с твердыми видами материалов. Они представляют собой плоский стальной диск толщиной 20–100 мм с многочисленными отверстиями. В отличие от агрегатов с цилиндрической матрицей, в этом оборудовании подача сырьевого материала осуществляется на поверхность дисков.
Диаметр диска варьируется в диапазоне 100–1250 мм. Чем больше диаметр матрицы, тем выше производительная мощность прессовочного станка. Станок для производства пеллет с матрицей диаметром 1250 мм способен производить до 3 т гранулированного топлива за час.
Изготовление пеллет в домашних условиях с использованием самодельного оборудования лучше осуществлять на установках с плоскими матрицами. Для организации процесса потребуется приобрести готовые матрицы и электродвигатель, металлическую раму, шкив привода и бункер для приема сырья можно изготовить самостоятельно.
Подведя итоги, можно сказать, что, задумываясь над вопросом, как сделать пеллеты в домашних условиях, следует первым делом просчитать экономическую выгоду от предприятия. Домашнее производство будет выгодно в случае наличия постоянного источника дешевого сырья и собственноручного изготовления комплекта необходимого оборудования.
‘; blockSettingArray[0][«setting_type»] = 6; blockSettingArray[0][«elementPlace»] = 2; blockSettingArray[1] = []; blockSettingArray[1][«minSymbols»] = 0; blockSettingArray[1][«minHeaders»] = 0; blockSettingArray[1][«text»] = ‘
‘; blockSettingArray[1][«setting_type»] = 6; blockSettingArray[1][«elementPlace»] = 0; blockSettingArray[3] = []; blockSettingArray[3][«minSymbols»] = 1000; blockSettingArray[3][«minHeaders»] = 0; blockSettingArray[3][«text»] = ‘
Оборудование для производства пеллет.
Оборудование для производства пеллет
Пеллеты — это гранулы цилиндрической формы, которые используются в качестве биотоплива, изготавливаются из отходов деревообрабатывающего производства и отходов лесозаготовки. Пеллеты – экологически чистое топливо, с содержанием золы до трех процентов.
Изготовление пеллет представляет собой высокорентабельное производство. Сырьевой базой для изготовления топливных древесных гранул в основном выступает отходное производство лесопильных предприятий. Поэтому в целях снижения транспортных расходов топливные заводы расположены непосредственно вблизи лесопилок или же произрастания низкосортной древесины. Утилизация лесопильных отходов для производства гранулированного биотоплива сегодня является выгодным бизнесом. Созданию экологически чистого продукта из древесных отходов, заменяющего топливно-энергетические ресурсы, государство России уделяет пристальное внимание. За последние пять лет благодаря усилиям, предпринятым на правительственном уровне, на территории России значительно расширилось пеллетное производство, которому присвоен статут приоритетного направления.
В течении последних десяти лет в России открыло более 150 предприятий по выпуску пеллет. Пеллетное производство растет год от года. Интересно отметить, что в современных условиях производство пеллет выпускают как крупные пеллетные заводы, так и малые предприятия. Причем крупные пеллетные заводы ориентированы в основном на экспортный рынок сбыта своей продукции. Набирают обороты и так называемые мини-заводы по изготовлению древесных гранул. Пеллеты сегодня являются востребованным биопродуктом. Экспортные поставки пеллет являются весьма доходными и пользуются высоким спросом европейских странах. Наиболее высокий уровень отгрузок пеллет осуществляется в скандинавские страны. Растет спрос на топливные гранулы и на азиатском рынке. Малые предприятия, выпускающие древесные гранулы из отходов лесопиления, снабжают местные котельные топливом, что также значительно сокращает расходы на топливно-энергетические издержки предприятия.
Сырье для производства пеллет
Пеллетные заводы расположены вблизи лесопильных предприятий, поскольку основу для выпуска пеллет составляют лесопильные отходы. В качестве сырья для изготовления пеллет используются в основном отходы пиления, опилки. Лесопильные отходы, т.н. опилки (стружка) образуются в ходе деревообработки. Опилки имеют разный размер, что зависит от параметров режущего инструмента.
Опилки – основное сырье для изготовления пеллет
Также для производства топливных древесных гранул широко используют отходы деревообрабатывающей промышленности, стружка. В качестве сырья для выпуска пеллет используют и отходы лесозаготовительной деятельности. В свою очередь к отходам лесозаготовки, предназначенным для изготовления пеллет, относится балансовая (некачественная древесина), низкосортная древесина, кора и ветки.
Важно отметить, что при изготовлении одной тонны пеллет уходит от трех до пяти кубометров древесных отходов естественной влажности.
Производственный цикл выпуска пеллет включает в себя во-первых, дробление — измельчение опилок, веток и коры до состояния древесной муки; затем, полученная масса поступает в сушку; после чего происходит доизмельчение сырья; после дополнительного увлажнения масса подвергается прессованию. Заключительным этапом создания топливных гранул из древесных отходов является охлаждение готового продукта, после чего происходит фасовка и упаковка готовой продукции.
Оборудование для дробления опилок, веток и низкорослой древесины
В начале производственного процесса изготовления пеллет опилки, ветки и низкорослая древесина подвергаются измельчению. Для этой цели предприятия используют различного вида дробилки и щепорезы, с помощью которых отходы деревообработки измельчаются до состояния муки. Рубильные машины (дробилки) подвергают измельчению древесного сырья до фракции 25Х25Х2 мм.
Все измельчители работают по принципу роторной дисковой дробилки. При этом древесные опилки подаются в специальный патрубок. Далее специальным узлом происходит самозахват сырья с последующей подачей на режущий инструмент. Диск ротора снабжен специальными ножами, которые разрезают древесное сырье до мелкой фракции. На роторе установлены шипы и пазлы для получения калиброванной щепы.
По способу установки дробилки бывают: мобильные и стационарные. В пеллетном производстве используются дробилки следующих видов: дробилки ударного действия, гидравлическая конусная дробилка, ударная дробилка, роторные дробилки, конусные дробилки и центробежные дробилки и другие виды.
Ударная дробилка широко применяется для измельчения всех видов мягких и средней твердости древесных опилок первичного дробления и вторичного дробления
Ударная дробилка для измельчения древесных опилок
В ходе измельчения сырья для производства топливных гранул пеллетные предприятия используют дробилки для измельчения отходов лесопиления и низкосортной древесины, а также измельчители веток различных видов.
Дробилки для измельчения отходов лесопиления и низкосортной древесины
Для измельчения небольших веток часто используют щепорез, работающий на бензине. Щепорез превращают низкосортную древесину и ветки в щепу. Промышленные предприятия используют как щепорезы, так и рубильные машины. Такие механизмы имеют конструкцию ротора с системами шипов и пазов. В результате получается калиброванная щепа без использования сеток. Такие измельчители снабжены самозахватом исходного сырья.
Щепорез для измельчения веток
Измельчитель веток
В результате измельчения древесных отходов путем сухого механического размола получается древесная мука.
Оборудование для сушки древесной муки
Вторым этапом создания топливных гранул из древесного сырья является сушка. К моменту прессования масса должна иметь влажность не более 10%. Процесс сушки является необходимым условием для изготовления пеллет. Таким образом топливные гранулы должны иметь низкую влажность, что создает дополнительные затраты в процессе производства. Сушка пеллетного сырья составляет высокую статью расходов.
Сушилки бывают двух типов – барабанные и ленточные. Сушилки могут работать на топочных газах, на горячем воздухе или же на водяном паре.
Прежде чем сырье поступает в пресс, фракция подвергается доизмельчению. Процесс доизмельчения необходим для создания фракции, размер которой не должен превышать 4 мм. Этот процесс обеспечивают молотковые мельницы, стружечные станки или дезинтеграторы.
После создания фракции нужного размера, массу подвергают дополнительному увлажнению, так как сырье с влажностью менее 8% плохо прессуется. Для дополнительного увлажнения применяют шнековые смесители. Такие смесители подают в массу воду и пар. Пар необходим для увеличения пластичности древесного сырья твердых древесных пород.
Оборудование для гранулирования пеллет
Прессование представляет собой процесс гранулирования. Гранулятор (окомкователь) предназначен для прессования и сжатия древесной муки в гранульную форму. Сжатие сырья в процессе прессования повышает температуру сырья, при этом лигнин, который содержится в древесной муке начинает размягчаться, склеивая частицы древесной муки в цилиндрики плотной формы. Пресс-гранулятор сжимает древесную муку до состояния гранул.
Полученные гранулы необходимо охладить. Охлаждение гранул требуется для кондиционирования гранул после процесса прессования.
Оборудование для фасовки пеллет
Готовые гранулы фасуют и упаковывают в различную упаковку – от небольших пакетов (от 2 до 20 кг) до биг-бэгов (большая промышленная упаковка, в такую упаковку входит несколько тонн пеллет.
Мелкая расфасовка топливных древесных гранул
Иногда топливные гранулы доставляют потребителю россыпью. Транспортировка пеллет насыпью осуществляется либо на крупные ТЭЦ, либо на дальнейшую фасовку в мелкую упаковку. Топливные гранулы из древесных отходов обладают неоспоримым преимуществом – пеллеты легко транспортировать. Пеллеты имеют правильную форму и однородную консистенцию, что позволяет автоматизировать процесс погрузки и разгрузки пеллетной продукции. Так же пеллеты удобны при использовании в процессе сжигания.
Технология производства пеллет. Экологически чистые виды топлива. Весь пеллетный ассортимент
Топливные пеллеты — это биотопливо, получаемое из древесных отходов и производных сельского хозяйства. Производится в виде прессованных гранул стандартного размера.
В основе технологии производства топливных брикетов, лежит процесс прессования шнеком отходов (шелухи подсолнечника, гречихи и т. п.) и мелко измельченных отходов древесины (опилок) под высоким давлением при нагревании от 250 до 350 С°. Получаемые топливные брикеты не включают в себя никаких связующих веществ, кроме одного натурального — лигнина, содержащегося в клетках растительных отходов. Температура, присутствующая при прессовании, способствует оплавлению поверхности брикетов, которая благодаря этому становится более прочной, что немаловажно для транспортировки брикета.
Одним из наиболее популярных методов получения топливных пеллет, является экструзия с использованием специальных экструдеров. Процесс производства древесных гранул классически строится по следующей схеме:
- Крупное дробление
- Сушка
- Мелкое дробление
- Корректировка влажности и микс
- Прессование
- Охлаждение, сушка
- Расфасовка
Крупное дробление
Крупные дробилки измельчают сырье для дальнейшей просушки. Измельчение должно дойти до размеров частиц не более 25x25x2 мм. Крупное дробление позволяет быстро и качественно высушить сырье и подготавливает его к дальнейшему дроблению в мелкой дробилке.
Обычно влажные древесные отходы хранятся на бетонном полу, чтобы избежать смешивания с песком или камнями. Сырье подается в систему сушки с помощью скребкового устройства. Оператор может брать сырье с различных площадок и подавать необработанный продукт в систему сушки.
Сушка
Древесные отходы с влажностью более 15% очень плохо прессуются особенно прессами с круглыми матрицами. Кроме этого, изготовленные гранулы с повышенной влажностью не подходят для котлов. Поэтому сырье перед прессованием должно иметь влажность между 8 и 12%. Для качественного продукта влажность должна составлять 10% +/- 1%. Сушилки бывают барабанного и ленточного типа. Выбор типа сушилки определяется видом сырья (щепа, опилки), требованиями к качеству продукции и источником получаемой тепловой энергии.
В пеллетном производстве сушка является наиболее энергоемким процессом. Для сушки опилок расходуется приблизительно 1 МВт энергии на тонну выпариваемой влаги или для практического расчета можно принимать, что на 1 т гранул требуется теплота сгорания от 1 плотного м3 древесины. Оптимальным решением является сжигание коры или опила в топке сушильной установки.
Мелкое дробление
В пресс сырье должно заходить с размерами частиц менее 4 мм. Поэтому дробилка измельчает сырье до необходимых размеров. Для качественного продукта насыпной вес после измельчения должен составлять 150 кг/м3 +/- 5%, а размер частиц не более 1,5 мм. Молотковые мельницы — наиболее подходящие устройства для измельчения волокнистой стружки, опилок или щепы.
Корректировка влажности
Сырье с влажностью менее 8% плохо поддается склеиванию во время прессования. Поэтому слишком сухое сырье также плохо. Для этого нужна установка дозирования воды в смесительной емкости. Лучший вариант — это шнековые смесители, в которых встроены входы для подачи воды или пара.
Добавление горячего пара требуется, если прессуются твердые сорта древесины (дуб, бук), или сырье залежалое, некачественное. Для мягких сортов древесины хвойных пород достаточно добавления воды в смесителе.
Прессование
Производиться на прессах различных конструкций, с плоской или цилиндрической матрицей. При этом диаметр матрицы может быть более метра, а мощность пресса до 500 кВт, в зависимости от заданной производительности. Так же на производительность пресса в пределах 20% влияет размер получаемых гранул, обычно 6 мм для частного потребления и 10 мм для промышленного.
Охлаждение
Охлаждение обеспечивает получение качественного конечного продукта. Оно нужно для осушения гранул, нагретых после прессования до 70°-90° С. Затем пеллеты просеивают и упаковывают для реализации.
Расфасовка
Чаще всего пеллеты хранятся в бункерах и транспортируются россыпью. Однако для исключения потери в качестве рекомендуется производить расфасовку в большие влагонепоницаемые мешки. Наиболее качественные пеллеты для частного потребителя могут поставляться в 20-30-ти килограммовых упаковках.
Исследование и исследование технологии производства топливных гранул из биомассы
PDFИсследование и исследование технологии производства гранул биомассы
I. Введение в топливные гранулы из биомассы
Энергия — это основа нашего существования и развития. Непрерывное потребление невозобновляемой энергии заставляет людей обратиться к использованию возобновляемых, экологически чистых источников энергии биомассы, в качестве представителя которой используется топливо из биомассы.Энергия биомассы стала стратегическим выбором для устойчивого развития гражданского общества и направления развития. Это может не только восполнить нехватку традиционных источников энергии, но также имеет большие экологические преимущества. По сравнению с другими методами получения энергии из биомассы, гранулированное топливо из биомассы легко добиться массового производства и использования. По удобству он может соперничать с газом и мазутом.
II. Необходимость разработки топлива из биомассы
С ростом потребления традиционной энергии необходимо использовать новую энергию из-за серьезной нехватки ресурсов.В Китае мы владеем богатыми топливными ресурсами в виде пеллет. В настоящее время основные ресурсы, которые могут быть использованы, включают: солому сельскохозяйственных культур, топливную древесину, отходы, древесные отходы в твердых бытовых отходах и многое другое. Согласно теоретическим расчетам, наши топливные ресурсы на древесных гранулах могут достигать 5 миллиардов тонн. Топливные гранулы из биомассы обычно относятся к твердому топливу цилиндрической формы диаметром менее 25 мм. Плотность гранул перед прессованием увеличивается до 1,2-1,4 кг / м³. Уменьшение объема от 75% до 90%, что упрощает хранение и транспортировку.Размер однородный с хорошей текучестью, облегчая автоматическую передачу и сгорание. Топливные пеллеты — это вид природного топлива из биомассы, в процессе производства нет необходимости добавлять клей. Благодаря низкому содержанию влаги легко регулировать воздух для горения, а эффективность горения высокая. Средний выброс газа при сгорании составляет 1,2 г / ч, что намного ниже 7,5 г / ч, предусмотренных USEPA. Гранулированное топливо из биомассы в гранулированной или блочной форме может значительно повысить эффективность сгорания материалов.Тепловой КПД может увеличиться более чем на 80%. Согласно расчетам, количество тепла, вырабатываемого 1,2 т древесных пеллет и 1 т угля, эквивалентно. Топливные гранулы биомассы получают из биологических отходов без химических веществ, таких как делящиеся и взрывоопасные химические вещества. При сгорании не произойдет отравления, взрыва, утечки.
III. Разработка топливных пеллет из биомассы в стране и за рубежом.
3.1 Развитие технологий использования и производства топливных гранул из биомассы в стране и за рубежом.
3.1.1 История развития
Использование топливных горелок на гранулах биомассы началось в 1970-х годах, но до конца 1980 года многие европейские страны (например, Швеция, Финляндия, Бельгия, Франция, Германия, Италия) начали придавать значение исследованиям и эксплуатации. топливных технологий из биомассы в результате мирового энергетического кризиса и роста цен на нефть. В настоящее время он сформировал промышленное производство с замечательными достижениями. Франция начинает использовать гранулы из соломы в качестве корма для дойных коров. В последние годы они также исследуют и производят топливо в форме блоков.Переработка лесных отходов в брикеты определенной формы путем механического прессования достигла практической стадии.
3.1.2 Технология гранулирования
Сушка: из-за высокого содержания влаги в опилках (обычно 50%) их следует сушить до содержания влаги в сырье 9-12%, чтобы удовлетворить потребность в формовании. Сушилка оборудована вращающимся барабаном прямого нагрева ( барабанная сушилка ).
Присыпка: После высыхания сырье необходимо измельчить в порошковой машине.Общий размер 1 мм.
Закалка и отпуск: это относится к размягчению древесного волокна в сырье, пополнению и увеличению количества высокотемпературного пара в сырье. Более чем на половине заводов по производству пеллетного топлива эта технология была применена в процессе производства.
Формование гранул: Большинство заводов по производству гранул из биомассы используют принцип экструзионного формования с роликовыми роликами, что означает вертикально-кольцевую формовочную машину и производительность 2-4 т / ч. Основные компоненты имеют длительный срок службы. Кольцевая матрица составляет 2000-3000 ч, а обжимной валок — 1000-1500 ч.
Охлаждение: Температура гранул, выгружаемых из гранулятора, составляет около 100 ℃, гранулы в таком состоянии легко ломаются и не должны храниться и транспортироваться. Следовательно, пеллеты необходимо охлаждать с помощью холодильника с принципом противоточного охлаждения.
Сборка и упаковка : После охлаждения гранулы собираются и упаковываются в соответствии с различными потребностями потребителей. Спецификации упаковки могут быть разделены на маленькие мешки (16 кг) и большие мешки (900 кг) в зависимости от потребностей. Для крупного потребителя тепловая электростанция может быть доставлена на грузовом транспорте или на лодке.
3.1.3 Анализ условий использования
Если взять, например, Америку, Швецию и Австрию, масштабы применения энергии биомассы соответственно составляют 4%, 16% и 10% от их потребления первичной энергии. В Америке общая установленная мощность производства энергии из биомассы составляет более 1 МВт, а единичная мощность составляет 10-25 МВт. Оборудование для сжигания гранулированного топлива из биомассы в Японии, Америке и некоторых европейских странах было промышленно использовано в областях отопления, сушки и генерации.Топливные гранулы из биомассы и соответствующие эффективные отопительные печи с чистым сжиганием были очень популярны, запрет на эффективность нагрева достигает 80-95%.
3.2 Использование условий и технологий производства. Разработка отечественного гранулированного топлива из биомассы
3.2.1 История разработки
Условно говоря, мы поздно начали исследования и производство в этой области, но мы уделяем этому много внимания. С 1980 года наше правительство сделало исследования и применение технологий применения топлива из биомассы в качестве ключевого национального вопроса.Технология энергии биомассы перешла на более высокую ступень. Машина для формования соломинок спирально-выталкивающего типа, представленная в 80-х годах, сформировала определенный масштаб. Но наши исследования в основном сосредоточены на технологиях производства биогаза для крупного и среднего скота и птицы, газификации соломы, централизованной подачи газа и электростанций на полигонах. Для производства топливных гранул из биомассы и исследований в области прямого сжигания нам предстоит пройти долгий путь. В некоторых университетах и научно-исследовательских учреждениях в последние годы были достигнуты определенные достижения и масштабы производства.
3.2.2 Анализ условий использования
Машина для формования соломы спирально-выталкивающего типа, представленная в 80-х годах, сформировала определенный масштаб. Но наши исследования в основном сосредоточены на технологиях производства биогаза для крупного и среднего скота и птицы, газификации соломы, централизованной подачи газа и электростанций на полигонах. Для производства топливных гранул из биомассы и исследований в области прямого сжигания нам предстоит пройти долгий путь. В некоторых университетах и научно-исследовательских учреждениях в последние годы были достигнуты определенные достижения и масштабы производства.Например, разработанная нами грануляторная мельница включает гранулятор с кольцевой матрицей и гранулятор с плоской матрицей , кроме того, они начали исследования по топливной машине для гранулирования биомассы из соломы сельскохозяйственных культур. С 2002 года первоначальный центрально-южный лесохозяйственный колледж разработал машину для формования топливных гранул из биомассы и подходящую печь для защиты окружающей среды и отопительную печь на основе передовых технологий, импортированных из-за границы (Швеция). Машина для формования гранулированного топлива из биомассы была разработана на основе технологии отечественного гранулятора для производства гранул в сочетании с технологией шведской машины для производства гранулированного топлива из биомассы.Новая экономичная печь, которая может использоваться для приготовления пищи и обогрева, была разработана на основе технологии абсорбционных горелок, применяемых в других странах, и, в соответствии с конкретной ситуацией в Китае, ее камера сгорания использует метод подачи вторичного воздуха, обеспечивающий достаточное сгорание и высокую теплоотдачу. эффективность. Защита окружающей среды и энергосбережение для обогревателя были разработаны на основе импорта передовых зарубежных каминов и в сочетании с нашей реальной ситуацией. За счет изменения размера машины, улучшения системы подачи пеллет и увеличения площади теплообменной трубы этот тип нагревателя подходит для домашнего использования.
3.3 Тенденции развития и советы
3.3.1 Правительство постоянно совершенствует соответствующую политику производства и использования топливных гранул из биомассы и устанавливает систему стандартов топлива.
В настоящее время в нашей стране приняты соответствующие законы и программы по энергии биомассы, также был принят ряд систем производства пеллетного топлива, и мы создали стандартную систему пеллетного топлива из биомассы. Однако наша промышленность по производству топливных пеллет находилась на ранней стадии развития и не была полностью принята рынком.Нам необходимо разработать конкретную политику и меры для содействия использованию и использованию пеллетного топлива и гарантировать, что существующие законы и политика могут работать эффективно. Нам необходимо оказать большую поддержку, особенно в производстве оборудования и использовании исследования рынка пеллетного топлива: сделать совершенное техническое состояние и стандарт по аспектам печей, котлов и камер сгорания, работающих на биомассе.
3.3.2 Улучшение системы обеспечения качества и создание национального центра сертификации топлива и оборудования для сжигания биомассы.
ЕС имеет зрелую и безупречную систему гарантии качества, прежде чем пеллетное топливо и оборудование для сжигания появятся на рынке, они должны быть протестированы в отделе инспекции. Поскольку пеллетное топливо в Китае только началось, гарантийная система несовершенна, пеллетное топливо и пеллетное топливо оборудование для сжигания выходит на рынок без тестирования и сертификации, что приводит к значительному различию качества топливных гранул и оборудования для сжигания, это влияет на прогресс отрасли производства твердого гранулированного топлива из биомассы, поэтому на основе существующего научно-исследовательского учреждения нам необходимо создать комплексные исследовательские институты в совокупность исследований, обнаружения и триединства изучения рынка для содействия изучению рынка, усвоения последней информации о рынке, ускорения трансформации научных исследований в рынок и обеспечения того, чтобы научные исследования отражали его огромную социальную и экономическую ценность : в то же время мы должны учиться из ЕС в опыте тестирования топливных гранул, создали национальную биомассу, чтобы крышка пеллетного топлива и испытательного центра оборудования для горения.
3.3.3 Расширить зону типичной демонстрационной рекламы, реализовать крупномасштабное производство и регулярно комбинировать с источником сырья
Топливные пеллеты нашего округа основаны на соломе сельскохозяйственных культур, учитывая проблемы радиуса транспортировки, стоимости и хранения в соломе , наши предприятия по производству пеллетного топлива должны ориентироваться на средние предприятия, которые производят 10000 ~ 20000 тонн в год, чтобы мы могли реализовать крупномасштабное производство, в том числе с учетом обширной территории, большой тепловой разницы и различных характеристик соломинок, Демонстрационные проекты должны быть созданы в различных областях, чтобы продвинуть развитие нашей топливной промышленности из гранул из биомассы и сделать ее полностью коммерциализированной и маркетинговой.
3.3.4 Дальнейшее изучение механизма формования в биомассе, Улучшение конструкции оборудования и минимизация количества повреждаемых частей и снижение энергопотребления оборудования для гранулирования
В настоящее время на рынке формованное производство оборудования для гранулирования биомассы в основном горячее, оно имеет проблему высокого энергопотребления, а детали формования (экстрактор шнека, формовка, кольцевая матрица, пресс-валок и т. д.} легко изнашиваются. Мы должны провести исследования механизма формования материала биомассы, изменить способ формования и, насколько это возможно, уменьшить трение между материалом и формованием, чтобы продлить срок службы штампа и снизить стоимость.Древесные пеллеты в мелкой упаковке на рынке США — 170 долларов за тонну, в крупной упаковке — около 135 долларов за тонну; Стоимость доставки по Швеции 150 $ / т. Цена на гранулы навалом в Амстердаме составляет 80 долларов за тонну. Если мы импортируем технологию ETS для производства древесных пеллет, себестоимость производства намного ниже, чем за рубежом. По расчетам, себестоимость массового производства составляет около 240 юаней / тонну, розничная цена — 329 юаней / тонну (39 долларов за тонну), нет сомнений в том, что эта цена не только на международном рынке, но и в Китае может побороться с ценой на уголь. Таким образом, улучшенная технология также является одним из эффективных методов повышения коэффициента использования.
IV. Исследования в области технологии гранулирования с кольцевой матрицей
4.1 Структура и принцип работы гранулятора с кольцевой матрицей
Гранулятор с кольцевой матрицей состоит из двигателя, редуктора скорости, главной оси, приводного вала, кольцевой матрицы, прижимного ролика, машины принудительной подачи, ножевого компонента, корпус и шибер. Двигатель приводит в движение кольцевую матрицу и заставляет ее вращаться «входящий материал в кольцевую матрицу приводит во вращение валок, когда материал подается в рабочую зону через машину принудительной подачи» с вращением кольцевой матрицы и прижимного валка » материал до того, как прижимной валок был раздавлен в зону сжатия, материал был раздавлен в области «промежуток в материале быстро уменьшился» «напряжение и плотность внутри материалов увеличились», упругая деформация материала превратилась в пластическую деформацию », когда материал достигнув своей плотности, он будет вытеснен через отверстие матрицы, и после определенного временного давления «материал с определенной плотностью выдавил отверстие матрицы» и превратился в гранулы биомассы топливо.
4.2 Состояние исследований технологии гранулирования с кольцевой матрицей
В целом, при разработке гранулятора с кольцевой матрицей принцип работы остался прежним, но уровень производства и технические характеристики значительно улучшились. В настоящее время широко используемый типовой гранулятор с кольцевой матрицей включает в себя: гранулятор с кольцевой матрицей компании CPM имеет конструкцию привода редуктора с угловым редуктором, он может осуществлять двухскоростной обмен в ручном режиме. Это называется гранулятором с подвижной моделью, в котором неподвижная кольцевая матрица вращается на полом валу большой зубчатой передачи, прижимной валок закреплен на твердом валу с помощью фиксированного устройства.Кольцевая матрица оснащена трехкомпонентными кольцевыми зажимами для фиксации, проста в установке и оснащена устройством автоматической циркуляционной системы смазки, обеспечивая безопасность при использовании. Гранулятор с кольцевой матрицей использует двухвалковый пресс, кольцевую матрицу, конструкцию устройства с клиноременной передачей с одним двигателем. Он имеет высокую эффективность производства, низкие эксплуатационные расходы, простую конструкцию и удобное управление. Система может работать с автоматической смазкой и контролем. В нем используется однодвигательный привод, полый вал, кольцевая матрица, шпиндель, ролик, большой ременной привод в сборе и т. Д., Натяжение ременного привода поддерживается хвостовой консолью шпинделя, который является подшипником высокой нагрузки и в состоянии частичной нагрузки.К проектированию, расчету и согласованию предъявляются высокие требования. Гранулятор с кольцевой матрицей в компании Munch включает в себя две мельницы: кольцевую матрицу и коническую роликовую плоскую матрицу. Конструктивная форма гранулятора с кольцевой матрицей такая же, как и одноступенчатый синхронный зубчатый ремень компании UMT. В грануляторе с кольцевой матрицей применен клиноременной привод от Munch, большой шкив широкий, основание двигателя выполнено из чугуна, машина довольно тяжелая, но гладкая, низкий уровень шума, пример большого шкива энергоэффективный.Фиксированная конструкция кольцевой матрицы должна использовать трехкомпонентный кольцевой зажим CPM, если мы используем болт, это займет много времени. Система может работать с автоматической смазкой и контролем. Трехвалковый гранулятор с кольцевой матрицей — подарок компании UK UMT. типичный гранулятор с кольцевой матрицей. Многие компании производят аналогичные продукты в стране и за рубежом, способ привода включает тип зубчатого и ременного типа. Все грануляторы с трехвалковой кольцевой матрицей Crown используют синхронную зубчатую ременную передачу, среди них тип 350B — двухмоторная синхронная зубчатая ременная передача, другие — все используют двухмоторные клиновые ремни и вторичную синхронную зубчатую ременную передачу.
V. Заключение
Пеллетный завод на биомассе будет иметь светлое будущее, однако из-за различных типов ресурсов опыт разработки в зарубежных странах не подходит для нашей страны. Мы должны разработать соответствующую политику для поощрения и эффективного контроля в области топливных гранул из биомассы и стандарт разработки
Wood Pellet — обзор
13.4.3 Пеллеты и брикеты
Пеллеты из прессованных опилок или древесных стружек доступны во многих частях мира уже более нескольких десятилетий. Поскольку гранулы спрессованы, они представляют собой более концентрированную форму топлива, чем древесная щепа. Следовательно, им требуется меньше места для хранения, и с ними легче обращаться. Производство древесных гранул требует больше энергии, чем древесная щепа, а капитальные затраты на производство завода высоки; пеллеты, следовательно, дороже щепы.
Древесные гранулы обычно изготавливаются из прессованных опилок, которые являются отходами других отраслей промышленности (например, лесопильных заводов). Гранулы удерживаются вместе естественным лигнином в древесине — обычно связующий клей не требуется. Лигнин составляет примерно от четверти до трети сухой древесины. Он укрепляет древесину, а также обладает водонепроницаемыми свойствами.
Древесные гранулы имеют очень низкое содержание влаги, обычно 6–10%, что означает, что древесные гранулы являются очень хорошим источником энергии, поскольку очень мало энергии в гранулах используется для испарения влаги.Общие свойства древесных гранул:
Влажность: 3,5% –5,5%
Зола: 0,2% –0,5%
Теплотворная способность: 8800 БТЕ / фунт
Насыпная плотность: 600–750 кг / м
Гранулы очень плотные, а низкая влажность (ниже 10%) позволяет их сжигать с очень высокой эффективностью сгорания. Правильная геометрия гранул и небольшой размер позволяют производить автоматическую подачу с очень точной калибровкой.Их высокая плотность также обеспечивает компактное хранение и рациональную транспортировку на большие расстояния.
Древесная щепа — это твердое топливо, получаемое из древесины, которое часто используется в качестве сырья для технической обработки древесины. В промышленности обработка стружки коры часто отделяется после лущения бревен из-за различных химических свойств. Древесная щепа также может использоваться в качестве древесного топлива.
Пеллеты можно использовать в качестве топлива для различных приборов и систем отопления. Самыми маленькими из них являются пеллетные печи мощностью до 9 кВт, которые подходят для отопления отдельных помещений.Эти печи имеют электронное управление, могут выдавать регулируемую тепловую мощность и требуют дозаправки только один раз в несколько дней. Пеллетные котлы доступны в широком диапазоне мощностей от небольших домашних масштабов до крупных промышленных масштабов для обогрева школ и больниц. Для бытового потребителя пеллеты представляют собой наиболее удобный вид дровяного отопления. В Скандинавии древесные гранулы доставляются цистернами и перекачиваются в силосы для хранения, откуда они автоматически поступают в котел.
Древесные гранулы используются в печах специальной конструкции.Пеллеты обычно производятся из древесных отходов лесопильных заводов. Древесина проходит довольно длительный процесс трансформации, прежде чем окончательно экструдируется в твердые гранулы. Несмотря на переработку, топливо остается углеродно-нейтральным и поэтому менее вредно для окружающей среды, чем другие ископаемые виды топлива. Для коммерческих предприятий, как и в случае с любым древесным топливом, древесные гранулы не облагаются налогом на изменение климата. В настоящее время в Соединенном Королевстве имеется ограниченное количество заводов по производству окатышей, хотя есть некоторые стимулы производить их из местных источников.Тем временем некоторые пеллеты импортируются. Гранулы для бытовых обогревателей и бойлеров поставляются в предварительно упакованных мешках, обычно весом 22 фунта (10 кг), что делает их удобными по размеру для хранения и загрузки в бункер. Для более крупных моделей котлов пеллеты могут поставляться оптом, но при этом должен быть доступен соответствующий бункер, подключенный к котлу. В настоящее время большая часть пеллет будет поставляться печным магазином, который продает котлы, но для других поставщиков см. Нашу страницу с ссылками ниже.
Топливные брикеты (иногда называемые топливными брикетами) — особенно брикеты, изготовленные из угля (Speight, 2013), которые стали важным коммерческим предприятием в 20 веке. В 1950-х годах было разработано несколько экономических методов изготовления брикетов без связующего. Множество заводов по всему миру производили буквально десятки миллионов тонн годного к употреблению и экономичного материала, который удовлетворял бытовые и промышленные потребности в энергии. Во время двух мировых войн домашние хозяйства во многих европейских странах изготавливали собственные брикеты из пропитанной макулатуры и других горючих бытовых отходов с помощью простых рычажных прессов (Lardinois and Klundert, 1993).Современные промышленные брикетирующие машины, хотя и намного больше и сложнее, работают по тому же принципу, хотя продаваемые брикеты сейчас продаются по более высокой цене для периодических барбекю на заднем дворе, а не для повседневного использования.
На протяжении более 100 лет неформальные сборщики отходов в Каире отделяют и сушат органические отходы для продажи в качестве твердого топлива для бытового использования. Этот процесс несколько затих, когда стали доступны источники ископаемого топлива. Переход на традиционные виды топлива может оказаться выгодным для тех, кто может себе это позволить, но с учетом экономических и энергетических условий во многих городах городские и сельскохозяйственные отходы остаются жизнеспособным альтернативным топливом.
Брикетирование переживает возрождение, в основном из-за совпадения трех важнейших факторов. Во-первых, последние разработки в области обработки и связывания брикетов резко изменили экономику использования топливных брикетов в качестве энергетического ресурса. Во-вторых, нехватка топливной древесины становится все более острой в большинстве развивающихся стран. Наконец, неуклонно растет озабоченность по поводу окружающей среды, направленная на решение проблемы удаления бытовых и городских отходов, и эту дилемму можно решить с помощью брикетирования.
13.4.3.1 Производство брикетов
Как правило, производство брикетов (брикетирование) включает сбор горючих материалов, которые нельзя использовать как таковые из-за их низкой плотности, и их прессование в твердый топливный продукт любой удобной формы, который можно сжигать. как дерево или уголь. Таким образом, материал сжимается, чтобы сформировать продукт с более высокой объемной плотностью, более низким содержанием влаги и однородным размером, формой и свойствами материала. Брикеты легче упаковывать и хранить, дешевле транспортировать, удобнее использовать, а их характеристики горения лучше, чем у исходных органических отходов.
Сырье брикета должно связываться при сжатии; в противном случае, когда брикет вынут из формы, он рассыпется. Улучшенная когезия может быть получена с помощью связующего, но также и без него, поскольку при высокой температуре и давлении некоторые материалы, такие как древесина, связываются естественным образом. Связующее не должно вызывать образование дыма или смолистых отложений, а также следует избегать образования избыточной пыли. Могут использоваться два разных типа связующих. Горючие связующие получают из природных или синтетических смол, навоза животных или обработанных обезвоженных осадков сточных вод.К негорючим вяжущим относятся глина, цемент и другие адгезивные минералы. Хотя горючие связующие являются предпочтительными, негорючие связующие могут быть подходящими, если используются в достаточно низких концентрациях. Например, если органические отходы смешаны со слишком большим количеством глины, брикеты не будут легко воспламеняться или гореть равномерно. Подходящие связующие включают крахмал (5–10% мас.) Или мелассу (15–25% мас.), Хотя их использование может оказаться дорогостоящим. Важно определить дополнительные недорогие материалы для использования в качестве связующих для брикетов в Кении и их оптимальные концентрации.Точный метод подготовки зависит от брикетируемого материала, как показано в следующих трех случаях прессования сахарного жома, опилок и городских отходов в брикеты для приготовления пищи.
13.4.3.2 Брикеты из жмыха
Излишки жмыха представляют собой проблему утилизации для многих сахарных заводов. Технология брикетирования остается простой и включает следующие этапы: (1) измельчение, при котором жом измельчается, раскатывается или забивается молотком, (2) сушка, при которой влага удаляется сушкой на открытом воздухе или с использованием принудительного нагретого воздуха в большом вращающемся помещении. барабан, (3) карбонизация, при которой жмых сжигается при ограниченном количестве кислорода в подземной яме или траншеи до тех пор, пока он не карбонизируется до древесного угля, (4) подготовка исходного сырья, при которой карбонизированный жмых смешивается со связующим, таким как глина или патока , (5) прессование и экструзия, при которых материал пропускается через экструдер с механическим или ручным управлением для формирования рулонов древесного угля, (6) сушка, при которой рулоны сушатся на воздухе в течение 1-3 дней, что приводит к их разрушению. на куски и (7) упаковка, в которой брикеты подготавливаются к продаже.
13.4.3.3 Брикеты из древесных опилок
Опилки являются отходами всех видов первичной и вторичной обработки древесины. От 10% до 13% бревна превращается в опилки при фрезеровании. Опилки громоздкие, поэтому их дорого хранить и перевозить. Кроме того, теплотворная способность опилок довольно низкая, поэтому брикетирование — идеальный способ уменьшить объем, увеличить плотность и, таким образом, увеличить теплотворную способность. Оборудование, необходимое для производства брикетов из опилок, состоит из сушилки, пресса и экструдера с коническим шнеком и большим вращающимся диском.
Брикеты из опилок формируются под достаточно высоким давлением, чтобы обеспечить сцепление между частицами древесины. При этом лигнин размягчается и связывает брикет, поэтому дополнительное связующее не требуется. Использование брикетов из опилок имеет несколько преимуществ, в том числе (1) цена, которая обычно примерно такая же, как и у топливной древесины, но намного удобнее в использовании, поскольку они не требуют дальнейшей резки и измельчения, (2) хорошие характеристики горения в любом виде твердого вещества. топливная печь и бойлер, (3) быстрое зажигание с последующим чистым сжиганием с оставлением только 1-6% минеральной золы, (4) отсутствие серы и горение без запаха, и (5) теплосодержание, которое почти эквивалентен по теплосодержанию угля среднего качества.
13.4.3.4 Брикеты для городских отходов
Удаление твердых отходов (мусора) — одна из наиболее серьезных проблем городской окружающей среды в развивающихся странах. Многие муниципальные власти собирают и надлежащим образом удаляют (в местах, отличных от свалок) менее половины этих отходов. Этот сбой объясняется (1) недостаточным количеством свалок, (2) разнообразием экологических норм, (3) отсутствием достаточных мощностей для обработки и переработки отходов и, наконец, что не менее важно, (4) запланированным устаревание упаковки и многих предметов, составляющих основу отходов.
Открытый сброс или сброс сырой нефти — наиболее распространенный метод, используемый муниципальными властями. Отходы представляют опасность для здоровья, когда они разбросаны по улицам и на свалках. В настоящее время общепринятой экологической философией является то, что отходы имеют ценность и должны использоваться на основе принципов сокращения, повторного использования, восстановления и переработки. Благодаря вторичной переработке городские отходы можно превратить в полезные продукты. В частности, макулатура и листья являются потенциально важным альтернативным источником топлива для приготовления пищи.
Переработка органических горючих материалов в топливные брикеты способствует решению городских проблем, таких как получение доходов, недостаток земли для удаления отходов и поддержание качества окружающей среды. Поскольку ресурсы Земли ограничены, для достижения приемлемого уровня обращения с органическими отходами необходимо более эффективное извлечение и использование ресурсов. Улучшение утилизации органических отходов может восстановить различные естественные циклы, тем самым предотвращая потерю сырья, энергии и питательных веществ.
С другой стороны, ожидается, что спрос на энергию во многих странах приведет к увеличению выбросов парниковых газов в результате сжигания ископаемого топлива. Существует острая необходимость в продвижении экологически безопасных технологий, и брикетирование топлива, по-видимому, является одной из таких технологий, которая удовлетворяет многочисленные потребности общества и окружающей среды.
Текущие потребности сосредоточены на поиске лучших связующих для брикетов из жома, улучшенной теплотворной способности и горения за счет производства брикетов более высокой плотности, внедрения более эффективных методов экструзии и снижения производственных затрат.
Технология производства древесных пеллет, факторы, влияющие на выпуск продукции
Древесные пеллеты из различных материалов биомассы
Предлагаем индивидуализированную систему производства древесных гранул из древесных отходов (опилки, ветки, валежник и листья после уборки леса, небольшие стволы или отходы сельскохозяйственных культур и т. Д.) До древесных гранул или брикетов. (Связанный проект: Производство древесных пеллет мощностью 3 тонны в час в Малайзии )
Завод по производству древесных гранул построен для переработки материалов из биомассы, таких как солома, трава, арахис, скорлупа, древесные отходы, например, ветки, опилки, стружка и любые другие горючие материалы, доступные для изготовления гранул биотоплива для отопления, обогрева, приготовления пищи и для различных целей.(Подробнее о стоимость установки завода по производству пеллет >> )
Увеличить производство древесных пеллет на заводе
Промышленный завод по производству древесных гранул
Вертикальный гранулятор
Обычный поток обработки древесных гранул : Дробление древесины, дробление, гранулирование, охлаждение гранул, упаковка гранул в мешки.
Сырье и рабочие факторы — вот что связано с производительностью машины для производства древесных гранул.Следовательно, качество сырья во многом напрямую определяет эффективность гранулирования. Кроме того, определяющие факторы также имеют жизненно важное значение для производственной мощности гранулятора. Однако большой вопрос заключается в том, как сохранить лучшее из грануляторов. (Связанное сообщение: Стоимость производства древесных пеллет )
Если вы собираетесь создать свой собственный завод по производству древесных гранул и стать одним из производителей топливных древесных гранул, вот несколько предложений по увеличению объемов производства.Вы можете взять для справки наше оборудование для переработки древесных гранул 5т / ч .
Требования к гранулируемому сырью
К сырью могут применяться следующие меры:
- Размер исходного материала гранулятора требуется, чтобы его можно было легко производить в виде гранул высокого качества, поэтому убедитесь, что вы уделяете существенное внимание и заботитесь о размере исходного материала.
- Во-вторых, убедитесь в чистоте сырья.В заявлении говорится, что чем чище сырье, тем выше эффективность гранулятора.
- Влага — еще одна важная особенность вашего сырья. Убедитесь, что ваше сырье не слишком влажное или менее влажное. Слишком высокая влажность может изменить качество гранул и привести к большему потреблению энергии и, что важно, к износу оборудования. Убедитесь, что влажность составляет 8-15%.
- Еще одна проблема, которую следует учитывать при выборе сырья, — это твердость.Убедитесь, что они не слишком твердые, чтобы облегчить процесс изготовления гранул, а также избежать повреждения запасных частей.
- Кроме того, убедитесь, что сырье для гранулятора из древесины / биомассы является очень вязким, чтобы оно могло легко прилипать к внутренней части гранулятора. В противном случае производственная мощность будет снижена, а также изменится нормальная работа гранулятора. Наконец, плотность сырья должна быть высокой, чтобы обеспечить более высокую производительность гранулятора.
Возможно, вас также интересует: Как сделать пеллеты из соломы? Как сделать гранулы из кокосового волокна? Или как сделать гранулы из стеблей кукурузы? Если у вас возникнут другие вопросы о запуске бизнес-плана по пеллетам, не стесняйтесь обращаться к нам!
Рекомендации по эксплуатации оборудования для производства древесных пеллет
Рабочие факторы должны иметь следующие характеристики, чтобы обеспечить лучшее из коммерческого оборудования для производства древесных гранул. (Продукт для горячей продажи: Переносная мельница для гранул >> )
- Какая регулировка ролика и кольцевой матрицы в нужном месте имеет жизненно важное значение.Правильное давление — гарантия хороших результатов с точки зрения плотности гранул.
- Во-вторых, всегда вовремя заменяйте старое кольцо на штампе, так как это изнашиваемая часть вместе с роликом. Если ваш наблюдатель использует их, гранулятор не будет работать должным образом.
- Убедитесь, что вы выбрали соответствующую спецификацию кольцевой матрицы. Это необходимо для того, чтобы у вас были хорошие и качественные гранулы.
- Еще раз убедитесь, что в машину для производства древесных гранул подается однородное сырье, чтобы поддерживать необходимый коэффициент трения между сырьем, роликами и кольцевой матрицей, которая находится внутри.
- Внедрение системы охлаждения также является важным операционным фактором. Это предотвращает разрыхление гранул. После остывания правильная температура должна быть на + 3-5 выше средней температуры в помещении.
Нажмите здесь, чтобы узнать больше о Гранулятор для пустых фруктовых гроздей >>
Самым важным шагом к операционному фактору является строгое соблюдение практического руководства. Следовательно, поддержание в хорошем состоянии и чистка оборудования при необходимости.Наконец, следует подчеркнуть, что однородное сырье обеспечит надлежащую координацию эксплуатационных факторов для эффективного функционирования и долговечности гранулятора.
Разработка технологии образования биомассы — гранулятор биомассы
Для смягчения последствий глобального потепления и нехватки традиционных источников энергии становится все более необходимым использование возобновляемых источников энергии. Биомасса — наиболее распространенная форма возобновляемой энергии, которая в последние годы широко используется во всем мире.В последнее время большое внимание было сосредоточено на технологии образования биомассы, чтобы определить подходящие виды биомассы, которые могут обеспечить выход высокой энергии для замены традиционных источников энергии на ископаемом топливе. Тип требуемой биомассы в значительной степени определяется процессом преобразования энергии и формой, в которой она требуется. Преобразование биомассы в энергию может быть достигнуто несколькими способами, среди которых наиболее распространенными являются технология гранулирования (с помощью гранулятора или гранулятора) и технология брикетирования (с помощью брикетировочной машины).
Технология уплотнения твердого топлива биомассы означает метод, технологию и т. Д. Переработки материала биомассы в твердое топливо для пластов, и включает в себя технологию и оборудование всей линии по производству биомассы. Теперь твердое топливо для образования биомассы подразделяется на две формы: брикет и гранулы. Из-за различных спецификаций обработки существуют большие различия между различными технологиями уплотнения, которые можно разделить на технологию брикетирования (машина для брикетирования соломы) и технологию гранулирования (гранулятор для опилок , гранулятор из соломы л и гранулятор для пальм так далее).По структуре производства его можно разделить на технологию непрерывной обработки и технологию обработки на одной машине. Он включает дробление материала, сушку, транспортировку, смешивание, подачу, формование, резку, охлаждение, вес и упаковку и т. Д. Технология, которая может производить непрерывно и стабильно, — это непрерывное производство. Отдельная машина должна зависеть от рабочей силы для подачи материала, это не непрерывное производство.
По степени автоматизации его можно разделить на автоматическую обработку и обработку без автоматизации.Маршрут процесса и доля рабочей силы для основного продукта или большинства продуктов каждой производственной линии определили необходимое оборудование для выполнения нескольких видов обработки продукта на одной производственной линии, а также расположение оборудования и настройку рабочего места и т. Д. Маршрут каждой технологии обработки должен адаптироваться к требованиям каждого продукта путем регулировки параметра, что позволяет достичь хорошей экономической эффективности при принятии лучших технологий обработки.
В этой статье в основном исследуется технология переработки твердого топлива для уплотнения биомассы, мы делаем общий идеал о текущей ситуации с топливом для твердого образования биомассы, а также исследуем текущую ситуацию и проблемы современной технологии обработки уплотнительного оборудования производственной линии. , чтобы поговорить о методе технологического маршрута и сопутствующем оборудовании во время масштабного производства и промышленного процесса.
1. Текущая ситуация в отрасли производства биомассы в стране и за рубежом
Из-за снижения мировой традиционной энергетики — нефти, угля и природного газа, а также давления выбросов парниковых газов и т. Д., Технология уплотнения твердой биомассы была затронута зарубежными странами. развитые страны повсеместно.Согласно плану ЕС по энергии биомассы, опубликованному ЕС, доля энергии биомассы будет увеличена с 14% до 20% с 2009 по 2020 год. В 2010 году применение энергии биомассы в Финляндии, Швеции и Австрии будет единовременным. потребление энергии около 18%, 16% и 10% по очереди. В 2010 году в Швеции насчитывалось около 94 грануляторов биомассы, а общая производственная мощность составила около 2,2 млн тонн.
С 1980-х годов наша страна начала заниматься исследованиями технологии уплотнения биомассы, мы многого достигли.В 2008 году Департамент сельского хозяйства Национальной академии дизайна установил линию по производству твердого уплотненного топлива мощностью 20 кт для демонстрации в стране Дасин, городе Пекин, которая включает в себя линию по производству гранулированного топлива из биомассы 10 кт и линию по производству брикетированного топлива мощностью 10 кт каждый год. Основным сырьем для производственной линии являются стебли кукурузы, опилки, а также стебли пшеницы, скорлупа арахиса, стебли кукурузы и т.д. , Город Чжэнь Чжоу, с производственной мощностью около 15 тыс. Тонн в год.В следующем году завод по производству пеллет из биомассы был построен отдельно в Да Сингоу и Цзяо Хэ. После этого в стране было создано около десяти демонстрационных площадок завода по производству пеллет из биомассы , таких как демонстрация топливных брикетов из биомассы Yan Qing в Пекине и демонстрация топливных гранул из биомассы Huai Nan в провинции Ань Хуэй.
2. Маршрут переработки биомассы
Технология твердого уплотняющего топлива биомассы означает метод и технологию переработки материала биомассы в твердое уплотняющее топливо, она включает в себя технологию регулировки и оборудование для регулировки параметров всей производственной линии.Топливо для образования твердой биомассы имеет разные формы: брикеты, гранулы или сырье. По форме готовой продукции она подразделяется на три типа технологии: брикет, окатыш и сырье. По непрерывности производства оно подразделяется на технологию непрерывного производства и технологию производства на одной машине.
Технология непрерывного производства позволяет производить стабильно и непрерывно; он включает дробление сырья, сушку, транспортировку, смешивание, подачу, формирование, охлаждение, взвешивание и упаковку.Отдельная машина относится к непрерывному производству. По степени автоматизации оно подразделяется на автоматические производственные технологии и неавтоматические производственные технологии. Технологический параметр может быть отрегулирован автоматически в процессе производства, чтобы соответствовать требованиям каждого продукта, это называется технологией автоматического производства.
В зарубежных странах образование твердой биомассы — это в основном непрерывная автоматическая технология производства, а материал биомассы в основном поступает с фермы, перерабатывающего предприятия или деревообрабатывающего предприятия.Ресурсы централизованы с помощью простых материалов. Нет смысла задумываться о процессе смешивания материала во время производства.
Прочтите: Как построить завод по производству пеллет?
В нашей стране в основном производство единичных машин, требуется только дробление и формование, с подачей рабочей силы. Оценка количества подаваемого материала и влажности материала при простой обработке и низкой стоимости зависит от опыта производителя.Но для этого нужна большая рабочая сила с нестабильным качеством продукции и низкой производительностью.
В непрерывном производстве в нашей стране есть брикетирование и гранулирование по разным технологиям. В настоящее время отечественная технология непрерывного производства в основном применяется в технологиях брикетирования и окомкования.
Маршрут технологии брикетирования обычно означает, что материал проходит через отверстие в кольцевой фильере цилиндрической или призматической формы для формовки, а диаметр фильеры или диагональная линия пересекающейся поверхности больше 25 мм.При этой технологии уплотнения влажность материала обычно составляет около 10-20%. Размер частиц материала менее 50 мм.
Материал технологического маршрута гранулирования обычно проходит через отверстие матрицы цилиндрической формы, диаметр матрицы обычно меньше 25 мм, а толщина матрицы, которая на самом деле равна длине отверстия матрицы, меньше, чем в 4 раза диаметр. Обычно он бывает трех типов: 6 мм, 8 мм и 10 мм. Влажность материала обычно составляет около 12-15%, размер частиц — от 1 до 5 мм.
Существуют большие различия между технологическим процессом формирования брикетов и окатышей, что в основном демонстрируется несколькими пунктами ниже:
1) Метод измельчения. В соответствии с различными требованиями к размеру частиц уплотнения, способ измельчения варьируется. Когда размер частиц составляет 50 мм, он подходит для сжатия, трения и резки. Формирование брикетирования требует однократного дробления для удовлетворения требований к размеру частиц. В технологии формирования окатышей оно включает грубое дробление и мелкое дробление второго раза.И тонкое дробление обычно происходит путем удара молотковой мельницы.
2) Метод транспортировки. Различный размер частиц влияет на пропускную способность исходного материала, который имеет разные способы подачи материала и транспортировки, поэтому изменяются с оборудованием подачи и транспортировки. Поскольку гранулы большого размера легко образуют перемычки, для этого требуется оборудование для принудительного кормления. Когда размер частиц составляет 30-50 мм, следует использовать винтовой конвейер, ленточный конвейер и скребковый конвейер; для частиц размером менее 5 мм необходимо использовать пневматическую трансмиссию.
3) Внесение примесей. Готовый продукт технологии уплотнения обычно составляет 6 мм, 8 мм и 10 мм, три спецификации, в то время как производство уплотнения брикетов имеет диаметр не менее 25 мм. Продукт уплотнения различного типа впитал различную способность имплантируемых примесей. Продукт уплотнения гранул имеет гораздо более строгие требования к содержанию примесей и размеру частиц по сравнению с продуктом брикетирования. Специально для удаления камней необходимо установить различные системы удаления.
4) Способ охлаждения.
Материал гранулятора легко раздавить после сжатия, резкое охлаждение вызывает разрыв талии, что требует охлаждающего устройства для понижения температуры. Топливный брикет обычно имеет большой объем, небольшую плотность, его можно охлаждать и обжаривать естественным путем.
KMEC — профессиональный производитель грануляторов, который объединяет исследования, разработки, производство, продажи и услуги. Наша компания занимается производством всех видов грануляторов, заводов по производству гранул и полного комплекта производственной линии.Если у вас есть какие-либо проблемы, связанные с гранулятором, пожалуйста, свяжитесь с нами. Мы готовы предложить свои предложения и внести свой вклад в ваш бизнес по гранулированию.
Развитие технологии формирования биомассы II
————————————— ————————————————— ————————————————— ——-
В 2015 году тенденция импорта древесных гранул по-прежнему сосредоточена в Европе и США.Европа импортирует гранулы во все больших объемах, сжигая их для получения электроэнергии для достижения целей в области возобновляемых источников энергии. Спрос изменил промышленность США, способствуя удвоению экспорта биомассы в прошлом году. Европейские страны, особенно Великобритания, используют древесные гранулы для замены угля для выработки электроэнергии и отопления.
Вот как вы производите древесные гранулы из биомассы
Древесина использовалась в качестве топлива десятки тысяч лет, но эта древесина — прессованные древесные гранулы — отличается.Он размером с детский цветной карандаш и почти ничего не весит, но в сочетании с множеством других предметов это разумное решение для выработки более чистой электроэнергии по сравнению с углем.
Подобные древесные гранулы используются на электростанции Drax для выработки электроэнергии и производства электроэнергии в городах. Они не только являются возобновляемыми и экологичными, но и потому, что они спрессованы, высушены и сделаны из невероятно тонких древесных волокон, они также являются очень эффективным топливом для электростанций.
Так производятся прессованные древесные гранулы на заводе Drax Biomass Amite BioEnergy Pellet Plant в Миссисипи.
Лес поступает во двор
Древесина поступает на завод на грузовике и отправляется в одно из четырех мест: склад древесины, лесной круг (где древесина грунтуется для обработки), груды опилок и щепы или сразу на переработку.
Кора удаляется и сохраняется для топлива
Бревна загружаются в окорочный станок, который сбивает бревна вместе внутри большого барабана для удаления коры. Кора откладывается и используется в качестве топлива для сушилки для щепы, которая используется позже в процессе.
Тонкие древесные стебли превращаются в мелкую стружку
Бревна — дешевое волокно из устойчиво управляемых лесных хозяйств — необходимо разрезать на еще более мелкие куски, чтобы затем их можно было измельчить до мелкого материала, необходимого для создания гранул. Внутри измельчителя древесины несколько ножей вращаются и разрезают бревна на щепу длиной примерно 10 мм и толщиной 3 мм. Полученная щепа загружается в штабель щепы, готовый к просеиванию.
Стружка проверяется на качество, а отходы удаляются
Сколотая древесина может содержать такие отходы, как песок, остатки коры или камни, которые могут повлиять на производство гранул.Стружка проходит через просеиватель, который удаляет отходы, оставляя только древесную стружку идеального размера.
Самый большой фен, который вы когда-либо видели
Древесная щепа должна иметь уровень влажности от 11,5% до 12%, прежде чем она попадет в процесс гранулирования. Все остальное, кроме этого, и качество получаемых гранул может быть поставлено под угрозу. Щепа попадает в большой барабан, который продувается горячим воздухом, создаваемым нагревателем, питаемым корой, собранной с окорочного станка. Стружка перемещается через барабан с помощью большого вентилятора, готового к работе с молотковой мельницей.
Мелкая щепа становится еще меньше древесной щепы
Внутри молотковой мельницы установлен вращающийся вал с рядом молотков. Древесная стружка подается в верхнюю часть барабана, а вращающиеся молотки измельчают ее до мелкого порошкообразного вещества, которое используется для создания гранул.
Давление стружки — давление много
Измельченная порошковая щепа подается в гранулятор. Внутри вращающийся рычаг проталкивает древесное волокно в порошок через решетку с множеством маленьких отверстий.Сильное давление нагревает древесное волокно и помогает ему соединяться вместе, когда оно проходит через отверстия в металлическом кольцевом красителе, образуя спрессованные древесные гранулы.
Отдых и остывание
Свежие окатыши с завода влажные и горячие, их нужно дать остыть и охладить перед транспортировкой за пределы предприятия. Их перемещают в большие бункеры для хранения, где хранятся при низких температурах, чтобы гранулы могли остыть и затвердеть, готовые к отправке.
Один из самых больших куполов, которые вы когда-либо видели
Это последний этап перед отправкой.Специально спроектированные и сконструированные купола для хранения используются для хранения древесных гранул после их транспортировки в реку Миссисипи, штат Луизиана, и до того, как они отправятся через Атлантический океан в Великобританию.
Расширение производства древесных гранул в США указывает на положительные тенденции, но необходимость в постоянном мониторинге
Соломон, С., Мэннинг, М., Маркиз, М. и Цинь, Д. Изменение климата 2007 — основы физических наук : Вклад Рабочей группы I в Четвертый оценочный отчет IPCC Vol 4 (Cambridge University Press, 2007).
Парламент, E. Директива 2009/28 / EC Европейского парламента и Совета от 23 апреля 2009 г. о содействии использованию энергии из возобновляемых источников и о внесении поправок и последующей отмене Директивы 2001/77 / EC и 2003/30 / EC. Оф. J. Eur. Союз Бельгии 20 , 20 (2009).
Google ученый
Парламент, E. Директива (ЕС) 2018/2001 Европейского парламента и Совета от 11 декабря 2018 г. о содействии использованию энергии из возобновляемых источников. Оф. J. Eur Union Belgium 20 , 2 (2018).
Google ученый
Конференция Организации Объединенных Наций по изменению климата. Парижское соглашение (2015).
Евростат. Поставка, преобразование и потребление возобновляемых источников энергии: данные за год. Веб-сайт Евростата. https://ec.europa.eu/eurostat/web/energy/data/database (2019).
Европейская комиссия.Национальные планы действий в области возобновляемых источников энергии на 2020 год. Https://ec.europa.eu/energy/en/topics/renewable-energy/national-renewable-energy-action-plans-2020 (2020).
Camia, A. et al. Производство, поставка, использование и потоки биомассы в Европейском Союзе. 1–126 (2018) https://doi.org/10.2760/181536.
Эванс, А., Стрезов, В. и Эванс, Т. Дж. Технологии обработки биомассы (CRC Press, Бока-Ратон, 2014). https://doi.org/10.1201/b17093.
Забронировать Google ученый
Гёрндт, М. Э., Агилар, Ф. X. и Ског, К. Ресурсный потенциал для производства возобновляемой энергии за счет совместного сжигания древесной биомассы с углем на севере США. Биомасса Биоэнергетика 59 , 348–361 (2013).
Артикул Google ученый
Спелтер, Х. и Тот, Д. Сектор древесных гранул Северной Америки . Министерство сельского хозяйства США, Лаборатория лесных товаров . https://www.fs.usda.gov/treesearch/pubs/35060 (2009 г.). https://doi.org/10.2737/FPL-RP-656.
Евростат. Международная торговля, торговля в ЕС с 1988 года по HS6. Продукт 440131. Веб-сайт Евростата . https://ec.europa.eu/eurostat/web/international-trade-in-goods/data/database (2019).
Проскурина, С., Юнгингер, М., Хейнимё, Дж., Текинель, Б. и Ваккилайнен, Э. Глобальная торговля биомассой для получения энергии — Часть 2: Производство и торговые потоки древесных пеллет, жидкого биотоплива, древесный уголь, деловой круглый лес и новая энергетическая биомасса. Биотопливо Биопрод. Биорефайнинг 13 , 371–387 (2019).
CAS Статья Google ученый
Абт, К. Л., Абт, Р. К., Галик, К. С. и Ског, К. Э. Влияние политики на производство пеллет и леса на юге США: технический документ, поддерживающий обновление лесной службы оценки РПД 2010 года. Gen. Tech. Представитель SRS-202 Asheville NC US Dep. Agric. Для. Серв. Юг. Res. Стн. 202 , 33 (2014).
Google ученый
Дейл В. Х., Пэриш Э., Клайн К. Л. и Тобин Э. Как производство древесных гранул влияет на состояние лесов на юго-востоке США ?. Для. Ecol. Manag. 396 , 143–149 (2017).
Артикул Google ученый
Сингх Д., Куббидж Ф., Гонсалес Р. и Абт Р. Локальные детерминанты для заводов по производству древесных гранул: обзор и тематическое исследование Северной и Южной Америки. Биоресурсы 11 , 7928–7952 (2016).
Google ученый
Управление энергетической информации США (EIA). Ежемесячный отчет о топливе из плотной биомассы . https://www.eia.gov/biofuels/biomass/#dashboard (2019).
Birdsey, R. et al. Воздействие производства древесины для биоэнергетики на климат, экономику и окружающую среду. Environ. Res. Lett. 13 , 050201 (2018).
ADS Статья CAS Google ученый
Стрэндж Олесен, А., Багер, Л., Киттлер, Б., Прайс, В. и Агилар, Ф. Экологические последствия возросшей зависимости ЕС от биомассы с юго-востока США. Брюссель DG Environ. https://doi.org/10.2779/30897 (2015).
Артикул Google ученый
Duden, A. S. et al. Моделирование воздействия спроса на древесные гранулы на динамику лесов на юго-востоке США. Биотопливо Биопрод. Биорефайнинг 11 , 1007–1029 (2017).
CAS Статья Google ученый
Седжо, Р. и Тиан, X. Увеличивает ли древесная биоэнергетика запасы углерода в лесах ?. J. For. 110 , 304–311 (2012).
Google ученый
de Oliveira Garcia, W., Amann, T. & Hartmann, J. Растущий спрос на биомассу увеличивает отрицательный баланс питательных веществ в лесах в регионах экспорта древесины. Sci. Отчетность 8 , 5280 (2018).
ADS PubMed PubMed Central Статья CAS Google ученый
Searchinger, T. D. et al. Европейская директива по возобновляемым источникам энергии может нанести вред мировым лесам. Nat. Commun. 9 , 3741 (2018).
ADS PubMed PubMed Central Статья CAS Google ученый
Галик, С. и Абт, Р. С. Руководящие принципы устойчивого развития и реакция лесного рынка: оценка спроса Европейского Союза на пеллеты на юго-востоке США. GCB Bioenergy 8 , 658–669 (2016).
Артикул Google ученый
ФОРИСК. Глобальный прогноз спроса на промышленные древесные пеллеты и обновленные данные по древесной биоэнергетике в США: 3 квартал 2017 года . https://forisk.com/blog/2017/08/08/global-industrial-wood-pellet-demand-forecast-u-s-wood-bioenergy-update-q3-2017/ (2017).
Агилар, Ф. X., Сонг, Н. и Шифли, С. Обзор тенденций потребления и государственной политики, продвигающей древесную биомассу в качестве энергетического сырья в США. Биомасса Биоэнергетика 35 , 3708–3718 (2011).
Артикул Google ученый
Робинсон, Дж., МакНалти, Дж. Э. и Красно, Дж. С. Наблюдая противное? Поиск политических экспериментов на природе. Полит. Анальный. 17 , 341–357 (2009).
Артикул Google ученый
Romijn, E. et al. Оценка изменений в потенциале национального мониторинга лесов 99 тропических стран. Для. Ecol. Manag. 352 , 109–123 (2015).
Артикул Google ученый
Корнуолл, W. Является ли древесина зеленым источником энергии? Ученые разделились. Наука (80) 355 , 18–21 (2017).
ADS CAS Статья Google ученый
Glasenapp, S. & McCusker, A. Данные по энергии древесины: совместное исследование энергии древесины. in Энергия древесины в регионе ЕЭК Данные, тенденции и перспективы в Европе, Содружестве Независимых Государств и Северной Америке 12 (Европейская экономическая комиссия Организации Объединенных Наций, 2017).
Вакернагель, М. и Юнт, Дж. Д. Экологический след: индикатор прогресса на пути к региональной устойчивости. Environ. Монит. Оценивать. 51 , 511–529 (1998).
Артикул Google ученый
Макканн, стр. Экономика промышленного размещения: подход к логистике и затратам (Springer, Berlin, 2013).
Google ученый
Гёрндт М. Э., Агилар Ф. X. и Ског К. Факторы совместного сжигания биомассы на угольных электростанциях США. Биомасса Биоэнергетика 58 , 158–167 (2013).
Артикул Google ученый
Перес-Вердин, Г., Гребнер, Д. Л., Манн, И. А., Сан, К. и Градо, С. С. Экономические последствия использования древесной биомассы для биоэнергетики в Миссисипи. Для. Prod. J. 58 , 75–83 (2008).
Google ученый
Объединенный исследовательский центр Европейской комиссии. Возобновляемые источники энергии — прогнозирование до 2030 года (RED II ). https://ec.europa.eu/jrc/en/jec/renewable-energy-recast-2030-red-ii (2019).
ФОРИСК. База данных по древесной биоэнергетике США: 1 квартал 2018 г. . https://forisk.com/ (2018).
Комиссия по международной торговле США (USITC). Внутренний экспорт 2012–2018 гг. Для HS 44 и HS 440131 . https://dataweb.usitc.gov/trade (2019).
Министерство транспорта США (USDOT). Основные порты . https://data-usdot.opendata.arcgis.com/datasets/major-ports (2019).
Блэкман А., Коррал Л., Лима, Э. С. и Аснер, Г. П. Присвоение титулов коренным общинам защищает леса в перуанской Амазонии. Proc. Natl. Акад. Sci. 114 , 4123–4128 (2017).
CAS PubMed Статья Google ученый
Мохебалиан, П. М. и Агилар, Ф. X. Под пологом: тропические леса, включенные в платежи за сохранение, свидетельствуют о меньшей деградации. Ecol. Экон. 143 , 64–73 (2018).
Артикул Google ученый
Burrill, E. A. et al. База данных инвентаризации и анализа лесов: описание базы данных и руководство пользователя версии 8.0 для этапа 2. US Dep. Agric. Для. Серв. 946 , 20 (2018).
Google ученый
Гулдин Р. У., Кинг С. Л. и Скотт К. Т. Видение будущего FIA: путь к прогрессу, возможностям и партнерам. Труды шестого ежегодного заседания. Изобретать. Анальный. Symp. 2004 г., 21–24 сентября; Денвер, штат Колорадо. Gen. Tech. Представитель WO-70. Вашингтон, округ Колумбия Деп. Agric. Для. Серв. 20090 , 126 (2006).
Лесная служба Министерства сельского хозяйства США. Национальная программа инвентаризации и анализа лесов .https://www.fia.fs.fed.us/tools-data/ (2019).
Бехтольд, У. А. и Паттерсон, П. Л. Расширенная программа инвентаризации и анализа лесов — национальные процедуры построения выборки и оценки . Gen. Tech. Представитель SRS-80. Эшвилл, Северная Каролина: Министерство сельского хозяйства США, Лесная служба, Южная исследовательская станция. 85 об. 80. https://www.fs.usda.gov/treesearch/pubs/20371 (2015).
Барбе Г. Способы транспортировки древесины на юге США. Rep. To Louisiana For. Prod. Dev. Cent. (1993).
Ферраро П. Дж. Контрфактическое мышление и оценка воздействия на экологическую политику. Новый реж. Eval. 2009 , 75–84 (2009).
Артикул Google ученый
Дандар, Б., МакГарви, Р. Г. и Агилар, Ф. Х. Определение оптимального сотрудничества между несколькими штатами для сокращения выбросов CO 2 путем совместного сжигания биомассы на угольных электростанциях. Comput. Ind. Eng. 101 , 403–415 (2016).
Артикул Google ученый
Woodall, C. W. et al. Обзор спада в секторе лесных товаров в США. Для. Prod. J. 61 , 595–603 (2011).
Google ученый
Монитор засухи США. Файлы данных ГИС . https: // daughtmonitor.unl.edu/Data/GISData.aspx (2019).
Лесная служба Министерства сельского хозяйства США. Средство просмотра оценки изменений лесов США ForWarn . https://forwarn.forestthreats.org/fcav2/ (2019).
Фишер М., Чаудхури М. и Маккаскер Б. Помогают ли леса сельским домохозяйствам адаптироваться к изменчивости климата? Свидетельства из Южного Малави. World Dev. 38 , 1241–1250 (2010).
Артикул Google ученый
Вулдридж, Дж. М. Эконометрический анализ поперечных сечений и панельных данных (MIT Press, Лондон, 2010).
MATH Google ученый
Millo, G. & Piras, G. splm: модели пространственных панельных данных в R. J. Stat. Софтв. 47 , 1–38 (2012).
Артикул Google ученый
Капур, М., Келеджян, Х. Х. и Пруча, И.R. Панельные модели данных с пространственно коррелированными компонентами ошибок. J. Econom. 140 , 97–130 (2007).
MathSciNet МАТЕМАТИКА Статья Google ученый
Балтаги Б. Эконометрический анализ панельных данных (Wiley, Oxford, 2008).
MATH Google ученый
Хаусман, Дж. А. Спецификационные тесты в эконометрике. Econometrica 46 , 1251 (1978).
MathSciNet МАТЕМАТИКА Статья Google ученый
Крауч, С. Э., Йенсен, Дж., Шварц, Б. Ф. и Швиннинг, С. Смертность деревьев после жаркой засухи: различение факторов, зависящих от плотности, и независимых, и почему это важно. Фронт. Для. Glob. Чанг. 2 , 21 (2019).
Артикул Google ученый
Европейская комиссия. Главное управление энергетики . https://ec.europa.eu/energy/en/topics/renewable-energy/biomass (2019).
Европейская комиссия. Заметка: Пересмотренная Директива по возобновляемым источникам энергии . https://ec.europa.eu/energy/sites/ener/files/documents/technical_memo_renewables.pdf (2016).
Программа устойчивой биомассы. Стандарты . https://sbp-cert.org/documents/standards-documents/standards (2015).
Stephens, S. L. et al. Эффекты лесных топливосберегающих обработок в Соединенных Штатах. Bioscience 62 , 549–560 (2012).
Артикул Google ученый
Berger, A. L. et al. Экологическое воздействие заготовок энергетической древесины: уроки заготовки целых деревьев и естественных нарушений. J. For. 111 , 139–153 (2013).
Google ученый
Яновяк, М. и Вебстер, К. Содействие экологической устойчивости при сборе древесной биомассы. J. For. 108 , 16–23 (2010).
Google ученый
Пауэрс, Р. Ф. et al. Долгосрочный эксперимент по продуктивности почвы в Северной Америке: результаты первого десятилетия исследований. Для. Ecol.Manag. 220 , 31–50 (2005).
Артикул Google ученый
Парламент, Постановление, делегированное Европейской комиссией (ЕС) 2019/807 от 13 марта 2019 года, дополняющее Директиву (ЕС) 2018/2001 Европейского парламента и Совета в отношении определения значительных косвенных изменений в землепользовании -рисковое сырье, для которого значительно увеличиваются. Оф. J. Eur Union Belgium 20 , 20 (2019).
Google ученый
Ханссен, С. В., Дуден, А. С., Юнгингер, М., Дейл, В. Х. и ван дер Хилст, Ф. Древесные пеллеты, что еще? Время паритета парниковых газов европейской электроэнергии из древесных пеллет, произведенных на юго-востоке Соединенных Штатов с использованием различного сырья хвойных пород. GCB Bioenergy 9 , 1406–1422 (2017).
CAS Статья Google ученый
Ван, В., Двиведи, П., Абт, Р. и Ханна, М. Экономия углерода при трансатлантической торговле пеллетами: учет рыночных эффектов. Environ. Res. Lett. 10 , 114019 (2015).
ADS Статья Google ученый
Управление энергетической информации США (EIA). Ежемесячный обзор энергетики: потребление возобновляемых источников энергии: сектор электроэнергетики (энергия древесины, потребляемая сектором электроэнергии) . https://www.eia.gov/totalenergy/data/monthly/#renewable (2019).
Седжо, Р. А. Программа помощи посевам биомассы (BCAP): некоторые последствия для лесной промышленности. ССРН Электрон. J. 20 , 10–22. https://doi.org/10.2139/ssrn.1581551 (2010).
Артикул Google ученый
Эванс, А. М., Першель, Р. Т. и Киттлер, Б. А. Обзор руководящих принципов заготовки лесной биомассы. J. Sustain. Для. 32 , 89–107 (2013).
Артикул Google ученый
Flach, B., Lieberz, S.& Bolla, S. Отчет: Годовой отчет по биотопливу . Служба сельского хозяйства США за рубежом . https://apps.fas.usda.gov/newgainapi/api/Report/DownloadReportByFileName?fileName=BiofuelsAnnual_TheHague_EuropeanUnion_06-29-2020.(2020).
Европейское агентство по окружающей среде. Возобновляемая энергия в Европе: ключ к климатическим целям, но загрязнение воздуха требует внимания . https://www.eea.europa.eu/themes/energy/renewable-energy/renewable-energy-in-europe-key (2019).
Управление энергетической информации США (EIA). Annual Energy Outlook 2018 Таблица: Производство возобновляемой энергии в разбивке по видам топлива: эталонный пример | Регион: США . https://www.eia.gov/outlooks/aeo/data/browser/#/?id=67-AEO2018&linechart=~ref2018-d121317a.9-67-AEO2018.3-0 (2018).
Агентство по охране окружающей среды США (EPA). Интегрированная база данных о выбросах и генерирующих ресурсах (eGRID) . https://www.epa.gov/energy/emissions-generation-resource-integrated-database-egrid.(2019).
Национальная конференция законодательных собраний штатов. Государственные стандарты и цели портфеля возобновляемых источников энергии . https://www.ncsl.org/research/energy/renewable-portfolio-standards.aspx (2018).
Shifley, S. R. et al. Пять антропогенных факторов, которые радикально изменят состояние лесов и потребности управления в северных Соединенных Штатах. Для. Sci. 60 , 914–925 (2014).
Артикул Google ученый
Уир, Д. Н. и Грейс, Дж. Г. Фьючерсный проект Южного леса: итоговый отчет / Дэвид Н. Уир и Джон Г. Грейс . Общий технический отчет SRS: 168 vol. 168. https://proxy-remote.galib.uga.edu/login?url=https://search.ebscohost.com/login.aspx?direct=true&db=edsgpr&AN=gprocn839703115&site=eds-live. https://www.srs.fs.fed.us/pubs/gtr/gtrsrs168.pdf (2012 г.).
Ruta, G. Мониторинг экологической устойчивости (Всемирный банк, Женева, 2010 г.).https://doi.org/10.1596/27445.
Забронировать Google ученый
Европейская комиссия. Устойчивая биоэкономика для Европы: укрепление связи между экономикой, обществом и окружающей средой . https://ec.europa.eu/research/bioeconomy/pdf/ec_bioeconomy_strategy_2018.pdf (2018).
Совет Европейских сообществ и Комиссия Европейских сообществ. Договор о Европейском Союзе — Маастрихтский договор .253 (1993).
Европейский Союз. Амстердамский договор . 144 (1997).
Дайер, Дж. М. Возвращение к лиственным лесам восточной части Северной Америки. Bioscience 56 , 341–352 (2006).
Артикул Google ученый
Управление энергетической информации США. Из подробных данных EIA-860 с данными предыдущей формы (EIA-860A / 860B) . https: // www.eia.gov/electricity/data/eia860/ (2019).
Управление энергетической информации США. Форма EIA-923 Подробные данные с данными предыдущей формы (EIA-906/920). https://www.eia.gov/electricity/data/eia923/ (2019).
Грей, Дж. А., Бентли, Дж. У., Купер, Дж. А. и Уолл, Д. Дж. Производство балансов в южной части Министерства сельского хозяйства США, 2016 . Бюллетень электронных ресурсов SRS – 222. Эшвилл, Северная Каролина: Лесная служба Министерства сельского хозяйства США, Южная исследовательская станция https: // www.fs.usda.gov/treesearch/pubs/56531 (2018).
Пива, Р. Дж., Бентли, Дж. У. и Хейс, С. В. Национальное производство балансовой древесины, 2010 год . Resour. Бык. НРС-89. Площадь Ньютаун, Пенсильвания: Министерство сельского хозяйства США, Лесная служба, Северная исследовательская станция https://www.fs.usda.gov/treesearch/pubs/45928 (2014). https://doi.org/10.2737/NRS-RB-89.
Prestemon, J. et al. Расположение деревообрабатывающих предприятий в континентальной части США.S . https://www.srs.fs.usda.gov/econ/data/mills/ (2005 г.).
Джонсон, Т. Г. и Степплтон, К. Д. Производство балансовой древесины в южной части Министерства сельского хозяйства США, 2005 г. . Resour. Бык. СРС-116. Эшвилл, Северная Каролина: Лесная служба Министерства сельского хозяйства США, Южная исследовательская станция . https://www.fs.usda.gov/treesearch/pubs/27728 (2007 г.).
Джонсон, Т. Г., Степлтон, К. Д. и Бентли, Дж. У. Производство балансов в южной части Министерства сельского хозяйства США, 2008 г. . Resour. Бык. СРС – 165. Эшвилл, Северная Каролина: Лесная служба Министерства сельского хозяйства США, Южная исследовательская станция . https://www.fs.usda.gov/treesearch/pubs/34565 (2010 г.).
Bentley, J. W. & Steppleton, C. D. Производство балансовой древесины в южной части страны, 2011 год . Resour. Бык. СРС-РБ-194. Эшвилл, Северная Каролина: Лесная служба Министерства сельского хозяйства США, Южная исследовательская станция . https://www.fs.usda.gov/treesearch/pubs/43626 (2013 г.).
Грей, Дж. А., Бентли, Дж. У., Купер, Дж. А. и Уолл, Д. Дж. Производство балансов в южной части Министерства сельского хозяйства США, 2014 г. . Бюллетень электронных ресурсов SRS – 219. Эшвилл, Северная Каролина: Лесная служба Министерства сельского хозяйства США, Южная исследовательская станция . https://www.fs.usda.gov/treesearch/pubs/56235 (2018).
Бюро переписи населения США. Картографические пограничные файлы . https://www.census.gov/geographies/mapping-files/time-series/geo/carto-boundary-file.html (2019).
Бюро переписи населения США. Население округа . https://www.census.gov/data/tables/time-series/demo/popest/2010s-counties-total.html (2020).
R Основная команда. R: Язык и среда для статистических вычислений . https://www.r-project.org/ (2019).
Pebesma, E. Простые функции для R: стандартизированная поддержка пространственных векторных данных. Р. Дж. 10 , 439 (2018).
Артикул Google ученый
Флауэрдью Р. и Грин М. Ареальная интерполяция и типы данных. В Пространственный анализ и ГИС (редакторы Fotheringham, S. & Rogerson, P.) 73–75 (CRC Press, Boca Raton, 2014).
Google ученый
Гёрндт, М. Э., Уилсон, Б. Т. и Агилар, Ф. Х. Сравнение методов оценки малых площадей, применяемых к поставкам биоэнергетического сырья в северном регионе США. Биомасса Биоэнергетика 121 , 64–77 (2019).
Артикул Google ученый
Ожидается, что мировая промышленность по производству древесных пеллет будет расти со среднегодовым темпом роста 14,47% в период с 2019 по 2025 год
ДУБЛИН, 4 декабря 2020 г. / PRNewswire / — В предложение ResearchAndMarkets.com был добавлен отчет «Мировой рынок древесных пеллет — прогнозы с 2020 по 2025 год».
Мировой рынок древесных пеллет был оценен в 10 долларов США.491 млрд долларов США в 2019 году и, как ожидается, будет расти со среднегодовым темпом роста 14,47% в течение прогнозируемого периода, чтобы достичь общего объема рынка в 23,604 млрд долларов США в 2025 году. Древесные пеллеты являются возобновляемыми энергоносителями. Их производят из опилок или других измельченных древесных материалов. В соответствии с международными стандартами определены требования к продукту в отношении удельной энергии, влажности, устойчивости к истиранию, размера частиц и формы древесных гранул, что превращает древесные гранулы в товар.
Таким образом, стандартизованные древесные гранулы обладают многообещающими свойствами для крупномасштабного производства.С ростом производства древесных пеллет произошел значительный рост торговых потоков древесных пеллет по всему миру. Древесные гранулы используются в различных сферах применения, что увеличивает их спрос во всем мире. Например, древесные гранулы широко используются в качестве удобного твердого биотоплива в автоматических печах и котлах в секторе домашнего отопления. Древесные пеллеты сокращают выбросы парниковых газов (ПГ) при выработке электроэнергии при совместном сжигании на угольных электростанциях. Промышленные древесные пеллеты используются вместо угля на электростанциях, а пеллеты премиум-класса используются в пеллетных котлах и пеллетных печах для отопления.
Древесные пеллеты стали жизнеспособным и многообещающим возобновляемым источником энергии в качестве замены угля, особенно в Европе и Северной Америке. За последние несколько лет рынок пеллет во всем мире стал свидетелем огромного роста с увеличением спроса как на промышленное применение на крупных электростанциях, так и на маломасштабное применение в системах отопления жилых помещений.
Рынок древесных гранул набирает обороты, поскольку они имеют низкий углеродный след.Таким образом, растущее беспокойство по поводу экологической устойчивости во всем мире является основным фактором роста спроса на древесные гранулы, который стимулирует рост мирового рынка. Правительства разных стран вместе с глобальными организациями постоянно предпринимают необходимые шаги и меры для достижения поставленной цели, связанной с сокращением углеродного следа или выбросов парниковых газов (ПГ). Ограниченная доступность невозобновляемых ресурсов и их неблагоприятное воздействие на окружающую среду вынудили мировую экономику переключиться на альтернативные источники энергии без ущерба для окружающей среды.Правительства по всему миру поставили перед собой цель перейти к использованию различных возобновляемых источников энергии.
Использование древесных пеллет в качестве топлива получило широкое распространение для отопления домов и энергетических котлов, особенно в европейском регионе. Легкая доступность сырья, такого как древесина и уплотненные опилки, в сочетании с низкой себестоимостью производства являются одними из факторов, которые также способствуют устойчивому росту спроса на древесные гранулы, тем самым стимулируя рост рынка.
Участники мирового рынка древесных гранул активно участвуют в исследованиях и разработках, чтобы повысить эффективность процесса производства древесных гранул и получить конкурентное преимущество над своими конкурентами. По этой причине разрабатываются новые и усовершенствованные конструкции для грануляторов, обеспечивающие высокий выход продукции при оптимальном расходе топлива. Кроме того, проводятся обширные исследования по производству древесных пеллет с высокой теплотворной способностью из доступного сырья. Ожидается, что все эти факторы будут способствовать росту мирового рынка древесных пеллет в течение следующих пяти лет.
Европа является крупнейшим потребителем, а также производителем древесных гранул
По географическому признаку глобальный рынок древесных гранул разделен на пять основных региональных рынков — Северная Америка, Южная Америка, Европа, Ближний Восток и Африка (MEA). ) и Азиатско-Тихоокеанский регион (APAC). На Европу приходилась основная доля на мировом рынке древесных пеллет в 2019 году. По данным Глобальной сельскохозяйственной информационной сети Министерства сельского хозяйства США Министерства сельского хозяйства США, ЕС (Европейский союз) потребил около 27 единиц.35 миллионов метрических тонн древесных пеллет в 2018 году по сравнению с 24,15 миллиона тонн в предыдущем году. Кроме того, потребление древесных пеллет в этом регионе, по оценкам, вырастет до 30 миллионов метрических тонн в 2019 году, при этом импорт вырастет до 12,2 миллиона метрических тонн с 10,355 миллиона метрических тонн в 2018 году.
Согласно отчету, в ЕС имеется 656 заводов по производству пеллет. 2017 г., с общей мощностью 2,75 млн метрических тонн. Ожидается, что мощность вырастет до 72 процентов в 2019 году по сравнению с 70 процентами в 2018 году и 67 процентами в 2017 году.По странам Великобритания стала крупнейшим потребителем древесных пеллет в регионе ЕС в 2018 году с 8 миллионами метрических тонн, за ней следуют Италия (3,75 миллиона метрических тонн), Дания (3,5 миллиона метрических тонн), Германия (2,19 миллиона метрических тонн. ) и Швеции (1,785 млн метрических тонн). Строгие правила в отношении экологической устойчивости и постоянные усилия по достижению целевых показателей выбросов в указанный период времени в значительной степени способствуют доминированию европейского региона на мировом рынке древесных пеллет.Поддерживающие правительственные инициативы и стимулы, предлагаемые странами-членами ЕС, также способствуют росту рынка древесных пеллет в этом регионе.
Северная Америка также увеличивает потребление древесных пеллет из-за конкурентоспособности региональных цен на пропан и мазут для отопления жилых помещений. Быстрая замена традиционных горелок для улучшения подачи корма также стимулирует спрос на древесные гранулы в этом регионе.
Ожидается, что на рынке древесных пеллет Азиатско-Тихоокеанского региона (APAC) будут наблюдаться заметные среднегодовые темпы роста (CAGR) в течение прогнозируемого периода.Благоприятная государственная политика по расширению использования древесных гранул для производства электроэнергии наряду с увеличением числа электростанций подпитывает спрос на древесные гранулы в странах Азиатско-Тихоокеанского региона, особенно в Японии, Южной Корее и Китае. Растущее внимание к сектору возобновляемых источников энергии в странах Азиатско-Тихоокеанского региона способствует дальнейшему росту регионального рынка. Samsung C&T постоянно расширяет свою роль в импорте древесных пеллет в Южную Корею, страну, в которой отсутствуют природные энергоресурсы. Кроме того, страна настолько активно субсидирует сектор биомассы, что фактически препятствует внедрению других возобновляемых источников энергии, таких как ветер и солнце.
Япония в настоящее время является основным мировым покупателем скорлупы пальмовых ядер (ПКС), закупив более 60% от общего объема экспорта ПКС в 2018 году. ПКС — это основное топливо, которое используется многими независимыми производителями электроэнергии в Японии, которые хотят получить выгоду. льготного тарифа (FIT), который является частью политики страны в области низкоуглеродной генерации. Схема FIT предлагает 20-летнюю субсидию компаниям, производящим возобновляемую энергию. Увеличение инвестиций в заводы по производству биомассы в этом регионе также будет способствовать росту рынка древесных пеллет в течение следующих пяти лет.Например, в феврале 2019 года Renova Inc приняла окончательное инвестиционное решение (FID) и достигла финансового закрытия проекта по выработке электроэнергии из биомассы Токусима Цуда мощностью 74,8 МВт в префектуре Токусима. Электростанция, работающая на биомассе, будет использовать древесные пеллеты и PKS в качестве источника топлива, и ее планируется запустить к марту 2023 года. В августе 2019 года Shell India инвестировала 7,7 млн долларов в местную фирму по производству биомассы Punjab Renewable Energy при поддержке Neev Fund.
Конкурентный анализ
К числу видных ключевых игроков на мировом рынке древесных пеллет относятся German Pellets GmbH, Pinnacle Renewable Energy Inc, Energex, Enviva LP, Wood & Sons, Drax Group plc, AS Graanul Invest, AVPGroup, Lignetics, Canfor, Stora Enso , Svenska Cellulosa Aktiebolaget SCA (publ), The Brookridge Group и PIVETEAUBOIS.Эти компании занимают заметную долю на рынке благодаря хорошему имиджу бренда и предлагаемой продукции. Были рассмотрены основные игроки на мировом рынке древесных пеллет, их относительное конкурентное положение и стратегии. В отчете также упоминаются недавние сделки и инвестиции различных игроков рынка за последние два года.
Ключевые темы:
1. Введение
1.1. Определение рынка
1.2. Сегментация рынка
2.Методология исследования
2.1. Данные исследования
2.2. Допущения
3. Резюме
3.1. Основные результаты исследования
4. Динамика рынка
4.1. Драйверы рынка
4.2. Ограничения рынка
4.3. Возможности рынка
4.4. Анализ сил Porters Five
4.4.1. Сила поставщиков на переговорах
4.4.2. Торговая сила покупателей
4.4.3. Угроза новых участников
4.4.4. Угроза замены
4.4.5. Конкурентное соперничество в отрасли
4.5. Анализ производственно-сбытовой цепочки
4.6. Рыночная привлекательность
5. Анализ мирового рынка древесных пеллет по приложениям
5.1. Введение
5.2. Тепло
5.3. ТЭЦ
5.4. Power
6. Анализ мирового рынка древесных пеллет, по конечным потребителям
6.1. Введение
6.2. Промышленный
6.3. Жилой и коммерческий сектор
7. Анализ мирового рынка древесных пеллет по географическому признаку
7.1. Введение
7.2. Северная Америка
7.2.1. Рынок древесных пеллет в Северной Америке, по заявкам, 2019-2025 гг.
7.2.2. Рынок древесных пеллет в Северной Америке, по конечным потребителям, 2019-2025 гг.
7.2.3. По странам
7.2.3.1. США
7.2.3.2. Канада
7.2.3.3. Мексика
7.3. Южная Америка
7.3.1. Рынок древесных пеллет в Южной Америке, по заявкам, 2019-2025 гг.
7.3.2. Рынок древесных пеллет в Южной Америке, по конечным потребителям, 2019-2025 гг.
7.3.3. По странам
7.3.3.1. Бразилия
7.3.3.2. Аргентина
7.3.3.3. Другое
7.4. Европа
7.4.1. Рынок древесных пеллет в Европе, по заявкам, 2019-2025 гг.
7.4.2. Рынок древесных пеллет в Европе, по конечным потребителям, 2019-2025 гг.
7.4.3. По странам
7.4.3.1. Германия
7.4.3.2. Франция
7.4.3.3. Соединенное Королевство
7.4.3.4. Италия
7.4.3.5. Испания
7.4.3.6. Дания
7.4.3.7. Австрия
7.4.3.8. Другое
7.5. Ближний Восток и Африка
7.5.1. Рынок древесных пеллет Ближнего Востока и Африки, по заявкам, 2019-2025 гг.
7.5.2. Рынок древесных пеллет Ближнего Востока и Африки, по конечным потребителям, 2019-2025 гг.
7.5.3. По странам
7.5.3.1. Саудовская Аравия
7.5.3.2. ОАЭ
7.5.3.3. Другое
7.6. Азиатско-Тихоокеанский регион
7.6.1. Рынок древесных пеллет в Азиатско-Тихоокеанском регионе, по заявкам, 2019-2025 гг.
7.6.2. Рынок древесных пеллет в Азиатско-Тихоокеанском регионе, по конечным потребителям, 2019-2025 гг.
7.6.3. По стране
7.6.3.1. Япония
7.6.3.2. Китай
7.6.3.3. Индия
7.6.3.4. Южная Корея
7.6.3.5. Другое
8. Конкурентная среда и анализ
8.1. Основные игроки и анализ стратегии
8.2. Развивающиеся игроки и прибыльность рынка
8.3. Слияния, поглощения, соглашения и сотрудничество
8.4. Матрица конкурентоспособности поставщиков
9. Профили компаний
9.1. Герман Пеллетс ГмбХ
9.2. Pinnacle Renewable Energy Inc
9.3. Energex
9.4. Enviva LP
9.5. Wood & Sons
9.6. Drax Group plc
9.7. AS Graanul Invest
9.8. AVPGroup
9.9. Лигнетика
9.10. Canfor
9.11. Stora Enso
9.12. Svenska Cellulosa Aktiebolaget SCA (publ)
9.13. Группа Брукридж
9.14. PIVETEAUBOIS
Для получения дополнительной информации об этом отчете посетите https://www.researchandmarkets.com/r/ujy7dr
Research and Markets также предлагает услуги Custom Research, обеспечивающие целенаправленное, всестороннее и индивидуальное исследование.
Контактное лицо для СМИ:
Research and Markets
Лаура Вуд, старший менеджер
[адрес электронной почты защищен]
Для работы в офисе E.S.T. Звоните + 1-917-300-0470
для США./ CAN Бесплатный звонок + 1-800-526-8630
В рабочие часы по Гринвичу звоните + 353-1-416-8900
Факс в США: 646-607-1904
Факс (за пределами США): + 353-1-481 -1716
ИСТОЧНИКИ Исследования и рынки
Ссылки по теме
http://www.